Introduction to PCB Drilled Holes
Printed Circuit Boards (PCBs) are essential components in electronic devices, serving as the foundation for mounting and interconnecting electronic components. One crucial aspect of PCB design and manufacturing is the creation of drilled holes. These holes serve various purposes, such as allowing component leads to pass through, enabling the mounting of components, and facilitating the interconnection of layers in multi-layer PCBs.
In this comprehensive article, we will dive deep into the world of PCB drilled holes, covering everything you need to know to avoid surprises and ensure the success of your PCB projects.
Types of PCB Drilled Holes
PCB drilled holes can be categorized into several types based on their purpose and characteristics. Let’s explore each type in detail.
Through Holes
Through holes are the most common type of drilled holes in PCBs. As the name suggests, these holes pass completely through the PCB, allowing component leads to be inserted and soldered on both sides of the board. Through holes are typically used for mounting through-hole components, such as resistors, capacitors, and connectors.
Blind Vias
Blind vias are drilled holes that start from one side of the PCB and terminate at a specific inner layer without reaching the opposite side of the board. These holes are used to interconnect the outer layer with one or more inner layers, facilitating more complex routing and saving space on the PCB surface.
Buried Vias
Buried vias are drilled holes that are located entirely within the inner layers of a multi-layer PCB. They do not extend to either side of the board. Buried vias are used to interconnect two or more inner layers, providing a means for efficient routing and reducing the overall size of the PCB.
Microvias
Microvias are small-diameter drilled holes, typically less than 0.15mm in diameter. They are commonly used in high-density interconnect (HDI) PCBs to achieve fine-pitch connections and higher routing density. Microvias can be drilled using advanced techniques like laser drilling or plasma etching.
Drilled Hole Specifications
When designing and manufacturing PCBs with drilled holes, several key specifications need to be considered to ensure the holes meet the required functionality and reliability.
Hole Diameter
The hole diameter is a critical parameter that determines the size of the drilled hole. It is measured in millimeters (mm) or mils (thousandths of an inch). The hole diameter should be selected based on the component lead diameter, the required clearance, and the manufacturing capabilities.
Component Type | Typical Hole Diameter Range |
---|---|
Resistors | 0.6mm – 0.8mm |
Capacitors | 0.6mm – 0.8mm |
Integrated Circuits | 0.7mm – 1.0mm |
Connectors | 0.8mm – 3.0mm |
Hole Tolerance
Hole tolerance refers to the acceptable variation in the hole diameter from the specified value. It is important to consider hole tolerance to ensure proper fit and solderability of component leads. The tolerance is usually specified as a plus/minus value in millimeters or mils.
Hole Diameter Range | Typical Tolerance |
---|---|
0.3mm – 0.8mm | ±0.05mm |
0.8mm – 1.5mm | ±0.1mm |
1.5mm – 3.0mm | ±0.15mm |
Plating
Drilled holes in PCBs are often plated with a conductive material, such as copper, to provide electrical connectivity and protect the hole walls from oxidation. The plating thickness and material should be specified based on the application requirements and the PCB manufacturing process.
Plating Material | Typical Thickness Range |
---|---|
Copper | 25µm – 35µm |
Gold | 0.05µm – 0.2µm |
Silver | 0.1µm – 0.3µm |
Aspect Ratio
The aspect ratio of a drilled hole is the ratio of the hole depth to its diameter. It is an important consideration when designing PCBs with high layer counts or thick substrates. The aspect ratio can impact the manufacturability and reliability of the drilled holes.
