Introduction to IoT and Industry 4.0
The Internet of Things (IoT) has emerged as a key enabler for the fourth industrial revolution, commonly known as Industry 4.0. IoT technologies have the potential to transform traditional manufacturing processes into smart, connected, and data-driven systems, leading to increased efficiency, flexibility, and innovation. This review article explores the role of IoT in enabling smart factories within the context of Industry 4.0, discussing its benefits, challenges, and future prospects.
What is the Internet of Things (IoT)?
The Internet of Things refers to the network of physical devices, vehicles, home appliances, and other items embedded with electronics, software, sensors, and connectivity, which enables these objects to connect and exchange data. IoT creates opportunities for more direct integration of the physical world into computer-based systems, resulting in improved efficiency, accuracy, and economic benefits.
Industry 4.0 and the Role of IoT
Industry 4.0 represents the fourth industrial revolution, characterized by the integration of advanced technologies such as IoT, artificial intelligence, robotics, and cloud computing into manufacturing processes. The goal of Industry 4.0 is to create smart factories that are highly efficient, flexible, and responsive to customer demands. IoT plays a crucial role in enabling this transformation by connecting machines, sensors, and systems, allowing for real-time data collection, analysis, and decision-making.
Key Components of IoT in Smart Factories
To understand how IoT enables smart factories, it is essential to examine the key components that make up an IoT-Enabled Manufacturing system.
Sensors and Actuators
Sensors and actuators are the foundation of IoT in smart factories. Sensors collect data from machines, products, and the environment, while actuators execute commands based on the analyzed data. Examples of sensors include temperature, humidity, pressure, and vibration sensors, while actuators can be valves, motors, or switches.
Connectivity and Communication Protocols
IoT devices in smart factories require reliable and secure connectivity to transmit data and receive commands. Various communication protocols are used, such as Wi-Fi, Bluetooth, Zigbee, and LoRaWAN, depending on the specific requirements of the application. Industrial Ethernet and 5G networks are also gaining traction for their high bandwidth and low latency capabilities.
Edge and Cloud Computing
Edge computing involves processing data close to the source, such as on the factory floor, to enable real-time decision-making and reduce latency. Cloud computing, on the other hand, provides scalable storage and processing power for more complex analytics and machine learning tasks. The combination of edge and cloud computing creates a powerful infrastructure for IoT in smart factories.
Data Analytics and Machine Learning
Data analytics and machine learning are critical components of IoT in smart factories. By analyzing the vast amounts of data generated by sensors and machines, manufacturers can gain valuable insights into production processes, identify inefficiencies, and optimize operations. Machine learning algorithms can also be used for predictive maintenance, quality control, and supply chain optimization.
Benefits of IoT in Smart Factories
The adoption of IoT in smart factories offers numerous benefits, including:
- Increased Efficiency and Productivity
- Improved Quality Control
- Predictive Maintenance
- Flexibility and Customization
- Enhanced Safety and Security
Increased Efficiency and Productivity
IoT enables real-time monitoring and control of production processes, allowing manufacturers to identify and address inefficiencies promptly. By optimizing machine performance, reducing downtime, and streamlining workflows, IoT can significantly increase overall equipment effectiveness (OEE) and productivity.
Improved Quality Control
IoT sensors can monitor product quality in real-time, detecting defects and anomalies early in the production process. This allows manufacturers to take corrective actions quickly, reducing waste and improving product quality. Machine learning algorithms can also be used to analyze quality data and identify patterns, enabling continuous improvement of quality control processes.
Predictive Maintenance
IoT enables predictive maintenance by continuously monitoring the health and performance of machines and equipment. By analyzing sensor data, manufacturers can detect potential failures before they occur, allowing for proactive maintenance and reducing unplanned downtime. This not only improves machine reliability but also reduces maintenance costs and extends asset lifetimes.
Flexibility and Customization
IoT-enabled smart factories are highly flexible and can quickly adapt to changing customer demands. By leveraging real-time data and advanced automation, manufacturers can easily reconfigure production lines and produce customized products in smaller batches. This flexibility allows for faster time-to-market and improved responsiveness to customer needs.
Enhanced Safety and Security
IoT can enhance worker safety in smart factories by monitoring the environment for potential hazards, such as gas leaks, high temperatures, or excessive noise levels. Wearable IoT devices can also track worker location and alert them to dangerous situations. In terms of security, IoT systems can be designed with advanced encryption and authentication mechanisms to protect sensitive data and prevent unauthorized access.
