Introduction to Aluminum PCBs
Aluminum PCBs, also known as metal core PCBs (MCPCBs), are printed circuit boards that feature an aluminum substrate instead of the traditional FR-4 material. These PCBs are designed to offer superior thermal management and heat dissipation properties, making them ideal for applications that generate significant amounts of heat, such as high-power LEDs, power electronics, and automotive systems.
In this comprehensive guide, we will delve into the world of aluminum PCBs, exploring their construction, advantages, applications, and design considerations. By the end of this article, you will have a thorough understanding of aluminum PCBs and their role in modern electronics.
The Structure of Aluminum PCBs
Layers of an Aluminum PCB
An aluminum PCB consists of several layers that work together to provide excellent thermal management and electrical performance. The typical layers of an aluminum PCB include:
- Dielectric layer
- Copper foil
- Thermal insulation layer
- Aluminum substrate
- Protective coating
Layer | Function |
---|---|
Dielectric layer | Insulates the copper foil from the aluminum substrate and provides a surface for the copper traces |
Copper foil | Carries electrical signals and provides a conductive path for heat dissipation |
Thermal insulation | Ensures efficient heat transfer from the copper foil to the aluminum substrate while maintaining electrical isolation |
Aluminum substrate | Acts as a heat sink, quickly dissipating heat away from the components |
Protective coating | Shields the aluminum substrate from oxidation and corrosion, enhancing the PCB’s durability |
Aluminum Substrate Thickness and Thermal Conductivity
The thickness and thermal conductivity of the aluminum substrate play a crucial role in the overall thermal performance of an aluminum PCB. Thicker substrates offer better heat dissipation but may increase the overall weight and cost of the PCB. The following table compares the thermal conductivity of common PCB materials:
Material | Thermal Conductivity (W/mK) |
---|---|
Aluminum | 150-200 |
Copper | 385-400 |
FR-4 | 0.3-0.4 |
As evident from the table, aluminum has a significantly higher thermal conductivity compared to FR-4, making it an excellent choice for heat dissipation. However, it is important to note that the thermal conductivity of aluminum is lower than that of copper, which is often used for thermal vias and heat spreaders in aluminum PCBs.
Advantages of Aluminum PCBs
Superior Thermal Management
One of the primary advantages of aluminum PCBs is their exceptional thermal management capabilities. The aluminum substrate acts as a built-in heat sink, quickly transferring heat away from the components and distributing it evenly across the PCB. This helps to maintain a stable operating temperature, preventing component damage and extending the lifespan of the device.
Improved Power Handling Capacity
Aluminum PCBs can handle higher power densities compared to traditional FR-4 PCBs. The superior thermal conductivity of aluminum allows for better heat dissipation, enabling the use of high-power components without the risk of thermal damage. This makes aluminum PCBs ideal for power electronics applications, such as motor drives, inverters, and power supplies.
Enhanced Mechanical Strength and Durability
The aluminum substrate provides a robust and rigid base for the PCB, enhancing its mechanical strength and durability. Aluminum PCBs are less susceptible to warping, twisting, and bending compared to FR-4 PCBs, making them suitable for applications that require high mechanical stability, such as automotive electronics and industrial control systems.
Reduced Size and Weight
Aluminum PCBs can help reduce the overall size and weight of electronic devices. The excellent thermal management properties of aluminum allow for higher component densities, enabling designers to create more compact layouts. Additionally, the use of an aluminum substrate can eliminate the need for external heat sinks, further reducing the size and weight of the final product.
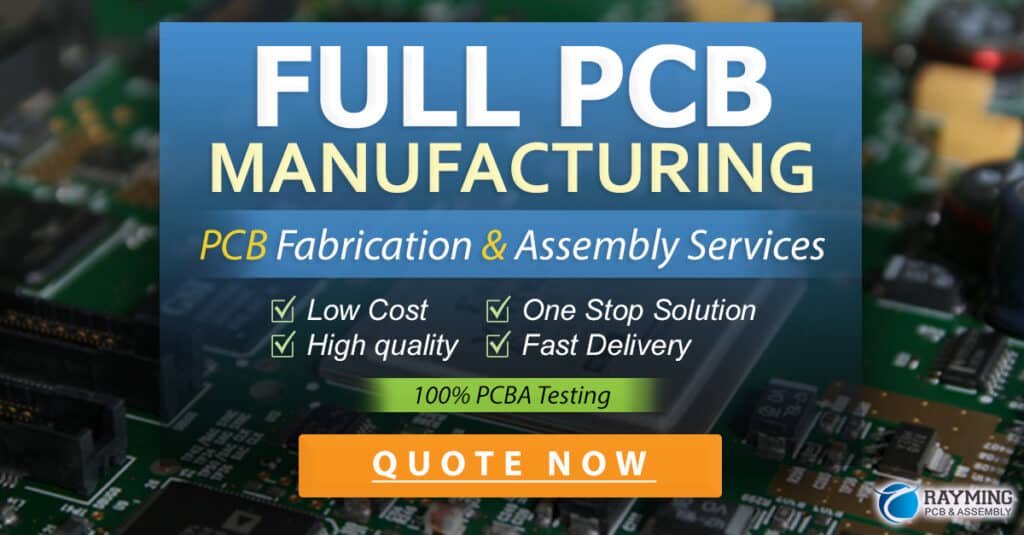
Applications of Aluminum PCBs
LED Lighting
Aluminum PCBs are widely used in LED lighting applications, particularly in high-power LED arrays. The superior thermal management capabilities of aluminum PCBs help to dissipate the heat generated by the LEDs, ensuring optimal performance and longevity. This is crucial for applications such as street lighting, stadium lighting, and automotive headlights, where reliable and efficient operation is essential.
