What is Flexible Flat Cable?
Flexible flat cable, also known as FFC, is a type of electrical cable that is designed to be thin, lightweight, and flexible. It consists of multiple conductors that are arranged in a flat, parallel configuration and are typically covered with a thin insulating material. The conductors are usually made of copper or other conductive materials, and the insulation is typically made of a flexible polymer such as polyester or polyimide.
FFCs are available in a variety of configurations, including single-sided, double-sided, and multi-layer designs. They can also be customized with different pitch sizes, conductor counts, and cable lengths to suit specific application requirements.
Benefits of Using Flexible Flat Cable
There are several benefits to using flexible flat cables in your designs, including:
Space Savings
One of the main advantages of FFCs is that they are very thin and compact compared to traditional round cables. This makes them ideal for use in applications where space is limited, such as in portable electronic devices or in tight spaces within larger systems.
Flexibility
As the name suggests, FFCs are designed to be flexible, which allows them to bend and flex without damaging the conductors or insulation. This makes them suitable for use in applications where the cable needs to move or flex regularly, such as in hinges, sliding mechanisms, or rotating joints.
Lightweight
FFCs are also very lightweight compared to traditional cables, which can help to reduce the overall weight of a device or system. This is particularly important in portable devices where weight is a critical factor.
High Density
Because FFCs have a flat, parallel configuration, they can accommodate a high number of conductors in a small space. This allows for higher signal density and more complex interconnects compared to traditional round cables.
Ease of Assembly
FFCs are typically easier to assemble and terminate than traditional cables, as they can be connected using simple connectors or soldered directly to a printed circuit board. This can help to reduce assembly time and costs.
Applications of Flexible Flat Cable
FFCs are used in a wide range of applications, including:
Consumer Electronics
FFCs are commonly used in consumer electronics devices such as laptops, cell phones, digital cameras, and portable media players. They are often used to connect displays, keyboards, and other components where flexibility and space savings are important.
Medical Devices
FFCs are also used in medical devices such as patient monitors, infusion pumps, and portable diagnostic equipment. They are valued for their flexibility, reliability, and ability to withstand repeated flexing and bending.
Automotive Electronics
FFCs are increasingly being used in automotive electronics, such as in dashboard displays, entertainment systems, and sensors. They offer a lightweight and flexible alternative to traditional wiring harnesses.
Industrial Automation
FFCs are used in industrial automation applications such as robotics, motion control systems, and machine vision equipment. They provide a reliable and flexible connection between sensors, actuators, and control systems.
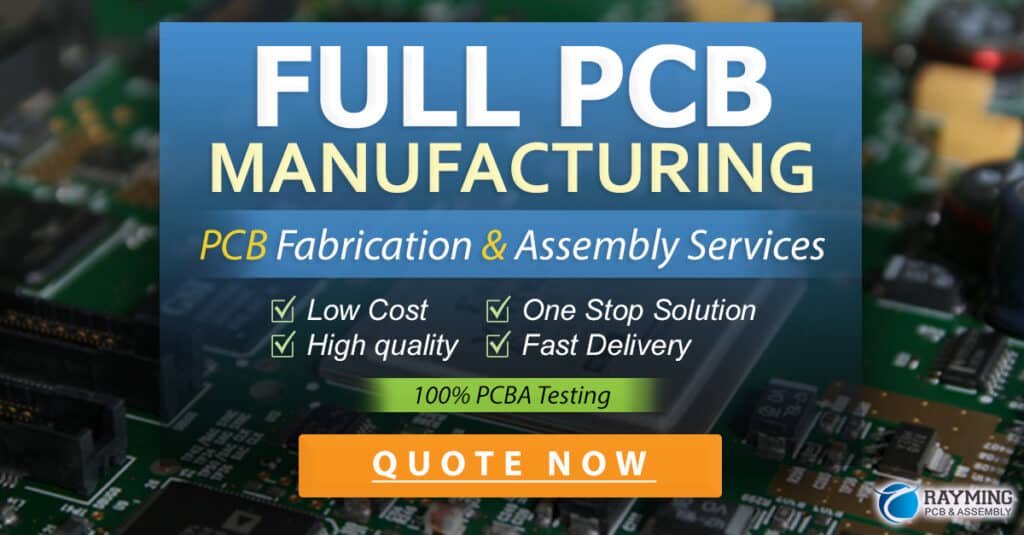
Designing with Flexible Flat Cable
When designing with flexible flat cables, there are several factors to consider to ensure optimal performance and reliability. Here are some tips and techniques for incorporating FFCs into your designs:
Choose the Right Cable
When selecting an FFC for your application, consider factors such as the number of conductors required, the pitch size (distance between conductors), the cable length, and the environmental conditions (e.g. temperature, humidity, vibration). Work with a reputable supplier to choose a cable that meets your specific requirements.
