Understanding PCB Assembly
Before we dive into the specifics of Box-PCB-Assembly, let’s first understand the fundamentals of PCB assembly. A printed circuit board (PCB) is the backbone of any electronic device, providing a platform for electrical components to be mounted and interconnected. PCB assembly involves the following key steps:
-
Solder Paste Application: Solder paste, a mixture of tiny solder particles suspended in flux, is precisely applied onto the PCB’s contact pads using a stencil or screen printing process.
-
Component Placement: Surface mount technology (SMT) components are accurately placed onto the solder paste using pick-and-place machines. These machines use computer-controlled nozzles to pick up components from reels or trays and position them on the PCB with high precision.
-
Reflow Soldering: The PCB with placed components undergoes a reflow soldering process, where it passes through a carefully controlled temperature profile in a reflow oven. The solder paste melts, forming strong electrical and mechanical connections between the components and the PCB.
-
Through-Hole Assembly: For components with wire leads, such as connectors or large capacitors, through-hole assembly is performed. This involves inserting the component leads into predrilled holes on the PCB and soldering them in place, either manually or using wave soldering machines.
-
Inspection and Testing: After assembly, the PCBAs undergo rigorous inspection and testing procedures to ensure their quality and functionality. This may include automated optical inspection (AOI), X-ray inspection, in-circuit testing (ICT), and functional testing.
Types of PCB Assembly
PCB assembly can be categorized into two main types based on the manufacturing process:
-
Surface Mount Technology (SMT) Assembly: SMT assembly involves placing components directly onto the surface of the PCB. SMT components have small metal leads or terminations that are soldered to pads on the PCB. This assembly method allows for higher component density, improved performance, and automated manufacturing processes.
-
Through-Hole (THT) Assembly: THT assembly involves inserting component leads through predrilled holes on the PCB and soldering them to pads on the opposite side. THT components are generally larger and more robust than SMT components. While THT assembly is slower and less automated compared to SMT, it is still used for certain components that require stronger mechanical connections or for prototype builds.
Assembly Type | Characteristics | Advantages | Disadvantages |
---|---|---|---|
SMT Assembly | – Components placed directly on PCB surface – Small component size – High component density – Automated process |
– Faster assembly – Lower cost for high volumes – Smaller PCB size – Better performance |
– Higher setup costs – Not suitable for large components – Requires specialized equipment |
THT Assembly | – Components inserted through holes in PCB – Larger component size – Lower component density – Manual or semi-automated process |
– Stronger mechanical connections – Suitable for large components – Easier for prototype builds |
– Slower assembly process – Higher labor costs – Larger PCB size |
The Importance of Box Builds in Electronics Manufacturing
Box builds play a crucial role in electronics manufacturing by integrating PCBAs into a complete, functional product. The process of box building involves the following steps:
-
Enclosure Design and Fabrication: The enclosure or box that houses the PCBA is designed and fabricated based on the product’s requirements. This may involve custom designing an enclosure or using off-the-shelf options. The enclosure provides protection, heat dissipation, and aesthetic appeal to the final product.
-
PCBA Integration: The assembled and tested PCBAs are integrated into the enclosure. This involves mounting the PCBA securely, making necessary electrical connections, and ensuring proper fit and alignment within the enclosure.
-
Wiring and Interconnections: Any additional wiring, cables, or interconnections required for the product’s functionality are installed during the box build process. This may include power cables, signal cables, or external connectors.
-
Subassembly Integration: If the product consists of multiple subassemblies or modules, these are integrated into the main enclosure during the box build stage. This ensures that all components work together seamlessly in the final product.
-
Final Assembly and Testing: Once all components are integrated, the final product undergoes a comprehensive testing procedure to verify its functionality, performance, and quality. This may include burn-in tests, environmental stress tests, and compliance testing to ensure the product meets required standards and regulations.
