Introduction
The electronics industry has faced significant supply chain challenges in recent years, with shortages and long lead times impacting the ability to bring new products to market on time and on budget. Effective BOM (Bill of Materials) part selection strategies are critical to minimizing supply risks.
At the AltiumLive 2022 conference, industry experts shared best practices and recommendations for avoiding supply chain issues through smart BOM part choices. This article summarizes the key takeaways to help you improve your BOM management and keep your projects on track.
The Impact of Supply Chain Disruptions on Electronics Manufacturing
The COVID-19 pandemic exposed the fragility of global electronics supply chains. Factory shutdowns, transportation bottlenecks, and spikes in demand led to widespread part shortages and cost increases. Even as the acute disruptions have eased, ongoing issues like geopolitical uncertainty, labor shortages, and climate events continue to stress supply chains.
The results have been painful for many companies:
- Delayed product launches
- Lost sales due to inability to fulfill orders
- Increased material and expediting costs
- Wasted time spent on supply chain firefighting vs. core design work
A Feb 2022 IPC industry survey highlighted the extent of the challenges:
Metric | Finding |
---|---|
Companies experiencing increased lead times | 90% |
Avg lead time increase for circuit board assemblies | 6 weeks |
Companies forced to redesign due to part availability | 75% |
Source: IPC Supply Chain Report, Feb 2022
While many factors driving supply chain volatility are outside a product company’s direct control, proactive BOM management and part selection can significantly reduce exposure to risks and disruptions. The following sections detail specific strategies to implement.
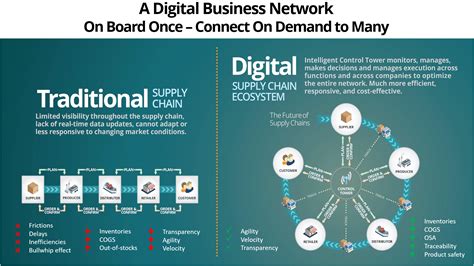
Avoiding Supply Issues When Selecting BOM Parts
Prioritize Availability Over Lowest Cost
Historically, companies aimed to minimize BOM cost by selecting the lowest priced part that met functional and quality requirements. However, in today’s constrained environment, availability should be weighted more heavily.
“The lowest cost part isn’t the lowest cost if it has a 52 week lead time and prevents you from getting your product to market,” noted one AltiumLive speaker. They recommended comparing “true cost” based on price, availability, and strategic value to the business.
Practical tips:
– Filter part choices based on current availability and lead times
– Calculate “cost of delay” and factor into part cost analysis
– Favor parts with wide distribution and good historical availability
Partner with Authorized Distributors
Authorized distributors have direct relationships with component manufacturers and the most up-to-date information on availabilty. Building strong partnerships with authorized distis provides access to:
- Accurate inventory and lead time data
- Visibility into product change notices and predicted supply constraints
- Faster issue resolution if supply problems occur
- Guaranteed authentic parts vs counterfeits
Major authorized distributors like Arrow, Avnet, Digi-Key and Mouser have sophisticated APIs and data services that can be integrated into PCB design and supply chain management tools to streamline part selection and procurement.
Leverage Supply Chain Intelligence
Access to component data and market intelligence helps identify potential supply risks early in the design process. Types of supply chain intelligence to leverage include:
- Lifecycle status – avoid parts nearing end-of-life; favor actively maintained parts
- Market availability – how widely is the part stocked; are there alternates from multiple manufacturers
- Historical lead times – has the part had stable lead times or frequent supply issues
- Geopolitical and environmental risks – is the part manufactured in a region facing instability or natural disasters
- Allocation and demand trends – are order patterns signaling an upcoming shortage
Subscription services like IHS Markit and SiliconExpert provide detailed part intelligence. Distributors and manufacturers may also share data. It’s important to integrate this intelligence into the BOM planning process vs. just checking a part’s current availability.
Design for Multiple Supply Sources
Whenever possible, design the product to accommodate alternate parts. Ways to do this include:
- Select generic parts available from multiple manufacturers vs single-sourced parts
- Allow for pin-compatible alternates that can be substituted without redesigning the board
- Define fall-back parts that can be used with small design modifications if the primary part becomes unavailable
- Consider designing in older, more widely available parts vs. cutting-edge parts in constrained supply
Having multiple vetted supply sources for critical components provides valuable flexibility to adapt to changing market conditions. Document the alternates in the BOM and AVL (approved vendor list) so the information is readily available if needed.
Consider Inventory Buffering for Critical Parts
For parts that are single-sourced or have a high risk of supply issues, consider buying buffer inventory to protect against shortages. The amount of buffer stock required depends on factors like:
- Projected demand for the finished product
- Confidence in the demand forecast
- Lead time for the part
- Cost of the part
- Storage and handling requirements
- Financial impact of a stockout
Work with your supply chain team to analyze parts and determine where a buffer makes sense. Be sure to also have a plan for managing excess if demand is lower than expected. In some cases, distributors will hold the buffer stock and only charge when parts are consumed.
