Understanding PCB Conductivity
Printed circuit boards (PCBs) are the backbone of modern electronics, providing a platform for interconnecting components and enabling complex circuits to function seamlessly. One of the key factors that determine the performance and reliability of a PCB is its conductivity. In this article, we will explore the role of vias and traces in PCB conductivity and how they impact the overall performance of electronic devices.
What is PCB Conductivity?
PCB conductivity refers to the ability of a printed circuit board to allow electric current to flow through its conductive layers, vias, and traces. The conductivity of a PCB is determined by several factors, including the materials used, the thickness of the conductive layers, and the design of the vias and traces.
The Importance of PCB Conductivity
Maintaining proper PCB conductivity is crucial for several reasons:
-
Signal Integrity: Good conductivity ensures that electrical signals can travel through the PCB without significant loss or distortion, maintaining signal integrity.
-
Power Delivery: Conductive layers, vias, and traces are responsible for delivering power to components on the PCB. Poor conductivity can lead to voltage drops and inadequate power delivery.
-
Heat Dissipation: Conductive materials help dissipate heat generated by components, preventing overheating and ensuring the longevity of the PCB and its components.
-
Electromagnetic Compatibility (EMC): Proper conductivity helps minimize electromagnetic interference (EMI) and ensures that the PCB complies with EMC regulations.
Vias: The Vertical Connections
Vias are small, conductive holes drilled through the layers of a PCB, allowing electrical signals to pass from one layer to another. They play a crucial role in PCB conductivity and are essential for creating Multilayer PCBs.
Types of Vias
There are several types of vias used in PCB design, each serving a specific purpose:
-
Through Hole Vias: These vias extend through all layers of the PCB, from the top to the bottom surface. They are commonly used for mounting through-hole components and providing electrical connections between layers.
-
Blind Vias: Blind vias start on an outer layer and terminate on an inner layer, without extending through the entire PCB. They are used to connect outer layers to inner layers.
-
Buried Vias: Buried vias are located entirely within the inner layers of the PCB and do not extend to the outer surfaces. They are used to connect inner layers to each other.
-
Micro Vias: Micro vias are small, laser-drilled vias that are typically used in high-density interconnect (HDI) PCBs. They offer improved space utilization and enable finer pitch connections.
Via Sizing and Spacing
The size and spacing of vias are critical factors in determining PCB conductivity. Smaller vias offer several advantages, such as:
-
Space Savings: Smaller vias allow for more compact PCB designs and higher component density.
-
Improved Signal Integrity: Smaller vias have lower inductance and capacitance, which can help maintain signal integrity, especially at high frequencies.
However, smaller vias also have some limitations:
-
Manufacturing Complexity: Smaller vias require more precise drilling and plating processes, which can increase manufacturing complexity and cost.
-
Current Carrying Capacity: Smaller vias have a lower current carrying capacity compared to larger vias, which may limit their use in high-power applications.
The spacing between vias is also important, as it affects the PCB’s ability to dissipate heat and maintain signal integrity. Proper via spacing helps minimize crosstalk and electromagnetic interference between adjacent vias.
Via Plating and Filling
To ensure proper conductivity, vias must be plated with a conductive material, typically copper. The plating process involves depositing a thin layer of copper on the walls of the via, creating a conductive path between layers.
In some cases, vias may also be filled with a non-conductive material, such as epoxy or resin, to improve the mechanical strength of the PCB and prevent solder from flowing into the via during the assembly process. Filled vias can also help dissipate heat more efficiently, as the filling material acts as a thermal conductor.
Traces: The Highways of the PCB
Traces are the conductive paths that carry electrical signals and power between components on a PCB. They are typically made of copper and are etched onto the PCB Layers during the manufacturing process.
Trace Width and Thickness
The width and thickness of traces are critical factors in determining PCB conductivity. Wider and thicker traces have lower resistance and can carry more current, making them suitable for power delivery and high-current applications.
However, wider traces also occupy more space on the PCB, which can limit the available routing area and the number of components that can be placed on the board. In high-speed designs, wider traces may also introduce unwanted capacitance and impact signal integrity.
The thickness of the copper used for traces is typically expressed in ounces per square foot (oz/ft²). Common copper thicknesses used in PCB manufacturing include:
Copper Thickness (oz/ft²) | Thickness (mm) | Typical Applications |
---|---|---|
0.5 oz/ft² | 0.0175 mm | Low-power, high-density designs |
1 oz/ft² | 0.0350 mm | General-purpose PCBs |
2 oz/ft² | 0.0700 mm | Power delivery, high-current applications |
3 oz/ft² | 0.1050 mm | High-power applications, automotive electronics |
Trace Routing and Spacing
Proper trace routing and spacing are essential for maintaining PCB conductivity and signal integrity. Some key considerations include:
-
Minimizing Trace Length: Shorter traces have lower resistance and inductance, which can improve signal integrity and reduce power loss.
-
Avoiding Sharp Bends: Sharp bends in traces can cause reflections and degrade signal quality. Use smooth, curved bends instead.
