Introduction to PCB Surface Mount Technology (PCB-SMP)
Surface Mount Technology (SMT) has revolutionized the PCB manufacturing industry by enabling the production of smaller, lighter, and more densely populated printed circuit boards (PCBs). PCB-SMP refers to the process of mounting electronic components directly onto the surface of a PCB, as opposed to through-hole mounting, where components are inserted into drilled holes and soldered on the opposite side of the board. This technology has become the dominant method for assembling electronic devices, offering numerous advantages over traditional through-hole mounting.
Advantages of PCB-SMP
- Miniaturization: SMT allows for the use of smaller components, resulting in more compact PCBs and electronic devices.
- Increased component density: With SMT, more components can be placed on a single PCB, enabling more complex designs and functionality.
- Improved performance: SMT components have shorter leads, reducing parasitic capacitance and inductance, which improves signal integrity and overall performance.
- Cost-effectiveness: Automated SMT Assembly processes reduce labor costs and increase production efficiency, making it a more cost-effective solution for high-volume production.
- Enhanced reliability: SMT components have a stronger mechanical bond to the PCB, resulting in better resistance to vibration and thermal stress.
Key Elements of a PCB Surface Mount Plant
A PCB Surface Mount Plant is a facility equipped with the necessary machinery, tools, and personnel to carry out the SMT assembly process. The following are the key elements of a PCB-SMP:
1. Solder Paste Printing
The first step in the SMT assembly process is applying solder paste to the PCB. Solder paste is a mixture of tiny solder particles suspended in a flux medium. The paste is applied to the PCB using a stencil printer, which ensures precise and consistent solder paste deposition on the component pads.
Stencil Printers
Stencil printers are automated machines that apply solder paste to the PCB through a stencil. The stencil is a thin metal sheet with openings that correspond to the component pads on the PCB. The printer aligns the stencil with the PCB and uses a squeegee to force the solder paste through the openings onto the pads.
Stencil Printer Type | Advantages | Disadvantages |
---|---|---|
Manual | Low cost, suitable for low-volume production | Slower, less consistent |
Semi-Automatic | Increased speed and consistency compared to manual printers | Higher cost than manual printers |
Fully Automatic | High speed, high precision, suitable for high-volume production | Highest cost, requires skilled operators |
2. Component Placement
Once the solder paste is applied, the next step is to place the surface mount components onto the PCB. This process is typically carried out by pick-and-place machines, which use vacuum nozzles or grippers to pick up components from feeders and place them accurately on the solder paste-coated pads.
Pick-and-Place Machines
Pick-and-place machines are automated systems that place surface mount components onto the PCB with high speed and precision. These machines use computer vision and advanced algorithms to locate and align components accurately.
Pick-and-Place Machine Type | Placement Speed (components per hour) | Accuracy (µm) |
---|---|---|
High-Speed | 60,000 – 100,000 | ±50 |
Medium-Speed | 20,000 – 60,000 | ±30 |
High-Precision | 5,000 – 20,000 | ±20 |
3. Reflow Soldering
After component placement, the PCB undergoes reflow soldering, where the entire board is heated in a controlled manner to melt the solder paste and form permanent electrical and mechanical connections between the components and the PCB.
Reflow Ovens
Reflow ovens are specialized ovens that heat the PCB according to a precise temperature profile, ensuring proper solder joint formation without damaging the components or the PCB.
Reflow Oven Type | Heating Method | Advantages | Disadvantages |
---|---|---|---|
Convection | Hot air circulation | Even heating, suitable for most PCBs | Slower than infrared |
Infrared | Infrared radiation | Fast heating, energy-efficient | Uneven heating, shadowing effects |
Vapor Phase | Condensation of vapor | Uniform heating, minimal thermal stress | Higher cost, limited PCB size |
4. Inspection and Quality Control
To ensure the quality and reliability of the assembLED PCBs, various inspection and quality control techniques are employed in a PCB-SMP.
Automated Optical Inspection (AOI)
AOI systems use high-resolution cameras and advanced image processing algorithms to detect surface mount defects such as missing components, misaligned components, and solder bridging.
X-Ray Inspection
X-ray inspection is used to detect hidden defects, such as voids in solder joints or components with internal defects, which cannot be detected by optical inspection methods.
In-Circuit Testing (ICT)
ICT is a test method that uses a bed-of-nails fixture to make electrical contact with the PCB and verify the functionality of individual components and the interconnections between them.
