Definition of PCB Solder Mask
PCB solder mask, also known as solder resist or solder stop mask, is a thin layer of polymer applied to the copper traces of a printed circuit board (PCB) to protect them from oxidation, prevent solder bridges, and provide electrical insulation. The solder mask is typically applied over the entire PCB surface, except for the areas where components will be soldered, such as pads and plated through-holes.
Functions of PCB Solder Mask
The primary functions of PCB solder mask include:
-
Protection against oxidation: Solder mask prevents the copper traces from oxidizing, which can lead to poor solderability and reduced electrical conductivity.
-
Electrical insulation: The solder mask layer provides electrical insulation between the copper traces, preventing short circuits and ensuring proper circuit functionality.
-
Solder bridge prevention: By covering the areas between the copper traces, solder mask helps prevent solder bridges from forming during the soldering process.
-
Improved aesthetics: Solder mask gives the PCB a clean, professional appearance and can be used to add text, logos, or other markings to the board.
Types of PCB Solder Mask
There are two main types of solder mask used in PCB manufacturing:
1. Liquid Photoimageable Solder Mask (LPISM)
LPISM is the most common type of solder mask used in the PCB industry. It is applied as a liquid and then exposed to UV light through a photomask to create the desired pattern. The unexposed areas are then washed away, leaving the solder mask only on the desired areas.
Advantages of LPISM:
- High resolution and accuracy
- Excellent adhesion to the PCB surface
- Good electrical insulation properties
- Available in various colors
2. Dry Film Solder Mask (DFSM)
DFSM is a solid film that is laminated onto the PCB surface using heat and pressure. The film is then exposed to UV light through a photomask, and the unexposed areas are removed using a chemical developer.
Advantages of DFSM:
- Faster application process compared to LPISM
- Consistent thickness across the PCB surface
- Good chemical resistance
- Suitable for high-volume production
Solder Mask Application Process
The solder mask application process typically involves the following steps:
-
Surface preparation: The PCB surface is cleaned to remove any contaminants and ensure good adhesion of the solder mask.
-
Solder mask application: The solder mask is applied to the PCB surface using either the LPISM or DFSM method.
-
Exposure: The solder mask is exposed to UV light through a photomask to create the desired pattern.
-
Development: The unexposed areas of the solder mask are removed using a chemical developer.
-
Curing: The solder mask is cured using heat to improve its mechanical and chemical properties.
-
Inspection: The PCB is inspected for any defects or inconsistencies in the solder mask application.
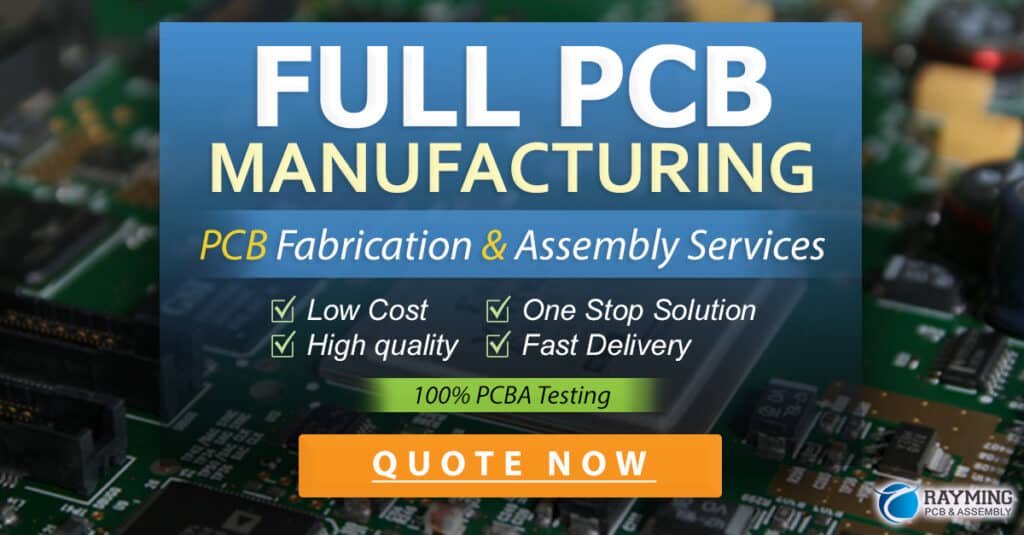
Solder Mask Colors and Markings
Solder mask is available in various colors, with green being the most common. Other popular colors include blue, red, yellow, black, and white. The choice of color is often based on aesthetic preferences or specific industry requirements.
