Introduction to Copper in PCB Design
Copper is the primary conductive material used in printed circuit board (PCB) design due to its excellent electrical conductivity, thermal conductivity, and cost-effectiveness. In PCB Manufacturing, Copper Foil is laminated onto a non-conductive substrate, such as FR-4, to create the conductive pathways that connect electronic components. The copper traces on a PCB are responsible for carrying electrical signals and power throughout the board.
Properties of Copper in PCBs
Property | Value |
---|---|
Electrical Conductivity | 5.96 × 10^7 S/m |
Thermal Conductivity | 401 W/(m·K) |
Density | 8.96 g/cm^3 |
Melting Point | 1084.62°C |
Copper’s high electrical conductivity allows for efficient signal transmission, while its thermal conductivity helps dissipate heat generated by electronic components. These properties make copper an ideal choice for PCB design.
The Importance of Board Edge in PCB Design
The board edge is the outer perimeter of a PCB, and it plays a crucial role in the overall design and functionality of the board. Proper management of the board edge is essential for several reasons:
- Mechanical stability: The board edge provides mechanical support for the PCB and helps maintain its structural integrity.
- Electromagnetic compatibility (EMC): The board edge can impact the electromagnetic compatibility of the PCB, as it can act as an antenna for electromagnetic interference (EMI).
- Signal integrity: Copper traces near the board edge can be susceptible to signal integrity issues, such as reflections and crosstalk.
- Manufacturing constraints: The board edge must adhere to manufacturing constraints, such as minimum distances between copper and the edge of the board.
Board Edge Clearance Requirements
To ensure proper manufacturing and functionality, PCB designers must adhere to board edge clearance requirements. These requirements specify the minimum distance between copper features (traces, pads, and planes) and the edge of the board.
Copper Feature | Minimum Edge Clearance |
---|---|
Traces | 0.2 mm |
Pads | 0.5 mm |
Planes | 0.5 mm |
Adhering to these clearance requirements helps prevent issues such as copper peeling, shorts, and signal integrity problems.
Designing Copper Features Near the Board Edge
When designing copper features near the board edge, PCB designers must consider several factors to ensure optimal performance and manufacturability.
Trace Routing Techniques
To minimize signal integrity issues and EMI, designers should follow these trace routing techniques near the board edge:
- Avoid parallel routing: Routing traces parallel to the board edge can create an antenna effect, leading to EMI. Instead, route traces perpendicular to the edge whenever possible.
- Maintain consistent impedance: Ensure that traces near the board edge maintain consistent impedance to minimize reflections and signal distortion.
- Use guard traces: Implement guard traces between sensitive signals and the board edge to reduce crosstalk and EMI.
Ground Planes and Stitching Vias
Proper use of ground planes and stitching vias near the board edge can help mitigate EMI and improve signal integrity.
- Extend ground planes: Extend ground planes to the board edge to provide a low-impedance return path for signals and reduce EMI.
- Implement stitching vias: Place stitching vias along the board edge to connect ground planes on different layers, creating a continuous shield against EMI.
Copper Thieving and Edge Plating
Copper thieving and edge plating are techniques used to improve copper balancing and mechanical stability at the board edge.
- Copper thieving: Add non-functional copper features near the board edge to balance Copper Distribution and prevent warping during manufacturing.
- Edge plating: Apply additional copper plating to the board edge to increase mechanical strength and protect against wear and tear.
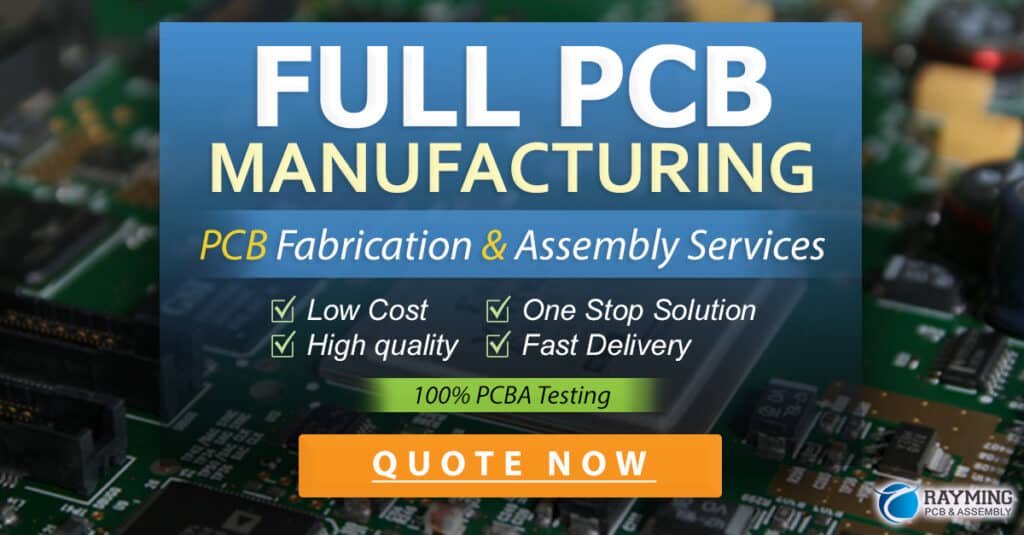
Manufacturing Considerations for Copper at the Board Edge
When designing PCBs with copper features near the board edge, it is essential to consider the manufacturing process to ensure the best possible results.
