Introduction to PCB Optimization for Motor Controls
When designing a high current PCB for motor controls, optimization is key to ensure reliable performance, efficient power delivery, and thermal management. In this comprehensive article, we will explore various techniques and considerations for optimizing PCB layouts specifically tailored for motor control applications.
Understanding the Challenges of High Current PCB Design
High current PCB design presents unique challenges compared to low current designs. Some of the key challenges include:
- Increased power dissipation and heat generation
- Larger trace widths and copper weights required for current carrying capacity
- Potential for voltage drops and power losses
- EMI and noise considerations due to high switching frequencies
Benefits of Optimizing High Current PCB for Motor Controls
By optimizing the PCB design for motor controls, you can achieve several benefits:
- Improved system efficiency and reduced power losses
- Better thermal management and heat dissipation
- Enhanced reliability and longevity of the motor control system
- Reduced EMI and noise interference
- Compact and cost-effective PCB layouts
PCB Layout Techniques for High Current Motor Controls
Power and Ground Plane Design
One of the most critical aspects of high current PCB design is the proper implementation of power and ground planes. Here are some best practices:
- Use dedicated power and ground planes to provide low-impedance paths for current flow
- Ensure adequate copper weight and thickness for the power and ground planes
- Minimize the impedance of the power distribution network (PDN)
- Use multiple vias to connect power and ground planes to component pins
Trace Routing and Sizing
Proper trace routing and sizing are crucial for handling high currents in motor control PCBs. Consider the following guidelines:
- Calculate the required trace width based on the maximum current, copper thickness, and temperature rise
- Use wide traces for high current paths to minimize resistance and voltage drops
- Provide sufficient spacing between traces to avoid crosstalk and interference
- Route high current traces away from sensitive analog or digital signals
Current (A) | Trace Width (mm) for 1 oz Copper | Trace Width (mm) for 2 oz Copper |
---|---|---|
5 | 2.5 | 1.25 |
10 | 5.0 | 2.5 |
20 | 10.0 | 5.0 |
30 | 15.0 | 7.5 |
Component Placement and Thermal Management
Strategic component placement and thermal management techniques help in optimizing high current PCBs for motor controls:
- Place power components, such as MOSFETs and drivers, close to each other to minimize trace lengths
- Use thermal reliefs for power components to improve heat dissipation
- Incorporate heat sinks or cooling mechanisms for critical components
- Consider using thermal vias to transfer heat from components to the opposite side of the PCB
Grounding and Shielding Techniques
Proper grounding and shielding are essential to mitigate EMI and noise in high current motor control PCBs:
- Implement a solid ground plane to provide a low-impedance return path for high-frequency currents
- Use ground loops or guard rings around sensitive analog or digital circuits
- Implement shielding techniques, such as copper pours or shield cans, to isolate noisy components
- Use differential signaling for critical control signals to reduce common-mode noise
Advanced PCB Optimization Techniques
Multi-Layer PCB Design
For complex motor control systems, multi-layer PCB design offers several advantages:
- Allows for dedicated power and ground planes on separate layers
- Provides flexibility in routing and component placement
- Enables better signal integrity and noise isolation
- Facilitates efficient heat dissipation through thermal vias
Simulation and Analysis
Simulation and analysis tools can greatly assist in optimizing high current PCB designs for motor controls:
- Use power integrity simulations to analyze voltage drops, current densities, and thermal behavior
- Perform signal integrity simulations to ensure proper signal quality and timing
- Conduct EMI/EMC simulations to identify and mitigate potential electromagnetic interference issues
- Utilize thermal simulations to optimize component placement and cooling strategies
Design for Manufacturing (DFM) Considerations
When optimizing high current PCBs for motor controls, it’s important to consider DFM aspects:
- Adhere to the manufacturer’s design rules and guidelines for minimum trace widths, clearances, and drill sizes
