Importance of Track to Track Distance
The Track to Track distance is essential for several reasons:
-
Signal Integrity: Proper spacing between traces helps minimize crosstalk, which is the unintended coupling of signals between adjacent traces. Crosstalk can lead to signal distortion, noise, and errors in data transmission.
-
Electromagnetic Compatibility (EMC): Adequate Track to Track distance helps reduce electromagnetic interference (EMI) between traces, which can cause issues with EMC compliance and potentially interfere with the operation of nearby electronic devices.
-
Manufacturing Feasibility: The Track to Track distance must be compatible with the capabilities of the PCB or IC package manufacturing process. Smaller Track to Track distances require more advanced and expensive manufacturing techniques.
Factors Affecting Track to Track Distance
Several factors influence the determination of the appropriate Track to Track distance for a given design:
-
Signal Frequency: Higher frequency signals require greater spacing between traces to minimize crosstalk and maintain signal integrity.
-
Dielectric Material: The dielectric constant (Dk) and dissipation factor (Df) of the PCB or IC package substrate material affect the required Track to Track distance. Materials with higher Dk and Df values generally require larger Track to Track distances.
-
Trace Geometry: The width, thickness, and shape of the traces impact the Track to Track distance. Wider traces and thicker copper layers generally require larger Track to Track distances.
-
Voltage Level: Higher voltage signals may require larger Track to Track distances to prevent arcing and maintain adequate insulation between traces.
-
Application Requirements: The specific requirements of the application, such as high-speed data transmission, RF performance, or high-density packaging, will influence the necessary Track to Track distance.
Industry Standards and Guidelines
Various industry standards and guidelines provide recommendations for Track to Track distances based on the factors mentioned above. Some of the most common standards include:
- IPC-2221: Generic Standard on Printed Board Design
- IPC-2223: Sectional Design Standard for Flexible Printed Boards
- IPC-2226: Design Standard for High Density Interconnect (HDI) Printed Boards
- JESD15: JEDEC Standard for Package Outline and Footprint
- HDMI Specification: For HDMI-specific PCB design requirements
These standards offer guidance on minimum Track to Track distances for various signal types, frequencies, and substrate materials. However, it is essential to consider the specific requirements of each design and consult with experienced PCB or IC package designers to determine the optimal Track to Track distance for a given application.
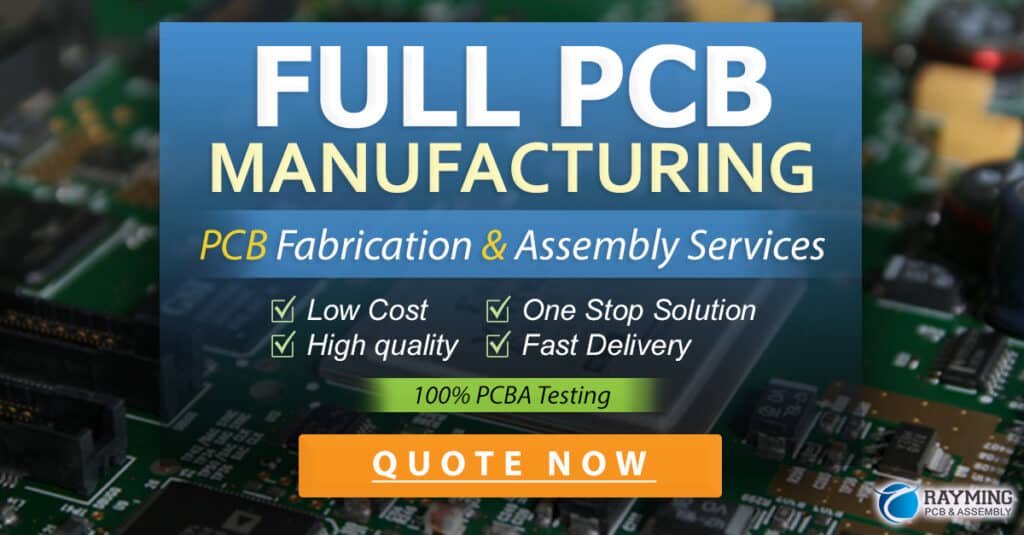
Calculating Track to Track Distance
The Track to Track distance can be calculated using various formulas and tools, depending on the specific factors involved. Some common methods include:
- IPC-2221 Formula: The IPC-2221 standard provides a formula for calculating the minimum Track to Track distance based on the dielectric material, trace geometry, and signal frequency.
