What is a Flexible Flat Cable (FFC)?
A Flexible Flat Cable (FFC) is a type of electrical cable that consists of multiple flat conductors arranged parallel to each other. These conductors are typically made of copper and are insulated with a thin layer of plastic material, such as polyester or polyimide. FFCs are designed to be flexible, allowing them to bend and twist without damaging the conductors or affecting the electrical performance.
Key Characteristics of FFCs
- Flat and Thin Profile: FFCs have a low profile and are very thin, making them suitable for applications where space is limited.
- Flexibility: The flat conductors and thin insulation material allow FFCs to be highly flexible, enabling them to be routed through tight spaces and around obstacles.
- High Conductor Count: FFCs can have a large number of conductors, ranging from a few to several hundred, depending on the cable width and pitch.
- Pitch Variations: FFCs are available in different pitch sizes, which refers to the distance between the centers of adjacent conductors. Common pitch sizes include 0.5mm, 1.0mm, and 1.25mm.
- Termination Options: FFCs can be terminated using various methods, such as insulation displacement connectors (IDCs), zero insertion force (ZIF) connectors, or soldering.
Applications of FFCs
FFCs find applications in various industries and electronic devices, including:
- Consumer electronics: smartphones, tablets, laptops, digital cameras
- Automotive electronics: infotainment systems, sensors, displays
- Medical devices: portable monitors, wearable devices
- Industrial automation: robotics, motion control systems
- Aerospace and defense: avionics, satellite systems
What is a Flexible Printed Circuit (FPC)?
A Flexible Printed Circuit (FPC) is a type of printed circuit board (PCB) that is designed to be flexible. Unlike traditional rigid PCBs, FPCs can bend and flex without damaging the circuit or components. FPCs consist of a thin, flexible substrate, typically made of polyimide or polyester, with conductive traces printed or etched onto the surface.
Key Characteristics of FPCs
- Flexibility: FPCs are highly flexible and can be bent, twisted, or folded to fit into tight spaces or conform to unique shapes.
- Lightweight and Thin: FPCs are very lightweight and have a thin profile, making them ideal for applications where weight and space are critical factors.
- Integration of Components: FPCs can have electronic components, such as resistors, capacitors, and ICs, directly mounted onto the flexible substrate using surface mount technology (SMT).
- 3D Packaging: FPCs can be designed to have multiple layers and can be folded or shaped into three-dimensional configurations, enabling compact and efficient packaging of electronic systems.
- Customization: FPCs can be customized to meet specific design requirements, including unique shapes, sizes, and circuit layouts.
Applications of FPCs
FPCs are widely used in various industries and applications, such as:
- Wearable electronics: smartwatches, fitness trackers, health monitoring devices
- Medical devices: implantable devices, surgical instruments, diagnostic equipment
- Automotive electronics: dashboard displays, sensors, control modules
- Consumer electronics: smartphones, cameras, gaming devices
- Aerospace and defense: unmanned aerial vehicles (UAVs), satellites, military communication systems
Differences Between FFC and FPC
While FFCs and FPCs share some similarities, there are several key differences between these two types of cables:
- Construction: FFCs consist of flat conductors insulated with a plastic material, while FPCs have conductive traces printed or etched onto a flexible substrate.
- Component Integration: FPCs can have electronic components directly mounted onto the flexible substrate, whereas FFCs are primarily used for interconnections between components.
- Customization: FPCs offer more customization options in terms of shape, size, and circuit layout compared to FFCs, which are typically available in standard configurations.
- 3D Packaging: FPCs can be designed to have multiple layers and can be folded or shaped into three-dimensional configurations, while FFCs are generally limited to two-dimensional routing.
- Cost: FPCs tend to be more expensive than FFCs due to their more complex manufacturing process and the ability to integrate components directly onto the substrate.
