Introduction
PCB Soldering is a critical process in the manufacturing of electronic devices. Soldering involves joining two or more metal surfaces by melting and flowing a filler metal into the joint. The quality of the solder joint directly impacts the reliability and performance of the PCB. Unfortunately, soldering defects are common and can lead to failures, rework, and increased production costs. In this article, we will discuss 9 common PCB soldering defects, their causes, and solutions to prevent them.
What is PCB Soldering?
PCB soldering is the process of joining electronic components to a printed circuit board (PCB) using a molten metal alloy called solder. The solder is heated to a high temperature, typically between 180°C and 250°C, and then applied to the joint between the component lead and the PCB pad. As the solder cools, it forms a strong electrical and mechanical bond between the component and the PCB.
Why is PCB Soldering Important?
PCB soldering is critical for several reasons:
-
Electrical Conductivity: Solder provides an electrical pathway between the component and the PCB, allowing current to flow through the circuit.
-
Mechanical Strength: Solder also provides mechanical strength to the joint, preventing the component from moving or becoming disconnected from the PCB.
-
Reliability: A well-soldered joint is less likely to fail over time due to vibration, thermal stress, or other environmental factors.
-
Manufacturing Efficiency: Soldering is a fast and efficient way to assemble electronic components onto a PCB, making it an essential process in high-volume manufacturing.
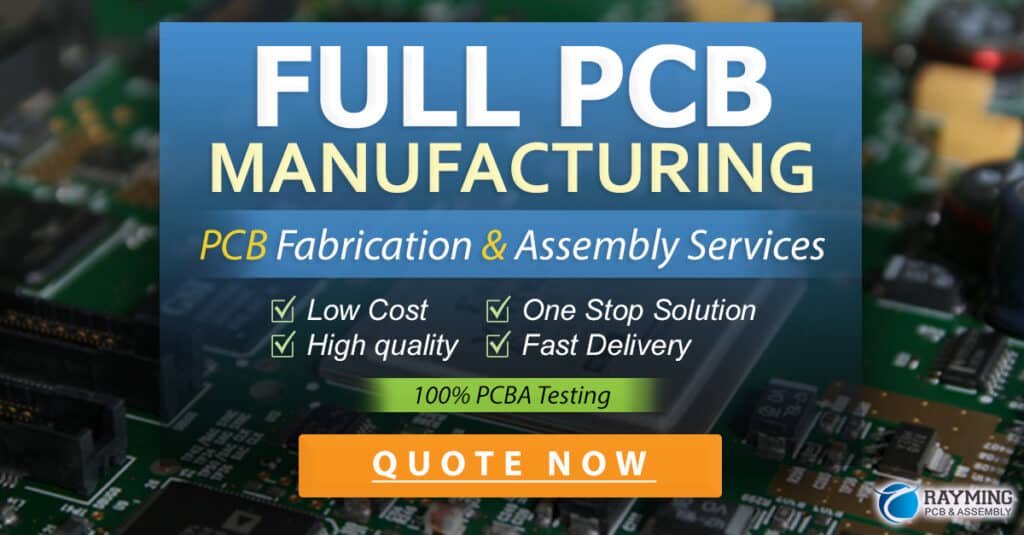
Common PCB Soldering Defects
Despite the importance of PCB soldering, defects are common and can lead to a variety of issues. Here are 9 common PCB soldering defects:
1. Bridging
Bridging occurs when solder inadvertently connects two or more adjacent pads or traces on the PCB. This can happen when too much solder is applied, or when the solder is not properly controlled during the soldering process.
Causes of Bridging
- Excessive solder
- Improper solder mask design
- Incorrect soldering temperature or time
- Poor soldering technique
Solutions for Bridging
- Use the correct amount of solder
- Ensure proper solder mask design
- Optimize soldering temperature and time
- Improve soldering technique through training and practice
2. Cold Joint
A cold joint occurs when the solder does not fully melt and flow into the joint, resulting in a weak and unreliable connection. Cold joints can be caused by insufficient heat, contamination, or poor soldering technique.
