Introduction to High-temperature PCB
High-temperature PCBs are designed to withstand extreme temperatures and harsh environments. These PCBs are essential in various industries, such as aerospace, automotive, oil and gas, and military applications. The ability to function reliably under high temperatures is crucial for the performance and longevity of electronic devices in these sectors.
What Makes a PCB High-temperature Resistant?
Several factors contribute to a PCB’s high-temperature resistance:
-
Substrate material: High-temperature PCBs use substrate materials with higher glass transition temperatures (Tg) and thermal decomposition temperatures (Td), such as polyimide, PTFE, and ceramic.
-
Copper thickness: Thicker copper traces help dissipate heat more efficiently and improve the PCB’s thermal stability.
-
Solder mask: High-temperature solder masks provide better insulation and protection against thermal stress.
-
Component selection: Components used in high-temperature PCBs must be rated for the expected temperature range to ensure reliable performance.
Designing High-temperature PCBs
Selecting the Right Substrate Material
Choosing the appropriate substrate material is crucial for high-temperature PCBs. The following table compares common substrate materials and their properties:
Substrate Material | Glass Transition Temperature (Tg) | Thermal Decomposition Temperature (Td) | Dielectric Constant | Dissipation Factor |
---|---|---|---|---|
FR-4 | 130°C – 140°C | 300°C – 320°C | 4.5 – 5.0 | 0.02 |
Polyimide | 260°C – 300°C | 500°C – 550°C | 3.5 – 4.0 | 0.003 – 0.007 |
PTFE | 327°C | 400°C – 450°C | 2.1 – 2.5 | 0.0002 – 0.0008 |
Ceramic | > 1000°C | > 1000°C | 6.0 – 10.0 | 0.001 – 0.005 |
Thermal Management Techniques
Proper thermal management is essential for high-temperature PCBs. Some techniques to improve thermal management include:
- Using thermal vias to conduct heat away from hot spots
- Incorporating heat sinks and heat spreaders
- Optimizing component placement to minimize heat buildup
- Using thermal interface materials (TIMs) to enhance heat transfer between components and the PCB
Component Selection and Placement
When designing high-temperature PCBs, it’s essential to select components rated for the expected temperature range. Some considerations include:
- Using high-temperature rated capacitors, resistors, and inductors
- Choosing high-temperature solder alloys, such as Sn-Ag-Cu (SAC) or Au-Sn
- Considering the use of ceramic or metal packaging for ICs
- Placing temperature-sensitive components away from hot spots
Manufacturing High-temperature PCBs
Material Handling and Processing
Manufacturing high-temperature PCBs requires special attention to material handling and processing:
- Proper storage and handling of substrate materials to prevent moisture absorption and contamination
- Adjusting drilling parameters to accommodate harder substrate materials
- Using high-temperature compatible solder masks and legend inks
- Employing appropriate cleaning processes to remove flux residues and contaminants
Quality Control and Testing
Rigorous quality control and testing are essential for high-temperature PCBs:
- Conducting thermal cycling tests to evaluate the PCB’s resilience to temperature fluctuations
- Performing high-temperature operational tests to verify the PCB’s performance under extreme conditions
- Inspecting solder joints and components for signs of thermal stress or damage
