Choosing the Right Materials for Your Military-grade PCB
The choice of materials is crucial when designing a military-grade PCB. The board must be able to withstand extreme temperatures, vibrations, shocks, and exposure to moisture and chemicals. Therefore, it is essential to select high-quality, robust materials that can meet these demands.
PCB Substrate Materials
The most common PCB substrate materials used in military applications are:
- FR-4: A flame-retardant, glass-reinforced epoxy laminate that offers good mechanical and electrical properties. It is suitable for most military applications.
- Polyimide: A high-temperature, flexible substrate that can withstand temperatures up to 260°C. It is ideal for applications that require high heat resistance and flexibility.
- PTFE (Teflon): A low-dielectric, low-loss substrate that offers excellent high-frequency performance. It is suitable for RF and microwave applications.
Copper Foil Thickness
The thickness of the copper foil used in the PCB can affect its current-carrying capacity, heat dissipation, and signal integrity. Military-grade PCBs typically use thicker copper foils (1 oz or more) to improve durability and reliability.
Solder Mask and Silkscreen
A high-quality solder mask and silkscreen are essential for protecting the PCB from moisture, dust, and other contaminants. The solder mask should be able to withstand harsh environmental conditions and provide good insulation properties. The silkscreen should be clear, durable, and resistant to abrasion and chemicals.
Ensuring Proper Grounding and Shielding
Proper grounding and shielding are critical for ensuring the reliability and performance of military-grade PCBs. Inadequate grounding and shielding can lead to electromagnetic interference (EMI), signal integrity issues, and even device failure.
Grounding Techniques
There are several grounding techniques that can be used in military-grade PCBs:
- Ground planes: A solid copper layer that provides a low-impedance return path for signals and helps reduce EMI.
- Grounding vias: Vias that connect the ground planes on different layers of the PCB, providing a better grounding connection.
- Grounding spurs: Short traces that connect components to the ground plane, reducing the loop area and minimizing EMI.
Shielding Methods
Shielding is essential for protecting sensitive components and signals from EMI. Some common shielding methods used in military-grade PCBs include:
- Metal enclosures: A metal box or case that surrounds the PCB, providing a barrier against EMI.
- Shielding gaskets: Conductive gaskets that seal the gaps between the PCB and the enclosure, preventing EMI from entering or escaping.
- Shielding coatings: Conductive coatings applied to the PCB surface to provide additional shielding against EMI.
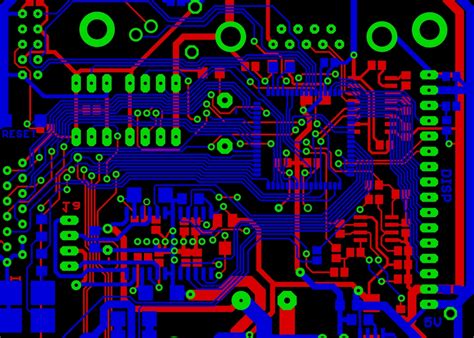
Implementing Robust Power Distribution
A robust power distribution network is essential for ensuring the stable and reliable operation of military-grade PCBs. The power distribution network must be able to provide clean, stable power to all components on the board, even under harsh environmental conditions.
Power Plane Design
A well-designed power plane can help minimize voltage drops, reduce EMI, and improve Power Integrity. Some best practices for designing power planes in military-grade PCBs include:
- Using thicker copper for power planes to reduce resistance and improve current-carrying capacity.
- Placing power planes close to the components that require power to minimize voltage drops.
- Using multiple power planes for different voltage levels to avoid interference between power supplies.
Decoupling Capacitors
Decoupling capacitors are used to provide a local energy source for components and help reduce noise on the power supply lines. In military-grade PCBs, it is essential to use high-quality, low-ESR (equivalent series resistance) capacitors that can withstand harsh environmental conditions.
Power Filtering
Power filtering is essential for removing noise and transients from the power supply lines. Common power filtering techniques used in military-grade PCBs include:
- Ferrite beads: Passive components that provide high-frequency noise suppression.
- LC filters: Combinations of inductors and capacitors that provide low-pass filtering to remove high-frequency noise.
- EMI filters: Specialized filters designed to suppress EMI at specific frequencies.
