Introduction to PCB Drilling
Printed Circuit Board (PCB) drilling is a crucial step in the manufacturing process of PCBs. It involves creating holes in the board to allow for the insertion of Electronic Components and the creation of electrical connections between layers. Drilling is typically done using specialized machines that can accurately create holes of various sizes and depths.
Types of PCB Drilling
There are two main types of PCB drilling:
-
Mechanical Drilling: This method uses physical drill bits to create holes in the PCB. It is the most common method of PCB drilling and is suitable for most applications.
-
Laser Drilling: This method uses a laser to create holes in the PCB. It is typically used for high-precision applications or for creating very small holes that cannot be achieved with mechanical drilling.
Importance of PCB Drilling
PCB drilling is an essential step in the manufacturing process of PCBs for several reasons:
-
Component Placement: Drilling creates holes that allow electronic components to be inserted into the PCB and soldered in place.
-
Electrical Connections: Drilling creates holes that allow for the creation of electrical connections between layers of the PCB.
-
Mounting: Drilling creates holes that allow the PCB to be mounted to other components or enclosures.
Challenges in PCB Drilling
While PCB drilling is a critical step in the manufacturing process, it also presents several challenges:
-
Accuracy: Drilling must be done with high accuracy to ensure that holes are placed precisely where they are needed. Any errors in drilling can lead to problems with component placement or electrical connections.
-
Speed: Drilling must be done quickly to keep up with production demands, but this can be challenging when dealing with high-density PCBs or boards with a large number of holes.
-
Hole Quality: The quality of the holes created during drilling is important for ensuring proper component placement and electrical connections. Poor hole quality can lead to issues such as burring or rough edges.
PCB Drilling Equipment
There are several types of equipment used for PCB drilling, each with its own advantages and disadvantages.
Mechanical Drilling Machines
Mechanical drilling machines use physical drill bits to create holes in the PCB. They are the most common type of drilling machine used in PCB manufacturing.
Advantages of Mechanical Drilling
- Suitable for most applications
- Can create holes of various sizes and depths
- Relatively low cost compared to laser drilling
Disadvantages of Mechanical Drilling
- Limited in terms of the smallest hole size that can be achieved
- Can be slower than laser drilling for high-density boards
- Can cause burring or rough edges on holes
Laser Drilling Machines
Laser drilling machines use a laser to create holes in the PCB. They are typically used for high-precision applications or for creating very small holes.
Advantages of Laser Drilling
- Can create very small holes (down to 25 microns)
- High precision and accuracy
- No physical contact with the PCB, reducing the risk of damage
- Fast drilling speeds for high-density boards
Disadvantages of Laser Drilling
- Higher cost compared to mechanical drilling
- Limited in terms of the maximum hole size that can be achieved
- May require additional equipment for handling and processing
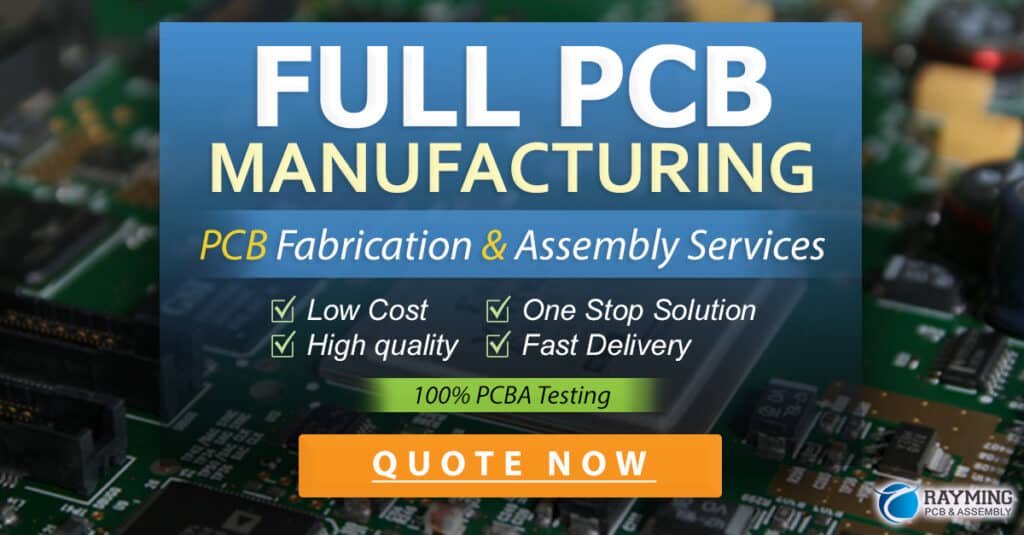
PCB Drilling Process
The PCB drilling process typically involves several steps:
-
Data Preparation: The first step is to prepare the data for the drilling process. This involves creating a drill file that specifies the location, size, and depth of each hole to be drilled.
-
Machine Setup: The drilling machine must be set up and calibrated to ensure accurate and precise drilling. This involves selecting the appropriate drill bits or laser settings and ensuring that the machine is properly aligned.
-
Drilling: The actual drilling process involves feeding the PCB into the drilling machine and creating the holes according to the drill file. This may be done in a single pass or in multiple passes, depending on the complexity of the board and the capabilities of the drilling machine.
-
Inspection: After drilling, the PCB is inspected to ensure that all holes have been drilled correctly and meet the required specifications. This may involve visual inspection, automated optical inspection (AOI), or other testing methods.
