What are Aluminum PCBs?
Aluminum PCBs, also known as metal core PCBs (MCPCBs), are a type of printed circuit board that uses an aluminum substrate instead of the traditional FR-4 substrate. The aluminum substrate provides excellent thermal conductivity, allowing for efficient heat dissipation from electronic components. This makes aluminum PCBs ideal for applications that generate significant amounts of heat, such as high-power LEDs, power electronics, and automotive systems.
Advantages of Aluminum PCBs
- Excellent thermal conductivity
- Improved reliability and longevity of electronic components
- Lightweight and durable
- Cost-effective solution for heat management
- Suitable for a wide range of applications
Structure of Aluminum PCBs
Aluminum PCBs consist of three main layers:
-
Dielectric Layer: This layer is an electrically insulating material that is applied directly to the aluminum substrate. It provides electrical isolation between the aluminum substrate and the copper circuit layer.
-
Copper Circuit Layer: The copper circuit layer is where the electronic components are mounted and the electrical connections are made. This layer is similar to the copper layer in traditional PCBs.
-
Aluminum Substrate: The aluminum substrate serves as the base of the PCB and provides the thermal management properties. The thickness of the aluminum substrate can vary depending on the specific application and thermal requirements.
Layer | Material | Function |
---|---|---|
Dielectric Layer | Thermally conductive, electrically insulating | Provides electrical isolation and thermal conductivity |
Copper Circuit Layer | Copper | Accommodates electronic components and connections |
Aluminum Substrate | Aluminum alloy (e.g., 5052, 6061) | Serves as the base and provides thermal management |
Manufacturing Process of Aluminum PCBs
The manufacturing process of aluminum PCBs involves several steps:
-
Substrate Preparation: The aluminum substrate is cleaned and treated to ensure proper adhesion of the dielectric layer.
-
Dielectric Layer Application: The dielectric layer is applied to the aluminum substrate using techniques such as lamination, screen printing, or thermal spraying.
-
Copper Foil Lamination: A copper foil is laminated onto the dielectric layer using heat and pressure.
-
Circuit Patterning: The copper foil is patterned using photolithography and etching processes to create the desired circuit layout.
-
Surface Finishing: The exposed copper areas are finished with a protective coating, such as ENIG (Electroless Nickel Immersion Gold) or OSP (Organic Solderability Preservative), to prevent oxidation and improve solderability.
-
Solder Mask Application: A solder mask is applied to protect the copper circuits and prevent short circuits during soldering.
-
Silkscreen Printing: The component designators, logos, and other markings are printed on the PCB using silkscreen printing.
-
Drilling and Routing: Holes are drilled for through-hole components, and the PCB is routed to its final shape and size.
-
Electrical Testing: The PCB undergoes electrical testing to ensure proper functionality and connectivity.
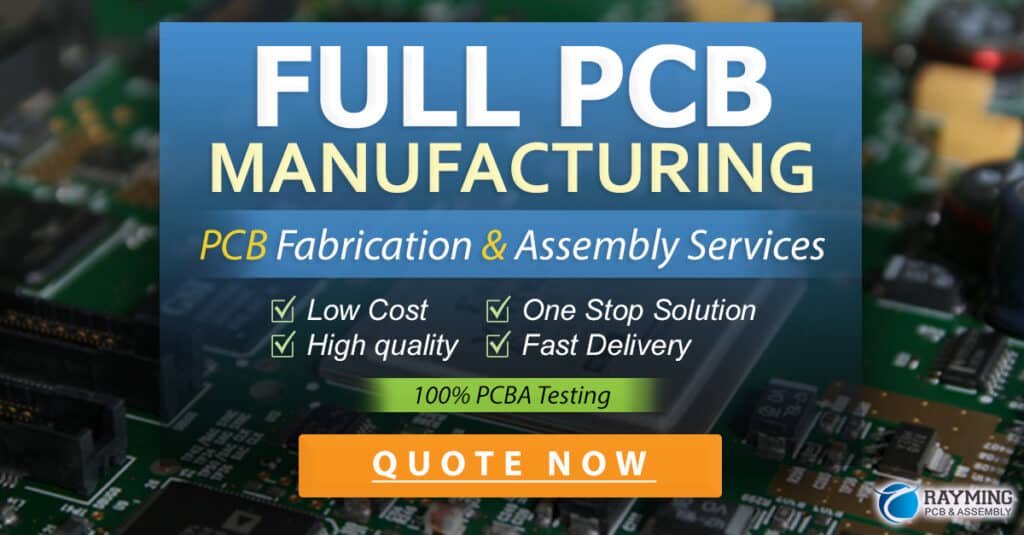
Applications of Aluminum PCBs
Aluminum PCBs are used in a wide range of applications where thermal management is critical:
-
High-Power LEDs: Aluminum PCBs are commonly used in LED lighting systems to dissipate heat generated by the LEDs, ensuring optimal performance and longevity.
