Understanding Electronic Assembly
Before diving into the specifics of choosing an electronic assembly service, it’s important to understand what electronic assembly entails. Electronic assembly is the process of combining various electronic components, such as printed circuit boards (PCBs), resistors, capacitors, and integrated circuits, to create a functional electronic device or system.
Types of Electronic Assembly
There are several types of electronic assembly, each with its own unique characteristics and applications:
-
Through-Hole Assembly (THA): This traditional method involves inserting component leads through holes in a PCB and soldering them on the opposite side.
-
Surface Mount Assembly (SMT): SMT is a more modern approach where components are placed directly onto the surface of a PCB and soldered using automated equipment.
-
Mixed Assembly: Some electronic devices require a combination of both through-hole and surface mount components, known as mixed assembly.
Advantages of Outsourcing Electronic Assembly
Outsourcing electronic assembly to a specialized service provider offers several benefits:
-
Cost Savings: Outsourcing eliminates the need for in-house equipment, skilled labor, and inventory management, reducing overall costs.
-
Faster Time-to-Market: Electronic assembly service providers have streamlined processes and advanced equipment, enabling faster production and shorter lead times.
-
Access to Expertise: Specialized assembly service providers have the knowledge and experience to handle complex projects and ensure high-quality results.
-
Scalability: Outsourcing allows businesses to scale production up or down based on demand, without investing in additional resources.
Key Factors to Consider When Choosing an Electronic Assembly Service
When selecting an electronic assembly service provider, there are several critical factors to keep in mind:
1. Technical Capabilities
Evaluate the service provider’s technical capabilities to ensure they can handle your specific project requirements. Consider the following:
- Equipment and Technology: Assess the provider’s manufacturing equipment and technology to ensure they have the necessary tools to produce your electronic assemblies efficiently and accurately.
- Process Capabilities: Determine if the provider has experience with the specific assembly processes required for your project, such as through-hole, surface mount, or mixed assembly.
- Certifications and Standards: Look for providers with relevant industry certifications, such as ISO 9001, IPC-A-610, or J-STD-001, to ensure they adhere to strict quality standards.
2. Quality Control and Testing
A robust quality control and testing process is essential to ensure the reliability and performance of your electronic assemblies. Consider the following:
- Quality Management System (QMS): Evaluate the provider’s QMS to ensure they have well-defined processes for quality control, documentation, and continuous improvement.
- Inspection and Testing: Inquire about the provider’s inspection and testing procedures, including automated optical inspection (AOI), in-circuit testing (ICT), and functional testing.
- Traceability: Ensure the provider has systems in place to track components, processes, and finished products throughout the manufacturing process.
3. Experience and Expertise
Choose a provider with extensive experience and expertise in electronic assembly:
- Industry Experience: Look for providers with experience in your specific industry, such as automotive, medical, or aerospace, to ensure they understand your unique requirements and regulations.
- Project Portfolio: Review the provider’s project portfolio to gauge their experience with projects similar in scope and complexity to yours.
- Engineering Support: Assess the provider’s engineering capabilities and their ability to provide design for manufacturability (DFM) recommendations and support throughout the project lifecycle.
4. Communication and Collaboration
Effective communication and collaboration are key to a successful electronic assembly partnership:
- Responsiveness: Evaluate the provider’s responsiveness to inquiries, requests for quotes, and project updates.
- Project Management: Ensure the provider has a dedicated project management team to oversee your project, facilitate communication, and address any issues that may arise.
- Intellectual Property (IP) Protection: Discuss the provider’s measures for protecting your IP, including non-disclosure agreements (NDAs) and secure data handling procedures.
5. Supply Chain Management
A reliable and efficient supply chain is crucial for ensuring timely delivery and minimizing disruptions:
- Component Sourcing: Evaluate the provider’s component sourcing capabilities, including their relationships with suppliers and their ability to secure hard-to-find or obsolete components.
- Inventory Management: Inquire about the provider’s inventory management practices, including their ability to handle consignment inventory or vendor-managed inventory (VMI) programs.
- Lead Times: Discuss the provider’s typical lead times and their ability to accommodate rush orders or changes in production schedules.
6. Pricing and Value
While cost is an important consideration, it should not be the sole deciding factor when choosing an electronic assembly service provider:
- Competitive Pricing: Compare quotes from multiple providers to ensure you are getting a competitive price for the services offered.
- Value-Added Services: Consider the value-added services offered by the provider, such as design support, prototyping, or post-assembly services, which can enhance the overall value of the partnership.
- Total Cost of Ownership (TCO): Evaluate the TCO, including factors such as quality, reliability, and long-term support, rather than focusing solely on the initial assembly cost.
Evaluating and Selecting an Electronic Assembly Service Provider
Now that you understand the key factors to consider, it’s time to evaluate and select an electronic assembly service provider:
1. Request for Quote (RFQ)
Prepare a detailed RFQ that includes the following information:
- Project scope and specifications
- Required certifications and standards
- Quality control and testing requirements
- Delivery schedules and lead times
- Intellectual property and confidentiality requirements
Send the RFQ to multiple service providers to compare their offerings and pricing.
2. Evaluate Responses
Carefully review the responses from each service provider, considering the following:
- Technical capabilities and experience
- Quality control and testing procedures
- Communication and project management approach
- Supply chain management and lead times
- Pricing and value-added services
Create a comparison matrix to help you evaluate each provider based on the key factors discussed earlier.
3. Conduct Site Visits and Audits
Before making a final decision, consider conducting site visits and audits of the top contenders:
- Tour the manufacturing facility to assess the equipment, processes, and working conditions.
