What is an MCPCB?
A Metal Core Printed Circuit Board (MCPCB) is a specialized type of PCB that uses a metal base as its core instead of the traditional FR-4 material. The metal core, usually made of aluminum, provides excellent thermal conductivity, allowing for efficient heat dissipation from high-power components such as LEDs, power amplifiers, and motor drivers. MCPCBs are widely used in applications that require effective thermal management to ensure optimal performance and longevity of the electronic components.
Advantages of MCPCBs
- Enhanced thermal management
- Improved reliability and lifespan
- Reduced size and weight
- Cost-effective solution for high-power applications
MCPCB Structure and Materials
An MCPCB typically consists of three main layers:
1. Dielectric Layer: A thin, electrically insulating layer that separates the metal core from the copper circuit layer. Common dielectric materials include:
– Alumina (Al2O3)
– Aluminum Nitride (AlN)
– Boron Nitride (BN)
2. Metal Core: The base of the MCPCB, usually made of aluminum alloy (e.g., 5052, 6061). Other metals, such as copper or steel, may be used for specific applications.
3. Copper Circuit Layer: The top layer where the electronic components are mounted and the circuits are etched. The copper thickness typically ranges from 1 oz to 10 oz.
Comparison of Dielectric Materials
Material | Thermal Conductivity (W/mK) | Dielectric Strength (kV/mm) | Relative Cost |
---|---|---|---|
Al2O3 | 20-30 | 10-20 | Low |
AlN | 150-180 | 15-20 | High |
BN | 250-300 | 40-50 | Very High |
MCPCB Manufacturing Process
The manufacturing process of MCPCBs involves several steps:
1. Cleaning and surface preparation of the metal core
2. Application of the dielectric layer through various methods:
– Thermal bonding
– Electrophoretic deposition (EPD)
– Direct bonding copper (DBC)
3. Lamination of the copper foil onto the dielectric layer
4. Photolithography and etching to create the desired circuit pattern
5. Surface finish application (e.g., ENIG, OSP, HASL)
6. Electrical testing and quality control
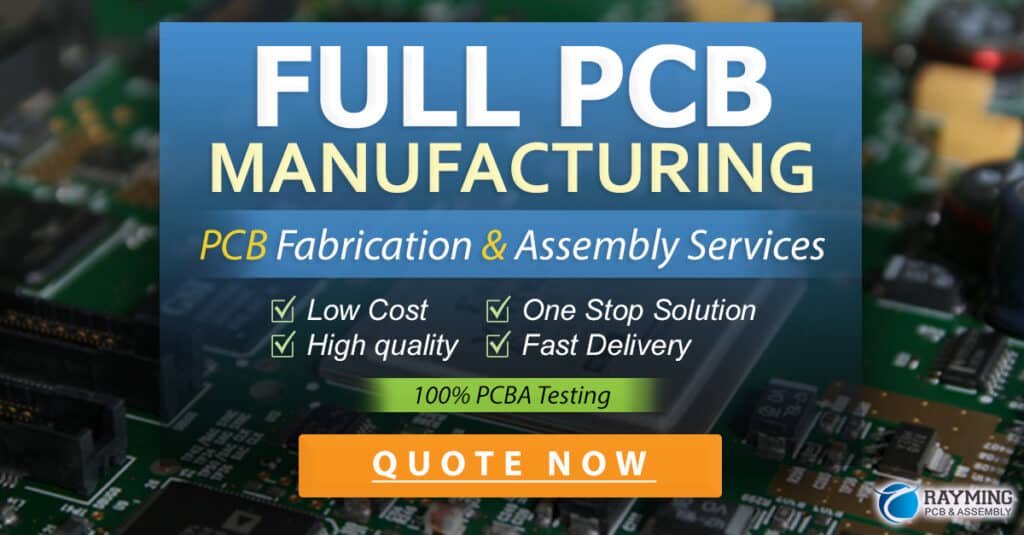
Applications of MCPCBs
MCPCBs are used in various industries and applications that require efficient thermal management:
1. LED lighting (e.g., street lights, automotive headlights)
2. Power electronics (e.g., motor drives, inverters)
3. Telecommunications (e.g., base stations, RF amplifiers)
4. Automotive electronics (e.g., ECUs, sensors)
5. Medical devices (e.g., X-ray machines, MRI scanners)
Case Study: LED Street Lighting
LED street lights have gained popularity due to their energy efficiency and long lifespan. However, LEDs generate a significant amount of heat that must be dissipated effectively to ensure optimal performance and reliability. MCPCBs provide an ideal solution for LED street light applications by offering:
– Excellent thermal conductivity to dissipate heat from the LEDs
– Compact design to fit within the limited space of the light fixture
– Cost-effectiveness compared to other thermal management solutions
By using MCPCBs, LED street lights can maintain a stable operating temperature, leading to improved luminous efficiency, color consistency, and a longer lifespan.
