What is PCBA?
PCBA stands for Printed Circuit Board Assembly, which is the process of assembling electronic components onto a printed circuit board (PCB) to create a functional electronic device. A PCB is a flat board made of insulating material, such as fiberglass or plastic, with conductive tracks, pads, and other features etched onto its surface. The electronic components, such as resistors, capacitors, integrated circuits, and connectors, are soldered onto the PCB to create the desired electronic circuit.
PCBA is a crucial process in the manufacturing of electronic devices, as it determines the functionality, reliability, and quality of the final product. It involves several steps, including component placement, soldering, inspection, and testing, which are performed using specialized equipment and techniques.
Types of PCBA
There are several types of PCBA, each with its own characteristics and applications. The most common types are:
1. Surface Mount Technology (SMT) Assembly
SMT assembly is a method of mounting electronic components directly onto the surface of a PCB. The components are smaller and lighter than those used in through-hole assembly, and they have flat contacts or leads that are soldered onto the PCB’s pads. SMT assembly is widely used in the production of high-density, compact electronic devices, such as smartphones, tablets, and wearables.
2. Through-Hole Technology (THT) Assembly
THT assembly involves inserting the leads of electronic components through holes drilled in the PCB and soldering them to the opposite side. This method is older and less efficient than SMT assembly, but it is still used for larger components, such as connectors and transformers, or in applications that require higher mechanical strength or heat dissipation.
3. Mixed Technology Assembly
Mixed technology assembly combines SMT and THT assembly methods on the same PCB. This approach is used when a device requires both types of components, such as a smartphone with a USB connector or a power supply with through-hole capacitors.
4. Flexible Circuit Assembly
Flexible circuit assembly involves mounting electronic components onto a flexible PCB made of thin, bendable materials, such as polyimide or polyester. Flexible circuits are used in applications that require the PCB to conform to a specific shape or to withstand repeated bending, such as in wearable devices, medical implants, or aerospace systems.
5. Rigid-Flex Circuit Assembly
Rigid-flex circuit assembly combines rigid and flexible PCBs into a single assembly. The rigid sections provide mechanical support and stability, while the flexible sections allow the circuit to bend or fold as needed. Rigid-flex circuits are used in applications that require both flexibility and durability, such as in automotive electronics, industrial controls, or military equipment.
Applications of PCBA
PCBA is used in a wide range of industries and applications, from consumer electronics to aerospace and defense. Some of the most common applications include:
1. Consumer Electronics
PCBA is the foundation of most consumer electronic devices, such as smartphones, tablets, laptops, televisions, and home appliances. These devices require high-density, compact PCBs with a large number of components and complex circuits.
2. Automotive Electronics
Modern vehicles rely heavily on electronic systems for engine control, safety, entertainment, and communication. PCBA is used in various automotive applications, such as engine control units (ECUs), infotainment systems, sensors, and power management modules.
3. Medical Devices
PCBA is essential in the production of medical devices, such as monitoring equipment, diagnostic tools, and implantable devices. These applications require high reliability, precision, and biocompatibility, as well as compliance with strict regulatory standards.
4. Industrial Automation
PCBA is used in various industrial automation systems, such as programmable logic controllers (PLCs), human-machine interfaces (HMIs), sensors, and actuators. These applications require rugged, reliable PCBs that can withstand harsh environments and operate continuously.
5. Aerospace and Defense
PCBA is critical in the production of aerospace and defense systems, such as avionics, radar, communication equipment, and weapon systems. These applications require high performance, reliability, and resistance to extreme conditions, such as high altitudes, temperatures, and vibrations.
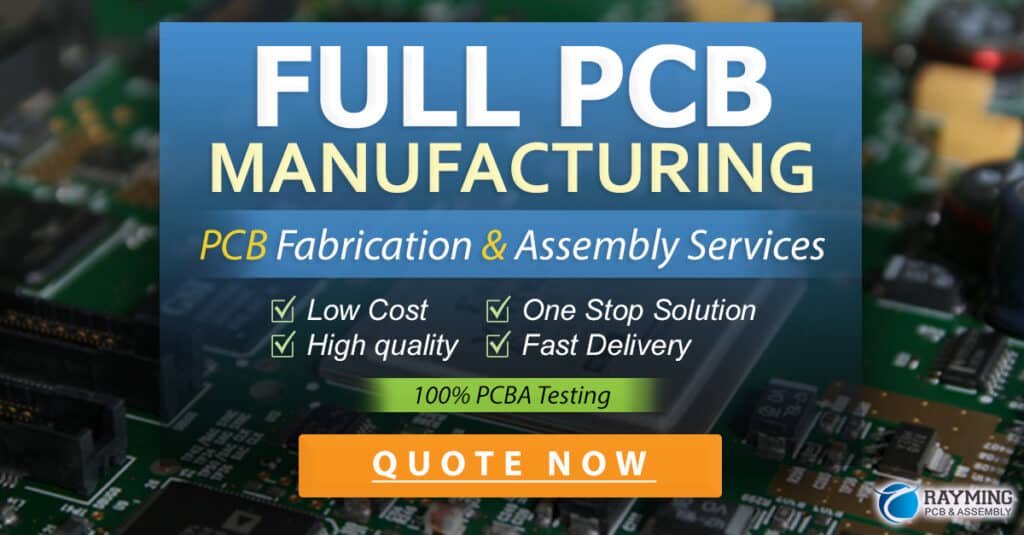
PCBA Process
The PCBA process involves several steps, each of which must be performed with precision and care to ensure the quality and reliability of the final product. The main steps in the PCBA process are:
1. PCB Design and Fabrication
The first step in the PCBA process is to design and fabricate the PCB. This involves creating a schematic diagram of the electronic circuit, laying out the components and tracks on the PCB, and generating the necessary files for manufacturing. The PCB is then fabricated using various methods, such as etching, drilling, and plating, depending on the complexity and requirements of the design.