- Meet with the project management and engineering teams to discuss your project in detail and gauge their expertise and communication skills.
- Review quality control documentation, certifications, and testing procedures to ensure they meet your requirements.
4. Make a Selection
Based on your evaluation and site visits, select the electronic assembly service provider that best meets your needs and aligns with your business objectives. Consider entering into a long-term partnership to foster collaboration, continuous improvement, and mutual success.
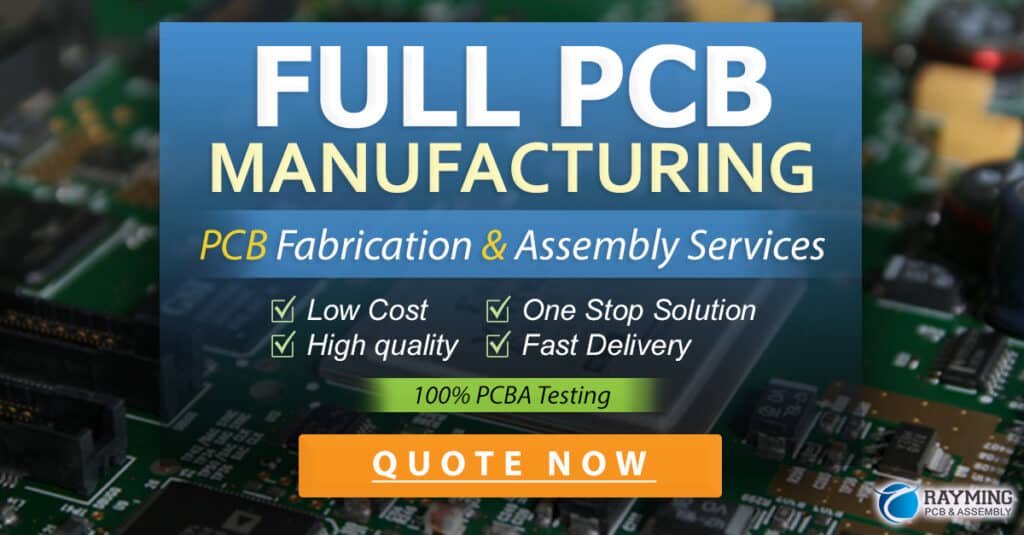
Frequently Asked Questions (FAQ)
-
Q: How long does it typically take to complete an electronic assembly project?
A: The timeline for an electronic assembly project varies depending on factors such as project complexity, component availability, and production volume. Generally, lead times can range from a few weeks to several months. It’s essential to discuss your specific project requirements and timelines with potential service providers during the RFQ process. -
Q: What certifications should I look for in an electronic assembly service provider?
A: Some of the most common and important certifications for electronic assembly service providers include: - ISO 9001: Quality Management Systems
- IPC-A-610: Acceptability of Electronic Assemblies
- J-STD-001: Requirements for Soldered Electrical and Electronic Assemblies
- IPC-A-620: Requirements and Acceptance for Cable and Wire Harness Assemblies
-
AS9100: Quality Management Systems – Requirements for Aviation, Space, and Defense Organizations
-
Q: How can I ensure the protection of my intellectual property when outsourcing electronic assembly?
A: To protect your intellectual property, take the following steps: - Sign a non-disclosure agreement (NDA) with the service provider before sharing any sensitive information.
- Discuss the provider’s data security measures and protocols for handling confidential information.
- Limit access to sensitive information to only those directly involved in the project.
-
Consider filing for patents, trademarks, or copyrights to protect your IP.
-
Q: What should I include in my RFQ to ensure I receive accurate and comprehensive quotes?
A: Your RFQ should include the following information: - Detailed project scope and specifications, including bill of materials (BOM) and Gerber files
- Required certifications and quality standards
- Quality control and testing requirements
- Delivery schedules and lead time expectations
- Intellectual property and confidentiality requirements
-
Any additional services required, such as design support or prototyping
-
Q: How can I manage the risks associated with outsourcing electronic assembly?
A: To manage the risks associated with outsourcing electronic assembly, consider the following: - Conduct thorough due diligence on potential service providers, including evaluating their financial stability, reputation, and track record.
- Establish clear communication channels and project management processes to ensure transparency and accountability.
- Implement quality control measures and regularly monitor the provider’s performance.
- Diversify your supply chain by working with multiple providers or maintaining alternative sources for critical components.
- Maintain adequate insurance coverage to protect against potential losses or liabilities.
Factor | Considerations |
---|---|
Technical Capabilities | – Equipment and technology – Process capabilities – Certifications and standards |
Quality Control and Testing | – Quality Management System (QMS) – Inspection and testing procedures – Traceability |
Experience and Expertise | – Industry experience – Project portfolio – Engineering support |
Communication and Collaboration | – Responsiveness – Project management – Intellectual property protection |
Supply Chain Management | – Component sourcing – Inventory management – Lead times |
Pricing and Value | – Competitive pricing – Value-added services – Total Cost of Ownership (TCO) |
Conclusion
Choosing the best electronic assembly service provider is a critical decision that can significantly impact the success of your product and business. By understanding the key factors to consider, such as technical capabilities, quality control, expertise, communication, supply chain management, and pricing, you can make an informed decision and select a partner that aligns with your goals and requirements.
Remember to conduct thorough evaluations, including RFQs, site visits, and audits, to ensure you choose a provider that can deliver high-quality results, reliable service, and long-term value. By fostering a strong partnership built on trust, communication, and continuous improvement, you can streamline your electronic assembly process, reduce risks, and achieve your business objectives.
No responses yet