Introduction to PCB Parameters
Printed Circuit Boards (PCBs) are the backbone of modern electronics. They provide a platform for mounting and interconnecting electronic components, enabling the creation of complex circuits and systems. To ensure optimal performance and reliability, it is crucial to understand and carefully consider the various parameters that define a PCB. In this article, we will explore the basic PCB parameters that every engineer and designer should be familiar with.
Key PCB Parameters
1. Board Size and Shape
The size and shape of a PCB are fundamental parameters that determine its physical dimensions and form factor. The board size is typically specified in terms of length and width, measured in millimeters (mm) or inches (in). The shape of the board can vary depending on the specific application and enclosure requirements. Common PCB shapes include rectangular, square, circular, and irregular shapes.
When deciding on the board size and shape, consider the following factors:
– Available space within the enclosure or device
– Component placement and routing requirements
– Manufacturing constraints and cost implications
– Mechanical and thermal considerations
2. Layer Stack-up
The layer stack-up refers to the arrangement and composition of the conductive layers within a PCB. It defines the number of layers, their order, and the materials used for each layer. The most common layer stack-ups include:
- Single-Layer PCB: Consists of a single conductive layer, typically used for simple circuits.
- Double-layer PCB: Has two conductive layers, one on each side of the substrate, allowing for more complex routing and component placement.
- Multi-layer PCB: Comprises three or more conductive layers, enabling high-density designs and improved signal integrity.
The choice of layer stack-up depends on factors such as signal integrity requirements, power distribution needs, and manufacturing cost. The following table provides an overview of common layer stack-ups and their characteristics:
Layer Stack-up | Layers | Complexity | Cost |
---|---|---|---|
Single-layer | 1 | Low | Low |
Double-layer | 2 | Medium | Medium |
4-layer | 4 | High | High |
6-layer | 6 | Very High | Very High |
8-layer+ | 8+ | Extremely High | Extremely High |
3. Material Selection
The choice of materials used in a PCB has a significant impact on its performance, reliability, and cost. The primary materials to consider are:
-
Substrate material: The substrate, also known as the base material or laminate, provides the foundation for the conductive layers and components. Common substrate materials include FR-4, Rogers, and polyimide. Each material has unique properties such as dielectric constant, loss tangent, and thermal stability.
-
Copper weight: The copper weight refers to the thickness of the copper foil used for the conductive layers. It is typically measured in ounces per square foot (oz/ft²) or microns (μm). Higher copper weights offer better current carrying capacity and thermal dissipation but increase the overall board thickness and cost.
-
Solder mask: The solder mask is a protective coating applied over the copper traces to prevent oxidation and provide electrical insulation. It also helps prevent Solder Bridges during the assembly process. Common Solder Mask Colors include green, red, blue, and black.
-
Silkscreen: The silkscreen is a printed layer on top of the solder mask that provides component labels, logos, and other visual indicators. It is typically white or yellow in color and aids in the assembly and identification of components.
4. Trace Width and Spacing
Trace width and spacing are critical parameters that determine the current carrying capacity, signal integrity, and manufacturability of a PCB. Trace width refers to the width of the copper traces on the board, while spacing refers to the distance between adjacent traces.
The choice of trace width and spacing depends on several factors, including:
– Current requirements: Wider traces can carry more current without excessive heating or voltage drop.
– Signal integrity: Narrower traces and tighter spacing can improve signal integrity by reducing crosstalk and impedance mismatch.
– Manufacturing capabilities: The minimum trace width and spacing are limited by the manufacturing process and the selected PCB fabricator.
The IPC (Association Connecting Electronics Industries) provides guidelines for trace width and spacing based on the copper weight and the desired electrical characteristics. The following table shows the recommended trace widths for various copper weights and current requirements:
Copper Weight (oz/ft²) | Current (A) | Trace Width (mm) |
---|---|---|
0.5 | 0.5 | 0.2 |
0.5 | 1.0 | 0.3 |
1.0 | 1.0 | 0.2 |
1.0 | 2.0 | 0.4 |
2.0 | 2.0 | 0.3 |
2.0 | 4.0 | 0.6 |
5. Hole Size and Pad Diameter
Hole size and pad diameter are important parameters for through-hole components and vias. The hole size refers to the diameter of the drilled hole, while the pad diameter is the size of the copper pad surrounding the hole.