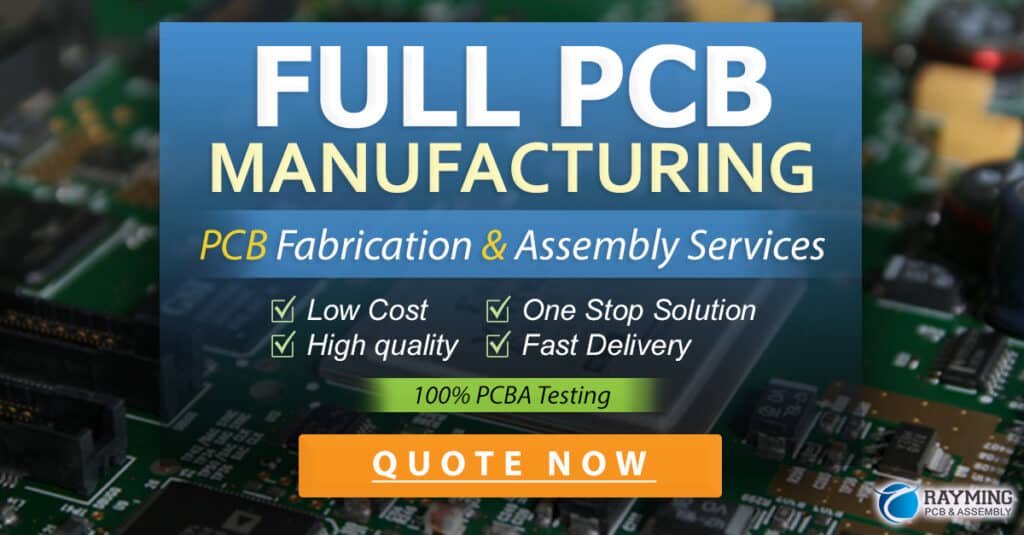
Incorporating Environmental Protection
Military-grade PCBs must be able to withstand harsh environmental conditions, including extreme temperatures, humidity, vibrations, and shocks. Incorporating environmental protection measures is essential for ensuring the reliability and longevity of the board.
Conformal Coating
Conformal coating is a protective layer applied to the PCB surface to provide insulation, moisture resistance, and protection against contaminants. Common conformal coating materials used in military-grade PCBs include:
- Acrylic: A general-purpose coating that offers good moisture and chemical resistance.
- Silicone: A flexible coating that provides excellent temperature and vibration resistance.
- Parylene: A thin, uniform coating that offers superior moisture and chemical resistance.
Potting and Encapsulation
Potting and encapsulation involve filling the spaces between components with a protective compound to provide additional environmental protection. Common potting and encapsulation materials used in military-grade PCBs include:
- Epoxy: A strong, durable material that offers good thermal and mechanical properties.
- Silicone: A flexible material that provides excellent temperature and vibration resistance.
- Urethane: A versatile material that offers good moisture and chemical resistance.
Underfill
Underfill is a process that involves filling the gap between a component (such as a BGA) and the PCB with a specialized epoxy. This helps improve the mechanical strength of the solder joints and protects them from thermal and mechanical stresses.
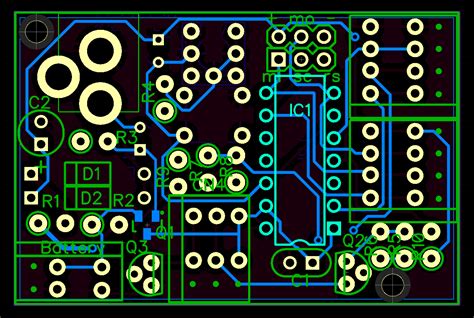
Designing for High-reliability
Designing for high-reliability is crucial for military-grade PCBs, as they are often used in critical applications where failure is not an option. Several design techniques can be employed to improve the reliability of military-grade PCBs.
Component Selection
Selecting high-quality, reliable components is essential for ensuring the overall reliability of the PCB. Military-grade components are typically subjected to more rigorous testing and have tighter tolerances compared to commercial-grade components.
Redundancy
Incorporating redundancy into the PCB design can help improve reliability by providing backup systems in case of component failure. This can include using multiple components in parallel or designing redundant power supplies and signal paths.
