Why Are Many Circuit Boards Blue or Green in Color?
Circuit boards, also known as printed circuit boards (PCBs), are the backbone of modern electronics. These flat boards are used to mechanically support and electrically connect electronic components using conductive pathways, tracks, or signal traces etched from copper sheets laminated onto a non-conductive substrate. One interesting aspect of PCBs is their color, with many boards having a distinctive blue or green hue. So why are circuit boards often blue or green in color?
The Role of Solder Mask in Circuit Board Color
The primary reason for the blue or green color of many circuit boards is the solder mask layer applied over the copper traces. Solder mask is a thin lacquer-like layer of polymer that is usually applied to the copper traces of a PCB for protection against oxidation and to prevent solder bridges from forming between closely spaced solder pads.
Solder mask is available in different colors, with green being the most common, followed by blue, black, red, yellow, and white. The availability of colored solder masks allows for aesthetic customization of circuit boards to match a product’s branding or for functional identification purposes.
Solder Mask Color | Popularity |
---|---|
Green | Most common |
Blue | Second most common |
Black | Less common |
Red | Less common |
Yellow | Rare |
White | Rare |
History of the Green Solder Mask Standard
The green solder mask has been used for decades and is something of an industry standard. Its origins date back to the early days of PCB manufacturing when the materials and processes were far less advanced than today.
In the 1960s, PCBs were screenprinted with an oil-based solder mask that had a dull greenish-brown color due to the materials used. As PCB manufacturing processes evolved, the development of UV-curable solder mask inks allowed for other colors like blue to emerge. However, green remained the most popular color choice, likely due to its familiarity and the fact that it provides good contrast for inspection of fine details.
The Emergence of Blue Circuit Boards
While green remains the most common solder mask color, in recent years there has been a trend towards blue PCBs, particularly in consumer electronics. The increasing use of blue circuit boards can be attributed to several factors:
-
Aesthetics: Blue PCBs can provide a distinctive look that helps products stand out. Many consumer electronics companies use blue PCBs to showcase the internal components as a design feature.
-
Branding: The use of colored PCBs can tie into a company’s brand identity. Blue is a popular choice for tech company branding.
-
Improved Materials: Advances in polymer technology have led to the development of new solder mask inks that offer better performance and a wider range of color options.
-
Inspection: Like green, blue provides good contrast for visual inspection of PCBs.
Benefits of Colored Solder Masks Beyond Aesthetics
Beyond aesthetics and branding, the use of colored solder masks can offer functional benefits as well:
-
Improved Visibility: The use of contrasting Solder Mask Colors can improve the visibility of PCB features and make it easier for automated optical inspection (AOI) systems to detect defects.
-
Functional Identification: Different color solder masks can be used to identify different circuit board assemblies or revisions at a glance.
-
UV Protection: Some colored solder masks offer increased resistance to UV light, which can cause greening or yellowing of the PCB over time.
-
Heat Dissipation: The use of lighter colors like white can help with heat dissipation by reflecting more heat away from the board.
The Manufacturing Process of Colored Circuit Boards
The process of manufacturing circuit boards with colored solder masks involves several key steps:
-
Circuit Board Fabrication: The bare PCB is fabricated using standard processes like etching, drilling, and plating.
-
Solder Mask Application: The liquid photoimageable solder mask ink is applied to both sides of the board by dipping, spraying or screen printing.
-
Solder Mask Imaging: The solder mask is selectively exposed to UV light through a photomask or laser-imaged. The exposed areas cure and harden.
-
Developing: The unexposed areas of the solder mask are removed using a chemical developer solution, leaving only the cured solder mask on the PCB.
-
Final Curing: The solder mask is fully cured using UV light and/or heat to achieve its final properties.
-
Surface Finish Application: The exposed copper pads are coated with the specified surface finish, such as HASL, ENIG, or OSP.
Process Step | Description |
---|---|
Circuit Board Fabrication | Etching, drilling, plating of bare PCB |
Solder Mask Application | Liquid solder mask ink applied by dipping, spraying, screen printing |
Solder Mask Imaging | UV exposure of solder mask through photomask or laser-imaged |
Developing | Removal of uncured solder mask with chemical developer |
Final Curing | Full UV/thermal cure of solder mask |
Surface Finish Application | Exposed pads coated with specified surface finish (HASL, ENIG, OSP) |
Choosing the Right Solder Mask Color for Your PCB
When selecting a solder mask color for a PCB design, there are several factors to consider:
Aesthetics and Branding
The solder mask color can be chosen to match the aesthetic requirements of the end product or to align with company branding. Custom colors are often available for high-volume orders.