-
Maintaining Proper Spacing: Adequate spacing between traces helps minimize crosstalk and electromagnetic interference. The spacing requirements depend on factors such as the signal frequency, trace width, and the dielectric constant of the PCB material.
-
Impedance Matching: For high-speed signals, it is important to maintain consistent trace impedance to prevent reflections and ensure proper signal termination.
Trace Shielding and Grounding
In some cases, traces may need to be shielded or properly grounded to minimize electromagnetic interference and maintain signal integrity. Shielding techniques include:
-
Ground Planes: Placing a continuous ground plane on an adjacent layer can help shield traces from external interference and provide a low-impedance return path for signals.
-
Coplanar Waveguides: In this technique, traces are routed between two ground planes on the same layer, providing shielding and controlled impedance.
-
Microstrip and Stripline: These are controlled impedance trace geometries that use ground planes to provide shielding and maintain consistent trace impedance.
Proper grounding is also essential for maintaining PCB conductivity and preventing ground loops, which can cause noise and interference. Techniques such as star grounding, where all ground traces are connected to a single point, can help minimize ground-related issues.
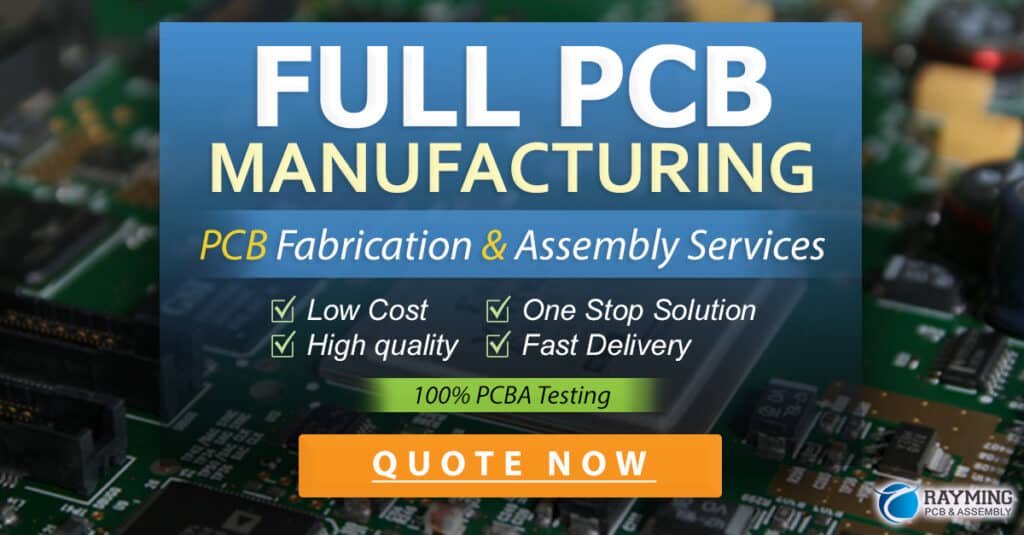
FAQ
1. What is the difference between a via and a trace?
A via is a conductive hole drilled through the layers of a PCB, allowing electrical signals to pass from one layer to another. Traces, on the other hand, are the conductive paths that carry electrical signals and power between components on the same layer of the PCB.
2. How does the size of a via affect PCB conductivity?
Smaller vias have lower inductance and capacitance, which can help maintain signal integrity, especially at high frequencies. However, smaller vias also have a lower current carrying capacity compared to larger vias, which may limit their use in high-power applications.
3. What is the purpose of via filling?
Vias may be filled with a non-conductive material, such as epoxy or resin, to improve the mechanical strength of the PCB and prevent solder from flowing into the via during the assembly process. Filled vias can also help dissipate heat more efficiently, as the filling material acts as a thermal conductor.
4. How does trace width affect PCB conductivity?
Wider traces have lower resistance and can carry more current, making them suitable for power delivery and high-current applications. However, wider traces also occupy more space on the PCB, which can limit the available routing area and the number of components that can be placed on the board.
5. What is the importance of trace spacing in PCB design?
Adequate spacing between traces helps minimize crosstalk and electromagnetic interference. The spacing requirements depend on factors such as the signal frequency, trace width, and the dielectric constant of the PCB material. Proper spacing is essential for maintaining signal integrity and preventing signal degradation.
Conclusion
PCB conductivity is a critical factor in ensuring the proper functioning and reliability of electronic devices. Vias and traces play a crucial role in maintaining conductivity, enabling electrical signals and power to flow through the PCB efficiently.
By understanding the characteristics and design considerations for vias and traces, engineers can optimize PCB conductivity and ensure that their designs meet the required performance and reliability standards. Proper via sizing, spacing, plating, and filling, along with appropriate trace width, thickness, routing, and shielding, are essential for achieving optimal PCB conductivity.
As electronic devices continue to become more complex and demanding, the importance of PCB conductivity will only continue to grow. By staying up-to-date with the latest techniques and best practices in PCB design, engineers can create high-performance, reliable electronic products that meet the needs of today’s rapidly evolving market.
No responses yet