Design Considerations for MCPCBs
When designing an MCPCB, several factors must be considered to ensure optimal performance and reliability:
1. Thermal management:
– Select the appropriate dielectric material based on thermal conductivity requirements
– Optimize the metal core thickness and design for efficient heat dissipation
– Consider the use of thermal vias to enhance heat transfer
2. Electrical performance:
– Choose the appropriate copper thickness based on current carrying requirements
– Ensure proper isolation between the metal core and the copper circuit layer
– Minimize the impact of the metal core on signal integrity and EMI
3. Mechanical strength:
– Select the appropriate metal core alloy based on mechanical requirements
– Consider the thermal expansion mismatch between the layers and its impact on reliability
– Optimize the MCPCB design to minimize stress and warpage
Thermal Simulation and Analysis
Thermal simulation and analysis tools (e.g., ANSYS, COMSOL) play a crucial role in optimizing the thermal performance of MCPCBs. These tools allow designers to:
– Predict the temperature distribution across the MCPCB
– Identify hot spots and thermal bottlenecks
– Evaluate the effectiveness of different cooling solutions (e.g., heatsinks, forced air cooling)
– Optimize the MCPCB layout and component placement for better thermal management
By leveraging thermal simulation and analysis, designers can create MCPCBs that meet the thermal requirements of the application while minimizing the development time and cost.
Future Trends in MCPCB Technology
As electronic devices continue to become more compact and powerful, the demand for advanced thermal management solutions like MCPCBs will continue to grow. Some of the future trends in MCPCB technology include:
1. Advanced dielectric materials with higher thermal conductivity and lower thermal expansion mismatch
2. Integration of active cooling solutions (e.g., thermoelectric coolers, micro-channel heat sinks) into MCPCBs
3. Development of multi-layer MCPCBs for improved thermal performance and circuit density
4. Adoption of additive manufacturing techniques (e.g., 3D printing) for rapid prototyping and customization of MCPCBs
5. Increased use of MCPCBs in emerging applications such as electric vehicles, 5G networks, and high-performance computing
Frequently Asked Questions (FAQ)
- What is the difference between an MCPCB and a standard PCB?
-
An MCPCB uses a metal core (usually aluminum) as its base, while a standard PCB uses an FR-4 material. The metal core provides better thermal conductivity, allowing for more efficient heat dissipation from high-power components.
-
Can MCPCBs be used for all electronic applications?
-
While MCPCBs offer excellent thermal management, they may not be suitable for all applications. MCPCBs are best suited for high-power applications that generate significant heat, such as LED lighting, power electronics, and telecommunications equipment.
-
What are the most common dielectric materials used in MCPCBs?
-
The most common dielectric materials used in MCPCBs are alumina (Al2O3), aluminum nitride (AlN), and boron nitride (BN). Each material has its own advantages in terms of thermal conductivity, dielectric strength, and cost.
-
How does the metal core affect the electrical performance of an MCPCB?
-
The metal core can potentially impact the electrical performance of an MCPCB by affecting signal integrity and electromagnetic interference (EMI). Proper design considerations, such as ensuring adequate isolation between the metal core and the copper circuit layer, can help minimize these effects.
-
Are MCPCBs more expensive than standard PCBs?
- MCPCBs are generally more expensive than standard PCBs due to the additional materials (e.g., metal core, dielectric layer) and specialized manufacturing processes involved. However, for high-power applications that require efficient thermal management, MCPCBs can be a cost-effective solution compared to other cooling methods.
In conclusion, Metal Core PCBs (MCPCBs) offer a powerful solution for electronic applications that require efficient thermal management. By combining the thermal conductivity of a metal core with the electrical functionality of a PCB, MCPCBs enable the development of compact, reliable, and high-performance electronic devices. As the demand for advanced thermal management solutions continues to grow, MCPCBs are poised to play an increasingly important role in shaping the future of electronics across various industries.
No responses yet