Introduction to PCB Issues
Printed Circuit Boards (PCBs) are essential components in modern electronics, forming the backbone of devices ranging from smartphones to industrial control systems. While PCBs have revolutionized the electronics industry, they are not without their share of problems. In this article, we will explore nine common issues encountered with PCBs and provide solutions to overcome them, ensuring the reliability and longevity of your electronic devices.
Problem 1: Solder Bridges and Short Circuits
What are Solder Bridges?
Solder bridges occur when excess solder creates an unintended connection between two or more conductors on a PCB. This results in a short circuit, which can lead to malfunctions or even permanent damage to the board and its components.
Solutions for Solder Bridges
-
Use the appropriate amount of solder: Applying the right amount of solder is crucial to avoid excess solder forming bridges. Follow the manufacturer’s guidelines and use solder with the correct diameter.
-
Proper soldering technique: Maintain a steady hand and use the correct soldering iron temperature. Apply solder quickly and precisely to prevent it from spreading to adjacent pads.
-
Solder mask: Ensure that the PCB has a properly designed solder mask, which helps prevent solder from bridging between closely spaced pads.
-
Inspect and rework: After soldering, visually inspect the board for any solder bridges. If found, use a desoldering wick or a solder sucker to remove the excess solder and rework the connection.
Problem | Cause | Solution |
---|---|---|
Solder Bridges | Excess solder | Use appropriate amount of solder |
Improper soldering technique | Maintain steady hand and correct temperature | |
Inadequate solder mask | Ensure properly designed solder mask | |
Lack of inspection | Visually inspect and rework if necessary |
Problem 2: Dry Solder Joints
What are Dry Solder Joints?
Dry solder joints, also known as Cold Solder Joints, occur when the solder fails to form a proper bond with the pad or component lead. This can happen due to insufficient heat, improper solder flow, or contamination of the surfaces being soldered.
Solutions for Dry Solder Joints
-
Clean surfaces: Ensure that the pads and component leads are clean and free from oxidation or contamination before soldering. Use a solvent or solder flux to clean the surfaces.
-
Correct soldering temperature: Use a soldering iron with the appropriate temperature for the type of solder being used. Insufficient heat can lead to dry solder joints.
-
Proper solder flow: Apply solder to both the pad and the component lead, allowing it to flow evenly and form a smooth, shiny joint. Avoid disturbing the joint until the solder has cooled and solidified.
-
Inspect and rework: Visually inspect the solder joints for any dull, grainy, or incomplete connections. If found, reheat the joint and apply additional solder or flux as needed.
Problem | Cause | Solution |
---|---|---|
Dry Solder Joints | Insufficient heat | Use correct soldering temperature |
Improper solder flow | Apply solder to both pad and lead | |
Surface contamination | Clean surfaces before soldering | |
Lack of inspection | Visually inspect and rework if necessary |
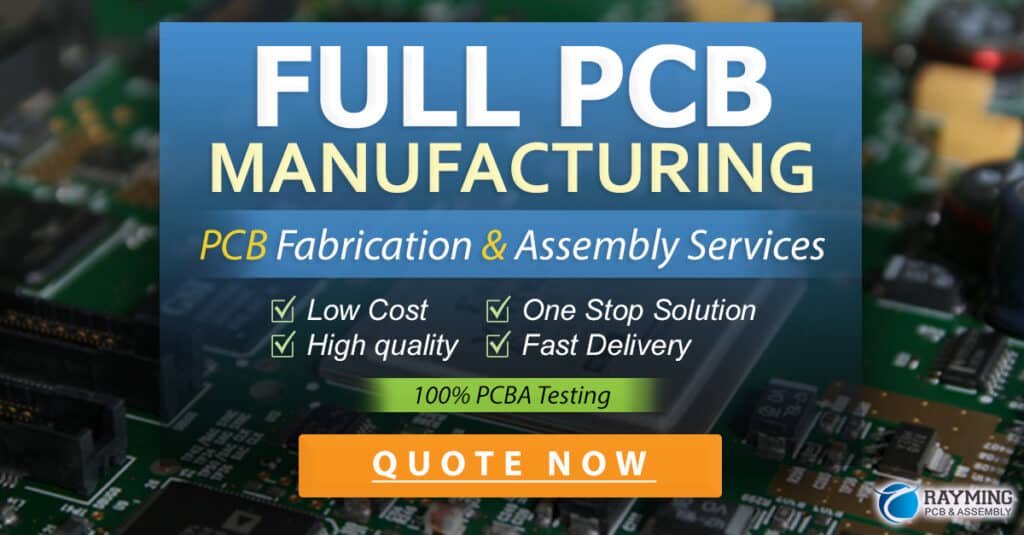
Problem 3: Component Misalignment
What is Component Misalignment?
Component misalignment occurs when a component is not placed accurately on its designated pads or footprint. This can lead to poor electrical connections, mechanical stress, and even short circuits if the misaligned component touches adjacent conductors.
Solutions for Component Misalignment
-
Use alignment tools: Employ pick-and-place machines, alignment jigs, or templates to ensure precise component placement during assembly.
