What is Immersion Silver?
Immersion silver, also known as ImAg or IAg, is a lead-free surface finish that involves the deposition of a thin layer of silver onto the exposed copper surfaces of a PCB. The process is an immersion reaction, where the silver ions in the plating solution replace the copper ions on the PCB surface, resulting in a uniform and smooth silver finish.
The typical thickness of an immersion silver layer ranges from 0.1 to 0.3 micrometers (µm). This thin layer provides excellent solderability, conductivity, and protection against oxidation.
Advantages of Immersion Silver
Immersion silver offers several advantages that make it an attractive choice for PCB manufacturers and designers:
-
Excellent Solderability: Immersion silver provides superior solderability compared to other lead-free surface finishes. The silver layer promotes good wetting and spreading of solder, resulting in reliable solder joints.
-
Flat Surface: The immersion silver process results in a flat and smooth surface, making it ideal for fine-pitch components and high-density designs. The flat surface also facilitates accurate component placement and improves the reliability of the assembled PCB.
-
Good Shelf Life: PCBs with immersion silver finish have a relatively long shelf life. The silver layer provides protection against oxidation, ensuring that the PCB remains solderable for an extended period.
-
Cost-Effective: Compared to other lead-free surface finishes like ENIG (Electroless Nickel Immersion Gold), immersion silver is a cost-effective option. The process is simpler and requires fewer steps, resulting in lower production costs.
-
RoHS Compliance: Immersion silver is a lead-free surface finish, making it compliant with the Restriction of Hazardous Substances (RoHS) directive. This compliance is essential for PCBs used in electronic products destined for markets with strict environmental regulations.
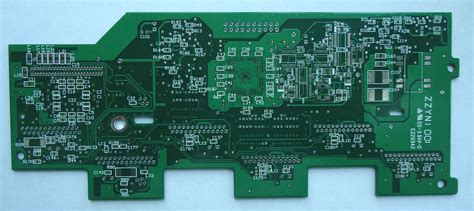
Other Lead-Free PCB Surfaces
While immersion silver is a popular lead-free surface finish, there are other options available. Let’s explore some of the commonly used lead-free PCB surfaces:
1. ENIG (Electroless Nickel Immersion Gold)
ENIG is a widely used lead-free surface finish that consists of a layer of electroless nickel followed by a thin layer of immersion gold. The nickel layer provides a barrier against copper diffusion, while the gold layer offers excellent solderability and protection against oxidation.
Advantages of ENIG:
– Excellent solderability
– Good shelf life
– Suitable for fine-pitch components
– Resistant to multiple reflow cycles
Disadvantages of ENIG:
– Higher cost compared to other surface finishes
– Potential for “black pad” defect due to brittle nickel-phosphorus layer
2. OSP (Organic Solderability Preservative)
OSP is a lead-free surface finish that involves the application of an organic compound to the exposed copper surfaces of a PCB. The organic coating acts as a barrier against oxidation and preserves the solderability of the copper.
Advantages of OSP:
– Cost-effective
– Flat surface finish
– Suitable for fine-pitch components
– Environmentally friendly
Disadvantages of OSP:
– Limited shelf life compared to other surface finishes
– Potential for poor solderability if not handled properly
– May require special handling and storage conditions
3. HASL (Hot Air Solder Leveling)
HASL is a traditional surface finish that involves dipping the PCB into a molten solder bath and then using hot air to level the surface. While lead-based HASL was commonly used in the past, lead-free HASL options are now available to meet RoHS requirements.
Advantages of HASL:
– Excellent solderability
– Good shelf life
– Cost-effective
Disadvantages of HASL:
– Uneven surface finish
– Not suitable for fine-pitch components
– Potential for Thermal Shock to the PCB during the process
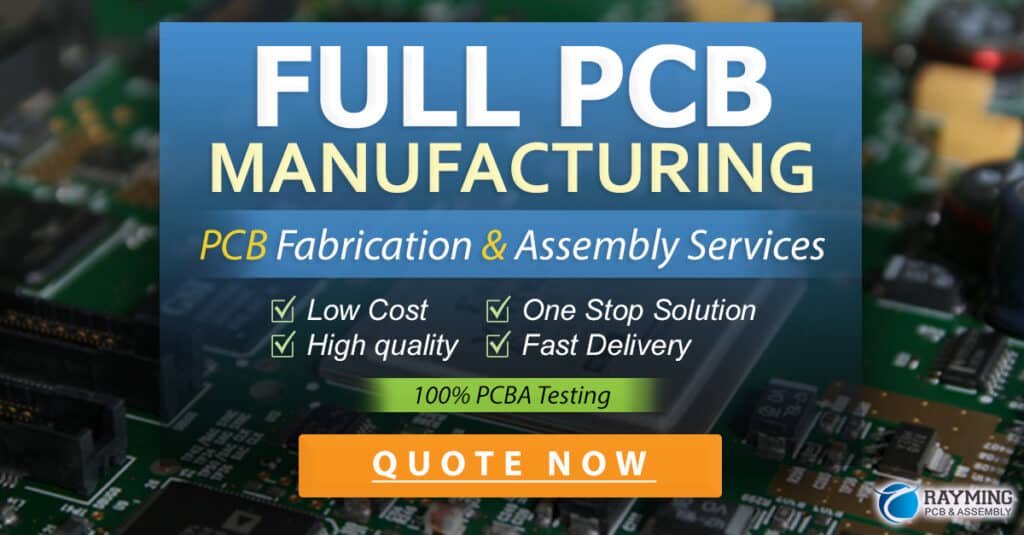
Comparison of Lead-Free PCB Surfaces
To help you make an informed decision when choosing a lead-free PCB Surface Finish, let’s compare the key characteristics of immersion silver, ENIG, OSP, and HASL:
Characteristic | Immersion Silver | ENIG | OSP | HASL |
---|---|---|---|---|
Solderability | Excellent | Excellent | Good | Excellent |
Shelf Life | Good | Excellent | Limited | Good |