PCB-SMP Process Flow
The typical process flow in a PCB Surface Mount Plant is as follows:
- Solder Paste Printing
- Component Placement
- Reflow Soldering
- Automated Optical Inspection (AOI)
- X-Ray Inspection (if required)
- In-Circuit Testing (ICT)
- Final Inspection and Packaging
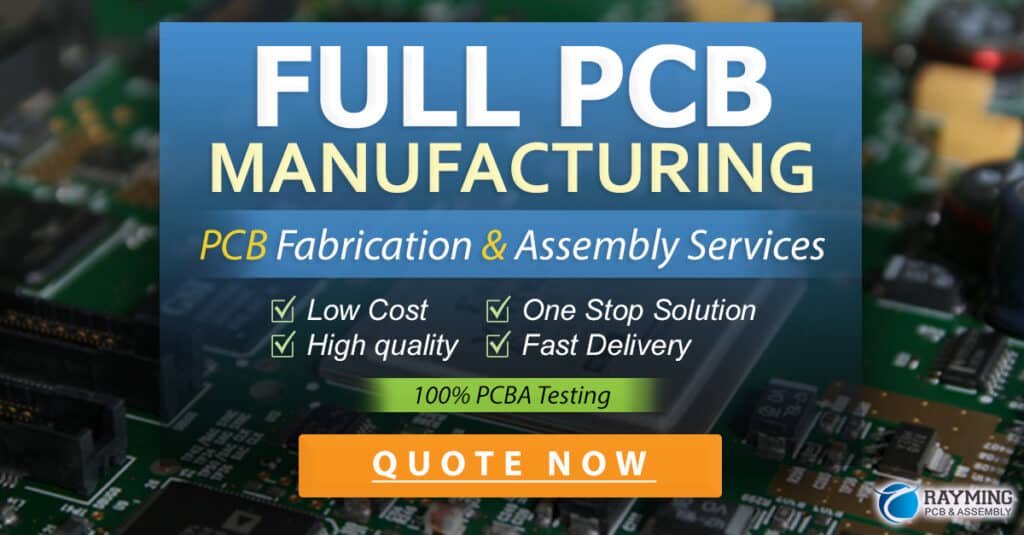
Challenges in PCB-SMP
Despite the numerous advantages of PCB-SMP, there are several challenges that manufacturers face:
- Component miniaturization: As components become smaller, placing and soldering them accurately becomes more challenging.
- Mixed technology boards: PCBs with both surface mount and through-hole components require special considerations in the assembly process.
- High-density designs: Increased component density can lead to thermal management issues and signal integrity challenges.
- Counterfeit components: The use of counterfeit or substandard components can compromise the quality and reliability of the assembled PCBs.
Future Trends in PCB-SMP
As the electronics industry continues to evolve, PCB-SMP is expected to adapt to new trends and technologies:
- Advanced packaging technologies: The adoption of packaging technologies such as System-in-Package (SiP) and Package-on-Package (PoP) will require new assembly techniques and equipment.
- Flexible and stretchable electronics: The growing demand for flexible and stretchable electronics will necessitate the development of new materials and assembly processes.
- Industry 4.0 and smart manufacturing: The integration of Industrial Internet of Things (IIoT) and artificial intelligence (AI) in PCB-SMP will enable real-time process monitoring, predictive maintenance, and optimization of the assembly process.
- Sustainability and environmental considerations: The focus on sustainable manufacturing practices will drive the adoption of lead-free soldering and the development of eco-friendly materials and processes.
Frequently Asked Questions (FAQ)
- What is the difference between Surface Mount Technology (SMT) and Through-Hole Technology (THT)?
-
SMT involves mounting components directly onto the surface of the PCB, while THT involves inserting component leads through drilled holes in the PCB and soldering them on the opposite side.
-
What are the main advantages of using SMT in PCB Assembly?
-
SMT enables the production of smaller, lighter, and more densely populated PCBs, improves performance, and is more cost-effective for high-volume production.
-
What is the purpose of solder paste in the SMT assembly process?
-
Solder paste is a mixture of tiny solder particles suspended in a flux medium. It is applied to the component pads on the PCB to facilitate the soldering process during reflow.
-
How do pick-and-place machines work in a PCB-SMP?
-
Pick-and-place machines use vacuum nozzles or grippers to pick up components from feeders and place them accurately on the solder paste-coated pads on the PCB. They use computer vision and advanced algorithms for precise component placement.
-
What is the role of reflow soldering in the SMT assembly process?
- Reflow soldering is the process of heating the PCB and components in a controlled manner to melt the solder paste and form permanent electrical and mechanical connections between the components and the PCB.
Conclusion
PCB Surface Mount Technology has become the dominant method for assembling electronic devices, offering numerous advantages over traditional through-hole mounting. A PCB Surface Mount Plant is equipped with the necessary machinery, tools, and personnel to carry out the SMT assembly process efficiently and effectively. By understanding the key elements, process flow, challenges, and future trends in PCB-SMP, manufacturers can optimize their assembly processes and stay competitive in the ever-evolving electronics industry.
No responses yet