-
Visual inspection: Perform a visual inspection of the board after component placement to identify any misaligned components before soldering.
-
Rework and replace: If a misaligned component is discovered after soldering, carefully desolder it using a desoldering tool or hot air rework station. Clean the pads and replace the component in its correct position.
-
Design for manufacturability: When designing the PCB, consider the component sizes, pad dimensions, and spacing to allow for easy and accurate placement during assembly.
Problem | Cause | Solution |
---|---|---|
Component Misalignment | Inaccurate placement | Use alignment tools and jigs |
Lack of inspection | Perform visual inspection before soldering | |
Improper PCB design | Design for manufacturability | |
Soldering before correction | Rework and replace misaligned components |
Problem 4: Copper Trace Damage
What is Copper Trace Damage?
Copper trace damage refers to the physical damage or deterioration of the conductive copper traces on a PCB. This can occur due to mechanical stress, corrosion, or manufacturing defects, resulting in open circuits or increased resistance.
Solutions for Copper Trace Damage
-
Proper handling: Handle PCBs with care during assembly and installation to avoid mechanical damage to the copper traces. Use anti-static mats and wrist straps to prevent electrostatic discharge (ESD) damage.
-
Conformal coating: Apply a conformal coating to the PCB to protect the copper traces from corrosion and environmental factors such as moisture and contaminants.
-
Inspection and testing: Perform visual inspections and continuity tests to identify any damaged traces. Use a Multimeter or automated testing equipment to verify the integrity of the traces.
-
Repair and rework: For minor trace damage, use conductive epoxy, wire jumpers, or trace repair kits to bridge the damaged area. For extensive damage, consider scrapping the board and fabricating a new one.
Problem | Cause | Solution |
---|---|---|
Copper Trace Damage | Mechanical stress | Proper handling and ESD Protection |
Corrosion | Apply conformal coating | |
Manufacturing defects | Inspection and testing | |
Open circuits or high resistance | Repair minor damage or scrap board |
Problem 5: Incorrect Component Polarity
What is Incorrect Component Polarity?
Incorrect component polarity occurs when a polarized component, such as an electrolytic capacitor or diode, is soldered onto the PCB with its polarity reversed. This can lead to component failure, circuit malfunction, or even damage to other components on the board.
Solutions for Incorrect Component Polarity
-
Clear markings: Ensure that the PCB layout includes clear polarity markings for polarized components, such as a “+” sign or a diode symbol. This helps prevent confusion during assembly.
-
Visual inspection: Before soldering, visually inspect the polarized components to ensure they are placed correctly according to the polarity markings on the board.
-
Rework and replace: If an incorrectly polarized component is discovered after soldering, carefully desolder it using a desoldering tool or hot air rework station. Replace the component with the correct polarity.
-
Use polarized component holders: When possible, use component holders or sockets that are designed to accept polarized components only in the correct orientation.
Problem | Cause | Solution |
---|---|---|
Incorrect Component Polarity | Confusion during assembly | Clear polarity markings on PCB |
Lack of inspection | Visual inspection before soldering | |
Improper component placement | Rework and replace with correct polarity | |
Non-polarized component holders | Use polarized component holders |
Problem 6: Inadequate Solder Mask Coverage
What is Inadequate Solder Mask Coverage?
Solder mask is a protective layer applied to the copper traces on a PCB to prevent solder bridging and provide insulation. Inadequate solder mask coverage can expose the copper traces, leading to short circuits, corrosion, or unintended solder connections.
Solutions for Inadequate Solder Mask Coverage
-
Proper solder mask design: Ensure that the solder mask is designed with adequate clearance around pads and traces, following the manufacturer’s guidelines for minimum solder mask webbing and spacing.
-
Solder mask expansion: Consider expanding the solder mask around critical areas, such as fine-pitch components or high-voltage traces, to provide extra protection against solder bridging.
-
Inspection and touch-up: Visually inspect the PCB for any areas where the solder mask is missing or inadequate. Use a solder mask pen or a small brush to apply additional solder mask to the exposed areas.
-
Quality control: Implement strict quality control measures during PCB fabrication to ensure consistent and adequate solder mask coverage across the entire board.
Problem | Cause | Solution |
---|---|---|
Inadequate Solder Mask Coverage | Improper solder mask design | Follow manufacturer’s guidelines for clearance |
Insufficient protection | Expand solder mask around critical areas | |
Manufacturing defects | Inspection and touch-up with solder mask pen | |
Inconsistent coverage | Implement strict quality control measures |
Problem 7: Tombstoning
What is Tombstoning?
Tombstoning, also known as Manhattan effect or Stonehenge effect, is a phenomenon where a surface-mounted component (SMD) stands up on one end during the soldering process. This typically occurs with small, lightweight components such as chip resistors and capacitors.
Solutions for Tombstoning
-
Balanced pad design: Ensure that the PCB pads for the SMD components are designed with equal size and symmetry. Uneven pad sizes can cause unbalanced surface tension during soldering, leading to tombstoning.