Power Electronics
Power electronics applications, such as motor drives, inverters, and power supplies, can greatly benefit from the use of aluminum PCBs. The improved power handling capacity and thermal management properties of aluminum PCBs enable the design of more compact and efficient power electronic systems. This is particularly important in applications where space is limited, such as electric vehicles and renewable energy systems.
Automotive Electronics
Aluminum PCBs are increasingly being used in automotive electronics, where reliability and durability are paramount. The enhanced mechanical strength and thermal management capabilities of aluminum PCBs make them well-suited for applications such as engine control units, transmission control modules, and battery management systems. The use of aluminum PCBs can help improve the overall performance and lifespan of these critical automotive components.
Industrial Control Systems
Industrial control systems often operate in harsh environments and require robust and reliable electronics. Aluminum PCBs can provide the necessary mechanical stability and thermal management to ensure the proper functioning of these systems. Applications such as programmable logic controllers (PLCs), human-machine interfaces (HMIs), and industrial sensors can benefit from the use of aluminum PCBs, enhancing their durability and performance in demanding industrial settings.
Design Considerations for Aluminum PCBs
Thermal Management Design
When designing aluminum PCBs, it is essential to consider the thermal management aspects of the layout. The placement of components, the use of thermal vias, and the incorporation of heat spreaders should be carefully planned to ensure optimal heat dissipation. Thermal simulation tools can be used to analyze the thermal performance of the PCB and identify potential hot spots that may require additional cooling measures.
Dielectric Material Selection
The choice of dielectric material is crucial for aluminum PCBs, as it must provide adequate electrical insulation while allowing efficient heat transfer. Common dielectric materials used in aluminum PCBs include:
- Polyimide
- Epoxy
- Ceramic-filled polymers
Each material has its own set of properties, such as thermal conductivity, dielectric strength, and CTE (coefficient of thermal expansion). The selection of the dielectric material should be based on the specific requirements of the application, considering factors such as operating temperature, voltage, and mechanical stress.
Coefficient of Thermal Expansion (CTE) Matching
Matching the CTE of the aluminum substrate with that of the dielectric material and copper foil is essential to minimize thermal stresses and prevent delamination. Mismatched CTEs can lead to warping, cracking, and other reliability issues, particularly in applications with wide temperature ranges. The use of a suitable thermal insulation layer can help mitigate CTE mismatches and ensure the long-term reliability of the aluminum PCB.
Manufacturing Process Considerations
The manufacturing process for aluminum PCBs differs from that of traditional FR-4 PCBs, and it is important to consider these differences during the design phase. Some key manufacturing considerations include:
- Minimum trace width and spacing
- Hole drilling and plating
- Surface finish options
- Solder mask application
Working closely with the PCB manufacturer and understanding their capabilities and limitations can help ensure a successful aluminum PCB design and manufacturing process.
FAQ
-
Q: What are the main differences between aluminum PCBs and traditional FR-4 PCBs?
A: Aluminum PCBs feature an aluminum substrate instead of the FR-4 material used in traditional PCBs. This provides superior thermal management, improved power handling capacity, and enhanced mechanical strength. Aluminum PCBs are better suited for applications that generate significant amounts of heat or require high reliability in demanding environments. -
Q: Can aluminum PCBs be used for high-frequency applications?
A: While aluminum PCBs offer excellent thermal management and mechanical properties, they may not be the best choice for high-frequency applications. The dielectric materials used in aluminum PCBs typically have higher dielectric constants and loss tangents compared to materials used in high-frequency FR-4 PCBs, which can lead to signal integrity issues at higher frequencies. -
Q: Are aluminum PCBs more expensive than FR-4 PCBs?
A: Yes, aluminum PCBs are generally more expensive than FR-4 PCBs due to the cost of the aluminum substrate and the specialized manufacturing processes required. However, the increased cost can be justified in applications where the superior thermal management and mechanical properties of aluminum PCBs are necessary. -
Q: How do I choose the right dielectric material for my aluminum PCB?
A: The choice of dielectric material depends on the specific requirements of your application. Factors to consider include the operating temperature range, voltage requirements, thermal conductivity, and CTE matching with the aluminum substrate. Consult with your PCB manufacturer and material suppliers to select the most suitable dielectric material for your project. -
Q: Can aluminum PCBs be used in flexible electronics applications?
A: While aluminum PCBs are known for their rigidity and mechanical strength, they can be used in certain flexible electronics applications. Thin aluminum substrates can provide a balance between flexibility and thermal management. However, for highly flexible applications, other substrate materials, such as polyimide or polyester, may be more suitable.
Conclusion
Aluminum PCBs offer a range of benefits over traditional FR-4 PCBs, including superior thermal management, improved power handling capacity, enhanced mechanical strength, and reduced size and weight. These advantages make aluminum PCBs an attractive choice for applications in LED lighting, power electronics, automotive systems, and industrial control.
When designing aluminum PCBs, it is crucial to consider factors such as thermal management, dielectric material selection, CTE matching, and manufacturing process requirements. By carefully addressing these design considerations and working closely with PCB manufacturers, engineers can unlock the full potential of aluminum PCBs and create reliable, high-performance electronic systems.
As technology continues to advance and the demand for efficient, compact, and robust electronics grows, aluminum PCBs will likely play an increasingly important role in shaping the future of the electronics industry.
No responses yet