Understanding SMT Tombstoning
SMT (Surface Mount Technology) tombstoning is a common defect that occurs during the reflow soldering process in PCB (Printed Circuit Board) assembly. It is a phenomenon where a small SMD (Surface Mount Device) component, such as a chip resistor or capacitor, stands up on one end, resembling a tombstone. This defect can lead to poor electrical connections, reduced reliability, and potential circuit failures.
Causes of SMT Tombstoning
Several factors can contribute to the occurrence of SMT tombstoning:
-
Uneven heating: If one side of the component heats up faster than the other during the reflow process, it can cause the component to lift up on one end.
-
Unbalanced solder paste: An unequal amount of solder paste applied to the pads can result in uneven surface tension forces, pulling the component up on one side.
-
Component geometry: Components with a high aspect ratio (length to width) or those with a small contact area are more susceptible to tombstoning.
-
Pad design: Incorrectly designed pads, such as those with unequal sizes or shapes, can lead to tombstoning.
-
Reflow profile: An improper reflow temperature profile, with excessive peak temperatures or rapid cooling rates, can increase the likelihood of tombstoning.
Preventing SMT Tombstoning
To minimize the occurrence of SMT tombstoning, several preventive measures can be implemented:
1. Component Selection
Choosing the right components plays a crucial role in preventing tombstoning. Consider the following factors when selecting components:
- Size: Opt for larger components whenever possible, as they are less prone to tombstoning due to their higher mass and larger contact area.
- Termination style: Components with end terminations, such as chip resistors and capacitors, are more susceptible to tombstoning compared to those with bottom terminations, like QFNs (Quad Flat No-leads) or BGAs (Ball Grid Arrays).
- Packaging: Choose components with packaging that minimizes the risk of tombstoning, such as those with symmetrical leads or those designed for better solder joint formation.
2. Pad Design
Proper pad design is essential for preventing tombstoning. Consider the following guidelines:
- Pad size: Ensure that the pads are appropriately sized for the component. Pads that are too small can lead to Insufficient Solder joint formation, while oversized pads can cause uneven heating and solder distribution.
- Pad shape: Use symmetrical pad shapes to promote even heating and solder distribution. Avoid using irregular or unbalanced pad shapes.
- Solder Mask: Apply solder mask between the pads to prevent solder bridging and ensure proper solder joint formation.
3. Solder Paste Application
Consistent and accurate solder paste application is crucial for preventing tombstoning. Consider the following practices:
- Stencil design: Use a well-designed stencil with appropriate aperture sizes and shapes to ensure even solder paste deposition.
- Solder paste quality: Choose a high-quality solder paste with the right particle size, flux activity, and rheological properties for your application.
- Printing process: Optimize the solder paste printing process parameters, such as squeegee pressure, speed, and separation distance, to achieve consistent solder paste deposits.
4. Reflow Profile Optimization
A well-optimized reflow profile is essential for minimizing tombstoning. Consider the following factors:
- Peak temperature: Ensure that the peak temperature is high enough to allow for proper solder joint formation but not so high that it causes excessive component heating and tombstoning.
- Time above liquidus (TAL): Maintain an appropriate TAL to ensure complete solder melting and wetting without prolonged exposure to high temperatures.
- Ramp rates: Use gradual ramp rates during heating and cooling to minimize thermal stress on the components and prevent rapid changes in solder viscosity.
- Cooling rate: Control the cooling rate to allow for proper solder joint solidification and to minimize the risk of tombstoning due to rapid solidification.
5. Process Control and Monitoring
Implementing process control and monitoring measures can help identify and address tombstoning issues promptly. Consider the following practices:
- Solder paste inspection (SPI): Use SPI systems to verify the consistency and accuracy of solder paste deposits before the reflow process.
- Automated optical inspection (AOI): Employ AOI systems to detect tombstoning defects after the reflow process and provide feedback for process improvement.
- Statistical process control (SPC): Monitor process parameters, such as reflow oven temperatures and conveyor speeds, using SPC techniques to identify trends and variations that may contribute to tombstoning.
Correcting SMT Tombstoning
If tombstoning defects are detected after the reflow process, corrective actions may be necessary to salvage the affected PCBs. Consider the following approaches:
1. Manual Rework
For small-scale production or low-volume rework, manual correction of tombstoned components may be feasible. This involves:
- Carefully repositioning the tombstoned component using tweezers or a vacuum pickup tool.
- Applying additional solder paste or flux to the affected pads if necessary.
- Reflowing the localized area using a hot air rework station or soldering iron.
2. Automated Rework
For larger-scale production or high-volume rework, automated rework systems can be employed. These systems typically include:
- Vision-based component alignment and placement.