-
Proper reflow profile: Optimize the reflow soldering profile to ensure even heating and cooling of the components. Rapid temperature changes can contribute to tombstoning.
-
Adequate solder paste: Apply the appropriate amount of solder paste to the pads. Insufficient solder paste can cause the component to stand up on one end due to uneven solder joint formation.
-
Component placement accuracy: Use a precise pick-and-place machine or placement jig to ensure accurate and consistent placement of SMD components on the pads.
Problem | Cause | Solution |
---|---|---|
Tombstoning | Uneven pad sizes | Balanced pad design |
Rapid temperature changes | Proper reflow profile | |
Insufficient solder paste | Adequate solder paste application | |
Inaccurate component placement | Precise pick-and-place machine or jig |
Problem 8: Whiskers
What are Whiskers?
Whiskers are thin, filament-like protrusions that can grow from the surface of tin, zinc, or cadmium plating on PCBs and electronic components. These whiskers can cause short circuits, signal disturbances, and reliability issues in electronic devices.
Solutions for Whiskers
-
Lead-free solder: Use lead-free solder alloys that are less prone to whisker growth, such as tin-silver-copper (SAC) alloys.
-
Conformal coating: Apply a conformal coating to the PCB to prevent whisker growth by providing a barrier between the metal surfaces and the environment.
-
Proper storage and handling: Store PCBs and components in a controlled environment with low humidity and stable temperature to minimize the risk of whisker growth.
-
Regular inspection: Perform periodic visual inspections of the PCBs and components to detect any whisker growth early on. Use magnification tools or scanning electron microscopy (SEM) for detailed examinations.
Problem | Cause | Solution |
---|---|---|
Whiskers | Tin, zinc, or cadmium plating | Use lead-free solder alloys |
Environmental factors | Apply conformal coating | |
Improper storage and handling | Proper storage in controlled environment | |
Lack of inspection | Regular visual inspections and SEM analysis |
Problem 9: Thermal Stress and Warpage
What is Thermal Stress and Warpage?
Thermal stress and warpage occur when a PCB is subjected to temperature fluctuations during manufacturing, assembly, or operation. The different thermal expansion rates of the PCB substrate, copper traces, and components can cause the board to warp or deform, leading to mechanical stress and potential failures.
Solutions for Thermal Stress and Warpage
-
Material selection: Choose PCB Substrate Materials with low coefficients of thermal expansion (CTE) that closely match the CTE of the components. This helps minimize the differential expansion and reduces thermal stress.
-
Proper design: Incorporate features such as balanced copper distribution, symmetrical component placement, and adequate thermal relief in the PCB design to evenly distribute heat and minimize warpage.
-
Controlled manufacturing processes: Implement strict temperature control during PCB fabrication and assembly processes to avoid excessive thermal stress. Use gradual heating and cooling cycles to minimize sudden temperature changes.
-
Conformal coating and underfill: Apply conformal coating or underfill materials to provide additional mechanical support and help distribute thermal stress evenly across the board and components.
Problem | Cause | Solution |
---|---|---|
Thermal Stress and Warpage | Differential thermal expansion | Material selection with matching CTE |
Uneven heat distribution | Proper PCB design for thermal management | |
Excessive temperature fluctuations | Controlled manufacturing processes | |
Lack of mechanical support | Conformal coating and underfill application |
FAQ
- What are the most common causes of solder bridges on PCBs?
- Excess solder application
- Improper soldering technique
- Inadequate solder mask coverage
-
Closely spaced pads or traces
-
How can I prevent component misalignment during PCB Assembly?
- Use alignment tools such as pick-and-place machines or jigs
- Perform visual inspections before soldering
- Design the PCB with consideration for manufacturability
-
Rework and replace misaligned components
-
What are the consequences of incorrect component polarity on a PCB?
- Component failure
- Circuit malfunction
- Damage to other components on the board
-
Reduced reliability and performance
-
How can whiskers cause problems in electronic devices?
- Short circuits between adjacent conductors
- Signal disturbances and interference
- Reliability issues and potential device failures
-
Intermittent or permanent malfunctions
-
What design considerations can help minimize thermal stress and warpage in PCBs?
- Choosing substrate materials with low and matching CTE
- Balancing copper distribution and component placement
- Incorporating thermal relief and heat dissipation features
- Using conformal coating or underfill for mechanical support
Conclusion
PCB issues can have a significant impact on the performance, reliability, and longevity of electronic devices. By understanding the common problems such as solder bridges, dry solder joints, component misalignment, copper trace damage, incorrect component polarity, inadequate solder mask coverage, tombstoning, whiskers, and thermal stress and warpage, designers and manufacturers can take proactive steps to mitigate these issues.
Implementing proper design practices, controlled manufacturing processes, and thorough inspection and testing procedures can help identify and resolve PCB issues early in the development cycle. By staying informed about the latest advancements in materials, techniques, and quality control measures, the electronics industry can continue to produce high-quality, reliable PCBs that power the devices we depend on every day.
No responses yet