Introduction to Purple PCBs
Purple PCBs, also known as printed circuit boards with a purple solder mask, have gained popularity in recent years due to their unique appearance and potential benefits. In this article, we will explore the world of purple PCBs, discussing their characteristics, advantages, manufacturing process, and applications.
What is a Purple PCB?
A purple PCB is a printed circuit board that features a purple-colored solder mask. The solder mask is a protective layer applied to the copper traces on the PCB, preventing short circuits and providing insulation. While green is the most common color for solder masks, purple has emerged as an attractive alternative.
Advantages of Purple PCBs
Purple PCBs offer several advantages over traditional green PCBs:
- Aesthetics: The distinctive purple color adds a unique and visually appealing aspect to the PCB, making it stand out from the standard green boards.
- Improved Contrast: The purple solder mask provides better contrast against the white silkscreen and copper traces, enhancing the visibility of components and labels on the board.
- UV Resistance: Purple solder masks have shown excellent resistance to ultraviolet (UV) light, reducing the risk of degradation and discoloration over time.
- Reduced Eye Strain: The softer hue of purple is considered more eye-friendly compared to the bright green of traditional PCBs, potentially reducing eye strain during prolonged inspection or assembly processes.
Manufacturing Process of Purple PCBs
The manufacturing process of purple PCBs is similar to that of other colored PCBs, with a few specific considerations:
PCB fabrication Steps
- Design: The PCB design is created using specialized software, such as Altium Designer or KiCad, taking into account the specific requirements of the project.
- Printing: The PCB design is printed onto a copper-clad laminate using a photoresist process, which involves applying a light-sensitive film and exposing it to UV light to transfer the pattern.
- Etching: The unwanted copper is removed through an etching process, leaving only the desired copper traces on the board.
- Drilling: Holes are drilled into the PCB to accommodate through-hole components and vias.
- Solder Mask Application: The purple solder mask is applied to the PCB using a silkscreen printing process or a photoimageable solder mask (LPSM) technique.
- Surface Finish: A surface finish, such as HASL (Hot Air Solder Leveling) or ENIG (Electroless Nickel Immersion Gold), is applied to protect the exposed copper and enhance solderability.
- Silkscreen Printing: The white silkscreen legend, which includes component labels and other markings, is printed onto the purple solder mask.
- Electrical Testing: The PCB undergoes electrical testing to ensure proper functionality and adherence to specifications.
Considerations for Purple Solder Mask
When manufacturing purple PCBs, there are a few factors to consider:
- Solder Mask Material: Ensure that the solder mask material is compatible with the purple pigment and provides the desired properties, such as UV resistance and durability.
- Color Consistency: Maintain consistent color quality throughout the manufacturing process to avoid variations in the final product.
- Supplier Selection: Choose a reliable PCB manufacturer with experience in producing purple solder mask PCBs to ensure high-quality results.
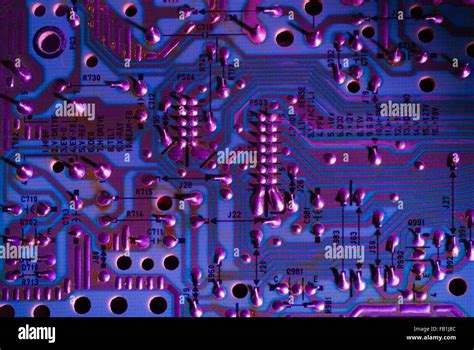
Applications of Purple PCBs
Purple PCBs find applications in various industries and projects:
Consumer Electronics
Purple PCBs are commonly used in consumer electronics, such as smartphones, tablets, and wearable devices. The eye-catching purple color adds a unique aesthetic appeal to these products, making them stand out in a competitive market.
Lighting and LED Applications
Purple PCBs are well-suited for lighting and LED applications due to their excellent UV resistance properties. The purple solder mask helps protect the PCB from the damaging effects of UV light emitted by LEDs, ensuring longer product life and reliability.
Automotive Industry
In the automotive industry, purple PCBs are used in various electronic systems, such as infotainment displays, instrument clusters, and advanced driver assistance systems (ADAS). The improved contrast and visibility offered by purple solder masks enhance the readability of components and labels, which is crucial in automotive applications.
Industrial Control Systems
Purple PCBs are also employed in industrial control systems, where reliability and durability are paramount. The UV resistance and enhanced contrast of purple solder masks contribute to the longevity and ease of maintenance of these systems.
