Introduction to PCB Material Prices
Printed Circuit Boards (PCBs) are essential components in virtually all electronic devices we use today. The cost of manufacturing PCBs is heavily influenced by the materials used in their production. In this article, we will dive deep into the world of PCB material prices, exploring the various factors that affect the overall cost and providing insights into the current market trends.
Factors Affecting PCB Material Prices
Several key factors play a role in determining the price of PCB Materials:
1. Raw Material Costs
The cost of raw materials used in PCB production, such as copper, fiberglass, and resin, can fluctuate based on global supply and demand. These price variations directly impact the overall cost of PCB materials.
2. Manufacturing Process Complexity
The complexity of the PCB manufacturing process can significantly affect material prices. Higher-complexity boards, such as those with multiple layers or advanced features like embedded components, require more specialized materials and processes, leading to increased costs.
3. Volume and Order Quantity
PCB material prices are often subject to economies of scale. Larger order quantities typically result in lower per-unit costs, as manufacturers can optimize their production processes and negotiate better prices with suppliers.
4. Market Competition
The level of competition among PCB Manufacturers and material suppliers can influence pricing. In a highly competitive market, companies may offer lower prices to attract customers and maintain market share.
Common PCB Materials and Their Prices
Let’s take a look at some of the most commonly used PCB materials and their typical price ranges:
Material | Price Range (per sq. ft.) |
---|---|
FR-4 | $0.10 – $0.30 |
Polyimide | $1.50 – $3.00 |
Aluminum | $0.50 – $1.50 |
Copper | $0.20 – $0.60 |
Solder Mask | $0.05 – $0.15 |
Silkscreen | $0.03 – $0.10 |
Note: Prices are estimates and may vary based on specific supplier, location, and market conditions.
FR-4
FR-4 is the most widely used PCB material, known for its excellent electrical insulation properties and mechanical strength. It is a composite material made of woven fiberglass cloth with an epoxy resin binder. FR-4 is affordable and suitable for a wide range of applications, making it a popular choice for many PCB Designs.
Polyimide
Polyimide is a high-performance polymer material that offers superior thermal stability, chemical resistance, and mechanical properties compared to FR-4. It is often used in applications that require reliability under extreme conditions, such as aerospace, military, and high-temperature environments. However, polyimide’s advanced properties come at a higher cost compared to FR-4.
Aluminum
Aluminum PCBs are known for their excellent thermal conductivity, making them ideal for applications that generate significant heat, such as high-power LED lighting and motor control systems. Aluminum substrates are typically more expensive than FR-4 but offer unique advantages in terms of heat dissipation and thermal management.
Copper
Copper is the primary conductive material used in PCBs, responsible for creating the electrical interconnections between components. The price of copper can vary based on its thickness (weight per square foot) and global commodity prices. Thicker copper layers are more expensive but offer better current-carrying capacity and improved thermal performance.
Solder Mask and Silkscreen
Solder mask and silkscreen are additional materials applied to the surface of PCBs. Solder mask is a protective coating that prevents accidental short circuits and helps to define the solderable areas on the board. Silkscreen is used to print text, logos, and component identifiers on the PCB surface. The cost of these materials is relatively low compared to the base PCB substrate.
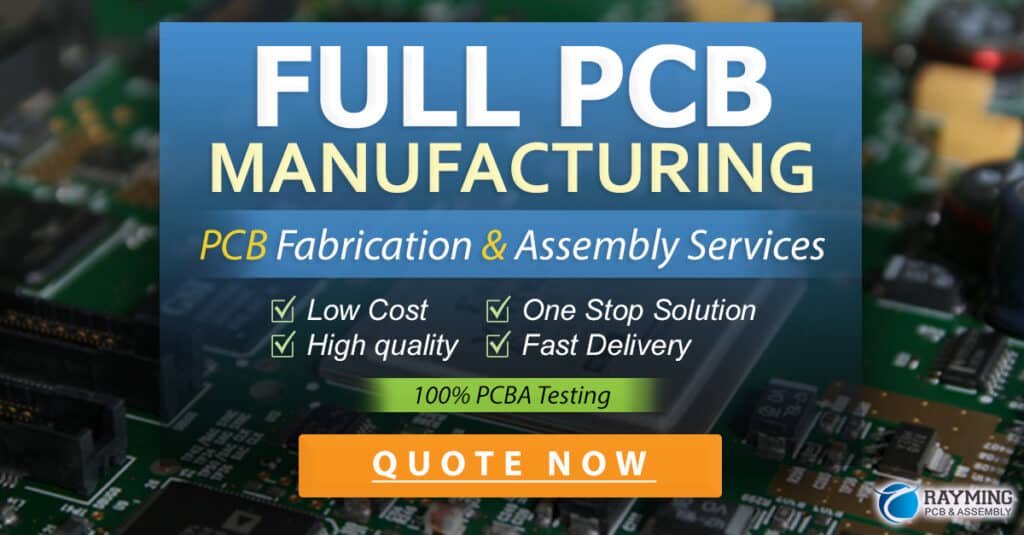
PCB Material Price Trends
The PCB material market is dynamic, with prices fluctuating based on various global factors. Some notable trends in recent years include:
-
Rising Copper Prices: The global demand for copper has been increasing, driven by the growth of industries such as electronics, renewable energy, and electric vehicles. This has led to a general upward trend in copper prices, which can impact the overall cost of PCB materials.