Causes of Cold Joint
- Insufficient soldering temperature
- Contaminated solder or PCB surface
- Improper soldering technique
- Incorrect solder alloy
Solutions for Cold Joint
- Ensure proper soldering temperature
- Clean and prepare the PCB surface before soldering
- Improve soldering technique through training and practice
- Use the correct solder alloy for the application
3. Tombstoning
Tombstoning, also known as chip lifting or drawbridging, occurs when one end of a surface-mount component lifts off the PCB during soldering. This can happen when there is an imbalance in the solder volume or temperature between the two pads.
Causes of Tombstoning
- Uneven solder paste application
- Incorrect component placement
- Unbalanced heating during soldering
- Inadequate solder paste volume
Solutions for Tombstoning
- Ensure even solder paste application using stencils or dispensing
- Use pick-and-place machines for accurate component placement
- Optimize reflow oven settings for balanced heating
- Adjust solder paste volume based on component size and type
4. Solder Balling
Solder balling occurs when small spheres of solder form on the surface of the PCB or component. This can happen when there is excess solder, contamination, or incorrect reflow settings.
Causes of Solder Balling
- Excessive solder paste
- Contaminated solder or PCB surface
- Incorrect reflow oven settings
- Poor solder mask design
Solutions for Solder Balling
- Adjust solder paste volume based on pad size and component type
- Clean and prepare the PCB surface before soldering
- Optimize reflow oven settings for the specific solder paste and PCB
- Ensure proper solder mask design to prevent solder spillage
5. Solder Wicking
Solder wicking, also known as capillary action, occurs when solder flows up the component lead or through-hole instead of forming a proper fillet. This can happen when there is too much solder or when the soldering temperature is too high.
Causes of Solder Wicking
- Excessive solder volume
- High soldering temperature
- Improper hole or pad design
- Contaminated component leads or through-holes
Solutions for Solder Wicking
- Use the correct amount of solder for the joint size
- Optimize soldering temperature and time
- Ensure proper hole and pad design for the component type
- Clean and prepare component leads and through-holes before soldering
6. Insufficient Solder
Insufficient solder occurs when there is not enough solder to form a proper joint between the component and the PCB. This can result in a weak or open connection that may fail over time.
Causes of Insufficient Solder
- Inadequate solder paste volume
- Incorrect stencil design or thickness
- Poor soldering technique
- Contaminated or oxidized PCB surface
Solutions for Insufficient Solder
- Adjust solder paste volume based on pad size and component type
- Use the correct stencil design and thickness for the application
- Improve soldering technique through training and practice
- Clean and prepare the PCB surface before soldering
7. Solder Flags
Solder flags, also known as solder spikes or peaks, are sharp protrusions of solder that can cause short circuits or damage to adjacent components. Solder flags can occur when there is excess solder or when the soldering temperature is too high.
Causes of Solder Flags
- Excessive solder volume
- High soldering temperature
- Incorrect solder wire diameter or composition
- Poor soldering technique
Solutions for Solder Flags
- Use the correct amount of solder for the joint size
- Optimize soldering temperature and time
- Choose the appropriate solder wire diameter and composition for the application
- Improve soldering technique through training and practice
8. Solder Voids
Solder voids are small gaps or holes within the solder joint that can weaken the connection and reduce reliability. Voids can be caused by contamination, outgassing, or incorrect reflow settings.
Causes of Solder Voids
- Contaminated solder paste or PCB surface
- Moisture or volatiles in the solder paste
- Incorrect reflow oven settings
- Inadequate solder paste volume
Solutions for Solder Voids
- Use fresh, high-quality solder paste
- Store solder paste in a controlled environment to prevent moisture absorption
- Optimize reflow oven settings for the specific solder paste and PCB
- Adjust solder paste volume based on pad size and component type
9. De-wetting
De-wetting occurs when the molten solder does not adhere to the PCB pad or component lead, resulting in a non-wettable surface. This can be caused by contamination, oxidation, or incorrect soldering temperature.