Fine-Pitch Suitability | Excellent | Excellent | Good | Poor |
Cost | Low to Moderate | High | Low | Low to Moderate |
Surface Flatness | Flat | Flat | Flat | Uneven |
RoHS Compliance | Yes | Yes | Yes | Yes (lead-free) |
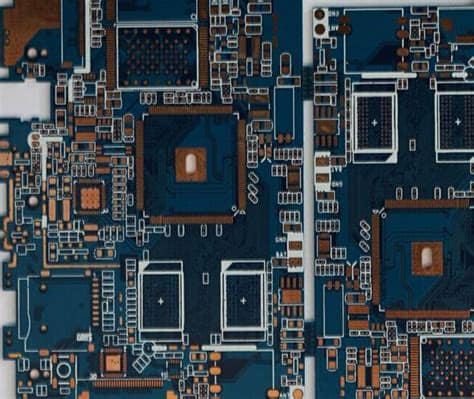
Considerations for Choosing a Lead-Free PCB Surface
When selecting a lead-free PCB surface finish, there are several factors to consider:
-
Application Requirements: Consider the specific requirements of your application, such as solderability, shelf life, and compatibility with the assembly process.
-
Component Compatibility: Ensure that the chosen surface finish is compatible with the components used in your PCB design. Some components may have specific requirements or preferences for surface finishes.
-
Cost: Evaluate the cost implications of each surface finish option. While some finishes may have a higher initial cost, they may offer long-term benefits in terms of reliability and performance.
-
Manufacturing Capabilities: Consider the capabilities and expertise of your PCB manufacturer. Some surface finishes may require specialized equipment or processes that not all manufacturers can accommodate.
-
Environmental Regulations: Ensure that the selected surface finish complies with the relevant environmental regulations, such as RoHS, in the target markets for your products.
Frequently Asked Questions (FAQ)
-
Q: Is immersion silver compatible with all PCB Substrates?
A: Immersion silver is compatible with most common PCB substrates, including FR-4, polyimide, and high-frequency materials. However, it is always recommended to consult with your PCB manufacturer to ensure compatibility with your specific substrate choice. -
Q: How does the shelf life of immersion silver compare to other lead-free surface finishes?
A: Immersion silver has a relatively good shelf life compared to other lead-free surface finishes. It can typically maintain its solderability for 6 to 12 months when stored properly. However, ENIG has an even longer shelf life, often exceeding 12 months. -
Q: Can immersion silver be used for both leaded and lead-free soldering processes?
A: Yes, immersion silver is suitable for both leaded and lead-free soldering processes. Its excellent solderability and compatibility with various solder alloys make it a versatile choice for different assembly processes. -
Q: Are there any specific handling or storage requirements for PCBs with immersion silver finish?
A: PCBs with immersion silver finish should be stored in a cool, dry environment to prevent oxidation and contamination. It is recommended to use moisture barrier bags with desiccants for long-term storage. Proper handling, such as wearing gloves and avoiding contact with contaminants, is also important to maintain the solderability of the surface. -
Q: How does the cost of immersion silver compare to other lead-free surface finishes?
A: Immersion silver is generally more cost-effective compared to ENIG, which involves a more complex and expensive process. However, the cost of immersion silver may be slightly higher than OSP and HASL. The exact cost comparison may vary depending on the specific manufacturer and production volume.
Conclusion
Immersion silver has emerged as a popular lead-free PCB surface finish due to its excellent solderability, flat surface, good shelf life, and cost-effectiveness. As the electronics industry continues to prioritize environmental sustainability and RoHS compliance, immersion silver offers a reliable and attractive option for PCB manufacturers and designers.
However, it is important to consider the specific requirements of your application, component compatibility, cost implications, manufacturing capabilities, and environmental regulations when selecting a lead-free PCB surface finish. Other options, such as ENIG, OSP, and lead-free HASL, also have their advantages and may be suitable for certain applications.
By understanding the characteristics and trade-offs of different lead-free PCB surfaces, you can make an informed decision that balances performance, reliability, and cost for your specific PCB design. Collaborating closely with your PCB manufacturer and considering their expertise and recommendations can help ensure the success of your lead-free PCB project.
No responses yet