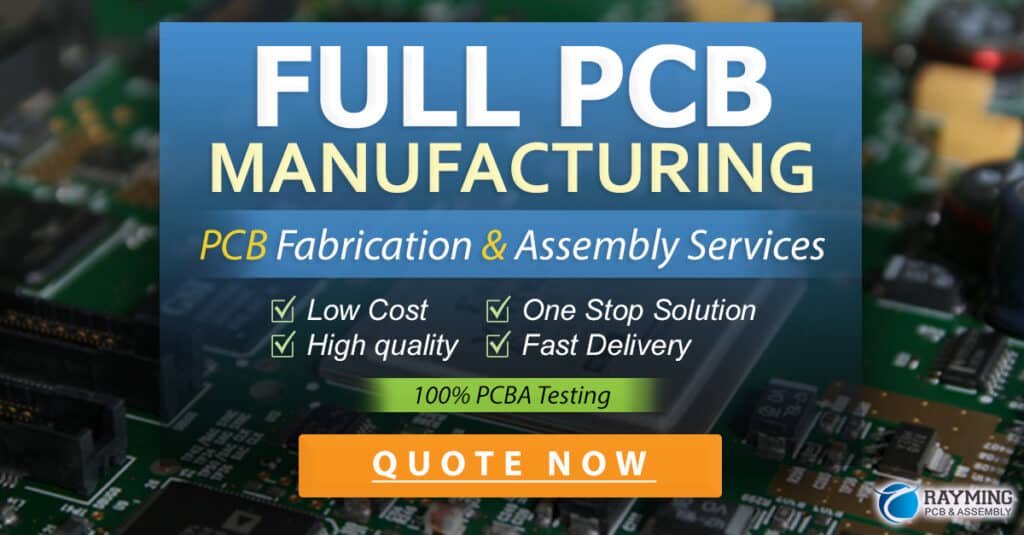
Challenges and Considerations
While IoT offers significant benefits for smart factories, there are also several challenges and considerations that must be addressed:
- Cybersecurity Risks
- Data Privacy and Ownership
- Interoperability and Standardization
- Workforce Skills and Training
- Investment and ROI
Cybersecurity Risks
As IoT devices and systems become more connected, they also become more vulnerable to cyber-attacks. Manufacturers must implement robust cybersecurity measures, such as secure communication protocols, device authentication, and regular security audits, to protect their IoT infrastructure from potential threats.
Data Privacy and Ownership
IoT generates vast amounts of data, which raises concerns about data privacy and ownership. Manufacturers must ensure that they have clear policies in place regarding data collection, storage, and usage, and that they comply with relevant regulations, such as the General Data Protection Regulation (GDPR) in the European Union.
Interoperability and Standardization
The lack of standardization in IoT technologies can lead to interoperability issues, making it difficult for devices and systems from different vendors to communicate and work together seamlessly. Efforts are being made to develop common standards and protocols, such as the Industrial Internet Consortium (IIC) and the Open Platform Communications Unified Architecture (OPC UA), to address this challenge.
Workforce Skills and Training
Implementing IoT in smart factories requires a skilled workforce that can design, deploy, and maintain these complex systems. Manufacturers must invest in training and upskilling their employees to ensure they have the necessary knowledge and expertise to work with IoT technologies effectively.
Investment and ROI
Adopting IoT in smart factories requires significant investment in hardware, software, and infrastructure. Manufacturers must carefully evaluate the potential return on investment (ROI) and develop a clear business case for IoT implementation. This may involve conducting pilot projects and gradually scaling up based on the results.
Future Prospects and Research Directions
As IoT continues to evolve, several future prospects and research directions are worth exploring:
- 5G and Edge Computing
- Artificial Intelligence and Machine Learning
- Digital Twins
- Blockchain and Distributed Ledger Technologies
- Sustainability and Circular Economy
5G and Edge Computing
The deployment of 5G networks and the growth of edge computing will enable faster, more reliable, and low-latency communication between IoT devices in smart factories. This will unlock new possibilities for real-time control, remote monitoring, and autonomous systems.
Artificial Intelligence and Machine Learning
The integration of artificial intelligence (AI) and machine learning (ML) with IoT will enable more advanced analytics, predictive maintenance, and optimization of production processes. AI and ML can also be used for anomaly detection, quality control, and supply chain management.
Digital Twins
Digital twins are virtual representations of physical assets, processes, or systems that can be used for simulation, optimization, and decision-making. The combination of IoT and digital twins will allow manufacturers to create highly accurate models of their production systems, enabling them to test scenarios, identify improvements, and optimize performance.