When selecting hole sizes and pad diameters, consider the following factors:
– Component lead diameter: Ensure that the hole size is large enough to accommodate the component leads without causing mechanical stress or difficulty during assembly.
– Plating requirements: The hole size and pad diameter should allow for proper plating of the hole walls to ensure reliable electrical connections.
– Manufacturing tolerances: Consider the manufacturing tolerances of the PCB fabricator to avoid issues with hole and pad sizing.
The IPC provides recommended hole sizes and pad diameters for various component lead diameters. The following table shows some common hole sizes and pad diameters:
Component Lead Diameter (mm) | Hole Size (mm) | Pad Diameter (mm) |
---|---|---|
0.5 | 0.7 | 1.5 |
0.8 | 1.0 | 2.0 |
1.0 | 1.2 | 2.5 |
1.2 | 1.4 | 3.0 |
6. Clearance and Creepage
Clearance and creepage are two essential parameters related to the spacing between conductive elements on a PCB. Clearance refers to the shortest distance through air between two conductive elements, while creepage is the shortest distance along the surface of the insulating material between two conductive elements.
Maintaining sufficient clearance and creepage distances is crucial for ensuring electrical safety, preventing arcing, and meeting regulatory requirements. The required clearance and creepage distances depend on factors such as:
– Operating voltage: Higher voltages require greater clearance and creepage distances to prevent electrical breakdown.
– Environmental conditions: Humid or contaminated environments may require increased clearance and creepage distances.
– Insulation material properties: The dielectric strength and surface resistivity of the insulating material influence the required distances.
The IPC and other safety standards provide guidelines for minimum clearance and creepage distances based on the operating voltage and environmental conditions. Designers should refer to these standards and consult with the PCB fabricator to ensure compliance.
7. Via Types and Sizes
Vias are conductive holes that allow signals to pass through different layers of a PCB. They are essential for routing signals and creating interconnections between layers. There are several types of vias, each with its own characteristics and applications:
- Through-hole vias: These vias go through all layers of the PCB and are typically used for mounting through-hole components or providing mechanical strength.
- Blind vias: Blind vias start from an outer layer and terminate at an inner layer, allowing for more compact routing and higher component density.
- Buried vias: Buried vias connect inner layers without reaching the outer layers, enabling even greater routing flexibility and density.
- Microvias: Microvias are small-diameter vias, usually less than 0.15 mm, that are used for high-density interconnects and fine-pitch components.
The choice of via type and size depends on the routing requirements, layer stack-up, and manufacturing capabilities. Smaller via sizes allow for denser routing but may increase manufacturing costs and complexity.
8. Solder Mask Expansion and Webbing
Solder mask expansion (SME) and webbing are parameters that define the spacing between the solder mask opening and the copper pad. SME refers to the additional space around the copper pad where the solder mask is pulled back, while webbing is the width of the solder mask between adjacent pads.
Proper control of SME and webbing is important for several reasons:
– Solder joint reliability: Adequate SME allows for proper solder wetting and helps prevent solder bridges between adjacent pads.
– Electrical insulation: Sufficient webbing provides electrical insulation between adjacent pads and prevents short circuits.
– Manufacturing process: The SME and webbing values should be compatible with the capabilities of the PCB fabricator and the assembly process.
The IPC provides recommended values for SME and webbing based on the pad size and pitch. The following table shows some typical SME and webbing values:
Pad Size (mm) | Pitch (mm) | SME (mm) | Webbing (mm) |
---|---|---|---|
0.5 | 0.8 | 0.05 | 0.15 |
0.6 | 1.0 | 0.075 | 0.2 |
0.8 | 1.27 | 0.1 | 0.25 |
1.0 | 1.5 | 0.125 | 0.3 |
FAQ
- What is the difference between a single-layer and a multi-layer PCB?
