Understanding Component Obsolescence
Component obsolescence is a critical issue facing many industries, particularly those relying on electronic components and systems. It occurs when a component is no longer available from the original manufacturer or authorized distributors, often due to technological advancements, market shifts, or changes in manufacturing processes. Obsolescence can lead to significant challenges, including increased costs, reduced system reliability, and potential supply chain disruptions.
Types of Component Obsolescence
There are several types of component obsolescence, each with its own characteristics and challenges:
-
Functional Obsolescence: This occurs when a component no longer meets the functional requirements of the system due to technological advancements or changes in industry standards.
-
Manufacturing Obsolescence: This happens when a component is no longer produced by the original manufacturer, often due to declining demand, changes in manufacturing processes, or the availability of newer, more advanced alternatives.
-
Logistical Obsolescence: This type of obsolescence arises when a component becomes difficult or impossible to procure due to supply chain issues, such as the discontinuation of raw materials or changes in distribution channels.
-
Economic Obsolescence: This occurs when the cost of maintaining or replacing a component becomes prohibitively expensive compared to the benefits it provides, often due to the availability of more cost-effective alternatives.
Impact of Component Obsolescence
The impact of component obsolescence can be significant and far-reaching, affecting various aspects of an organization’s operations and bottom line:
-
Increased Costs: Obsolete components often come with higher prices due to limited availability and increased demand. Organizations may need to invest in expensive last-time buys, redesigns, or alternative sourcing strategies to mitigate the impact of obsolescence.
-
Reduced System Reliability: As components age and become harder to procure, the risk of system failures and downtime increases. This can lead to reduced productivity, customer dissatisfaction, and potential safety hazards.
-
Supply Chain Disruptions: Component obsolescence can cause significant disruptions to an organization’s supply chain, as the availability of critical components becomes uncertain. This can lead to production delays, missed deadlines, and potential contractual penalties.
-
Compliance and Regulatory Challenges: In some industries, such as aerospace and defense, obsolete components may no longer meet the necessary compliance and regulatory requirements, forcing organizations to undertake costly redesigns or seek special exemptions.
Strategies for Managing Component Obsolescence
To effectively manage component obsolescence, organizations must adopt a proactive and strategic approach that addresses the issue throughout the product lifecycle. Some key strategies include:
1. Proactive Obsolescence management
Proactive obsolescence management involves anticipating and planning for component obsolescence before it occurs. This can be achieved through:
- Obsolescence Forecasting: Using data analytics and market intelligence to predict when components are likely to become obsolete, allowing organizations to plan accordingly.
- Lifecycle Analysis: Conducting thorough analyses of component lifecycles to identify potential obsolescence risks and develop mitigation strategies.
- Supplier Collaboration: Working closely with suppliers to stay informed about potential obsolescence issues and develop joint mitigation plans.
2. Designing for Obsolescence
Designing products with obsolescence in mind can help minimize the impact of component obsolescence over the long term. Some key design strategies include:
- Modular Design: Using modular design principles to allow for easier replacement or upgrading of obsolete components without requiring a complete system redesign.
- Standardization: Standardizing components and interfaces to reduce the risk of obsolescence and increase the availability of alternative sourcing options.
- Technology Roadmapping: Aligning product designs with technology roadmaps to ensure that components remain viable and supported throughout the product lifecycle.
3. Strategic Inventory Management
Strategic inventory management involves carefully planning and managing component inventories to ensure a steady supply of critical components throughout the product lifecycle. This can be achieved through:
- Last-Time Buys: Making large, one-time purchases of components that are at risk of obsolescence to ensure a sufficient supply for the remaining product lifecycle.
- Bonded Inventory: Establishing agreements with suppliers to store and maintain a dedicated inventory of critical components, ensuring their availability when needed.
- Inventory Pooling: Collaborating with other organizations or industry partners to pool inventories and share the costs and risks associated with component obsolescence.
4. Obsolescence Monitoring and Communication
Effective obsolescence management requires continuous monitoring and communication to stay informed about potential obsolescence risks and take timely action. This can be achieved through:
- Obsolescence Databases: Utilizing obsolescence databases and services to stay informed about component lifecycles, end-of-life notices, and potential alternatives.
- Supplier Communication: Maintaining open and regular communication with suppliers to stay informed about potential obsolescence issues and collaborate on mitigation strategies.
- Cross-Functional Collaboration: Fostering collaboration between engineering, procurement, and supply chain teams to ensure a coordinated and proactive approach to obsolescence management.
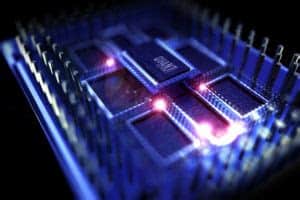
Best Practices for Effective Component Obsolescence Management
To ensure the success of component obsolescence management efforts, organizations should consider the following best practices:
-
Establish a Dedicated Obsolescence Management Team: Assign a dedicated team responsible for monitoring, assessing, and mitigating obsolescence risks across the organization.
-
Develop a Comprehensive Obsolescence Management Plan: Create a detailed plan that outlines the organization’s approach to obsolescence management, including roles and responsibilities, processes, and metrics for success.
-
Invest in Training and Education: Provide training and education to employees to ensure they understand the importance of obsolescence management and are equipped with the necessary skills and knowledge to effectively address the issue.
