How Press-Fit Holes Work
The principle behind press-fit holes relies on the elastic deformation of the materials being joined. When the mating component is forced into the slightly smaller hole, the material around the hole elastically deforms, creating a strong compressive force that holds the components together. This process is also known as interference fit or friction fit.
Advantages of Press-Fit Holes
Press-fit holes offer several advantages over other fastening methods:
- Simplicity: Press-fit assembly is a simple and straightforward process that does not require additional fasteners or adhesives.
- Cost-effective: By eliminating the need for extra components, press-fit holes can reduce overall assembly costs.
- Strong and reliable: The compressive force created by the interference fit provides a strong and reliable connection between components.
- Efficient assembly: Press-fit holes allow for quick and efficient assembly, which can help streamline production processes.
- Compact design: Press-fit connections enable more compact designs, as they do not require extra space for fasteners or adhesives.
Disadvantages of Press-Fit Holes
Despite their many advantages, press-fit holes also have some limitations:
- Limited disassembly: Once components are press-fit together, they can be difficult to disassemble without damaging the parts.
- Material limitations: Press-fit holes work best with materials that have some degree of elasticity, such as metals and certain plastics. Brittle materials may crack or break under the pressure of the interference fit.
- Precision required: Creating press-fit holes requires precise manufacturing tolerances to ensure a proper fit between components.
- Potential for stress concentrations: The high compressive forces involved in press-fit assembly can create stress concentrations around the hole, which may lead to fatigue or failure over time.
Designing Press-Fit Holes
When designing press-fit holes, several factors must be considered to ensure a successful and reliable connection.
Hole and Shaft Tolerances
The most critical aspect of press-fit hole design is selecting the appropriate hole and shaft tolerances. The hole should be slightly smaller than the shaft to create the necessary interference fit. The amount of interference depends on various factors, including:
- Material properties: The elasticity and strength of the materials being joined will influence the required interference.
- Component size: Larger components generally require greater interference to maintain a secure fit.
- Operating conditions: Environmental factors such as temperature, vibration, and loading should be considered when determining the appropriate interference.
The table below provides general guidelines for selecting press-fit hole tolerances based on shaft diameter:
Shaft Diameter (mm) | Hole Tolerance (mm) |
---|---|
1-6 | -0.005 to -0.020 |
6-12 | -0.010 to -0.030 |
12-25 | -0.015 to -0.040 |
25-50 | -0.020 to -0.050 |
Material Selection
Choosing the right materials for press-fit holes is essential for achieving a strong and reliable connection. The materials should have sufficient strength and elasticity to withstand the compressive forces involved in the press-fit assembly without breaking or deforming excessively.
Common materials used for press-fit holes include:
- Metals: Steel, stainless steel, aluminum, brass, and copper are often used in press-fit applications due to their strength and elasticity.
- Plastics: Certain engineering plastics, such as nylon, acetal, and polycarbonate, can be used for press-fit holes in lower-stress applications.
Surface Finish and Lubrication
The surface finish and lubrication of the components can also influence the success of a press-fit assembly. A smooth surface finish can help reduce friction and prevent galling or seizing during the assembly process. In some cases, a light lubricant may be applied to the shaft or hole to further reduce friction and ease assembly.
Hole Preparation
Proper hole preparation is crucial for creating a successful press-fit connection. The hole should be machined to the correct size and tolerance, with a smooth surface finish and no burrs or debris. Chamfering or radiusing the edge of the hole can help guide the shaft during assembly and reduce stress concentrations.
Assembly Methods for Press-Fit Holes
There are several methods for assembling components with press-fit holes, depending on the size, materials, and geometry of the parts involved.
Manual Press
For smaller components or low-volume production, manual presses can be used to assemble press-fit holes. The shaft is typically placed in a fixture or guide, and the operator uses a lever or handle to apply pressure and force the shaft into the hole.
Hydraulic or Pneumatic Press
For larger components or higher-volume production, hydraulic or pneumatic presses can be used to automate the assembly process. These presses use fluid power to apply a controlled force to the shaft, ensuring a consistent and reliable press-fit connection.
Thermal Assembly
In some cases, thermal expansion and contraction can be used to create a press-fit connection. The shaft is cooled to reduce its diameter, while the hole is heated to expand its size. When the cooled shaft is inserted into the heated hole, the components return to their original temperatures, creating a tight interference fit.
