Understanding NRE Cost
NRE (Non-Recurring Engineering) cost refers to the one-time expenses incurred during the design and development phase of a project. These costs are typically associated with creating a new product or modifying an existing one to meet specific requirements. NRE costs can include expenses related to research, design, prototyping, testing, and tooling.
Components of NRE Cost
The NRE cost consists of several components, each contributing to the overall expense:
-
Design and Engineering: This includes the cost of designing and engineering the product, which may involve creating blueprints, 3D models, and other technical documentation.
-
Prototyping: Building prototypes is an essential part of the development process, and it can be a significant contributor to the NRE cost. Prototyping expenses may include materials, labor, and equipment costs.
-
Testing and Validation: Before a product can be released, it must undergo rigorous testing and validation to ensure it meets the required specifications and standards. This process can be time-consuming and costly.
-
Tooling and Equipment: Depending on the product, specialized tooling and equipment may be required for manufacturing. The cost of designing and fabricating these tools is included in the NRE cost.
Factors Affecting NRE Cost
Several factors can influence the NRE cost of a project:
-
Project Complexity: The more complex the project, the higher the NRE cost is likely to be. Complex projects may require more design iterations, prototyping, and testing.
-
Material Selection: The choice of materials can have a significant impact on the NRE cost. Some materials may require specialized tooling or processing, which can increase expenses.
-
Manufacturing Process: The manufacturing process selected for the project can also affect the NRE cost. Some processes, such as injection molding, may require expensive tooling, while others, like 3D printing, may have lower upfront costs.
-
Quantity: The number of units to be produced can also influence the NRE cost. Higher production volumes may justify higher NRE costs, as the expenses can be amortized over a larger number of units.
Strategies for Optimizing NRE Cost
While NRE costs are an inevitable part of product development, there are several strategies that can help optimize these expenses:
1. Design for Manufacturing (DFM)
Design for Manufacturing (DFM) is an approach that involves designing products with manufacturing in mind from the outset. By considering the manufacturing process early in the design phase, it is possible to identify potential issues and optimize the design for efficiency and cost-effectiveness.
Some key principles of DFM include:
- Simplifying the design to minimize the number of parts and assembly steps
- Selecting materials that are easy to process and readily available
- Designing parts that can be manufactured using standard processes and equipment
- Incorporating features that facilitate assembly, such as snap-fits or self-locating components
2. Leverage Existing Technologies and Components
Another way to optimize NRE costs is to leverage existing technologies and components wherever possible. By using off-the-shelf parts or adapting existing designs, it is possible to reduce the amount of custom engineering required, which can significantly lower NRE expenses.
This approach can be particularly effective for projects that do not require highly specialized or unique components. For example, using a standard microcontroller or sensor instead of developing a custom solution can save time and money in the development process.
3. Collaborate with Suppliers and Partners
Collaborating with suppliers and partners can also help optimize NRE costs. By involving key stakeholders early in the development process, it is possible to identify potential issues and opportunities for cost savings.
For example, working closely with a manufacturing partner can help ensure that the design is optimized for their specific processes and equipment. This can help avoid costly redesigns or modifications later in the development cycle.
Similarly, collaborating with suppliers can help identify opportunities for cost savings through volume discounts, standardization, or other strategies.
4. Implement Agile Development Methodologies
Agile development methodologies, such as Scrum or Kanban, can also help optimize NRE costs by allowing for faster iteration and adaptation throughout the development process.
In an Agile approach, the development process is broken down into smaller, more manageable chunks, with regular feedback and adjustment along the way. This can help identify potential issues or opportunities for improvement early on, before significant resources have been invested.
Agile methodologies also prioritize close collaboration between team members and stakeholders, which can help ensure that everyone is aligned on project goals and priorities.
5. Invest in Prototyping and Testing
While prototyping and testing can be significant contributors to NRE costs, they are also essential for ensuring the success of the final product. Investing in these activities can help identify potential issues early on, before they become more costly to address.
Rapid prototyping techniques, such as 3D printing or CNC machining, can help accelerate the prototyping process and reduce costs compared to traditional methods. Similarly, automated testing tools can help streamline the validation process and catch potential issues more quickly and efficiently.
Managing NRE Cost in the Project Lifecycle
Effectively managing NRE costs requires a strategic approach throughout the project lifecycle. Here are some key considerations for each stage of the process:
1. Planning and Budgeting
During the planning and budgeting phase, it is essential to carefully estimate the expected NRE costs and allocate sufficient resources to cover these expenses. This may involve conducting market research, soliciting quotes from suppliers and partners, and developing detailed project plans and timelines.
It is also important to establish clear goals and priorities for the project, as well as metrics for measuring success. This can help ensure that resources are allocated effectively and that the project stays on track.
2. Design and Development
In the design and development phase, the focus should be on optimizing the design for manufacturing and leveraging existing technologies and components where possible. This may involve close collaboration with suppliers and partners, as well as regular design reviews and feedback sessions.