-
A single-layer PCB has only one conductive layer, while a multi-layer PCB has three or more conductive layers. Multi-layer PCBs offer higher routing density, better signal integrity, and improved power distribution compared to single-layer PCBs.
-
How does the copper weight affect the performance of a PCB?
-
The copper weight determines the thickness of the copper traces on the PCB. Higher copper weights provide better current carrying capacity and improved thermal dissipation. However, they also increase the overall board thickness and manufacturing cost.
-
What factors should be considered when selecting the trace width and spacing?
-
When selecting trace width and spacing, consider the current requirements, signal integrity, and manufacturing capabilities. Wider traces can carry more current, while narrower traces and tighter spacing can improve signal integrity. The minimum trace width and spacing are limited by the manufacturing process and the PCB fabricator.
-
Why are clearance and creepage distances important in PCB Design?
-
Clearance and creepage distances are important for ensuring electrical safety, preventing arcing, and meeting regulatory requirements. Maintaining sufficient clearance and creepage distances helps prevent electrical breakdown and short circuits, especially in high-voltage applications or harsh environmental conditions.
-
What are the advantages of using microvias in PCB design?
- Microvias are small-diameter vias that offer several advantages in PCB design. They enable higher routing density, improved signal integrity, and better compatibility with fine-pitch components. Microvias are particularly useful in high-density interconnect (HDI) designs and advanced packaging technologies.
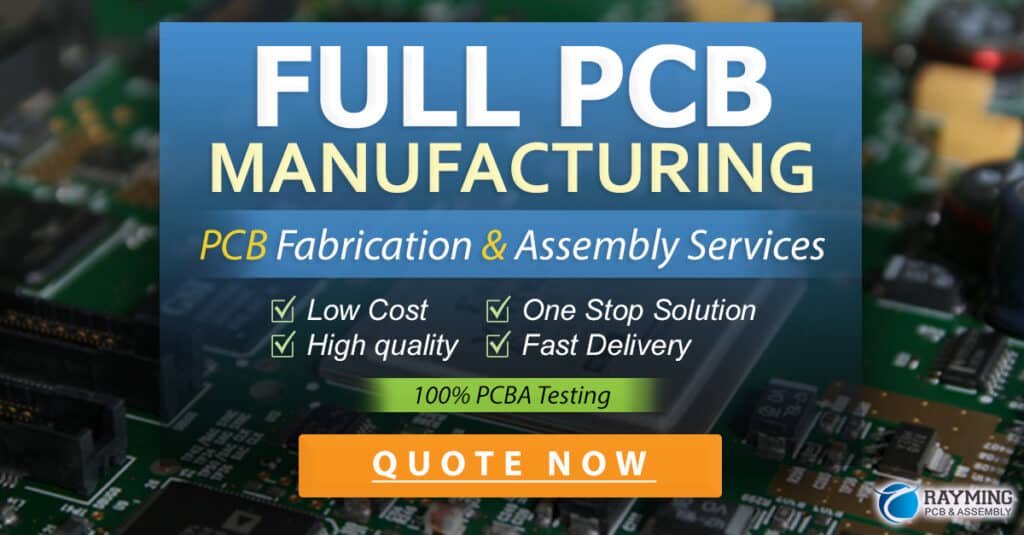
Conclusion
Understanding and carefully considering the basic PCB parameters is essential for designing reliable, high-performance electronic circuits. From board size and shape to trace width and spacing, each parameter plays a crucial role in the overall functionality and manufacturability of the PCB.
By following industry guidelines, such as those provided by the IPC, and collaborating closely with PCB fabricators, designers can ensure that their PCBs meet the desired specifications and perform optimally in their intended applications.
As technology advances and electronic devices become more complex, staying up-to-date with the latest PCB design techniques and best practices is crucial. By mastering the fundamental PCB parameters and continuously expanding their knowledge, engineers and designers can create innovative and robust PCBs that power the electronic devices of today and tomorrow.
No responses yet