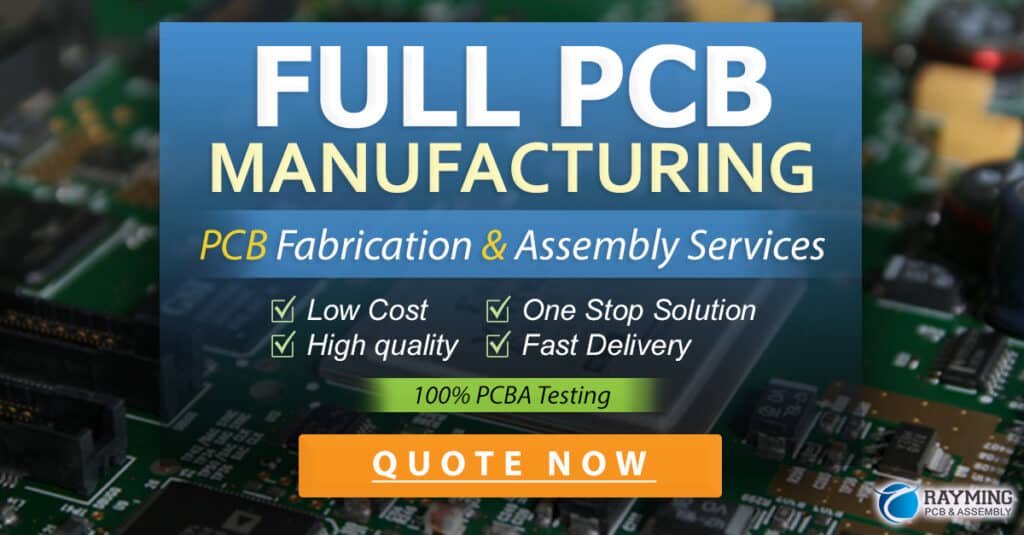
Frequently Asked Questions (FAQ)
-
Q: Are purple PCBs more expensive than traditional green PCBs?
A: The cost difference between purple and green PCBs is typically minimal. While there may be a slight premium for purple solder masks due to pigment costs and production processes, the overall impact on the total PCB cost is usually negligible. -
Q: Can purple PCBs be manufactured with different surface finishes?
A: Yes, purple PCBs can be produced with various surface finishes, such as HASL, ENIG, or OSP (Organic Solderability Preservative). The choice of surface finish depends on the specific requirements of the project, such as solderability, durability, and cost considerations. -
Q: Are there any limitations to the design or layout of purple PCBs?
A: Purple PCBs do not impose any significant limitations on the design or layout compared to other colored PCBs. The same design rules and guidelines apply, ensuring proper functionality and manufacturability. -
Q: How do I specify the purple color when ordering PCBs from a manufacturer?
A: When placing an order for purple PCBs, communicate your color requirements clearly to the manufacturer. Provide the specific Pantone color code or a sample of the desired purple shade to ensure accurate color matching. Most PCB manufacturers have standard purple options available, but custom colors may also be accommodated upon request. -
Q: Are purple PCBs suitable for high-volume production runs?
A: Yes, purple PCBs can be manufactured in high volumes without any additional challenges compared to other colored PCBs. The production process remains the same, and the purple solder mask can be applied consistently across large quantities of boards.
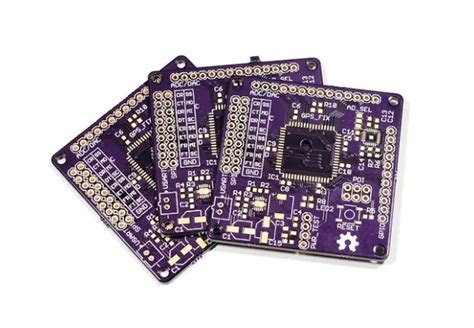
Conclusion
Purple PCBs offer a unique and visually appealing alternative to traditional green PCBs. With their improved contrast, UV resistance, and potential for reducing eye strain, purple PCBs have gained popularity in various industries, including consumer electronics, lighting, automotive, and industrial control systems.
When considering purple PCBs for your project, it is essential to work with a reliable PCB manufacturer that has experience in producing high-quality purple solder mask boards. By carefully specifying your color requirements and ensuring compatibility with your design, you can leverage the benefits of purple PCBs to create visually striking and reliable electronic products.
As the demand for differentiation and aesthetics in electronic devices continues to grow, purple PCBs are likely to become increasingly prevalent in the market. By staying informed about the latest trends and advancements in PCB technology, you can make informed decisions and incorporate purple PCBs into your projects where appropriate.
Characteristic | Purple PCBs | Green PCBs |
---|---|---|
Aesthetics | Unique and visually appealing | Standard and common |
Contrast | Improved contrast against white silkscreen and copper traces | Less contrast compared to purple |
UV Resistance | Excellent resistance to UV light | Good UV resistance, but may be prone to discoloration over time |
Eye Strain | Softer hue, potentially reducing eye strain | Bright green color may cause more eye strain during prolonged inspection |
Cost | Slightly higher due to pigment costs and production processes | Lower cost due to widespread availability and standardization |
Remember, the choice between purple and green PCBs ultimately depends on your specific project requirements, aesthetic preferences, and budget considerations. By weighing the advantages and disadvantages of each option, you can make an informed decision that best suits your needs.
No responses yet