-
Shift Towards Advanced Materials: As electronic devices become more sophisticated and operate in demanding environments, there is a growing demand for advanced PCB materials like polyimide, high-frequency laminates, and thermal management solutions. These materials command higher prices due to their superior performance characteristics.
-
Impact of Global Supply Chain Disruptions: Disruptions in the global supply chain, such as those caused by the COVID-19 pandemic or geopolitical events, can affect the availability and pricing of PCB materials. Shortages or delays in the supply of raw materials can lead to temporary price increases and longer lead times.
Strategies for Optimizing PCB Material Costs
To manage PCB material costs effectively, consider the following strategies:
-
Design Optimization: Collaborate with experienced PCB design engineers to optimize your board layout and minimize the use of expensive materials. Techniques like reducing the number of layers, using standard material thicknesses, and optimizing the copper weight can help control costs without compromising functionality.
-
Volume Consolidation: Consolidate your PCB orders to take advantage of volume discounts offered by manufacturers. Larger order quantities often result in lower per-unit material costs, as well as reduced setup and tooling charges.
-
Strategic Sourcing: Develop relationships with multiple PCB manufacturers and material suppliers to ensure a stable and competitive supply chain. Regularly review pricing and negotiate based on your specific requirements and market conditions.
-
Material Substitution: Evaluate alternative materials that can meet your performance requirements at a lower cost. For example, consider using FR-4 instead of polyimide for applications that do not require extreme temperature resistance.
-
Continuous Cost Monitoring: Stay informed about market trends and price fluctuations for key PCB materials. Regularly review your material costs and adjust your sourcing strategies accordingly to optimize your expenditure.
Frequently Asked Questions (FAQ)
-
What is the most common PCB material, and why?
FR-4 is the most common PCB material due to its excellent balance of electrical, mechanical, and thermal properties, as well as its affordability compared to other materials. -
How do I know which PCB material is best suited for my application?
The choice of PCB material depends on various factors such as the operating environment, required electrical performance, thermal management needs, and budget constraints. Consult with experienced PCB design engineers or manufacturers to determine the most suitable material for your specific application. -
Can I reduce PCB material costs by using thinner copper layers?
Yes, using thinner copper layers can help reduce material costs, as copper is one of the more expensive components in PCBs. However, it’s essential to ensure that the selected copper thickness meets your electrical and thermal requirements to avoid compromising the board’s performance and reliability. -
How often should I review and update my PCB material pricing?
It’s recommended to review your PCB material pricing regularly, typically every 3-6 months, or whenever there are significant changes in market conditions or your production requirements. Staying informed about pricing trends and actively managing your material costs can help optimize your overall PCB expenditure. -
Are there any eco-friendly PCB materials available, and how do their prices compare to traditional materials?
Yes, there are eco-friendly PCB materials available, such as halogen-free laminates and substrates made from recycled materials. The prices of these materials can vary depending on the specific type and manufacturer, but they are generally comparable to or slightly higher than traditional materials. However, the use of eco-friendly materials can contribute to your company’s sustainability goals and may be preferred by environmentally conscious customers.
Conclusion
Understanding PCB material prices is crucial for effectively managing the cost of electronic product development and manufacturing. By considering factors such as raw material costs, manufacturing complexity, order quantity, and market competition, you can make informed decisions when selecting materials and optimizing your PCB designs.
Staying up-to-date with market trends, exploring alternative materials, and implementing cost-saving strategies can help you control PCB material expenses without compromising product quality or performance. Collaborating with experienced PCB design engineers and manufacturers can provide valuable insights and support in navigating the complex landscape of PCB material pricing.
As the electronics industry continues to evolve, it’s essential to remain proactive in managing PCB material costs to maintain a competitive edge in the market. By carefully considering the information and strategies presented in this article, you can make well-informed decisions that drive cost efficiency and profitability in your PCB-based projects.
No responses yet