What is IoT-Enabled Manufacturing?
IoT-enabled manufacturing refers to the integration of IoT technologies into the manufacturing process. This involves the use of connected devices, sensors, and software to collect, analyze, and exchange data in real-time. By leveraging the power of IoT, manufacturers can gain unprecedented visibility into their operations, optimize their processes, and make data-driven decisions.
Key Components of IoT-Enabled Manufacturing
-
Connected Devices: IoT-enabled manufacturing relies on a network of connected devices, including machines, sensors, and actuators, that can communicate with each other and exchange data.
-
Data Collection: IoT devices collect vast amounts of data from various sources, such as machine performance, product quality, and environmental conditions.
-
Data Analysis: The collected data is analyzed using advanced analytics tools and machine learning algorithms to extract valuable insights and identify patterns and trends.
-
Real-time Monitoring: IoT-enabled manufacturing allows for real-time monitoring of production processes, enabling manufacturers to detect and address issues promptly.
-
Automation: IoT technologies enable the automation of various manufacturing tasks, reducing human intervention and improving efficiency.
Benefits of IoT-Enabled Manufacturing
The adoption of IoT in manufacturing offers numerous benefits, including:
1. Increased Efficiency and Productivity
IoT-enabled manufacturing streamlines production processes, reduces downtime, and optimizes resource utilization. By leveraging real-time data and analytics, manufacturers can identify bottlenecks, minimize waste, and improve overall efficiency. This leads to increased productivity and faster time-to-market.
2. Enhanced Quality Control
IoT sensors and devices enable continuous monitoring of product quality throughout the manufacturing process. By collecting and analyzing data on various quality parameters, manufacturers can detect defects early, reduce scrap rates, and ensure consistent product quality. This helps to improve customer satisfaction and reduce warranty claims.
3. Predictive Maintenance
IoT-enabled manufacturing allows for predictive maintenance of equipment and machinery. By monitoring machine performance and analyzing data patterns, manufacturers can predict when a machine is likely to fail and schedule maintenance proactively. This reduces unplanned downtime, extends equipment lifespan, and minimizes maintenance costs.
4. Supply Chain Optimization
IoT technologies enable end-to-end visibility and traceability across the supply chain. By tracking raw materials, work-in-progress inventory, and finished goods in real-time, manufacturers can optimize inventory levels, reduce stockouts, and improve delivery performance. IoT also facilitates collaboration with suppliers and partners, enabling better coordination and responsiveness to changing market demands.
5. Customization and Flexibility
IoT-enabled manufacturing supports mass customization and flexible production. By leveraging data from connected devices and customer preferences, manufacturers can quickly adapt their production processes to meet individual customer requirements. This enables the production of personalized products at scale, providing a competitive advantage in the market.
Challenges and Considerations
While IoT-enabled manufacturing offers significant benefits, there are also challenges and considerations that manufacturers must address:
1. Cybersecurity
IoT devices and networks are vulnerable to cyber threats, such as hacking, data breaches, and malware attacks. Manufacturers must implement robust cybersecurity measures, including device authentication, data encryption, and network segmentation, to protect their IoT infrastructure and sensitive data.
2. Interoperability and Standards
The lack of standardization and interoperability among IoT devices and systems can hinder the seamless integration and data exchange within a manufacturing environment. Manufacturers need to adopt industry standards and protocols to ensure compatibility and smooth communication between different devices and systems.
3. Data Management and Analytics
IoT-enabled manufacturing generates vast amounts of data, which can be challenging to manage and analyze effectively. Manufacturers must invest in data management platforms, data storage solutions, and advanced analytics tools to extract valuable insights from the data and make informed decisions.
4. Workforce Skills and Training
Implementing IoT in manufacturing requires a skilled workforce with expertise in IoT technologies, data analytics, and cybersecurity. Manufacturers need to invest in training and upskilling their employees to adapt to the new technologies and processes. Collaborating with educational institutions and industry partners can help bridge the skills gap and ensure a future-ready workforce.
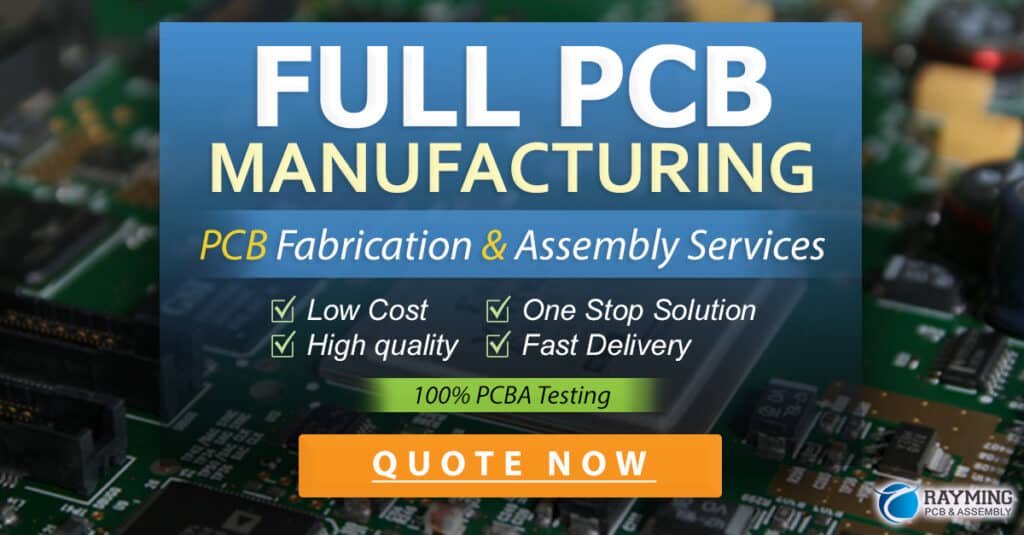
Future of IoT-Enabled Manufacturing
The future of IoT-enabled manufacturing is promising, with several emerging trends and technologies shaping the industry:
1. Edge Computing
Edge computing brings data processing and analysis closer to the source of data generation, reducing latency and enabling real-time decision-making. By processing data at the edge, manufacturers can optimize their IoT infrastructure, reduce network bandwidth requirements, and improve responsiveness to changing conditions.