- Use standard component sizes and footprints to improve manufacturability and reduce costs
- Incorporate testability features, such as test points and boundary scan, for easier debugging and validation
- Consider the assembly process, including component orientation and placement, to ensure smooth manufacturing
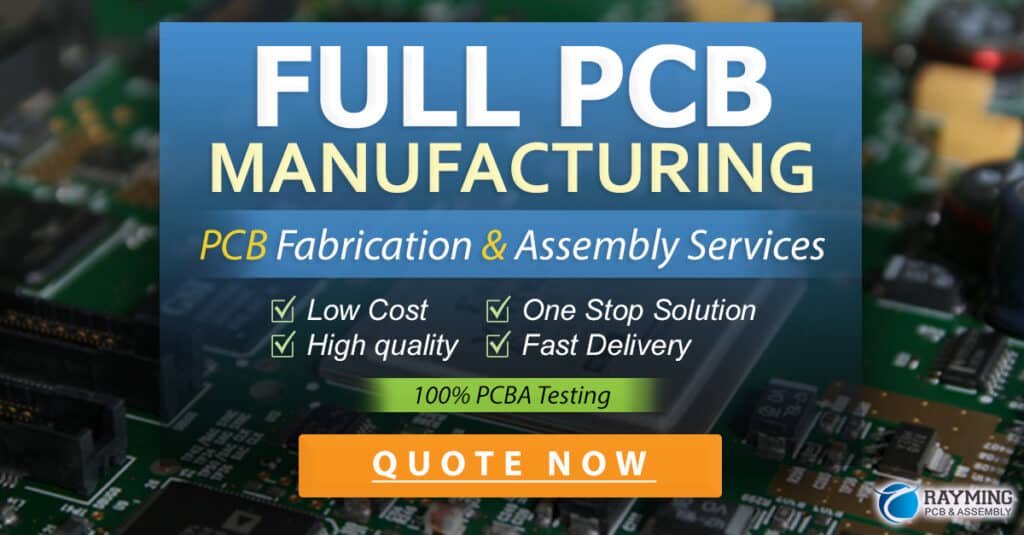
Testing and Validation
Prototyping and Bench Testing
Before finalizing the PCB design, prototyping and bench testing are crucial steps:
- Fabricate prototype PCBs to validate the design and identify any issues
- Perform functional testing to ensure the motor control system operates as intended
- Conduct thermal testing to verify the effectiveness of cooling mechanisms and thermal management techniques
- Measure and analyze key parameters, such as voltage levels, current waveforms, and switching frequencies
Compliance Testing and Certification
Depending on the application and target market, compliance testing and certification may be required:
- Conduct EMC testing to ensure the PCB meets electromagnetic compatibility standards
- Perform safety testing, such as isolation and insulation tests, to comply with relevant safety regulations
- Obtain necessary certifications, such as UL, CE, or FCC, based on the specific requirements of the motor control system
Best Practices and Common Pitfalls
Design Guidelines and Checklist
To ensure a well-optimized high current PCB for motor controls, follow these design guidelines:
- Use a checklist to review and verify critical design aspects, such as power and ground plane design, trace sizing, and component placement
- Follow industry-standard design rules and guidelines for high current PCB design
- Document the design decisions, calculations, and simulations for future reference and maintenance
Common Mistakes to Avoid
Be aware of common mistakes that can hinder PCB optimization for motor controls:
- Underestimating the required trace widths and copper weights for high current paths
- Neglecting thermal management and heat dissipation considerations
- Inadequate grounding and shielding techniques leading to EMI and noise issues
- Overlooking DFM aspects, resulting in manufacturing challenges and delays
Frequently Asked Questions (FAQ)
-
Q: What is the recommended copper weight for high current PCB traces in motor control applications?
A: The recommended copper weight depends on the specific current requirements. For high current traces, using 2 oz or even 4 oz copper is common to ensure sufficient current carrying capacity and minimize voltage drops. -
Q: How can I minimize voltage drops in high current PCB traces?
A: To minimize voltage drops, use wider traces with adequate copper weight, keep trace lengths as short as possible, and consider using multiple vias to connect the traces to power and ground planes. -
Q: What are some effective thermal management techniques for high current motor control PCBs?
A: Effective thermal management techniques include using dedicated power and ground planes, incorporating thermal vias, using heat sinks or cooling mechanisms for critical components, and strategically placing components to optimize heat dissipation. -
Q: How can I reduce EMI and noise in high current motor control PCBs?
A: To reduce EMI and noise, implement proper grounding techniques, use shielding methods like copper pours or shield cans, route high current traces away from sensitive signals, and consider using differential signaling for critical control signals. -
Q: What are the benefits of using multi-layer PCBs for high current motor control applications?
A: Multi-layer PCBs offer benefits such as dedicated power and ground planes, improved signal integrity, better noise isolation, efficient heat dissipation through thermal vias, and increased flexibility in routing and component placement.
Conclusion
Optimizing high current PCBs for motor controls requires careful consideration of various design aspects, including power and ground plane design, trace routing and sizing, component placement, thermal management, grounding, and shielding. By following best practices, utilizing advanced techniques, and conducting thorough testing and validation, you can achieve reliable, efficient, and robust motor control systems.
Remember to prioritize safety, comply with relevant standards and regulations, and collaborate with experienced PCB designers and manufacturers to ensure the success of your high current motor control PCB projects.
No responses yet