1. Choose the Right Materials for Flexible PCB Optimization
The first step in optimizing your flexible PCB manufacturing process is choosing the right materials. The most common materials used for flexible PCBs are polyimide (PI) and polyethylene terephthalate (PET). PI is more expensive but offers better thermal stability and electrical properties, while PET is cheaper but less durable.
Other materials to consider include:
- Flame Retardant 4 (FR-4): A popular choice for rigid PCBs, FR-4 can also be used for flexible PCBs in some cases.
- Thermoplastic Polyurethane (TPU): TPU offers excellent flexibility and durability, making it a good choice for wearable devices.
- Polyetherimide (PEI): PEI is a high-performance polymer that offers excellent thermal stability and mechanical properties.
Material | Advantages | Disadvantages |
---|---|---|
PI | High thermal stability, excellent electrical properties | Expensive |
PET | Affordable, good electrical properties | Less durable than PI |
FR-4 | Widely available, good mechanical properties | Limited flexibility |
TPU | Excellent flexibility and durability | Limited thermal stability |
PEI | High thermal stability, excellent mechanical properties | Expensive |
2. Use the Right Copper Thickness for Flexible PCB Optimization
The thickness of the copper layer in your flexible PCB can have a significant impact on its performance. Thicker copper layers offer better electrical conductivity and mechanical strength, but they also reduce flexibility and increase the overall thickness of the PCB.
The most common copper thicknesses used for flexible PCBs are:
- 18 microns (1/2 oz)
- 35 microns (1 oz)
- 70 microns (2 oz)
In general, thinner copper layers are better for applications that require high flexibility, while thicker layers are better for applications that require high current carrying capacity or mechanical strength.
3. Optimize Your Circuit Design for Flexible PCBs
Designing circuits for flexible PCBs requires a different approach than designing for rigid PCBs. Here are some tips for optimizing your circuit design for flexible PCBs:
- Use larger trace widths and spacing to reduce the risk of cracking or breaking during flexing.
- Avoid sharp corners and use rounded traces to reduce stress concentrations.
- Use teardrops at the junction of traces and pads to strengthen the connection.
- Avoid placing components near the edges of the PCB where flexing is most likely to occur.
- Use strain relief features such as slots or cutouts to reduce stress on the PCB.
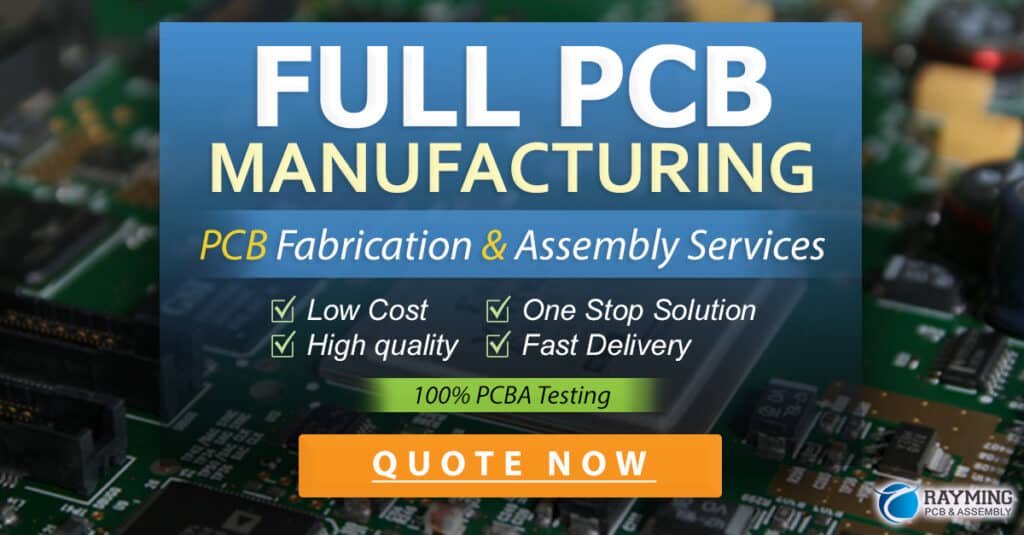
4. Choose the Right Adhesive for Flexible PCB Optimization
The adhesive used to bond the layers of a flexible PCB together can have a significant impact on its performance. The most common adhesives used for flexible PCBs are:
- Acrylic: Acrylic adhesives offer good adhesion and flexibility but have limited temperature resistance.
- Epoxy: Epoxy adhesives offer excellent strength and temperature resistance but are less flexible than acrylic adhesives.
- Silicone: Silicone adhesives offer excellent flexibility and temperature resistance but have lower adhesion strength than acrylic or epoxy adhesives.
When choosing an adhesive for your flexible PCB, consider the following factors:
- Temperature range: Choose an adhesive that can withstand the temperature range your PCB will be exposed to.
- Flexibility: Choose an adhesive that offers the right balance of flexibility and strength for your application.
- Adhesion strength: Choose an adhesive that offers sufficient adhesion strength to prevent delamination.
5. Use the Right Solder Mask for Flexible PCB Optimization
The solder mask is a protective layer that covers the copper traces on a PCB to prevent short circuits and improve solderability. When choosing a solder mask for your flexible PCB, consider the following factors:
- Flexibility: Choose a solder mask that remains flexible after curing to prevent cracking or peeling during flexing.
- Adhesion: Choose a solder mask that adheres well to the copper traces and substrate material.
- Thickness: Choose a solder mask thickness that provides sufficient coverage without adding too much stiffness to the PCB.
Some common solder mask materials used for flexible PCBs include:
- Photoimageable solder mask (PSM): PSM is a liquid photopolymer that is applied and then exposed to UV light to cure it. It offers excellent resolution and flexibility.