PCB Thickness | Maximum Recommended Aspect Ratio |
---|---|
0.8mm | 8:1 |
1.6mm | 10:1 |
2.4mm | 12:1 |
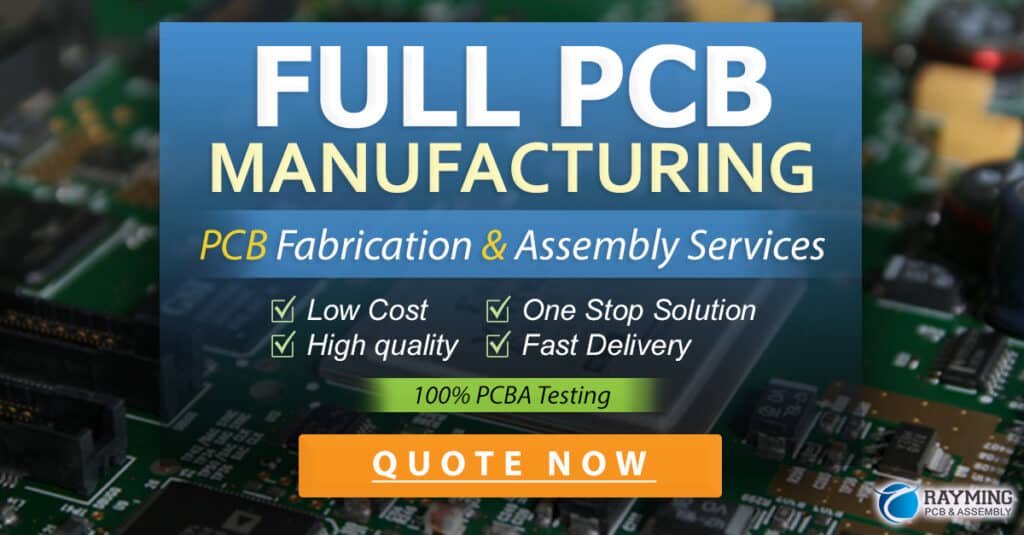
Design Considerations for PCB Drilled Holes
When designing PCBs with drilled holes, several key factors should be taken into account to ensure the holes are functional, reliable, and manufacturable.
Pad Size and Clearance
The pad size and clearance around drilled holes are critical for ensuring proper solderability and preventing short circuits. The pad size should be large enough to accommodate the hole diameter, the component lead, and any potential misalignment during assembly.
Hole Diameter | Recommended Pad Diameter | Recommended Clearance |
---|---|---|
0.6mm | 1.0mm – 1.2mm | 0.2mm – 0.3mm |
0.8mm | 1.2mm – 1.4mm | 0.2mm – 0.3mm |
1.0mm | 1.4mm – 1.6mm | 0.3mm – 0.4mm |
Hole Placement and Spacing
The placement and spacing of drilled holes on the PCB should be carefully considered to avoid manufacturing issues and ensure proper functionality. Holes should be placed with sufficient spacing to accommodate the required pad sizes and clearances, as well as to facilitate efficient routing.
PCB Layer Count | Minimum Recommended Hole Spacing |
---|---|
1 – 2 layers | 0.8mm |
4 layers | 1.0mm |
6 – 8 layers | 1.2mm |
Drill File Generation
To communicate the drilled hole information to the PCB manufacturer, a drill file must be generated from the PCB design software. The drill file contains the location, size, and type of each drilled hole on the PCB. It is essential to ensure the drill file is accurate and complete to avoid manufacturing errors.
Manufacturing Process for PCB Drilled Holes
The manufacturing process for PCB drilled holes involves several steps to ensure the holes are accurately created and meet the specified requirements.
Drilling Methods
PCB drilled holes can be created using various drilling methods, depending on the hole size, quantity, and required precision.
- Mechanical Drilling: This is the most common method for creating drilled holes in PCBs. It uses high-speed drill bits to mechanically remove material and create the holes.
- Laser Drilling: Laser drilling is used for creating small-diameter holes, such as microvias, with high precision. It uses a focused laser beam to vaporize the material and create the holes.
- Plasma Etching: Plasma etching is another method for creating small-diameter holes, particularly in high-density PCBs. It uses a plasma arc to remove material and create the holes.