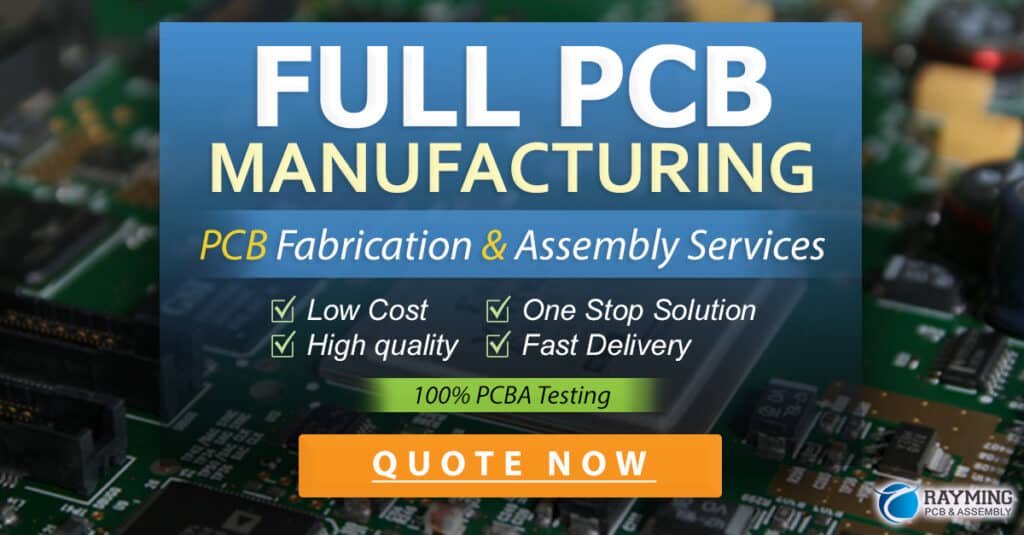
Quality Control and Testing
To ensure the reliability and performance of press-fit holes, quality control measures and testing should be implemented throughout the design and assembly process.
Dimensional Inspection
Components should be inspected before assembly to ensure they meet the specified tolerances for hole and shaft diameters. This can be done using various measuring tools, such as micrometers, calipers, or coordinate measuring machines (CMMs).
Assembly Force Monitoring
During the assembly process, the force required to press the shaft into the hole should be monitored and recorded. Excessive force may indicate an improper fit or potential damage to the components, while insufficient force may result in a loose or unstable connection.
Pull-Out Testing
After assembly, pull-out testing can be performed to evaluate the strength and reliability of the press-fit connection. This involves applying a controlled tensile force to the assembled components and measuring the force required to separate them.
Applications of Press-Fit Holes
Press-fit holes are used in a wide range of industries and applications, including:
-
Automotive: Press-fit holes are commonly used in automotive components, such as bearings, gears, and shafts, to create strong and reliable connections without the need for additional fasteners.
-
Electronics: In electronic devices, press-fit holes are used to assemble connectors, pins, and other components onto printed circuit boards (PCBs).
-
Medical devices: Press-fit connections are used in medical devices to assemble components such as implants, instruments, and equipment, where reliability and sterility are critical.
-
Aerospace: Press-fit holes are used in aerospace applications to join components in engines, airframes, and other systems where high strength and reliability are essential.
-
Industrial machinery: Press-fit connections are used in various industrial machinery, such as pumps, valves, and compressors, to assemble components and create strong, reliable joints.
Frequently Asked Questions (FAQ)
-
Q: What is the difference between a press-fit hole and a clearance hole?
A: A press-fit hole is designed to be slightly smaller than the mating component, creating an interference fit when the components are assembled. A clearance hole, on the other hand, is slightly larger than the mating component, allowing for easy insertion and removal without creating a tight fit. -
Q: Can press-fit holes be used with dissimilar materials?
A: Yes, press-fit holes can be used with dissimilar materials, provided that the materials have compatible thermal expansion coefficients and sufficient strength and elasticity to withstand the compressive forces involved in the assembly process. -
Q: How do I determine the appropriate interference for a press-fit hole?
A: The appropriate interference for a press-fit hole depends on factors such as material properties, component size, and operating conditions. Engineers typically use reference tables, standards, or finite element analysis (FEA) to determine the optimal interference for a given application. -
Q: Can press-fit holes be disassembled and reassembled?
A: Press-fit holes are generally designed for permanent assembly and can be difficult to disassemble without damaging the components. In some cases, special tools or techniques, such as heating or cooling, may be used to facilitate disassembly, but the interference fit may be compromised upon reassembly. -
Q: What are some common failure modes for press-fit holes?
A: Common failure modes for press-fit holes include excessive deformation or damage during assembly, fatigue failure due to stress concentrations, and loosening or separation under operating conditions. Proper design, material selection, and quality control can help mitigate these failure modes and ensure reliable performance.
Conclusion
Press-fit holes are a simple, cost-effective, and reliable method for assembling components in various industries. By creating a strong interference fit between mating components, press-fit holes eliminate the need for additional fasteners or adhesives, streamlining the assembly process and enabling more compact designs.
Successful implementation of press-fit holes requires careful consideration of design factors, such as hole and shaft tolerances, material selection, surface finish, and lubrication. Proper assembly methods, quality control measures, and testing are also essential for ensuring the reliability and performance of press-fit connections.
As industries continue to demand stronger, more efficient, and more cost-effective assembly solutions, press-fit holes will likely remain a valuable tool in the designer’s arsenal, enabling the creation of high-quality, reliable products across a wide range of applications.
No responses yet