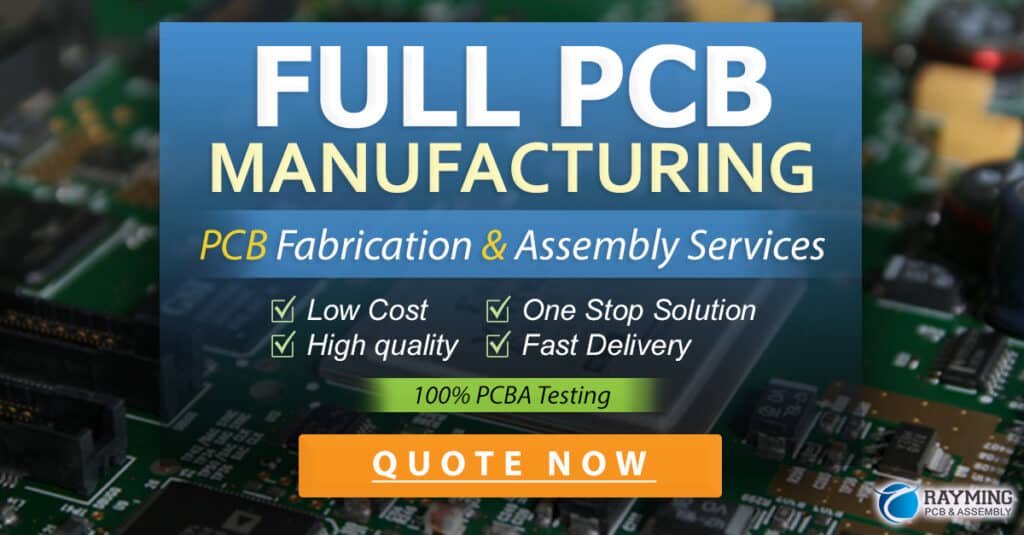
Adapting BOMs to Supply Chain Volatility
Even with proactive planning, supply chain issues will still occur. The ability to quickly adapt the BOM when parts become unavailable is essential. Tips include:
Keep BOMs Up-to-Date with Current Availability
Review BOMs frequently to identify parts at risk of shortage before there’s an impact on production. Your ERP or supply chain management system should have tools to flag parts with worsening availability or lead times.
Assign clear ownership of the BOM review process and automate notifications to stay on top of supply changes. Aim to review BOMs for active products at least monthly, and more frequently for parts known to be volatile.
Have Substitution Procedures Ready
When a part shortage occurs, have a defined process to qualify and approve alternates quickly. Key steps:
- Assess the impact – how many products are affected, how much inventory is on-hand, when will production be impacted
- Identify alternates – refer to pre-approved substitutes if available, otherwise work with engineers and suppliers to find replacements
- Verify form, fit and function – test alternatives to ensure they meet all performance and quality requirements, engage engineers for redesign if needed
- Update documentation – revise BOMs, drawings, procedures and communicate changes to all stakeholders
- Adjust supply plans – update forecasts and orders based on selected substitute parts
Having clear roles, decision criteria, and change procedures defined in advance will accelerate the substitution process.
Collaborate Closely with Suppliers
Open communication with suppliers is critical to navigating supply issues. Schedule regular check-ins to discuss demand forecasts, potential supply concerns, and mitigation plans. Ask for suppliers’ input when exploring substitute parts.
If possible, provide suppliers 12+ month rolling forecasts so they have advanced warning of demand changes. Commit to purchases within the supplier’s standard lead time to give them confidence to allocate inventory for your orders.
Also discuss suppliers’ allocation procedures in the event of shortages. Understand how they prioritize customers and what information they need from you to ensure fair allocation of constrained parts.
Design Products with Supply Flexibility in Mind
Engineers are usually focused on functionality, performance and cost when designing new products. But in today’s environment, it’s important to also consider supply flexibility.
Ways to design products to withstand supply volatility include:
- Use standard, widely available parts and avoid custom or single-sourced parts unless absolutely necessary
- Allow for multiple pin-compatible alternates in the schematic and layout
- Consider designing separate product configurations optimized for different supply scenarios
- Design power supplies and other subsystems to handle a wider range of alternate parts
Work with your engineering team to make supply flexibility a key requirement in the product development process. Engage procurement early in the design cycle to vet part selections and source alternates.
