What is a Bill of Materials (BOM)?
A Bill of Materials (BOM) is a comprehensive list of raw materials, components, and instructions required to construct, manufacture, or repair a product or service. It serves as a complete recipe detailing each ingredient needed to produce an end product. The BOM is an essential part of the manufacturing process, as it provides a clear overview of all required parts, along with quantities of each item.
Key Components of a BOM
A typical BOM includes:
- Part name and description
- Part number
- Phase (in which the part is used)
- Quantity required
- Procurement type (manufactured in-house or purchased from external suppliers)
- Part revision and reference designators
- Unit cost
Here is an example table showing key components of a simple BOM:
Part Number | Part Name | Description | Phase | Quantity | Procurement Type | Revision | Reference Designator | Unit Cost |
---|---|---|---|---|---|---|---|---|
101 | Widget A | 1/4″ steel widget | Assembly | 4 | Purchased | A1 | – | $2.50 |
102 | Gadget X | Aluminum gadget | Assembly | 1 | Manufactured | B2 | – | $17.00 |
103 | Screw M3x0.5 | M3x0.5 machine screw | Assembly | 12 | Purchased | – | S1-S12 | $0.05 |
104 | Washer M3 | M3 lock washer | Assembly | 12 | Purchased | – | W1-W12 | $0.02 |
Types of Bill of Materials
There are several types of BOMs used in manufacturing, each serving a specific purpose at different stages of the product lifecycle. The main types include:
1. Engineering BOM (EBOM)
An Engineering BOM, also known as a Design BOM, is created by the product design team. It lists all the components and materials required to build a product based on the design specifications. The EBOM is typically organized by the product’s functional areas and may include subassemblies.
2. Manufacturing BOM (MBOM)
The Manufacturing BOM, also called a Production BOM, is derived from the EBOM and adapted for the manufacturing process. It includes all parts and components needed to build the product on the factory floor, organized in the order of the assembly process. The MBOM may have differences compared to the EBOM, such as substituted parts or consolidated subassemblies.
3. Sales BOM (SBOM)
A Sales BOM, or Customer BOM, is a simplified version of the BOM used by the sales team. It lists the finished products or subassemblies that are available for sale to customers. The SBOM typically does not include detailed component information found in the EBOM or MBOM.
4. Service BOM (SVBOM)
The Service BOM is used by the service and maintenance teams to identify parts required for product repairs and maintenance. It includes spare parts, consumables, and other components needed to keep the product functioning properly over its lifecycle.
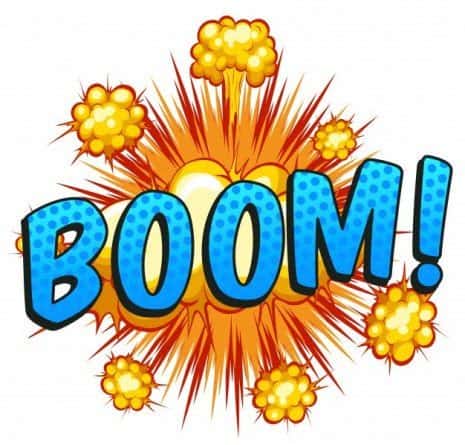
Importance of BOM in Manufacturing
An accurate and well-maintained BOM is crucial for several reasons:
-
Procurement: The BOM provides a clear list of parts and materials that need to be purchased, helping the procurement team ensure that all necessary components are available when needed.
-
Production planning: By detailing the required parts and quantities, the BOM helps production planners schedule manufacturing activities and allocate resources effectively.
-
Inventory Management: The BOM assists in managing inventory levels by providing information on the parts and quantities needed for production, helping to avoid shortages or excess inventory.
-
Cost Control: An accurate BOM enables better cost estimation and control by providing visibility into the materials and components required for each product.
-
Quality Assurance: The BOM serves as a reference for quality control, ensuring that the correct parts and materials are used in the manufacturing process.
-
Communication: The BOM acts as a central document that facilitates communication between various departments, such as engineering, procurement, manufacturing, and sales.
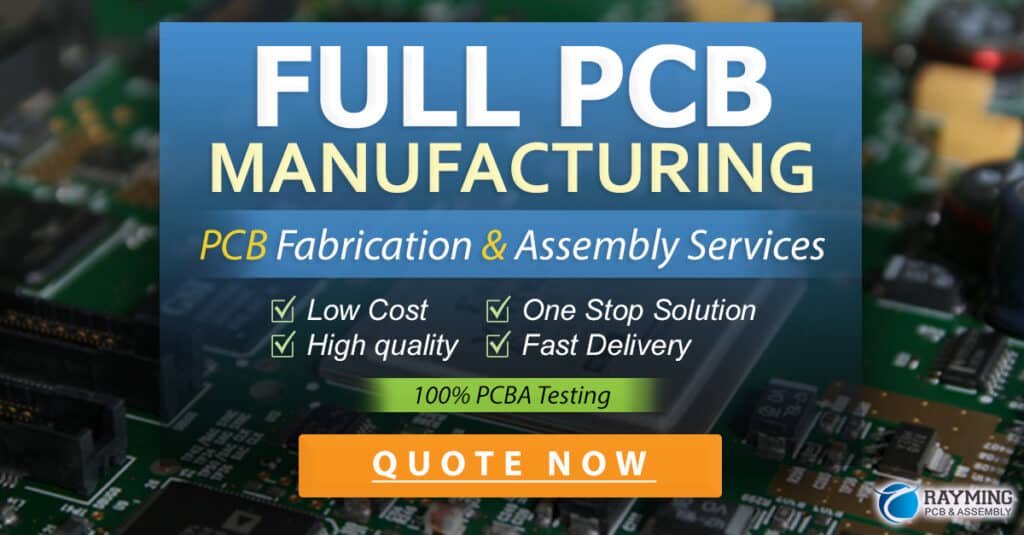
How to Create a Bill of Materials
Creating a comprehensive and accurate BOM involves several steps:
1. Product Design and Development
The process begins with the product design and development phase. The engineering team creates a detailed product design, specifying all required components, materials, and subassemblies.