Box builds offer several advantages in electronics manufacturing:
-
Streamlined Production: By combining PCB assembly and box building services, manufacturers can streamline their production process, reducing lead times and minimizing the risk of errors or compatibility issues.
-
Cost Efficiency: Outsourcing box build services to a specialized provider can be more cost-effective than maintaining separate in-house assembly and integration facilities. This is particularly beneficial for companies with limited production volumes or those lacking the necessary expertise and equipment.
-
Quality Assurance: Box build service providers have the knowledge, experience, and resources to ensure the highest quality standards throughout the assembly and integration process. They employ strict quality control measures and testing procedures to deliver reliable and consistent products.
-
Customization and Flexibility: Box build services offer the flexibility to customize products according to specific requirements. This includes the ability to accommodate unique enclosure designs, incorporate additional features or components, and adapt to changing market demands.
Box Build Examples
Box builds find applications across various industries, such as:
-
Consumer Electronics: Box builds are essential for consumer electronic devices like smartphones, tablets, smart home devices, and wearables. These products require precise integration of PCBAs, displays, batteries, and other components into compact and aesthetically pleasing enclosures.
-
Medical Devices: Medical equipment, such as patient monitors, diagnostic devices, and surgical instruments, relies on box builds for reliable and safe operation. The enclosures must meet stringent medical standards and provide protection against moisture, dust, and electromagnetic interference (EMI).
-
Industrial Control Systems: Industrial control panels, automation systems, and process control equipment utilize box builds to house complex PCBAs, displays, and user interfaces. These enclosures must withstand harsh industrial environments and ensure reliable operation.
-
Automotive Electronics: Box builds are crucial for automotive electronic systems, including engine control units (ECUs), infotainment systems, and advanced driver assistance systems (ADAS). The enclosures must be rugged, heat-resistant, and able to withstand vibrations and shocks.
Choosing the Right Box-PCB-Assembly Service Provider
When selecting a Box-PCB-Assembly service provider, consider the following factors:
-
Technical Capabilities: Ensure that the provider has the necessary technical expertise, equipment, and facilities to handle your specific Box-PCB-Assembly requirements. They should have experience in PCB assembly, box building, and product integration.
-
Quality Standards: Look for a provider that adheres to rigorous quality standards, such as ISO 9001, IPC-A-610, and IPC-J-STD-001. They should have well-documented quality control processes and utilize advanced inspection and testing techniques to ensure product reliability.
-
Scalability and Flexibility: Choose a provider that can accommodate your production volume requirements, whether it’s small prototype runs or large-scale mass production. They should also offer flexibility in terms of design customization, component sourcing, and lead times.
-
Supply Chain Management: A reliable Box-PCB-Assembly service provider should have a robust supply chain management system in place. They should have established relationships with component suppliers, ensure timely procurement of materials, and manage inventory effectively to minimize lead times and avoid supply disruptions.
-
Customer Support and Communication: Effective communication and responsive customer support are essential for a successful Box-PCB-Assembly partnership. Look for a provider that offers clear communication channels, regular project updates, and prompt issue resolution.
-
Cost and Value: While cost is an important consideration, it should not be the sole deciding factor. Evaluate the overall value provided by the Box-PCB-Assembly service provider, taking into account their quality, reliability, turnaround time, and additional services offered.