-
Cleaning: Finally, the PCB is cleaned to remove any debris or burrs created during the drilling process. This is typically done using a combination of mechanical and chemical cleaning methods.
Factors Affecting PCB Drilling Quality
There are several factors that can affect the quality of PCB drilling:
Drill Bits
The type and quality of drill bits used can have a significant impact on the quality of the holes created. Factors to consider include:
-
Material: Drill bits can be made from a variety of materials, including tungsten carbide, high-speed steel, and diamond-coated carbide. The choice of material depends on the specific application and the type of PCB being drilled.
-
Size: Drill bit size must be carefully selected to ensure that holes are the correct size for the components being used. Using the wrong size drill bit can lead to issues with component placement or electrical connections.
-
Wear: Drill bits can wear out over time, leading to reduced accuracy and hole quality. Regular inspection and replacement of drill bits is necessary to maintain high-quality drilling.
Spindle Speed and Feed Rate
The spindle speed and feed rate of the drilling machine can also affect the quality of the holes created. Higher spindle speeds and feed rates can lead to faster drilling times but may also result in reduced hole quality or increased wear on the drill bits.
PCB Material
The type of material used for the PCB can also affect the drilling process. Some materials, such as FR-4, are easier to drill than others, such as ceramic or metal-backed PCBs. The thickness of the PCB can also affect the drilling process, with thicker boards requiring more powerful drilling machines and slower feed rates.
Common PCB Drilling Defects
There are several common defects that can occur during PCB drilling:
Burring
Burring refers to the creation of rough edges or protrusions around the edges of drilled holes. This can be caused by dull or worn drill bits, incorrect spindle speeds or feed rates, or improper cleaning after drilling.
Misaligned Holes
Misaligned holes occur when the drilling machine is not properly calibrated or aligned, resulting in holes that are not placed precisely where they are needed. This can lead to issues with component placement or electrical connections.
Oversized or Undersized Holes
Oversized or undersized holes can occur when the wrong size drill bit is used or when the drilling machine is not properly calibrated. This can lead to issues with component placement or electrical connections.
Roughness
Roughness refers to the surface finish of the drilled holes. Rough or uneven surfaces can be caused by worn or damaged drill bits, incorrect spindle speeds or feed rates, or improper cleaning after drilling.
Best Practices for PCB Drilling
To ensure high-quality PCB drilling, there are several best practices that should be followed:
-
Use high-quality drill bits: Using high-quality drill bits that are appropriate for the specific application and PCB material can help ensure accurate and precise drilling.
-
Regularly inspect and replace drill bits: Regular inspection and replacement of drill bits can help prevent issues with hole quality and accuracy.
-
Use appropriate spindle speeds and feed rates: Using the appropriate spindle speeds and feed rates for the specific application and PCB material can help ensure high-quality drilling while minimizing wear on the drill bits.
-
Properly calibrate and align drilling machines: Regular calibration and alignment of drilling machines can help ensure accurate and precise drilling.
-
Use proper cleaning methods: Using appropriate cleaning methods after drilling can help remove debris and burrs and ensure high-quality holes.
Conclusion
PCB drilling is a critical step in the manufacturing process of PCBs, allowing for the placement of components and the creation of electrical connections between layers. While drilling presents several challenges, including accuracy, speed, and hole quality, following best practices and using appropriate equipment can help ensure high-quality drilling.
As PCB technology continues to advance, with smaller and more complex designs becoming increasingly common, the importance of high-quality PCB drilling will only continue to grow. By staying up-to-date with the latest drilling technologies and best practices, PCB Manufacturers can ensure that they are able to meet the demands of this evolving industry.
FAQ
-
What is PCB drilling?
PCB drilling is the process of creating holes in a printed circuit board to allow for the insertion of electronic components and the creation of electrical connections between layers. -
What are the two main types of PCB drilling?
The two main types of PCB drilling are mechanical drilling, which uses physical drill bits to create holes, and laser drilling, which uses a laser to create holes. -
Why is PCB drilling important?
PCB drilling is important because it allows for the placement of electronic components, the creation of electrical connections between layers, and the mounting of the PCB to other components or enclosures. -
What are some common defects that can occur during PCB drilling?
Common defects that can occur during PCB drilling include burring, misaligned holes, oversized or undersized holes, and roughness. -
What are some best practices for ensuring high-quality PCB drilling?
Best practices for ensuring high-quality PCB drilling include using high-quality drill bits, regularly inspecting and replacing drill bits, using appropriate spindle speeds and feed rates, properly calibrating and aligning drilling machines, and using proper cleaning methods after drilling.
PCB Drilling Method | Advantages | Disadvantages |
---|---|---|
Mechanical Drilling | – Suitable for most applications – Can create holes of various sizes and depths – Relatively low cost compared to laser drilling |
– Limited in terms of the smallest hole size that can be achieved – Can be slower than laser drilling for high-density boards – Can cause burring or rough edges on holes |
Laser Drilling | – Can create very small holes (down to 25 microns) – High precision and accuracy – No physical contact with the PCB, reducing the risk of damage – Fast drilling speeds for high-density boards |
– Higher cost compared to mechanical drilling – Limited in terms of the maximum hole size that can be achieved – May require additional equipment for handling and processing |
No responses yet