Deburring and Cleaning
After the drilling process, the PCB undergoes deburring and cleaning to remove any debris or burrs around the hole edges. This step is crucial for ensuring the holes are clean and smooth, facilitating proper plating and component assembly.
Plating and Finishing
Once the holes are drilled and cleaned, they are plated with a conductive material to provide electrical connectivity and protect the hole walls. The plating process typically involves electroless copper deposition followed by electrolytic copper plating. Additional finishing layers, such as gold or silver, may be applied depending on the application requirements.
Common Challenges and Solutions
When working with PCB drilled holes, several challenges may arise that can impact the functionality and reliability of the PCB. Let’s explore some common challenges and their solutions.
Hole Misalignment
Hole misalignment occurs when the drilled holes do not align accurately with the pads or other features on the PCB. This can lead to assembly issues and poor electrical connections.
Solutions:
– Use precise drilling equipment and maintain proper calibration.
– Implement registration marks or fiducials on the PCB to aid in alignment.
– Consider using a larger pad size to accommodate potential misalignment.
Inadequate Plating
Inadequate plating can result in poor electrical connectivity, reduced hole wall strength, and susceptibility to corrosion.
Solutions:
– Specify the appropriate plating thickness and material based on the application requirements.
– Ensure proper cleaning and surface preparation before plating.
– Perform quality control checks to verify plating thickness and uniformity.
Hole Breakout
Hole breakout occurs when the drilling process causes the hole to extend beyond the desired pad or copper area, potentially causing short circuits or weakening the PCB Structure.
Solutions:
– Use precise drilling equipment and maintain proper drill bit sharpness.
– Adjust the drilling parameters, such as feed rate and spindle speed, to minimize breakout.
– Consider using a smaller hole diameter or increasing the pad size to provide more clearance.
Frequently Asked Questions (FAQ)
- What is the minimum hole diameter that can be drilled in a PCB?
-
The minimum hole diameter depends on the PCB thickness and the drilling method used. With mechanical drilling, holes as small as 0.2mm can be achieved. Laser drilling and plasma etching can create even smaller holes, down to 0.1mm or less.
-
How do I choose the appropriate hole size for my components?
-
The hole size should be selected based on the component lead diameter, allowing for some clearance. Refer to the component datasheet or consult with the PCB manufacturer for recommended hole sizes.
-
Can I have different hole sizes on the same PCB?
-
Yes, it is possible to have multiple hole sizes on a single PCB. The PCB design software allows you to specify different hole sizes for different components or purposes.
-
What is the maximum aspect ratio for drilled holes in PCBs?
-
The maximum recommended aspect ratio depends on the PCB thickness. Generally, an aspect ratio of 8:1 to 12:1 is considered achievable, depending on the specific manufacturing capabilities.
-
How can I ensure the accuracy and reliability of drilled holes in my PCBs?
- To ensure the accuracy and reliability of drilled holes, consider the following:
- Use precise drilling equipment and maintain proper calibration.
- Specify appropriate hole tolerances and plating requirements.
- Implement proper design practices, such as pad sizes and clearances.
- Collaborate closely with the PCB manufacturer and communicate your requirements clearly.
Conclusion
Drilled holes are a critical aspect of PCB design and manufacturing, enabling the mounting and interconnection of electronic components. Understanding the types of drilled holes, their specifications, design considerations, and manufacturing processes is essential for avoiding surprises and ensuring the success of your PCB projects.
By carefully considering hole diameters, tolerances, plating, aspect ratios, pad sizes, clearances, and placement, you can design PCBs with reliable and functional drilled holes. Collaborating closely with your PCB manufacturer and staying informed about the latest manufacturing capabilities and best practices will help you navigate the challenges and achieve optimal results.
With this comprehensive knowledge of PCB drilled holes, you are well-equipped to tackle your next PCB design project with confidence and avoid any unexpected surprises along the way.
No responses yet