Inspection and Testability
Contrasting solder mask colors like blue or green offer good visibility for inspection and testing of fine pitch components and circuitry. Automated optical inspection (AOI) systems may have specific color requirements for optimal performance.
Environment and Reliability
For PCBs used in harsh environments or mission-critical applications, solder mask properties beyond color need to be considered. High-temperature or UV-resistant solder masks may be necessary to ensure long-term reliability.
Cost and Availability
While green is the most widely available and lowest cost solder mask color, other standard colors like blue and black are readily available from most PCB manufacturers without a significant cost premium. Custom colors may require higher minimum order quantities and setup charges.
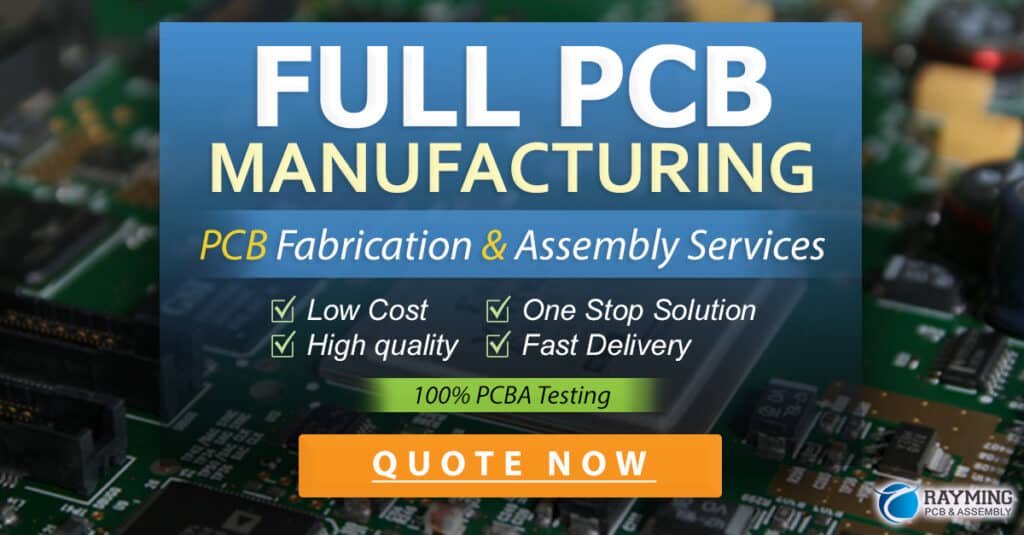
Frequently Asked Questions (FAQ)
1. Are blue circuit boards more expensive than green ones?
In most cases, there is no significant cost difference between blue and green solder masks. Both are readily available standard color options from PCB manufacturers.
2. Can I get a PCB with a custom solder mask color?
Yes, many PCB manufacturers offer custom solder mask colors for high-volume orders. However, there may be higher minimum order quantities and setup charges compared to standard colors.
3. Does the solder mask color affect circuit board performance?
In general, the solder mask color itself does not directly impact the electrical performance of the PCB. However, some specialty solder masks formulated for high-temperature or UV resistance may have different properties than standard masks.
4. Are there any industry standards for PCB solder mask colors?
There are no hard industry standards, but green is considered the default solder mask color for PCBs. Blue has emerged as a popular second choice, particularly for consumer electronics.
5. Can I mix different solder mask colors on the same PCB?
Yes, it is possible to use multiple solder mask colors on different areas of the same PCB. This is sometimes done for functional identification of different circuit blocks or for cosmetic purposes. However, it does require additional processing steps and may incur extra costs.
Conclusion
The blue or green color of many circuit boards is primarily due to the solder mask layer applied over the copper traces. While green is the traditional default choice, blue has gained popularity in recent years for its aesthetic appeal and use in consumer electronics branding.
The choice of solder mask color depends on various factors, including aesthetics, inspection requirements, environment, and cost. With a wide range of standard and custom color options now available, PCB designers have more flexibility than ever to create visually distinctive and functional circuit boards.
As PCB manufacturing technologies continue to evolve, it’s likely that we’ll see even more innovations in solder mask materials and colors in the future. Regardless of the color, the humble circuit board will remain the unsung hero that powers our increasingly electronic world.
No responses yet