2. EBOM Creation
Based on the product design, the engineering team creates the Engineering BOM (EBOM). The EBOM lists all the parts and components needed to build the product, organized by functional areas and subassemblies.
3. BOM Review and Approval
The EBOM undergoes a review process to ensure accuracy and completeness. Stakeholders from various departments, such as manufacturing, procurement, and quality control, provide input and approvals.
4. MBOM Creation
Once the EBOM is approved, it is transformed into the Manufacturing BOM (MBOM). The MBOM is adapted to suit the manufacturing process, considering factors such as assembly sequence, production capabilities, and supply chain constraints.
5. BOM Maintenance
As the product undergoes changes or improvements, the BOM must be updated accordingly. Engineering Change Orders (ECOs) are used to manage and track changes to the BOM throughout the product lifecycle.
Here is an example table outlining the steps to create a BOM:
Step | Description | Responsible Team |
---|---|---|
1 | Product Design and Development | Engineering |
2 | EBOM Creation | Engineering |
3 | BOM Review and Approval | Cross-functional Team |
4 | MBOM Creation | Manufacturing |
5 | BOM Maintenance | Engineering |
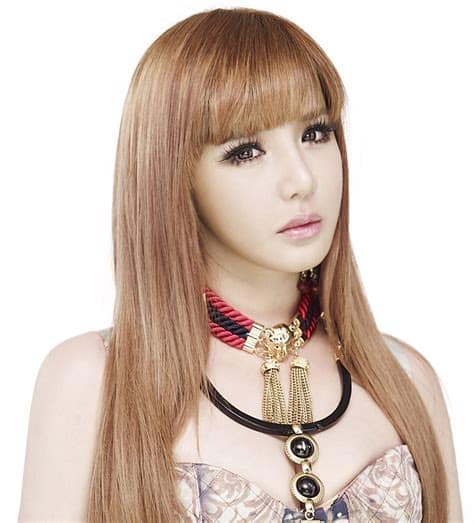
Best Practices for BOM Management
To ensure effective BOM management, consider the following best practices:
-
Standardize BOM Format: Establish a standard format for your BOMs to ensure consistency and clarity across all products and departments.
-
Use a Unique Numbering System: Implement a unique numbering system for parts and components to avoid confusion and duplication.
-
Maintain BOM Accuracy: Regularly review and update BOMs to reflect any changes in product design, components, or suppliers.
-
Integrate with Other Systems: Integrate your BOM with other systems, such as ERP, MRP, or PLM, to ensure data consistency and facilitate seamless information flow.
-
Collaborate with Suppliers: Work closely with suppliers to ensure that they understand your BOM requirements and can provide the necessary parts and materials in a timely manner.
-
Implement Version Control: Use version control to track changes to the BOM over time, ensuring that all stakeholders are working with the most up-to-date information.
-
Train Employees: Provide training to employees involved in BOM creation and management to ensure they understand the processes and best practices.
FAQ
1. What is the difference between an EBOM and an MBOM?
An Engineering BOM (EBOM) is created by the product design team and lists all the components and materials required to build a product based on the design specifications. A Manufacturing BOM (MBOM) is derived from the EBOM and adapted for the manufacturing process, considering factors such as assembly sequence and production capabilities.
2. How often should a BOM be updated?
A BOM should be updated whenever there are changes to the product design, components, or suppliers. It is essential to maintain an accurate and up-to-date BOM throughout the product lifecycle to ensure efficient manufacturing and avoid costly errors.
3. What is the role of a BOM in inventory management?
The BOM assists in managing inventory levels by providing information on the parts and quantities needed for production. This helps in planning procurement activities, ensuring that the necessary components are available when needed, and avoiding shortages or excess inventory.
4. Can a BOM be used for multiple products?
While a BOM is typically specific to a single product or product family, some components or subassemblies may be used across multiple products. In such cases, it is essential to maintain accurate and consistent information across all related BOMs.
5. What are the consequences of an inaccurate BOM?
An inaccurate BOM can lead to various problems, such as:
- Incorrect parts or quantities ordered, leading to production delays or excess inventory
- Increased costs due to rush orders or inventory write-offs
- Quality issues arising from using incorrect or substandard components
- Delayed product launches or missed delivery deadlines
- Difficulty in tracking and managing inventory levels
Maintaining an accurate and up-to-date BOM is crucial for avoiding these consequences and ensuring smooth manufacturing operations.
Conclusion
A Bill of Materials (BOM) is a critical tool in the manufacturing process, providing a comprehensive list of raw materials, components, and instructions required to produce a product. An accurate and well-maintained BOM is essential for effective procurement, production planning, inventory management, cost control, and quality assurance.
Creating a BOM involves several steps, from product design and development to EBOM creation, review, and approval, and finally, the creation of the MBOM for manufacturing. Effective BOM management requires standardization, collaboration, version control, and regular maintenance to ensure accuracy and consistency throughout the product lifecycle.
By understanding the importance of BOMs and implementing best practices for their creation and management, manufacturers can streamline their operations, reduce costs, and improve product quality, ultimately leading to increased customer satisfaction and business success.
No responses yet