2. Component Placement
Once the PCB is fabricated, the electronic components are placed onto its surface using automated pick-and-place machines or manual methods, depending on the type and quantity of components. The machines use computer vision and precision nozzles to pick up the components from reels or trays and place them accurately onto the PCB’s pads.
3. Soldering
After the components are placed, they are soldered onto the PCB using various methods, such as reflow soldering, wave soldering, or hand soldering. Reflow soldering is the most common method for SMT assembly, which involves applying solder paste onto the PCB’s pads, placing the components, and heating the assembly in an oven to melt the solder and form the connections. Wave soldering is used for THT assembly, where the PCB is passed over a wave of molten solder to coat the component leads and holes.
4. Inspection and Testing
After soldering, the PCBA undergoes various inspection and testing procedures to ensure its quality and functionality. These may include:
- Visual inspection: A manual or automated visual inspection of the PCBA to check for defects, such as missing or misaligned components, solder bridges, or contamination.
- Automated Optical Inspection (AOI): An automated inspection using cameras and image processing software to detect surface-level defects.
- X-ray inspection: An inspection using X-ray imaging to detect hidden defects, such as voids or cracks in the solder joints.
- In-Circuit Testing (ICT): A functional test using a bed-of-nails fixture to verify the electrical continuity and performance of the PCBA.
- Functional Testing: A test of the PCBA’s operation and functionality under real-world conditions, such as power-on, signal injection, or environmental stress.
5. Conformal Coating and Potting
In some applications, the PCBA may require additional protection against moisture, dust, or other environmental factors. This can be achieved by applying a conformal coating, which is a thin layer of insulating material, such as acrylic, silicone, or polyurethane, onto the surface of the PCBA. Alternatively, the PCBA can be potted, which involves encapsulating it in a solid compound, such as epoxy or silicone, to provide mechanical support and insulation.
6. Final Assembly and Packaging
After all the processing and testing steps are completed, the PCBA is ready for final assembly and packaging. This may involve installing the PCBA into a housing or enclosure, connecting it to other components or subsystems, and packaging it for shipping or storage. The final product is then subjected to additional testing and quality control procedures to ensure its performance and reliability.
Advantages of PCBA
PCBA offers several advantages over other Electronic Assembly methods, such as point-to-point wiring or breadboarding. Some of the main advantages of PCBA include:
1. Miniaturization
PCBA allows for the creation of compact, high-density electronic circuits with a large number of components in a small space. This is especially important in applications that require miniaturization, such as portable devices, wearables, or implantable medical devices.
2. Reliability
PCBA provides a reliable and consistent method of interconnecting electronic components, with a low risk of errors or failures. The use of automated assembly processes and rigorous testing procedures ensures that the PCBA meets the required quality and performance standards.
3. Cost-Effectiveness
PCBA is a cost-effective method of producing electronic assemblies in large quantities. The use of automated assembly equipment and standardized components reduces the labor and material costs, while the high yield and low defect rates minimize the need for rework or scrap.
4. Flexibility
PCBA allows for a wide range of design options and customization possibilities, from simple single-layer boards to complex multi-layer assemblies with mixed technologies. The use of computer-aided design (CAD) tools and rapid prototyping methods enables fast and efficient product development and iteration.
5. Scalability
PCBA is a scalable technology that can be adapted to different production volumes and requirements, from small batches to mass production. The use of modular design approaches and standardized processes enables the easy scaling up or down of production as needed.
Challenges and Considerations in PCBA
Despite its many advantages, PCBA also presents some challenges and considerations that must be addressed to ensure a successful and reliable assembly. Some of the main challenges and considerations in PCBA include:
1. Design for Manufacturability (DFM)
DFM is the practice of designing the PCB and components in a way that facilitates their efficient and reliable assembly. This involves considering factors such as component placement, orientation, spacing, and accessibility, as well as the compatibility and availability of materials and processes. A good DFM approach can help to minimize assembly defects, improve yield, and reduce costs.