Agile development methodologies can be particularly effective during this phase, allowing for faster iteration and adaptation as the project progresses.
3. Prototyping and Testing
Prototyping and testing are critical for validating the design and identifying potential issues before moving into full-scale production. Investing in rapid prototyping techniques and automated testing tools can help accelerate this process and reduce costs.
It is also important to establish clear criteria for evaluating prototypes and test results, as well as a process for incorporating feedback and making necessary adjustments to the design.
4. Production and Launch
As the project moves into production and launch, the focus shifts to optimizing the manufacturing process and ensuring a smooth transition to full-scale operations. This may involve working closely with manufacturing partners to identify opportunities for cost savings and efficiency improvements.
It is also important to have a clear plan for managing any issues or challenges that may arise during production, such as quality control or supply chain disruptions.
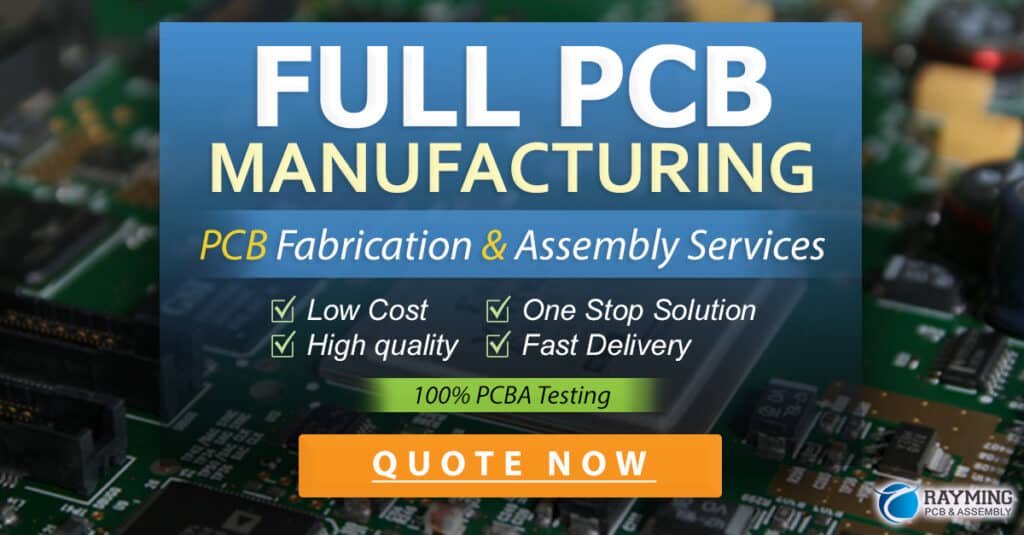
Frequently Asked Questions
-
What is NRE cost?
NRE (Non-Recurring Engineering) cost refers to the one-time expenses incurred during the design and development phase of a project. These costs are associated with creating a new product or modifying an existing one to meet specific requirements. -
What are the components of NRE cost?
The components of NRE cost include design and engineering, prototyping, testing and validation, and tooling and equipment. -
What factors can influence NRE cost?
Factors that can influence NRE cost include project complexity, material selection, manufacturing process, and quantity. -
How can NRE costs be optimized?
NRE costs can be optimized through strategies such as Design for Manufacturing (DFM), leveraging existing technologies and components, collaborating with suppliers and partners, implementing Agile development methodologies, and investing in prototyping and testing. -
Why is managing NRE cost important?
Managing NRE cost is important because it helps ensure that the project stays within budget and that resources are allocated effectively. Effectively managing NRE costs can also help accelerate time to market and improve the overall success of the project.
Conclusion
NRE costs are an inevitable part of product development, but there are several strategies that can help optimize these expenses and ensure the success of the project. By understanding the components and factors that influence NRE cost, and implementing best practices throughout the project lifecycle, it is possible to effectively manage these costs and deliver a high-quality product on time and within budget.
Strategy | Description |
---|---|
Design for Manufacturing (DFM) | Designing products with manufacturing in mind from the outset to optimize efficiency and cost-effectiveness. |
Leverage Existing Technologies and Components | Using off-the-shelf parts or adapting existing designs to reduce custom engineering and lower NRE expenses. |
Collaborate with Suppliers and Partners | Involving key stakeholders early in the development process to identify potential issues and opportunities for cost savings. |
Implement Agile Development Methodologies | Breaking down the development process into smaller, more manageable chunks with regular feedback and adjustment to identify issues early on. |
Invest in Prototyping and Testing | Using rapid prototyping techniques and automated testing tools to accelerate the validation process and catch potential issues more quickly and efficiently. |
By carefully planning and budgeting for NRE costs, optimizing the design and development process, and effectively managing the transition to production and launch, it is possible to make the project perfect and deliver a successful product to market.
No responses yet