Causes of De-wetting
- Contaminated or oxidized PCB surface
- Insufficient soldering temperature
- Incorrect solder flux or alloy
- Poor soldering technique
Solutions for De-wetting
- Clean and prepare the PCB surface before soldering
- Ensure proper soldering temperature
- Use the correct solder flux and alloy for the application
- Improve soldering technique through training and practice
Soldering Defect Prevention Strategies
While soldering defects can be difficult to eliminate completely, there are several strategies that can help prevent them:
-
Design for Manufacturing (DFM): Collaborate with the PCB design team to ensure that the board layout, pad sizes, and solder mask openings are optimized for soldering.
-
Process Control: Implement strict process controls for solder paste printing, component placement, and reflow soldering to ensure consistency and repeatability.
-
Equipment Maintenance: Regularly maintain and calibrate soldering equipment, including stencil printers, pick-and-place machines, and reflow ovens.
-
Material Selection: Choose high-quality solder paste, flux, and components from reputable suppliers to minimize the risk of contamination or defects.
-
Training and Certification: Provide regular training and certification programs for soldering operators to ensure that they have the necessary skills and knowledge to perform high-quality soldering.
Soldering Defect Inspection and Rework
Even with the best prevention strategies in place, soldering defects can still occur. It is important to have a robust inspection and rework process to identify and correct defects before they reach the end customer.
Visual Inspection
Visual inspection is the most common method for identifying soldering defects. Trained operators use magnification and lighting to examine each solder joint for signs of bridging, insufficient solder, solder balls, or other defects.
Automated Optical Inspection (AOI)
AOI is a machine vision system that uses cameras and image processing algorithms to automatically inspect PCBs for soldering defects. AOI can quickly identify defects that may be missed by human inspectors, but it requires careful programming and calibration to avoid false positives or negatives.
X-ray Inspection
X-ray inspection is used to examine solder joints that are hidden from view, such as ball grid array (BGA) or flip-chip packages. X-ray systems can detect voids, bridging, or other defects within the solder joint that cannot be seen with visual or AOI Inspection.
Rework
When soldering defects are identified, they must be corrected through rework. Rework involves removing the defective component or solder joint and replacing it with a new one. Rework can be a time-consuming and expensive process, so it is important to minimize the need for rework through effective prevention and inspection strategies.
Frequently Asked Questions (FAQ)
-
What is the most common PCB soldering defect?
The most common PCB soldering defect is bridging, which occurs when solder inadvertently connects two or more adjacent pads or traces on the PCB. -
Can soldering defects be completely eliminated?
While it is difficult to completely eliminate soldering defects, they can be minimized through effective prevention strategies such as design for manufacturing, process control, equipment maintenance, material selection, and operator training. -
What is the difference between AOI and X-ray inspection?
AOI (automated optical inspection) uses cameras and image processing algorithms to automatically inspect PCBs for soldering defects that are visible on the surface. X-ray inspection, on the other hand, is used to examine solder joints that are hidden from view, such as those in BGA or flip-chip packages. -
How can I prevent tombstoning defects?
Tombstoning defects can be prevented by ensuring even solder paste application, using pick-and-place machines for accurate component placement, optimizing reflow oven settings for balanced heating, and adjusting solder paste volume based on component size and type. -
What should I do if I identify a soldering defect on my PCB?
If a soldering defect is identified on a PCB, it must be corrected through rework. Rework involves removing the defective component or solder joint and replacing it with a new one. However, rework can be time-consuming and expensive, so it is important to minimize the need for rework through effective prevention and inspection strategies.
Conclusion
PCB soldering is a critical process in the manufacturing of electronic devices, and soldering defects can have a significant impact on the reliability and performance of the final product. By understanding the common types of soldering defects, their causes, and solutions, manufacturers can implement effective prevention and inspection strategies to minimize defects and improve quality.
Design for manufacturing, process control, equipment maintenance, material selection, and operator training are all essential components of a comprehensive soldering defect prevention strategy. When defects do occur, a robust inspection and rework process can help identify and correct them before they reach the end customer.
By following best practices for PCB soldering and continuously improving their processes, manufacturers can reduce costs, improve efficiency, and deliver high-quality products to their customers.
No responses yet