2. Component Selection and Sourcing
The selection and sourcing of components is a critical factor in PCBA, as it affects the quality, reliability, and cost of the final product. It is important to choose components that meet the required specifications and standards, and to ensure their availability and consistency of supply. The use of counterfeit or substandard components can lead to assembly failures, performance issues, and legal liabilities.
3. Process Control and Optimization
The PCBA process involves many variables and parameters that must be carefully controlled and optimized to achieve the desired results. This includes factors such as solder paste printing, component placement accuracy, reflow temperature profiles, and cleaning and inspection procedures. The use of statistical process control (SPC) methods and continuous improvement initiatives can help to identify and eliminate sources of variation and waste.
4. Environmental and Regulatory Compliance
PCBA is subject to various environmental and regulatory requirements, such as the Restriction of Hazardous Substances (RoHS) directive, the Waste Electrical and Electronic Equipment (WEEE) directive, and the Registration, Evaluation, Authorization, and Restriction of Chemicals (REACH) regulation. These requirements impose restrictions on the use of certain materials and substances, as well as obligations for the collection, treatment, and disposal of electronic waste. Compliance with these requirements is essential to avoid legal and reputational risks, as well as to meet customer and market demands for sustainable and responsible products.
5. Supply Chain Management
PCBA involves a complex and global supply chain, with components, materials, and services sourced from multiple suppliers and locations. Effective supply chain management is essential to ensure the timely and reliable delivery of high-quality products, as well as to minimize risks and disruptions. This involves establishing strong partnerships with suppliers, implementing robust quality and logistics processes, and maintaining visibility and traceability throughout the supply chain.
Table of PCBA types
PCBA Type | Characteristics | Applications |
---|---|---|
Surface Mount Technology | High density, compact, flat contacts | Smartphones, tablets, wearables |
Through-Hole Technology | Larger components, higher mechanical strength, heat dissipation | Connectors, transformers, power supplies |
Mixed Technology | Combines SMT and THT on the same PCB | Devices with both SMT and THT components |
Flexible Circuit | Thin, bendable materials, conforms to specific shapes | Wearable devices, medical implants, aerospace systems |
Rigid-Flex Circuit | Combines rigid and flexible PCBs, provides support and flexibility | Automotive electronics, industrial controls, military equipment |
Table of PCBA applications
Application | Description | Requirements |
---|---|---|
Consumer Electronics | Smartphones, tablets, laptops, TVs, home appliances | High density, compact PCBs, complex circuits |
Automotive Electronics | Engine control units, infotainment systems, sensors | Rugged, reliable PCBs, compliance with automotive standards |
Medical Devices | Monitoring equipment, diagnostic tools, implantable devices | High reliability, precision, biocompatibility, regulatory compliance |
Industrial Automation | PLCs, HMIs, sensors, actuators | Rugged, reliable PCBs, continuous operation in harsh environments |
Aerospace and Defense | Avionics, radar, communication equipment, weapon systems | High performance, reliability, resistance to extreme conditions |
Frequently Asked Questions (FAQ)
1. What is the difference between PCB and PCBA?
A PCB (Printed Circuit Board) is the bare board with the conductive tracks and pads, but without any components mounted on it. PCBA (Printed Circuit Board Assembly) is the complete assembly of the PCB with all the electronic components soldered onto it, ready for use in an electronic device.
2. What are the main steps in the PCBA process?
The main steps in the PCBA process are:
- PCB design and fabrication
- Component placement
- Soldering
- Inspection and testing
- Conformal coating and potting (if required)
- Final assembly and packaging
3. What are the advantages of using SMT assembly over THT assembly?
SMT (Surface Mount Technology) assembly offers several advantages over THT (Through-Hole Technology) assembly, including:
- Higher component density and smaller board size
- Faster and more automated assembly process
- Lower cost and higher yield
- Better electrical performance and signal integrity
- Easier to design for high-frequency and high-speed applications
4. What are some common defects that can occur in PCBA?
Some common defects that can occur in PCBA include:
- Solder bridges, balls, or splashes
- Cold or insufficient solder joints
- Tombstoning or lifting of components
- Misaligned or missing components
- Damaged or burnt components
- Contamination or residue on the board
- Incorrect or missing markings or labels
5. How can I ensure the quality and reliability of my PCBA?
To ensure the quality and reliability of your PCBA, you should:
- Follow good design for manufacturability (DFM) practices
- Select high-quality and reliable components from reputable suppliers
- Use appropriate assembly processes and materials for your application
- Implement rigorous inspection and testing procedures at every stage of the process
- Maintain strict process control and continuous improvement efforts
- Comply with relevant environmental and regulatory requirements
- Establish a robust supply chain management system with full traceability and accountability
By following these guidelines and best practices, you can achieve a high-quality and reliable PCBA that meets your performance, cost, and sustainability objectives.
No responses yet