Blockchain and Distributed Ledger Technologies
Blockchain and distributed ledger technologies (DLTs) can be used to create secure, transparent, and tamper-proof records of IoT data transactions in smart factories. This can enhance trust, traceability, and accountability in supply chains and enable new business models, such as machine-to-machine (M2M) transactions and smart contracts.
Sustainability and Circular Economy
IoT can play a key role in enabling sustainable manufacturing and the transition towards a circular economy. By monitoring resource consumption, optimizing energy efficiency, and enabling predictive maintenance, IoT can help reduce waste, minimize environmental impact, and extend the lifespan of assets.
Frequently Asked Questions (FAQ)
1. What is the role of IoT in enabling smart factories?
IoT plays a crucial role in enabling smart factories by connecting machines, sensors, and systems, allowing for real-time data collection, analysis, and decision-making. This enables manufacturers to optimize production processes, improve quality control, and increase overall efficiency and productivity.
2. What are the key components of IoT in smart factories?
The key components of IoT in smart factories include sensors and actuators, connectivity and communication protocols, edge and cloud computing, and data analytics and machine learning. These components work together to create a connected, data-driven manufacturing environment.
3. What are the main benefits of adopting IoT in smart factories?
The main benefits of adopting IoT in smart factories include increased efficiency and productivity, improved quality control, predictive maintenance, flexibility and customization, and enhanced safety and security. These benefits can lead to significant cost savings, improved customer satisfaction, and increased competitiveness.
4. What are some of the challenges associated with implementing IoT in smart factories?
Some of the challenges associated with implementing IoT in smart factories include cybersecurity risks, data privacy and ownership concerns, interoperability and standardization issues, workforce skills and training requirements, and investment and ROI considerations. Addressing these challenges is crucial for successful IoT adoption in smart factories.
5. What are some future prospects and research directions for IoT in smart factories?
Future prospects and research directions for IoT in smart factories include the integration of 5G and edge computing, artificial intelligence and machine learning, digital twins, blockchain and distributed ledger technologies, and sustainability and circular economy. These developments will further enhance the capabilities of IoT in enabling smart, efficient, and sustainable manufacturing.
Conclusion
The Internet of Things has emerged as a key enabler for the transformation of traditional manufacturing into smart factories within the context of Industry 4.0. By connecting machines, sensors, and systems, IoT allows for real-time data collection, analysis, and decision-making, leading to increased efficiency, flexibility, and innovation. The adoption of IoT in smart factories offers numerous benefits, such as improved productivity, quality control, predictive maintenance, and enhanced safety and security.
However, implementing IoT in smart factories also comes with challenges, including cybersecurity risks, data privacy and ownership concerns, interoperability and standardization issues, workforce skills and training requirements, and investment and ROI considerations. To successfully adopt IoT in smart factories, manufacturers must address these challenges and develop clear strategies for implementation and scaling.
As IoT continues to evolve, future prospects and research directions, such as the integration of 5G and edge computing, artificial intelligence and machine learning, digital twins, blockchain and distributed ledger technologies, and sustainability and circular economy, will further enhance the capabilities of IoT in enabling smart, efficient, and sustainable manufacturing.
In conclusion, the Internet of Things is a critical component of Industry 4.0 and the transformation of traditional manufacturing into smart factories. By embracing IoT technologies and addressing the associated challenges, manufacturers can unlock significant benefits and remain competitive in the rapidly evolving landscape of industrial innovation.
Table 1: Key Components of IoT in Smart Factories
Component | Description |
---|---|
Sensors and Actuators | Sensors collect data from machines, products, and the environment, while actuators execute commands based on the data |
Connectivity and Communication | Various protocols such as Wi-Fi, Bluetooth, Zigbee, LoRaWAN, Industrial Ethernet, and 5G are used for data transmission |
Edge and Cloud Computing | Edge computing enables real-time decision-making, while cloud computing provides scalable storage and processing power |
Data Analytics and Machine Learning | Analyzing data and applying machine learning algorithms for insights, optimization, and predictive maintenance |
Table 2: Benefits of IoT in Smart Factories
Benefit | Description |
---|---|
Increased Efficiency and Productivity | Real-time monitoring and control of production processes, optimizing machine performance, and reducing downtime |
Improved Quality Control | Real-time defect detection, corrective actions, and continuous improvement of quality control processes |
Predictive Maintenance | Monitoring machine health, detecting potential failures, and enabling proactive maintenance to reduce downtime and costs |
Flexibility and Customization | Quickly adapting to changing customer demands, reconfiguring production lines, and producing customized products |
Enhanced Safety and Security | Monitoring the environment for hazards, tracking worker location, and implementing advanced encryption and authentication |
No responses yet