Example: PCB Design Rules for High-Speed Interfaces
Parameter | Min (in) | Nom (in) | Max (in) |
---|---|---|---|
Track Width | 0.003 | 0.005 | 0.007 |
Track Spacing | 0.003 | 0.005 | 0.007 |
-
Simulation Tools: Advanced PCB and IC package design software often include tools for simulating signal integrity and EMC performance based on the Track to Track distance and other design parameters. These tools can help optimize the Track to Track distance for a specific design.
-
Rule of Thumb: In some cases, experienced designers may use rule of thumb estimates for Track to Track distance based on the signal frequency and substrate material. For example, a common rule of thumb is to use a Track to Track distance of at least 3 times the trace width for high-speed signals on FR-4 PCBs.
It is important to note that these calculation methods provide a starting point for determining the appropriate Track to Track distance, but the final design should be verified through simulation, prototyping, and testing to ensure optimal performance and manufacturability.
PCB Manufacturing Considerations
The Track to Track distance directly impacts the manufacturability of PCBs and IC packages. Smaller Track to Track distances require more advanced manufacturing processes and tighter tolerances, which can increase production costs and lead times.
Some manufacturing considerations related to Track to Track distance include:
-
Etching Process: The minimum achievable Track to Track distance depends on the capabilities of the PCB etching process. Advanced processes, such as high-density interconnect (HDI) or modified semi-additive process (mSAP), can achieve smaller Track to Track distances compared to standard subtractive etching processes.
-
Copper Thickness: Thicker copper layers require larger Track to Track distances to ensure proper etching and prevent short circuits between adjacent traces.
-
Solder Mask Application: The solder mask layer applied over the PCB Traces can affect the minimum achievable Track to Track distance. Tight registration between the solder mask and trace layers is necessary to maintain the desired Track to Track spacing.
-
Via Placement: The placement of vias (vertical interconnect access) between PCB Layers can impact the Track to Track distance. Vias should be placed to maintain adequate spacing from adjacent traces while minimizing signal integrity issues.
-
Manufacturing Yield: Smaller Track to Track distances can reduce manufacturing yield, as they are more susceptible to defects and process variations. This can lead to increased production costs and longer lead times.
Close communication between the PCB designer and the manufacturing team is essential to ensure that the desired Track to Track distances are achievable and cost-effective for the specific application and production volume.
Signal Integrity Considerations
Maintaining proper signal integrity is a critical factor in determining the appropriate Track to Track distance. The two main signal integrity issues related to Track to Track spacing are crosstalk and impedance control.
Crosstalk
Crosstalk occurs when signals from one trace couple onto adjacent traces, causing signal distortion and potential errors in data transmission. The severity of crosstalk depends on several factors, including:
-
Signal Frequency: Higher frequency signals are more susceptible to crosstalk, as the coupling between traces increases with frequency.
-
Trace Geometry: Longer parallel trace segments and smaller Track to Track distances increase the potential for crosstalk.
-
Dielectric Material: PCB or IC package substrates with higher dielectric constants (Dk) can increase the coupling between traces and exacerbate crosstalk.
To minimize crosstalk, designers can:
- Increase the Track to Track distance between sensitive signal traces
- Use differential signaling techniques, which can cancel out common-mode noise
- Implement guard traces or ground planes between sensitive signal traces
- Route sensitive signals on different layers of the PCB or IC package substrate
Impedance Control
Maintaining consistent trace impedance is essential for high-speed signal integrity. Impedance mismatches can cause signal reflections, leading to signal distortion and potential errors in data transmission.
The characteristic impedance of a trace depends on several factors, including:
-
Trace Geometry: The width, thickness, and spacing of the traces affect their characteristic impedance.
-
Dielectric Material: The dielectric constant (Dk) and dissipation factor (Df) of the PCB or IC package substrate material influence the characteristic impedance of the traces.
-
Reference Plane: The presence and proximity of reference planes (ground or power) impact the characteristic impedance of the traces.
To maintain consistent impedance, designers can:
- Use controlled impedance design techniques, such as stripline or microstrip traces
- Adjust the trace geometry (width, thickness, and spacing) to achieve the desired characteristic impedance
- Use dielectric materials with consistent and well-controlled Dk and Df values
- Ensure proper reference plane placement and spacing relative to the signal traces
By carefully considering crosstalk and impedance control, designers can select the appropriate Track to Track distance to maintain signal integrity in their PCB or IC package designs.
EMC Considerations
Electromagnetic compatibility (EMC) is another important factor in determining the appropriate Track to Track distance. EMC refers to the ability of an electronic device to operate properly in its electromagnetic environment without causing or being susceptible to electromagnetic interference (EMI).