Panelization and Depaneling
Panelization is the process of grouping multiple PCBs onto a single panel for efficient manufacturing. Depaneling is the process of separating individual boards from the panel after manufacturing.
- Panelization techniques: Use tab-routing or V-scoring to create break-away tabs that connect individual boards within a panel.
- Depaneling methods: Employ methods such as manual breaking, routing, or punching to separate individual boards without damaging the copper features near the edge.
Solder Mask and Silkscreen
Proper application of solder mask and silkscreen near the board edge can help protect copper features and improve the overall aesthetics of the PCB.
- Solder mask coverage: Ensure that solder mask covers exposed copper features near the board edge to prevent oxidation and improve insulation.
- Silkscreen placement: Position silkscreen text and graphics away from the board edge to avoid interference with copper features and ensure legibility.
Troubleshooting Copper Issues at the Board Edge
Despite careful design and manufacturing considerations, issues related to copper at the board edge may still arise. Common problems include:
- Copper peeling: Copper traces or planes lifting away from the substrate near the board edge.
- Shorts: Unintended electrical connections between copper features due to insufficient clearance or manufacturing defects.
- Signal integrity issues: Reflections, crosstalk, or EMI affecting the performance of signals near the board edge.
To troubleshoot these issues, designers and manufacturers can:
- Review design files: Check the PCB design files for adherence to board edge clearance requirements and proper trace routing techniques.
- Inspect manufactured boards: Visually inspect manufactured PCBs for signs of copper peeling, shorts, or other defects near the board edge.
- Perform electrical testing: Conduct electrical tests to identify signal integrity issues or unintended connections related to copper at the board edge.
By identifying and addressing these issues early in the design and manufacturing process, PCB designers and manufacturers can ensure the optimal performance and reliability of their products.
Frequently Asked Questions (FAQ)
1. What is the minimum distance between copper traces and the board edge?
The minimum distance between copper traces and the board edge is typically 0.2 mm. However, this may vary depending on the specific manufacturing capabilities and design requirements of the PCB.
2. Why is it important to extend ground planes to the board edge?
Extending ground planes to the board edge provides a low-impedance return path for signals and helps reduce electromagnetic interference (EMI). This improves signal integrity and overall electromagnetic compatibility of the PCB.
3. What is copper thieving, and why is it used?
Copper thieving is the practice of adding non-functional copper features near the board edge to balance copper distribution during the PCB manufacturing process. This helps prevent warping and ensures a more uniform surface finish on the board.
4. How can I minimize signal integrity issues near the board edge?
To minimize signal integrity issues near the board edge, follow these best practices:
– Route traces perpendicular to the board edge whenever possible
– Maintain consistent impedance for traces near the edge
– Use guard traces between sensitive signals and the board edge
– Implement stitching vias to connect ground planes on different layers
5. What should I do if I encounter copper peeling near the board edge?
If you encounter copper peeling near the board edge, review your design files to ensure that you have adhered to the recommended board edge clearance requirements. If the issue persists, consult with your PCB Manufacturer to identify potential manufacturing process improvements or alternative material choices that can help prevent copper peeling.
Conclusion
Copper and the board edge are critical considerations in PCB design and manufacturing. By understanding the properties of copper, the importance of board edge management, and the various design and manufacturing techniques available, PCB designers can create high-quality, reliable, and electromagnetically compatible products. Adhering to best practices for trace routing, ground plane management, and manufacturing processes can help minimize issues related to copper at the board edge and ensure the optimal performance of the PCB.
No responses yet