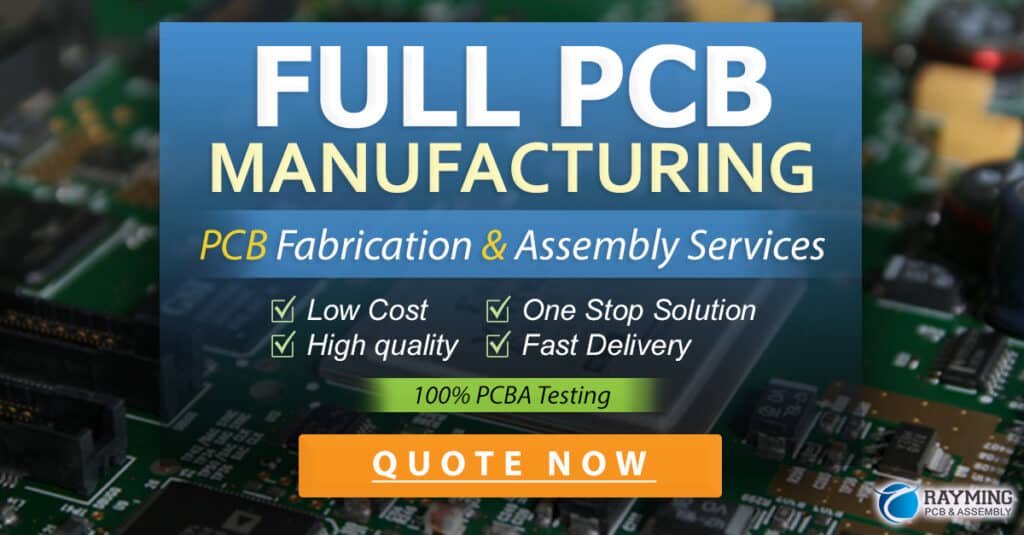
Frequently Asked Questions (FAQ)
-
What is the difference between PCB assembly and box build services?
PCB assembly focuses on the manufacturing and assembly of printed circuit boards, including component placement and soldering. Box build services, on the other hand, involve integrating the assembled PCBs into a complete product, often housed in an enclosure or box. Box builds encompass the entire product assembly process, including enclosure fabrication, wiring, subassembly integration, and final testing. -
Can Box-PCB-Assembly services handle both SMT and THT components?
Yes, most Box-PCB-Assembly service providers are equipped to handle both surface mount technology (SMT) and through-hole technology (THT) components. They have the necessary equipment and expertise to perform SMT assembly using pick-and-place machines and reflow soldering, as well as THT assembly using wave soldering or manual soldering techniques. -
How long does a typical Box-PCB-Assembly project take?
The lead time for a Box-PCB-Assembly project depends on various factors, such as the complexity of the design, the availability of components, and the production volume. Simple projects with readily available components can be completed within a few weeks, while more complex projects or those requiring custom components may take several months. It’s essential to discuss your specific requirements and timelines with your chosen service provider to get an accurate estimate. -
What certifications should I look for in a Box-PCB-Assembly service provider?
When selecting a Box-PCB-Assembly service provider, look for certifications that demonstrate their commitment to quality and adherence to industry standards. Some key certifications include: - ISO 9001: Quality Management System
- IPC-A-610: Acceptability of Electronic Assemblies
- IPC-J-STD-001: Requirements for Soldered Electrical and Electronic Assemblies
-
UL (Underwriters Laboratories) or CSA (Canadian Standards Association) certifications for safety and compliance
-
Can Box-PCB-Assembly services help with product design and prototyping?
Many Box-PCB-Assembly service providers offer design and prototyping services to assist customers in developing their products. They can provide guidance on PCB layout, component selection, enclosure design, and manufacturability optimization. Some providers also offer rapid prototyping services, such as 3D printing or CNC machining, to create functional prototypes for testing and validation before proceeding with mass production.
Conclusion
Box builds and PCB assembly services are integral components of electronics manufacturing, enabling the creation of complete, functional products. By combining PCB assembly with box building, manufacturers can streamline their production process, reduce lead times, and ensure the highest quality standards. When choosing a Box-PCB-Assembly service provider, consider factors such as technical capabilities, quality standards, scalability, supply chain management, customer support, and overall value.
As technology continues to advance and consumer demands evolve, the importance of reliable and efficient Box-PCB-Assembly services will only grow. By partnering with a trusted service provider, companies can focus on their core competencies while leaving the complex task of product assembly and integration to the experts. This collaboration enables the development of innovative, high-quality electronic products that meet the needs of today’s dynamic market.
No responses yet