-
Power Electronics: In power electronic devices, such as motor drives, inverters, and power supplies, aluminum PCBs help manage heat generated by high-current components like MOSFETs and IGBTs.
-
Automotive Electronics: Aluminum PCBs are used in automotive applications, such as headlights, engine control units, and power steering systems, where they must withstand harsh environmental conditions and high temperatures.
-
Telecommunications: In telecommunication systems, aluminum PCBs are used in power amplifiers and base station equipment to ensure reliable operation and prevent overheating.
-
Industrial Control Systems: Aluminum PCBs are used in industrial control systems, such as programmable logic controllers (PLCs) and motor drives, where they provide efficient heat dissipation and improve system reliability.
Design Considerations for Aluminum PCBs
When designing aluminum PCBs, several factors must be considered to ensure optimal performance and reliability:
-
Thermal Management: The thermal conductivity of the dielectric layer and the thickness of the aluminum substrate must be carefully selected based on the specific application and power requirements.
-
Coefficient of Thermal Expansion (CTE): The CTE of the aluminum substrate, dielectric layer, and copper layer should be closely matched to prevent warping and delamination due to temperature changes.
-
Electrical Isolation: The dielectric layer must provide sufficient electrical isolation between the aluminum substrate and the copper circuit layer to prevent short circuits and ensure proper functioning of the electronic components.
-
Mechanical Stress: The design should account for mechanical stress caused by the difference in CTE between the aluminum substrate and the electronic components, which can lead to solder joint failure or component cracking.
-
Manufacturing Constraints: The design must adhere to the manufacturing constraints of aluminum PCBs, such as minimum hole sizes, trace widths, and clearances, to ensure manufacturability and reliability.
Comparison of Aluminum PCBs with Other Thermal Management Solutions
Aluminum PCBs offer several advantages over other thermal management solutions:
Thermal Management Solution | Advantages | Disadvantages |
---|---|---|
Aluminum PCBs | Excellent thermal conductivity, lightweight, cost-effective, easy to manufacture | Limited flexibility in design, higher cost than traditional PCBs |
Heatsinks | Can be used with traditional PCBs, wide range of sizes and shapes available | Adds weight and size to the system, requires additional assembly |
Thermal Interface Materials | Easy to apply, suitable for various applications, can be used with traditional PCBs | Limited thermal conductivity compared to aluminum PCBs |
Ceramic Substrates | High thermal conductivity, excellent electrical insulation, suitable for high-temperature | Brittle, expensive, limited design flexibility |
Choosing the Right Aluminum PCB Manufacturer
When selecting an aluminum PCB manufacturer, consider the following factors:
-
Experience: Choose a manufacturer with extensive experience in producing aluminum PCBs for various applications.
-
Quality Control: Ensure that the manufacturer has strict quality control processes in place to guarantee the reliability and consistency of their products.
-
Technical Support: Look for a manufacturer that offers technical support and design assistance to help optimize your aluminum PCB design for manufacturability and performance.
-
Manufacturing Capabilities: Verify that the manufacturer has the necessary equipment and expertise to produce aluminum PCBs that meet your specific requirements, such as layer count, material selection, and surface finish.
-
Certifications: Select a manufacturer that holds relevant certifications, such as ISO 9001, ISO 14001, and UL, to ensure that their processes and products meet industry standards.
Frequently Asked Questions (FAQ)
-
Q: What is the primary advantage of using aluminum PCBs over traditional PCBs?
A: The primary advantage of aluminum PCBs is their excellent thermal conductivity, which allows for efficient heat dissipation from electronic components, improving system reliability and longevity. -
Q: Can aluminum PCBs be used in applications that do not require significant heat dissipation?
A: While aluminum PCBs are primarily used in applications that generate significant heat, they can also be used in other applications where lightweight, durable, and cost-effective PCBs are required. -
Q: Are aluminum PCBs more expensive than traditional PCBs?
A: Yes, aluminum PCBs are generally more expensive than traditional PCBs due to the additional materials and manufacturing processes involved. However, they can be a cost-effective solution for applications that require efficient thermal management. -
Q: What is the role of the dielectric layer in aluminum PCBs?
A: The dielectric layer in aluminum PCBs provides electrical isolation between the aluminum substrate and the copper circuit layer while allowing for efficient heat transfer from the electronic components to the aluminum substrate. -
Q: Can aluminum PCBs be manufactured with multiple copper layers?
A: Yes, aluminum PCBs can be manufactured with multiple copper layers, depending on the specific design requirements and the capabilities of the manufacturer. However, the number of layers may be limited compared to traditional PCBs due to the thickness of the aluminum substrate and the dielectric layer.
In conclusion, aluminum PCBs provide an excellent solution for applications that require efficient thermal management, reliability, and durability. By understanding the structure, manufacturing process, and design considerations of aluminum PCBs, engineers and designers can make informed decisions when selecting the most suitable thermal management solution for their projects. Choosing the right aluminum PCB manufacturer is crucial to ensure the quality, performance, and reliability of the final product.
No responses yet