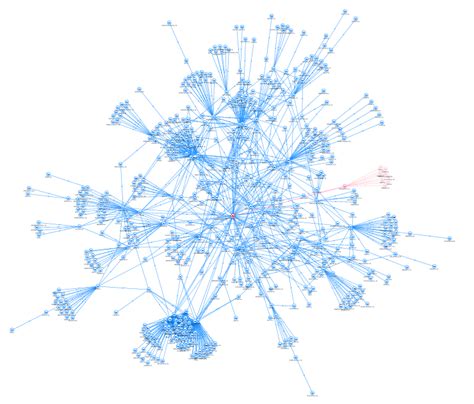
Putting It All Together
Effective BOM management is a cross-functional effort involving engineering, procurement, supply chain, and production teams. Integrate supply risk analysis into each phase of the product lifecycle:
- Design – consider availability and sourcing risks in initial part selection; allow for multiple alternates
- New Product Introduction – vet selected parts with suppliers; buy additional stock of critical parts; document alternates
- Production – monitor BOM status regularly; react quickly to supply issues; collaborate with suppliers
- Sustaining – assess lifecycle risk of older parts; redesign proactively to mitigate obsolescence
The right tools and processes are also essential. At a minimum you need:
- Component & supplier management system with availability, lead time, lifecycle, and risk data
- BOM management tools integrated with your CAD and ERP systems
- Alerts and workflows to monitor supply changes and drive corrective actions
- Strong relationships with suppliers and contract manufacturers
Conclusion
While supply chains are likely to remain volatile for the foreseeable future, product companies can greatly reduce their risks through smart BOM strategies and processes. By making part selection a strategic priority and partnering closely with suppliers, you can keep production running smoothly and bring innovative new products to market quickly. The key is staying vigilant, flexible, and proactive to adapt to shifting market conditions.
FAQs
What are the most important factors to consider when selecting parts for a new product BOM?
The key factors are:
1. Functionality and performance – does the part meet the design requirements
2. Availability and lead time – is the part readily available and are lead times acceptable
3. Cost – is the price competitive and are volume discounts available
4. Quality and reliability – does the part meet quality and reliability standards
5. Compliance – does the part meet regulatory and environmental requirements
6. Lifecycle status – how long will the part be maintained and supported by the manufacturer
Weigh each of these factors based on the specific needs of the product and market. Achieving the optimal balance is key to a successful design.
How can I find alternate parts if my first choice becomes unavailable?
There are several ways to identify alternate parts:
- Consult with your suppliers – authorized distributors and manufacturers can often recommend alternates or confirm compatibility of parts you’ve identified
- Use online cross-reference tools – sites like Octopart and IHS Markit Component have tools to find equivalent parts from other manufacturers
- Check manufacturer part families – many manufacturers offer families of pin- and function-compatible parts in various speed grades, temp ranges, packages, etc
- Engage your engineering team – for complex parts, work with engineers to assess potential alternates and redesign options
Be sure to thoroughly validate any alternate parts to ensure they meet all performance, quality, and reliability requirements before modifying the BOM.
How much buffer inventory should I stock for critical parts?
The right amount of buffer stock depends on several factors:
- Criticality of the part to production
- Availability and lead time of the part
- Variability and confidence in demand forecasts
- Cost of the part
- Storage and handling costs
- Risk and cost of a stockout
A common approach is to set the buffer target based on a certain number of weeks or months of projected usage. For example, you may decide to always keep 4 weeks of inventory on hand for critical parts with 8 week lead times.
However, it’s important to adjust buffers dynamically based on changing conditions. You may need more buffer for highly constrained parts or new products with uncertain demand.
Work with your procurement and supply chain planning teams to analyze parts and determine appropriate inventory targets. Regularly review buffer levels and adjust as needed based on the latest lead time and demand data.
How often should I review the BOMs for my products?
The frequency of BOM reviews depends on the product lifecycle stage and supply chain conditions. In general:
- New products – review BOMs at least monthly to identify any supply issues that could impact the launch schedule
- High volume products – review BOMs monthly or even weekly to ensure uninterrupted supply, especially for parts with long lead times
- Low volume/specialty products – review BOMs at least quarterly to identify lifecycle risks and initiate redesigns proactively as needed
- End-of-life products – monitor supply availability and execute last-time buys well in advance of the planned discontinuation
Also review BOMs more frequently during periods of supply chain disruption or when introducing major design changes.
Assign clear ownership for BOM reviews and use automation to alert teams to parts with worsening availability or lifecycle risks. The goal is to identify potential issues early, before there’s an impact to production.
What’s the best way to collaborate with suppliers to avoid supply chain disruptions?
Building strong, strategic relationships with your key suppliers is essential to weathering supply chain challenges. Some best practices:
- Share forecasts and production plans – provide suppliers with regular updates on your demand outlook so they can plan their inventory and capacity accordingly
- Set up regular check-in meetings – discuss demand trends, supply constraints, quality issues, and continuous improvement opportunities
- Establish clear communication channels – make sure your teams know who to contact at the supplier to get fast answers to supply issues
- Align on metrics and scorecards – establish shared KPIs and use supplier scorecards to track and discuss performance
- Collaborate on risk mitigation – work together to identify supply risks and develop backup plans to ensure continuity
- Invest in the relationship – look for opportunities to partner on new product designs, process improvements, and technology roadmaps
Treating suppliers as strategic partners, rather than transactional vendors, will pay dividends in terms of better supply availability, faster issue resolution, and access to the latest technologies. Focus on building trust and mutual benefit for long-term success.
No responses yet