Introduction
Solder mask, also known as solder resist or solder stop, is a protective coating applied to the copper traces of a printed circuit board (PCB) to prevent solder from bridging between conductors during the soldering process. It also provides protection against oxidation and corrosion, enhances the PCB’s appearance, and serves as an insulating layer. One of the most noticeable features of a solder mask is its color, which can vary depending on the manufacturer and the specific requirements of the PCB design.
In this article, we will explore the different Solder Mask Colors available, their properties, and how to choose the right one for your PCB project.
Why Does Solder Mask Color Matter?
While the color of the solder mask may seem like a purely aesthetic choice, it can actually have a significant impact on the functionality and performance of the PCB. Here are some reasons why solder mask color matters:
Visibility and Inspection
The color of the solder mask can affect the visibility of the PCB features during inspection and assembly. Some colors, such as white or yellow, provide high contrast against the copper traces, making it easier to spot defects or misalignments. Other colors, like black or dark blue, may require special lighting or magnification tools for proper inspection.
UV Resistance
Certain solder mask colors, particularly lighter shades, are more susceptible to degradation when exposed to ultraviolet (UV) light. This can lead to discoloration, brittleness, and reduced insulation properties over time. If your PCB will be exposed to sunlight or other sources of UV radiation, it’s essential to choose a solder mask color with good UV resistance, such as green or black.
Thermal Properties
The color of the solder mask can also influence the thermal properties of the PCB. Darker colors, like black, absorb more heat, which can be beneficial in applications where the PCB needs to dissipate heat efficiently. Lighter colors, on the other hand, reflect more heat and may be preferred in designs where temperature control is critical.
Aesthetics and Branding
In some cases, the choice of solder mask color may be driven by aesthetic preferences or branding requirements. For example, a company may want their PCBs to feature their signature colors to maintain a consistent visual identity across their products.
Common Solder Mask Colors and Their Properties
There are several standard solder mask colors available, each with its own set of properties and advantages. Let’s take a closer look at some of the most common options:
Green
Green is the most widely used solder mask color in the PCB industry. It offers a good balance of properties, including:
- High contrast against copper traces for easy inspection
- Good UV resistance and durability
- Decent thermal properties
- Wide availability and cost-effectiveness
Blue
Blue solder masks are another popular choice, especially for high-end or military-grade PCBs. They provide:
- Excellent UV resistance and long-term stability
- Good contrast and visibility
- Aesthetic appeal and a professional appearance
- Compatibility with a wide range of PCB finishes
Red
Red solder masks are less common but can be used for specific applications or to create a unique visual effect. They offer:
- High visibility and contrast against copper traces
- Good insulation properties
- Potential for branding or color-coding purposes
- Compatibility with various PCB finishes
Black
Black solder masks are gaining popularity due to their sleek appearance and thermal properties. They provide:
- Excellent heat absorption and dissipation
- UV resistance and durability
- High-end aesthetic appeal
- Good contrast when used with white silkscreen
White
White solder masks are relatively rare but can be used for specific design requirements. They offer:
- High contrast against copper traces and dark silkscreen
- Reflective properties for better heat dissipation
- Unique aesthetic appeal
- Potential for use in LED lighting applications
Yellow
Yellow solder masks are not as common as other colors but can be used for specific purposes, such as:
- High visibility and contrast against copper traces
- Potential for color-coding or branding
- Compatibility with certain PCB finishes
- Use in applications where visual inspection is critical
Here’s a table summarizing the properties of these common solder mask colors:
Color | Contrast | UV Resistance | Thermal Properties | Availability | Common Uses |
---|---|---|---|---|---|
Green | High | Good | Decent | High | General-purpose |
Blue | Good | Excellent | Good | High | High-end, military |