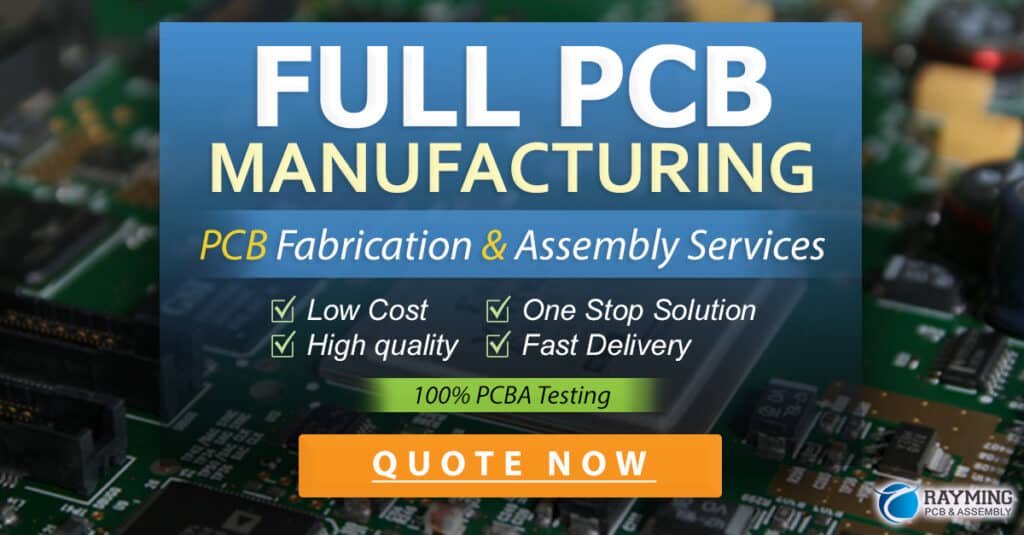
Comparison Table: FFC vs FPC
Feature | FFC | FPC |
---|---|---|
Construction | Flat conductors insulated with plastic | Conductive traces on flexible substrate |
Component Integration | Primarily used for interconnections | Can have components directly mounted |
Customization | Limited to standard configurations | Highly customizable in shape, size, and layout |
3D Packaging | Generally limited to 2D routing | Can be folded or shaped into 3D configurations |
Cost | Lower cost compared to FPCs | Higher cost due to complex manufacturing |
Frequently Asked Questions (FAQ)
-
Q: Can FFCs be used in place of FPCs?
A: While FFCs and FPCs serve similar purposes in providing flexible electrical connections, they are not always interchangeable. FPCs offer more customization options and can have components directly integrated, which may be required for certain applications. However, in situations where simple interconnections are needed, FFCs can be a suitable and cost-effective alternative. -
Q: What are the common pitches available for FFCs?
A: FFCs are available in various pitch sizes, with common options being 0.5mm, 1.0mm, and 1.25mm. The pitch refers to the distance between the centers of adjacent conductors. Smaller pitch sizes allow for higher conductor density, while larger pitches provide more space for conductor routing and termination. -
Q: Can FPCs be used in high-temperature environments?
A: FPCs can be designed to withstand high temperatures, depending on the materials used for the substrate and conductors. Polyimide-based FPCs are commonly used for high-temperature applications due to their excellent thermal stability. However, it is essential to consider the temperature ratings of the components and materials used in the FPC assembly to ensure reliable operation in high-temperature environments. -
Q: What are the advantages of using FFCs in electronic devices?
A: FFCs offer several advantages in electronic devices, including their thin and flat profile, which allows for space-saving designs. They are highly flexible, enabling them to be routed through tight spaces and around obstacles. FFCs also provide high conductor density, allowing for the transmission of multiple signals or power lines in a compact form factor. -
Q: How are FPCs manufactured?
A: FPCs are manufactured using a process similar to that of rigid PCBs, but with materials and techniques adapted for flexibility. The process typically involves the following steps: - Substrate preparation: A flexible substrate, such as polyimide or polyester, is cleaned and treated to improve adhesion.
- Circuit patterning: Conductive traces are formed on the substrate using techniques like photolithography, screen printing, or etching.
- Coverlay application: A protective coverlay is laminated onto the circuit pattern to provide insulation and mechanical protection.
- Component assembly: Electronic components are mounted onto the FPC using surface mount technology (SMT) or other suitable methods.
- Finishing and testing: The FPC assembly undergoes final finishing processes, such as solder mask application and surface finishing, followed by electrical and functional testing to ensure quality and reliability.
Conclusion
FFC and FPC are two types of flexible cables used in electronic devices and systems. While they share the common goal of providing flexible electrical connections, they have distinct differences in their construction, capabilities, and applications. FFCs are flat cables with multiple conductors, offering a thin profile and high flexibility for interconnections between components. On the other hand, FPCs are flexible printed circuits that can have components directly integrated onto the substrate and offer greater customization options.
When choosing between FFC and FPC, designers and engineers must consider factors such as space constraints, flexibility requirements, component integration needs, and cost. Understanding the unique characteristics and advantages of each type of cable helps in selecting the most suitable solution for a given application.
As technology continues to advance, the demand for flexible and compact electronic devices will drive further innovations in FFC and FPC designs. By leveraging the capabilities of these flexible cables, manufacturers can create products that are lighter, more compact, and more adaptable to various environments and user needs.
No responses yet