- Liquid photoimageable solder mask (LPSM): LPSM is similar to PSM but offers even better resolution and flexibility.
- Dry film solder mask (DFSM): DFSM is a solid film that is laminated onto the PCB and then exposed to UV light to cure it. It offers good coverage and durability but may be less flexible than PSM or LPSM.
6. Optimize Your Flexible PCB Stackup
The stackup of your flexible PCB refers to the arrangement of the layers that make up the PCB. Optimizing your stackup can help improve the performance and reliability of your flexible PCB. Here are some tips for optimizing your flexible PCB stackup:
- Use symmetric stackups: A symmetric stackup has an equal number of layers on either side of the neutral axis, which helps reduce warping and improves flexibility.
- Use thinner dielectric layers: Thinner dielectric layers reduce the overall thickness of the PCB and improve flexibility.
- Use copper-clad laminates: Copper-clad laminates (CCLs) are pre-bonded layers of copper and dielectric material that can be used to build up the layers of your PCB. Using CCLs can help improve the reliability and consistency of your PCB.
- Use blind and buried vias: Blind and buried vias allow you to make connections between internal layers of the PCB without drilling through the entire board. This can help reduce the size and improve the flexibility of your PCB.
Here’s an example of a simple 4-layer flexible PCB stackup:
Layer | Material | Thickness |
---|---|---|
Top Cover | PI | 25 microns |
Top Copper | Copper | 18 microns |
Dielectric 1 | PI | 50 microns |
Inner Layer 1 Copper | Copper | 18 microns |
Dielectric 2 | PI | 50 microns |
Inner Layer 2 Copper | Copper | 18 microns |
Dielectric 3 | PI | 50 microns |
Bottom Copper | Copper | 18 microns |
Bottom Cover | PI | 25 microns |
7. Use the Right Surface Finish for Flexible PCB Optimization
The surface finish is the final coating applied to the copper traces on a PCB to protect them from oxidation and improve solderability. When choosing a surface finish for your flexible PCB, consider the following factors:
- Flexibility: Choose a surface finish that remains flexible after application to prevent cracking or peeling during flexing.
- Solderability: Choose a surface finish that provides good solderability and prevents oxidation of the copper traces.
- Durability: Choose a surface finish that can withstand the environmental conditions your PCB will be exposed to.
Some common surface finishes used for flexible PCBs include:
- Immersion silver (IAg): IAg is a thin layer of silver that is chemically deposited onto the copper traces. It offers good solderability and flexibility but may tarnish over time.
- Electroless nickel immersion gold (ENIG): ENIG is a two-layer finish consisting of a nickel underlayer and a thin gold toplayer. It offers excellent solderability and durability but may be less flexible than other finishes.
- Organic solderability preservative (OSP): OSP is a thin organic coating that is applied to the copper traces to prevent oxidation. It offers good flexibility and is relatively inexpensive but may have limited shelf life.
8. Implement Proper Quality Control Measures
Implementing proper quality control measures is essential for ensuring the reliability and performance of your flexible PCBs. Here are some quality control measures to consider:
- Visual inspection: Visually inspect your PCBs for defects such as cracks, voids, or delamination.
- Electrical testing: Perform electrical testing to ensure that your PCBs meet your specified electrical requirements.
- Mechanical testing: Perform mechanical testing to ensure that your PCBs can withstand the stresses and strains they will be subjected to in use.
- Thermal cycling: Perform thermal cycling tests to ensure that your PCBs can withstand the temperature fluctuations they will be exposed to in use.
- Accelerated life testing: Perform accelerated life testing to simulate the aging of your PCBs and identify potential failure modes.
9. Work with an Experienced Flexible PCB Manufacturer
Finally, working with an experienced flexible PCB manufacturer can help ensure that your PCBs are manufactured to the highest quality standards. Look for a manufacturer with experience in flexible PCB fabrication and a proven track record of delivering high-quality products.
Some factors to consider when choosing a flexible PCB manufacturer include:
- Experience: Look for a manufacturer with experience in fabricating flexible PCBs for applications similar to yours.
- Capabilities: Ensure that the manufacturer has the equipment and capabilities necessary to meet your specific requirements.
- Quality certifications: Look for a manufacturer with relevant quality certifications such as ISO 9001 or UL certification.
- Customer service: Choose a manufacturer with responsive customer service and support.
FAQ
-
What is the difference between a flexible PCB and a rigid PCB?
A flexible PCB is made from flexible materials such as polyimide or PET and can bend and flex without breaking. A rigid PCB is made from rigid materials such as FR-4 and cannot bend or flex. -
What are some common applications for flexible PCBs?
Flexible PCBs are commonly used in applications that require flexibility or space savings, such as wearable devices, medical devices, automotive electronics, and consumer electronics. -
What are some common challenges in manufacturing flexible PCBs?
Some common challenges in manufacturing flexible PCBs include maintaining the flexibility and durability of the materials, ensuring proper adhesion between layers, and preventing cracking or delamination during flexing. -
How can I ensure the reliability of my flexible PCBs?
To ensure the reliability of your flexible PCBs, choose the right materials and adhesives, optimize your circuit design and stackup, implement proper quality control measures, and work with an experienced flexible PCB manufacturer. -
What should I look for in a flexible PCB manufacturer?
When choosing a flexible PCB manufacturer, look for experience in fabricating flexible PCBs for applications similar to yours, capabilities to meet your specific requirements, relevant quality certifications, and responsive customer service and support.
In conclusion, optimizing your flexible PCB manufacturing process requires careful consideration of materials, design, and manufacturing practices. By following the nine tips outlined in this article and working with an experienced flexible PCB manufacturer, you can ensure that your flexible PCBs are manufactured to the highest quality standards and meet the performance and reliability requirements of your application.
No responses yet