In addition to colors, solder mask can also be used to add text, logos, or other markings to the PCB. This is typically done using a silkscreen printing process, where the markings are printed onto the solder mask surface using a fine mesh screen and ink.
Solder Mask Performance Characteristics
To ensure optimal performance, solder mask must meet certain key characteristics:
-
Adhesion: The solder mask must adhere well to the PCB surface to prevent delamination or peeling.
-
Electrical insulation: The solder mask should provide sufficient electrical insulation between the copper traces to prevent short circuits.
-
Chemical resistance: The solder mask must be resistant to the chemicals used in the PCB manufacturing process, as well as to the operating environment of the finished product.
-
Thermal stability: The solder mask should maintain its properties over the expected temperature range of the PCB during operation.
-
Solder resistance: The solder mask must be resistant to the high temperatures and chemicals used during the soldering process.
Solder Mask Standards and Specifications
Several standards and specifications govern the use of solder mask in PCB manufacturing:
- IPC-SM-840: This standard defines the requirements for the qualification and performance of permanent solder mask.
- IPC-A-600: This standard provides acceptability criteria for printed circuit boards, including solder mask requirements.
- MIL-PRF-31032: This military specification defines the requirements for solder mask used in high-reliability applications.
Standard | Description |
---|---|
IPC-SM-840 | Requirements for qualification and performance of permanent solder mask |
IPC-A-600 | Acceptability criteria for printed circuit boards, including solder mask requirements |
MIL-PRF-31032 | Military specification for solder mask used in high-reliability applications |
Common Solder Mask Defects and Troubleshooting
Several defects can occur during the solder mask application process, which can impact the quality and reliability of the finished PCB:
-
Pinholes: Small holes in the solder mask that expose the underlying copper traces, increasing the risk of short circuits and corrosion.
-
Solder mask undercut: When the solder mask does not fully adhere to the edges of the copper traces, allowing solder to flow underneath and potentially cause short circuits.
-
Solder mask residue: Incomplete removal of unexposed solder mask, which can interfere with the soldering process and cause poor solder joint formation.
-
Misregistration: Misalignment between the solder mask and the copper traces, which can result in exposed copper or solder mask covering areas intended for soldering.
To troubleshoot and prevent these defects, PCB manufacturers should:
- Ensure proper surface cleaning and preparation before solder mask application.
- Use high-quality solder mask materials and follow the manufacturer’s application guidelines.
- Regularly maintain and calibrate the solder mask application equipment.
- Implement strict quality control measures and inspect the PCBs at various stages of the manufacturing process.
Frequently Asked Questions (FAQ)
-
What is the purpose of solder mask on a PCB?
Answer: Solder mask serves to protect the copper traces from oxidation, provide electrical insulation, prevent solder bridges, and improve the overall aesthetics of the PCB. -
What is the difference between liquid photoimageable solder mask (LPISM) and dry film solder mask (DFSM)?
Answer: LPISM is applied as a liquid and then exposed to UV light to create the desired pattern, while DFSM is a solid film that is laminated onto the PCB surface and then exposed to UV light. LPISM offers high resolution and accuracy, while DFSM is faster to apply and provides consistent thickness across the PCB surface. -
What is the most common color for solder mask?
Answer: The most common color for solder mask is green, but other colors such as blue, red, yellow, black, and white are also available. -
Can solder mask be used to add text or logos to a PCB?
Answer: Yes, solder mask can be used to add text, logos, or other markings to a PCB using a silkscreen printing process. -
What are some common defects that can occur during the solder mask application process?
Answer: Common solder mask defects include pinholes, solder mask undercut, solder mask residue, and misregistration. These defects can be prevented by ensuring proper surface preparation, using high-quality materials, maintaining equipment, and implementing strict quality control measures.
Conclusion
PCB solder mask is a critical component in the manufacturing of printed circuit boards, providing essential protection, insulation, and aesthetic benefits. By understanding the types of solder mask, application processes, performance characteristics, and common defects, PCB designers and manufacturers can ensure the production of high-quality, reliable circuits that meet the demands of various industries and applications. Adhering to industry standards and best practices for solder mask application and troubleshooting will help minimize defects and improve the overall performance of the finished product.
No responses yet