- Utilizing X-ray and acoustic microscopy to detect internal defects or delamination
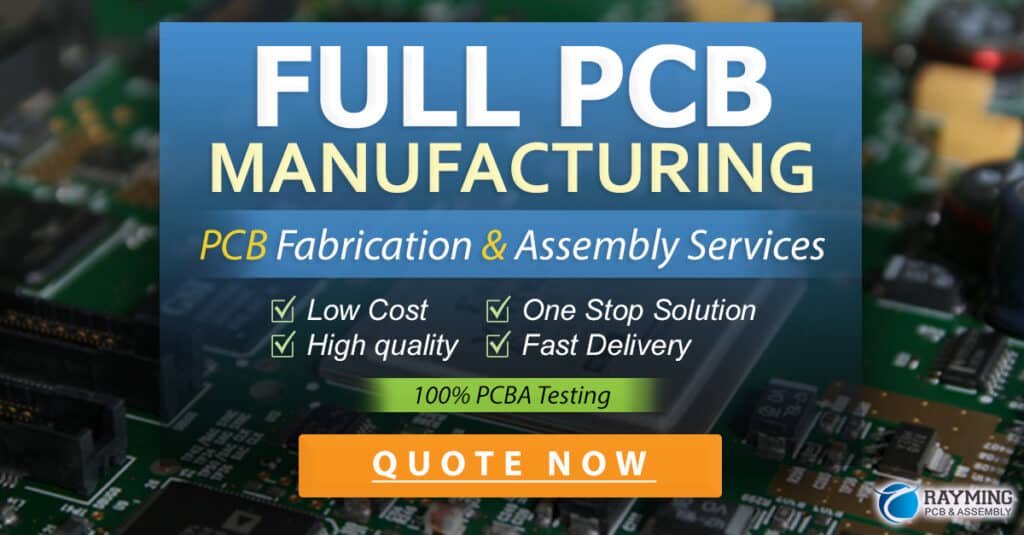
Applications of High-temperature PCBs
High-temperature PCBs find applications in various industries:
Aerospace and Aviation
- Jet engine control systems
- Satellite communications equipment
- Avionic displays and instrumentation
Automotive
- Engine control units (ECUs)
- Exhaust gas sensors
- Brake system electronics
Oil and Gas
- Downhole logging tools
- Drilling equipment
- Pipeline monitoring systems
Industrial and Power Electronics
- Motor drives and controls
- Welding equipment
- Power inverters and converters
Frequently Asked Questions (FAQ)
-
Q: What is the maximum operating temperature for high-temperature PCBs?
A: The maximum operating temperature depends on the substrate material and components used. Polyimide-based PCBs can typically withstand temperatures up to 260°C, while ceramic-based PCBs can operate at temperatures exceeding 500°C. -
Q: Can high-temperature PCBs be repaired or reworked?
A: Repairing or reworking high-temperature PCBs can be challenging due to the specialized materials and processes involved. It’s essential to use high-temperature compatible soldering equipment and techniques to avoid damaging the PCB or components. -
Q: How do high-temperature PCBs differ from standard PCBs in terms of cost?
A: High-temperature PCBs are generally more expensive than standard PCBs due to the specialized materials, components, and manufacturing processes required. The cost can be several times higher, depending on the complexity and performance requirements of the application. -
Q: What are the primary challenges in designing high-temperature PCBs?
A: The main challenges in designing high-temperature PCBs include selecting appropriate materials, managing thermal stresses, ensuring reliable component performance, and optimizing thermal management. Designers must also consider the impact of thermal expansion on the PCB’s mechanical integrity and interconnections. -
Q: Are there any specific standards or certifications for high-temperature PCBs?
A: While there are no specific standards dedicated solely to high-temperature PCBs, several industry standards cover aspects relevant to their design and manufacturing, such as IPC-4101 (Specification for Base Materials for Rigid and Multilayer Printed Boards) and IPC-6012 (Qualification and Performance Specification for Rigid Printed Boards). Additionally, some applications may require compliance with sector-specific standards, such as AEC-Q100 for automotive electronics or DO-160 for avionics.
Conclusion
High-temperature PCBs are critical components in various industries where electronic devices must operate reliably in extreme temperatures and harsh environments. Designing and manufacturing these PCBs requires careful consideration of substrate materials, thermal management techniques, component selection, and processing methods.
By understanding the unique challenges and requirements of high-temperature PCBs, engineers and manufacturers can create robust and reliable electronic systems that can withstand the most demanding applications. As technology advances and new materials emerge, the capabilities and applications of high-temperature PCBs will continue to expand, enabling even more innovative solutions in fields such as aerospace, automotive, oil and gas, and industrial electronics.
No responses yet