Proper Track to Track spacing can help minimize EMI issues in several ways:
-
Reducing Loop Area: Larger Track to Track distances can help reduce the loop area between adjacent traces, which can decrease the amount of EMI radiated by the traces.
-
Minimizing Coupling: Adequate spacing between traces can reduce the capacitive and inductive coupling between them, which can decrease the potential for EMI.
-
Improving Shielding Effectiveness: In some cases, designers may use shielding techniques, such as guard traces or ground planes, to reduce EMI. Proper Track to Track spacing can help maintain the effectiveness of these shielding techniques.
To ensure EMC compliance, designers should consider the following:
-
Regulatory Requirements: Different countries and regions have specific EMC regulations that electronic devices must meet. Designers should be aware of the applicable standards and design their PCBs and IC packages accordingly.
-
Application Environment: The intended operating environment of the electronic device can impact the EMC requirements. For example, devices used in medical or automotive applications may have more stringent EMC requirements compared to consumer electronics.
-
Frequency Range: The frequency range of the signals in the PCB or IC package can affect the EMC performance. Higher frequency signals may require greater Track to Track distances to minimize EMI.
-
Simulation and Testing: EMC simulation tools can help predict the EMI performance of a PCB or IC package design based on the Track to Track distances and other factors. Final designs should be tested in a certified EMC laboratory to ensure compliance with the relevant standards.
By considering EMC requirements and carefully selecting the appropriate Track to Track distances, designers can help ensure that their electronic devices operate properly and do not cause or suffer from electromagnetic interference.
Frequently Asked Questions (FAQ)
-
What is the minimum Track to Track distance for a typical PCB?
The minimum Track to Track distance for a typical PCB depends on several factors, such as the signal frequency, dielectric material, and manufacturing process. As a general rule of thumb, for standard FR-4 PCBs with signal frequencies below 1 GHz, a minimum Track to Track distance of 0.006 inches (0.15 mm) is often used. However, for high-speed designs or advanced manufacturing processes, smaller Track to Track distances may be achievable. -
Can I use the same Track to Track distance for all the traces in my PCB design?
In most cases, it is not recommended to use the same Track to Track distance for all traces in a PCB design. Different signal types, frequencies, and impedance requirements may necessitate varying Track to Track distances. For example, high-speed signals or sensitive analog traces may require larger Track to Track distances compared to low-speed digital traces. It is essential to consider the specific requirements of each signal and consult industry guidelines or work with experienced PCB designers to determine the appropriate Track to Track distances for your design. -
How does the PCB substrate material affect the Track to Track distance?
The PCB substrate material can have a significant impact on the required Track to Track distance. The dielectric constant (Dk) and dissipation factor (Df) of the substrate material influence the signal propagation speed and losses, which can affect the potential for crosstalk and signal integrity issues. In general, materials with higher Dk and Df values may require larger Track to Track distances to maintain signal integrity and minimize crosstalk. It is essential to consider the properties of the substrate material when determining the appropriate Track to Track distances for your design. -
What are some common techniques for minimizing crosstalk between adjacent traces?
There are several common techniques for minimizing crosstalk between adjacent traces in a PCB design:
a. Increasing the Track to Track distance: Larger spacing between traces reduces the coupling and potential for crosstalk.
b. Using differential signaling: Differential pairs can help cancel out common-mode noise and reduce the impact of crosstalk.
c. Implementing guard traces or ground planes: Placing grounded traces or planes between sensitive signal traces can help shield them from crosstalk.
d. Routing sensitive signals on different layers: Separating sensitive signals on different layers of the PCB can reduce the coupling between them.
e. Minimizing parallel trace segments: Reducing the length of parallel trace segments can decrease the potential for crosstalk.
- How can I ensure that my PCB design meets EMC requirements?
To ensure that your PCB design meets EMC requirements, consider the following:
a. Understand the applicable EMC regulations and standards for your target market and application.
b. Use appropriate Track to Track distances to minimize EMI and maintain signal integrity.
c. Implement shielding techniques, such as guard traces or ground planes, where necessary.
d. Use EMC simulation tools to predict the EMI performance of your design and make adjustments as needed.
e. Have your final design tested in a certified EMC laboratory to ensure compliance with the relevant standards.
f. Work with experienced PCB designers and EMC specialists to review your design and provide guidance on meeting EMC requirements.
By carefully considering these factors and following industry guidelines and best practices, you can help ensure that your PCB design meets the necessary EMC requirements for your application and target market.
No responses yet