Red | High | Good | Good | Medium | Specific applications, branding |
Black | High (with white silkscreen) | Excellent | Excellent | Medium | High-end, thermal management |
White | High | Poor | Reflective | Low | LED lighting, specific designs |
Yellow | High | Fair | Good | Low | Color-coding, visual inspection |
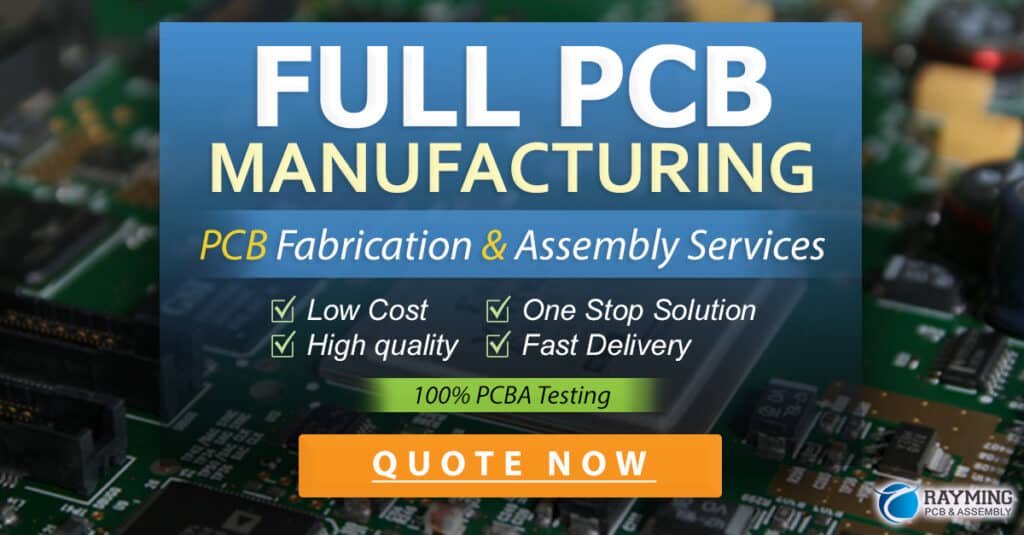
Factors to Consider When Choosing a Solder Mask Color
When selecting a solder mask color for your PCB project, there are several factors to consider:
Application Requirements
The intended use of your PCB should be the primary driver for choosing a solder mask color. Consider the following questions:
- Will the PCB be exposed to UV light or harsh environmental conditions?
- Are there specific thermal management requirements?
- Is high visibility or contrast needed for inspection or assembly?
- Are there any color-coding or branding considerations?
Manufacturing Capabilities
Not all PCB manufacturers offer the same range of solder mask colors. Some colors may be more readily available or cost-effective than others. It’s essential to consult with your manufacturer early in the design process to ensure they can accommodate your preferred color choice.
Silkscreen Compatibility
The color of your solder mask should also be compatible with the silkscreen color you intend to use. High contrast between the solder mask and silkscreen is crucial for legibility and ease of assembly. Common silkscreen colors include white, black, and yellow.
Cost Considerations
The cost of different solder mask colors can vary depending on the manufacturer and the specific formulation used. Generally, standard colors like green and blue are more cost-effective than specialized colors like white or yellow. It’s essential to balance your color preferences with your project budget.
Frequently Asked Questions (FAQ)
-
Q: Can I mix and match different solder mask colors on the same PCB?
A: Yes, it is possible to use multiple solder mask colors on a single PCB, although it may increase manufacturing complexity and cost. This technique is sometimes used for color-coding or creating unique visual effects. -
Q: How does the solder mask color affect the assembly process?
A: The solder mask color can impact the visibility of PCB features during assembly, particularly when using automated pick-and-place machines. High-contrast colors like green or blue can make it easier for machine vision systems to accurately place components. -
Q: Are there any industry standards for solder mask colors?
A: While there are no strict industry standards for solder mask colors, green is widely considered the default choice for most PCB Applications. Blue is often used for high-reliability or military-grade PCBs, while other colors may be specified for particular industries or applications. -
Q: Can I change the solder mask color on an existing PCB design?
A: Yes, changing the solder mask color on an existing PCB design is generally possible, as long as the manufacturer supports the desired color. However, it’s essential to verify that the new color choice is compatible with the existing silkscreen and any other design elements. -
Q: How does the solder mask color affect the PCB’s electrical properties?
A: The solder mask color itself does not directly affect the electrical properties of the PCB, such as impedance or signal integrity. However, the quality and consistency of the solder mask application, regardless of color, can impact the PCB’s overall performance and reliability.
Conclusion
Choosing the right solder mask color for your PCB project involves considering various factors, including application requirements, manufacturing capabilities, silkscreen compatibility, and cost. While green is the most common and versatile choice, other colors like blue, red, black, white, and yellow can be used to meet specific design goals or aesthetic preferences.
By understanding the properties and advantages of different solder mask colors, you can make an informed decision that balances functionality, reliability, and visual appeal. Always consult with your PCB manufacturer early in the design process to ensure your color choice is feasible and cost-effective for your particular project.
Ultimately, the right solder mask color will depend on your specific needs and priorities. Whether you opt for the tried-and-true green, the high-end appeal of blue, or a more unconventional choice like white or yellow, the key is to select a color that enhances the performance and longevity of your PCB while also meeting your aesthetic and branding goals.
No responses yet