Stress Analysis
Performing stress analysis on the PCB design can help identify potential failure points and allow for design optimizations to improve reliability. This can include analyzing the thermal, mechanical, and electrical stresses on the board using simulation tools.
Complying with Military Standards
Military-grade PCBs must comply with various military standards to ensure they meet the required performance and reliability criteria. Some of the most common military standards for PCBs include:
- MIL-PRF-31032: A performance specification for printed circuit board assemblies.
- MIL-PRF-55110: A performance specification for rigid, single and double-sided printed wiring boards.
- MIL-STD-810: A series of environmental test methods for determining the effects of various environmental conditions on equipment.
IPC Standards
In addition to military standards, many military-grade PCBs also comply with IPC (Association Connecting Electronics Industries) standards. Some relevant IPC standards for military-grade PCBs include:
- IPC-6012: A qualification and performance specification for rigid printed boards.
- IPC-A-610: An acceptability standard for electronic assemblies.
- IPC J-STD-001: A standard for soldered electrical and electronic assemblies.
Testing and Qualification
Thorough testing and qualification are essential for ensuring that military-grade PCBs meet the required performance and reliability standards. Some common testing methods used for military-grade PCBs include:
- Environmental testing: Subjecting the PCB to various environmental conditions, such as temperature cycling, humidity, and vibration, to ensure it can withstand harsh environments.
- Functional testing: Verifying that the PCB performs as intended under different operating conditions.
- Accelerated life testing: Subjecting the PCB to increased stress levels to estimate its expected lifespan under normal operating conditions.
Burn-in Testing
Burn-in testing involves operating the PCB at elevated temperatures and voltages for an extended period to identify and eliminate early-life failures. This helps improve the overall reliability of the board by weeding out weak components before they are put into service.
X-ray Inspection
X-ray inspection is a non-destructive testing method that allows for the examination of solder joints, component placement, and internal structures of the PCB. This can help identify potential defects or issues that may not be visible through visual inspection.
FAQ
-
Q: What is the difference between a military-grade PCB and a commercial-grade PCB?
A: Military-grade PCBs are designed to withstand harsher environmental conditions, have higher reliability requirements, and must comply with specific military standards. Commercial-grade PCBs are typically designed for less demanding applications and may not have the same level of durability or performance. -
Q: What are some common materials used in military-grade PCBs?
A: Common materials used in military-grade PCBs include FR-4, polyimide, and PTFE (Teflon) for substrates, and thicker copper foils for improved durability and current-carrying capacity. High-quality solder masks and silkscreens are also essential for protecting the PCB from environmental factors. -
Q: Why is proper grounding and shielding important in military-grade PCBs?
A: Proper grounding and shielding are critical for ensuring the reliability and performance of military-grade PCBs by reducing electromagnetic interference (EMI) and improving signal integrity. Inadequate grounding and shielding can lead to device failure or malfunction. -
Q: What are some environmental protection measures used in military-grade PCBs?
A: Common environmental protection measures used in military-grade PCBs include conformal coating, potting and encapsulation, and underfill. These measures help protect the PCB and its components from moisture, contaminants, and mechanical stresses. -
Q: What are some common military standards that military-grade PCBs must comply with?
A: Some common military standards for PCBs include MIL-PRF-31032 for printed circuit board assemblies, MIL-PRF-55110 for rigid printed wiring boards, and MIL-STD-810 for environmental testing. Many military-grade PCBs also comply with relevant IPC standards.
Conclusion
Designing a military-grade PCB requires careful consideration of various factors to ensure the board can withstand harsh environments and perform reliably. From choosing the right materials and implementing proper grounding and shielding to incorporating environmental protection measures and complying with military standards, each aspect of the design process plays a crucial role in the overall performance and reliability of the PCB.
By understanding and addressing these seven essential factors, designers can create military-grade PCBs that meet the demanding requirements of defense and aerospace applications. Thorough testing and qualification, including environmental testing, burn-in testing, and x-ray inspection, further ensure that the PCB will perform as intended under the most challenging conditions.
As technology continues to advance, the design and manufacture of military-grade PCBs will continue to evolve, pushing the boundaries of performance and reliability in the most demanding environments.
No responses yet