-
Leverage Technology and Automation: Utilize technology and automation tools to streamline obsolescence management processes, such as data collection, analysis, and reporting.
-
Foster a Culture of Proactive Obsolescence Management: Encourage a culture that prioritizes proactive obsolescence management, with a focus on continuous improvement and collaboration across the organization.
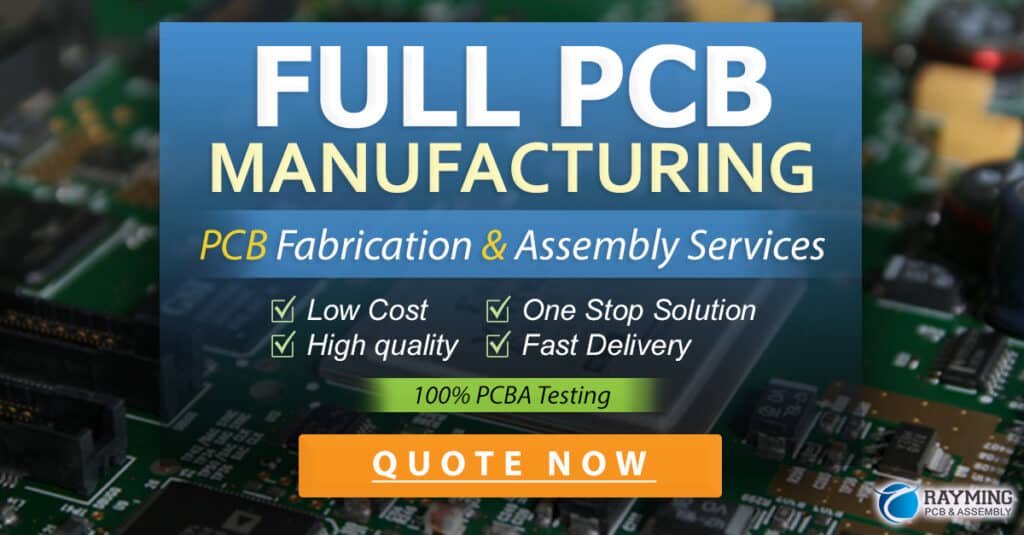
FAQs
-
What are the main causes of component obsolescence?
The main causes of component obsolescence include technological advancements, market shifts, changes in manufacturing processes, and the discontinuation of raw materials or components by suppliers. -
How can organizations predict component obsolescence?
Organizations can predict component obsolescence by using data analytics and market intelligence to monitor component lifecycles, staying informed about supplier plans and industry trends, and conducting regular obsolescence risk assessments. -
What are the benefits of designing products with obsolescence in mind?
Designing products with obsolescence in mind can help minimize the impact of component obsolescence over the long term by allowing for easier replacement or upgrading of obsolete components, reducing the risk of system failures, and minimizing the need for costly redesigns. -
How can organizations effectively collaborate with suppliers to manage component obsolescence?
Organizations can effectively collaborate with suppliers by maintaining open and regular communication, sharing information about potential obsolescence risks, and working together to develop joint mitigation strategies, such as last-time buys or bonded inventory agreements. -
What role does technology play in component obsolescence management?
Technology plays a critical role in component obsolescence management by enabling organizations to streamline processes, such as data collection, analysis, and reporting, and by providing access to obsolescence databases and services that help organizations stay informed about component lifecycles and potential risks.
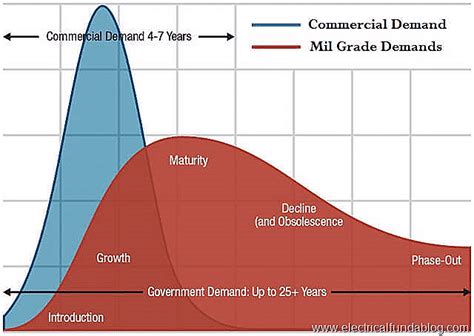
Conclusion
Component obsolescence is a complex and ongoing challenge that requires a proactive and strategic approach to effectively manage. By understanding the types and impacts of obsolescence, adopting key management strategies, and following best practices, organizations can minimize the risks and costs associated with obsolete components and ensure the long-term viability and reliability of their products and systems. Through continuous monitoring, collaboration, and a commitment to proactive obsolescence management, organizations can stay ahead of the curve and maintain a competitive edge in today’s rapidly evolving technological landscape.
Strategy | Description |
---|---|
Proactive Obsolescence Management | Anticipating and planning for component obsolescence before it occurs through obsolescence forecasting, lifecycle analysis, and supplier collaboration. |
Designing for Obsolescence | Designing products with obsolescence in mind, using modular design principles, standardization, and technology roadmapping to minimize the impact of component obsolescence. |
Strategic Inventory Management | Carefully planning and managing component inventories through last-time buys, bonded inventory, and inventory pooling to ensure a steady supply of critical components. |
Obsolescence Monitoring and Communication | Continuous monitoring and communication to stay informed about potential obsolescence risks and take timely action through obsolescence databases, supplier communication, and cross-functional collaboration. |
By implementing these strategies and following best practices, organizations can effectively manage component obsolescence and ensure the long-term success and sustainability of their products and systems.
No responses yet