- Localized reflow using focused hot air or laser heating.
- Automated solder paste dispensing or flux dipping.
3. Selective Solder Mask Removal
In some cases, selective removal of the solder mask around the affected pads can help correct tombstoning. This allows for better solder wetting and helps to redistribute the solder evenly. However, this approach should be used cautiously and only when other methods have proven ineffective.
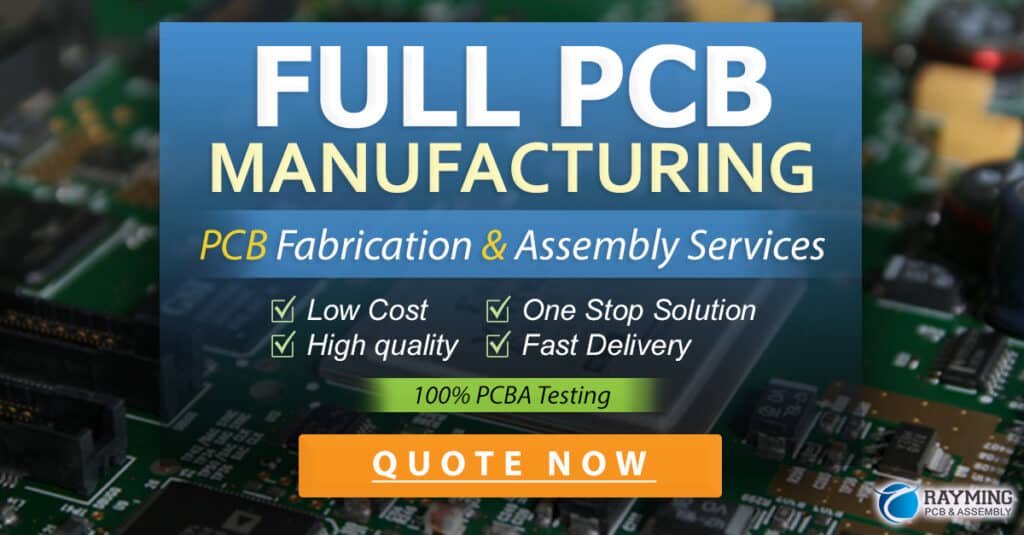
Conclusion
SMT tombstoning is a common defect that can adversely affect the reliability and functionality of PCB assemblies. By understanding the causes of tombstoning and implementing preventive measures, such as proper component selection, pad design, solder paste application, and reflow profile optimization, the occurrence of this defect can be minimized. Process control and monitoring techniques, along with appropriate rework methods, can further help in identifying and correcting tombstoning issues. By addressing SMT tombstoning proactively, manufacturers can improve the quality and reliability of their PCB assemblies, ultimately leading to better product performance and customer satisfaction.
Frequently Asked Questions (FAQ)
1. What is the most common cause of SMT tombstoning?
The most common cause of SMT tombstoning is uneven heating during the reflow soldering process. When one side of a component heats up faster than the other, it can cause the component to lift up on one end, resulting in a tombstone-like appearance.
2. Can SMT tombstoning be completely eliminated?
While it may not be possible to completely eliminate SMT tombstoning, implementing a combination of preventive measures, such as proper component selection, pad design, solder paste application, and reflow profile optimization, can significantly reduce its occurrence.
3. What types of components are most susceptible to tombstoning?
Components with a high aspect ratio (length to width) or those with a small contact area, such as chip resistors and capacitors with end terminations, are more susceptible to tombstoning compared to components with bottom terminations or larger contact areas.
4. How can solder paste application affect tombstoning?
Uneven or inconsistent solder paste application can lead to unbalanced surface tension forces during the reflow process, which can pull the component up on one side and cause tombstoning. Ensuring consistent and accurate solder paste deposition using a well-designed stencil and optimized printing process parameters can help minimize this issue.
5. What role does the reflow profile play in preventing tombstoning?
The reflow profile plays a crucial role in preventing tombstoning. An optimized reflow profile should have a peak temperature high enough for proper solder joint formation but not so high that it causes excessive component heating. Gradual ramp rates, appropriate time above liquidus (TAL), and controlled cooling rates can help minimize thermal stress on the components and reduce the risk of tombstoning.
Cause | Prevention |
---|---|
Uneven heating | Optimize reflow profile, use gradual ramp rates |
Unbalanced solder paste | Ensure consistent solder paste application |
Component geometry | Choose components with larger contact area or bottom terminations |
Pad design | Use symmetrical pad shapes and appropriate sizes |
Improper reflow profile | Optimize peak temperature, TAL, and cooling rate |
No responses yet