Consider Strain Relief
To prevent damage to the cable and ensure reliable performance, it is important to incorporate strain relief into your design. This can be achieved through the use of cable clamps, adhesives, or other mechanical means to secure the cable and prevent excessive bending or pulling.
Avoid Sharp Bends
While FFCs are designed to be flexible, they should not be bent too sharply or repeatedly in the same location, as this can cause damage to the conductors or insulation. Follow the manufacturer’s recommendations for minimum bend radius and avoid routing the cable in tight spaces or around sharp corners.
Use Appropriate Connectors
FFCs are typically terminated with specialized connectors that are designed to mate with the cable’s flat, parallel configuration. Choose connectors that are compatible with your chosen cable and that provide a secure, reliable connection. Consider factors such as contact pitch, orientation, and locking mechanisms.
Plan for Assembly
When designing with FFCs, it is important to consider the assembly process and ensure that the cable can be easily and reliably installed. This may involve designing custom fixtures or jigs to hold the cable in place during assembly, or incorporating features such as alignment pins or polarization keys to ensure correct orientation.
FAQ
Q: What is the difference between FFC and FPC?
A: FFC (Flexible Flat Cable) and FPC (Flexible Printed Circuit) are similar in that they are both designed to be thin, lightweight, and flexible. However, FFCs consist of discrete conductors that are laminated between layers of insulation, while FPCs have conductors that are printed or etched onto a flexible substrate. FPCs often include additional features such as surface-mounted components or shielding.
Q: Can FFCs be used in high-temperature applications?
A: Yes, FFCs are available with insulation materials that are rated for high-temperature use, such as polyimide or PTFE. However, it is important to choose a cable that is specifically designed for the temperature range and environmental conditions of your application.
Q: How do I terminate an FFC?
A: FFCs are typically terminated using specialized connectors that are designed to mate with the cable’s flat, parallel configuration. The cable is inserted into the connector and secured using a clamping mechanism or adhesive. Some FFCs can also be soldered directly to a printed circuit board.
Q: What is the maximum length for an FFC?
A: The maximum length for an FFC depends on factors such as the conductor size, insulation material, and application requirements. In general, FFCs are available in lengths up to several meters, but longer lengths may require special considerations for signal integrity and mechanical support.
Q: Can FFCs be used in dynamic applications?
A: Yes, FFCs are well-suited for use in dynamic applications where the cable needs to move or flex regularly, such as in hinges, sliding mechanisms, or rotating joints. However, it is important to choose a cable that is specifically designed for the required range of motion and to incorporate appropriate strain relief to prevent damage to the cable over time.
Conclusion
Flexible flat cables offer a versatile and reliable solution for interconnecting components in a wide range of applications, from consumer electronics to industrial automation. By understanding the benefits and limitations of FFCs and following best practices for design and assembly, engineers can create innovative and efficient designs that take full advantage of this technology.
When selecting an FFC for your application, consider factors such as conductor count, pitch size, length, and environmental conditions, and work with a reputable supplier to ensure that you are getting a high-quality cable that meets your specific requirements. By incorporating strain relief, avoiding sharp bends, and using appropriate connectors and assembly techniques, you can ensure reliable performance and long service life for your FFC-based designs.
Specification | Value |
---|---|
Conductor Material | Copper, Silver-Plated Copper, Tinned Copper |
Insulation Material | Polyester, Polyimide, PVC, FEP, PTFE |
Pitch Size | 0.5mm to 2.54mm |
Conductor Count | 4 to 80 |
Cable Length | Up to several meters |
Temperature Range | -40°C to +105°C (polyester), -40°C to +150°C (polyimide) |
Voltage Rating | Up to 300V |
Current Rating | Up to 1A per conductor |
Table 1: Typical specifications for flexible flat cables.
As the demand for smaller, lighter, and more flexible electronic devices continues to grow, flexible flat cables will play an increasingly important role in enabling innovative and efficient designs. By staying up-to-date with the latest developments in FFC technology and following best practices for design and assembly, engineers can create products that are more reliable, more compact, and more cost-effective than ever before.
No responses yet