2. 5G Networks
The deployment of 5G networks will revolutionize IoT-enabled manufacturing by providing high-speed, low-latency, and reliable connectivity. 5G will enable the seamless integration of a large number of IoT devices, support real-time data transmission, and facilitate the implementation of advanced manufacturing applications, such as augmented reality and remote monitoring.
3. Artificial Intelligence and Machine Learning
The integration of artificial intelligence (AI) and machine learning (ML) into IoT-enabled manufacturing will enable intelligent decision-making and process optimization. AI and ML algorithms can analyze vast amounts of data, identify patterns, and predict outcomes, enabling manufacturers to optimize production schedules, improve quality control, and enhance supply chain management.
4. Digital Twins
Digital twins are virtual replicas of physical assets, processes, or systems that simulate their behavior in real-time. By creating digital twins of manufacturing equipment, production lines, and even entire factories, manufacturers can optimize performance, test scenarios, and make informed decisions without disrupting physical operations.
IoT-Enabled Manufacturing Use Cases
To better understand the practical applications of IoT in manufacturing, let’s explore some real-world use cases:
Use Case | Description | Benefits |
---|---|---|
Predictive Maintenance | Monitoring machine health and predicting failures | Reduced downtime, extended equipment lifespan, lower maintenance costs |
Quality Control | Real-time monitoring of product quality parameters | Early defect detection, reduced scrap rates, improved customer satisfaction |
Inventory Management | Tracking inventory levels and optimizing replenishment | Reduced stockouts, optimized inventory levels, improved supply chain efficiency |
Energy Management | Monitoring and optimizing energy consumption in the factory | Reduced energy costs, improved sustainability, compliance with regulations |
Worker Safety | Monitoring worker movements and environmental conditions | Enhanced worker safety, reduced accidents, improved compliance |
Frequently Asked Questions (FAQ)
1. What is the difference between IoT and Industry 4.0?
Industry 4.0 is a broader concept that encompasses the digital transformation of manufacturing, including the use of IoT, artificial intelligence, robotics, and other advanced technologies. IoT is a key enabler of Industry 4.0, providing the connectivity and data exchange necessary for smart manufacturing.
2. How can manufacturers ensure the security of their IoT devices and networks?
Manufacturers can ensure the security of their IoT devices and networks by implementing best practices such as device authentication, data encryption, network segmentation, regular security updates, and employee training on cybersecurity awareness. Collaborating with trusted IoT solution providers and following industry security standards can also help mitigate risks.
3. What are the costs associated with implementing IoT in manufacturing?
The costs of implementing IoT in manufacturing vary depending on the scale and complexity of the implementation. Factors such as hardware and software investments, network infrastructure, data storage and analytics solutions, and workforce training contribute to the overall costs. However, the long-term benefits of IoT-enabled manufacturing, such as increased efficiency, productivity, and cost savings, often outweigh the initial investment.
4. How can manufacturers overcome the challenge of legacy systems when adopting IoT?
Manufacturers can overcome the challenge of legacy systems by gradually integrating IoT technologies into their existing infrastructure. This can involve retrofitting legacy equipment with IoT sensors and devices, using gateway solutions to bridge the communication gap between old and new systems, and adopting a phased approach to IoT implementation. Collaborating with experienced IoT solution providers can help navigate the integration process.
5. What role does data analytics play in IoT-enabled manufacturing?
Data analytics plays a crucial role in IoT-enabled manufacturing by turning the vast amounts of data collected from connected devices into actionable insights. Advanced analytics tools and machine learning algorithms can process and analyze the data to identify patterns, predict outcomes, and optimize processes. Data analytics enables manufacturers to make data-driven decisions, improve operational efficiency, and gain a competitive edge in the market.
Conclusion
The IoT-enabled manufacturing revolution is transforming the way factories operate, bringing unprecedented levels of efficiency, productivity, and competitiveness. By leveraging the power of connected devices, real-time data, and advanced analytics, manufacturers can optimize their processes, improve product quality, and meet the evolving needs of their customers.
However, the adoption of IoT in manufacturing also presents challenges, such as cybersecurity risks, interoperability issues, and the need for a skilled workforce. Manufacturers must address these challenges proactively and invest in the necessary technologies, infrastructure, and talent to fully realize the benefits of IoT-enabled manufacturing.
As the manufacturing industry continues to evolve, the future of IoT-enabled manufacturing looks promising, with emerging trends such as edge computing, 5G networks, artificial intelligence, and digital twins set to further revolutionize the industry. By embracing these technologies and adapting to the changing landscape, manufacturers can position themselves for success in the era of smart manufacturing.
No responses yet