Introduction to DC Motor Controllers
A DC motor controller is an electronic device that regulates the speed, torque, direction, and other parameters of a DC motor. It essentially acts as an intermediary between the power source and the motor, allowing precise control over the motor’s operation. DC Motor Controllers are used in a wide range of applications, from small household appliances to large industrial machinery.
How DC Motor Controllers Work
DC motor controllers work by manipulating the voltage and current supplied to the motor. They typically use pulse-width modulation (PWM) to vary the average voltage delivered to the motor, which in turn controls the motor’s speed. The controller can also reverse the polarity of the voltage to change the motor’s direction of rotation.
The basic components of a DC motor controller include:
- Power supply: Provides the necessary voltage and current to operate the motor.
- Microcontroller or control circuit: Processes input signals and generates the appropriate output signals to control the motor.
- Power electronics: Includes components such as transistors, MOSFETs, or IGBTs that switch the power supplied to the motor.
- Feedback sensors: Provide information about the motor’s speed, position, or current, which is used by the controller to make adjustments.
Types of DC Motor Controllers
There are several types of DC motor controllers, each with its own unique features and applications:
1. PWM Controllers
PWM controllers are the most common type of DC motor controller. They use pulse-width modulation to vary the average voltage supplied to the motor, which in turn controls the motor’s speed. PWM controllers are relatively simple and inexpensive, making them a popular choice for many applications.
2. PID Controllers
PID (Proportional-Integral-Derivative) controllers use a feedback loop to continuously monitor the motor’s performance and make adjustments as needed. They are more advanced than PWM controllers and offer better precision and stability, particularly in applications where load conditions may vary.
3. Servo Controllers
Servo controllers are designed specifically for use with servo motors, which are commonly used in robotics and automation applications. These controllers provide precise position control and can handle more complex motion profiles than standard DC motor controllers.
4. Brushless DC Motor Controllers
Brushless DC (BLDC) motors require specialized controllers that can manage the motor’s commutation sequence. BLDC controllers are typically more complex and expensive than brushed DC motor controllers but offer higher efficiency and performance.
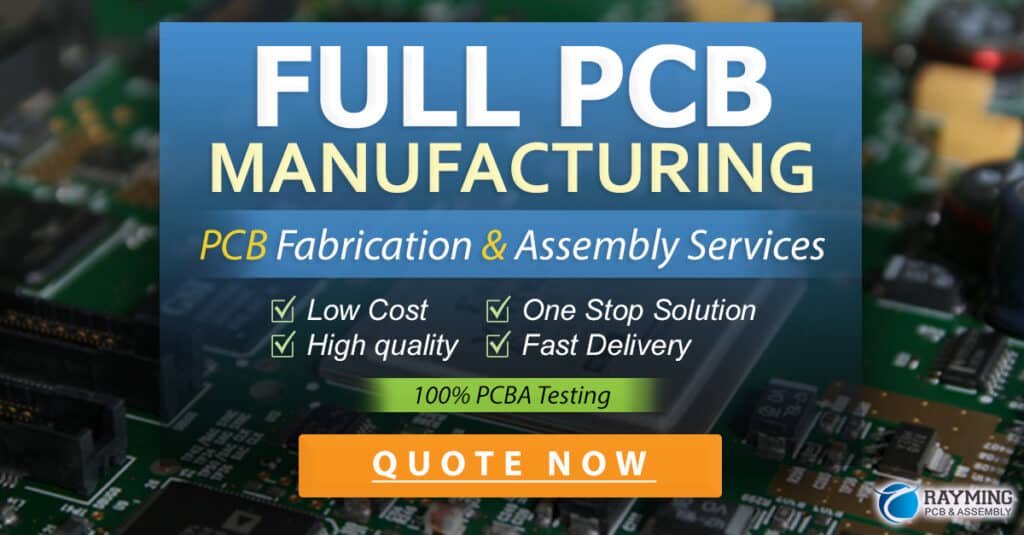
Selecting the Right DC Motor Controller
When choosing a DC motor controller for your application, consider the following factors:
- Motor type: Ensure that the controller is compatible with your specific DC motor (brushed or brushless).
- Power requirements: Select a controller that can handle the voltage and current requirements of your motor.
- Control features: Consider the level of control you need, such as speed, position, or torque control, and choose a controller that offers those features.
- Environment: If the controller will be used in harsh conditions (e.g., high temperatures, moisture, or vibration), choose one that is designed to withstand those conditions.
- Budget: DC motor controllers vary in price, so consider your budget when making a selection.
Implementing a DC Motor Controller
Once you have selected an appropriate DC motor controller for your application, you’ll need to properly implement it. The specific steps will vary depending on the type of controller and motor you are using, but the general process involves:
-
Wiring: Connect the power supply, motor, and any necessary feedback sensors to the controller according to the manufacturer’s instructions.
-
Programming: If the controller requires programming, use the provided software or development environment to configure the controller’s parameters and settings.
-
Tuning: Depending on the type of controller and the requirements of your application, you may need to tune the controller’s settings to achieve optimal performance. This may involve adjusting parameters such as PID gains, current limits, or acceleration/deceleration rates.
-
Testing: Before putting the motor and controller into service, thoroughly test the system to ensure that it performs as expected and that all safety features are functioning properly.
Troubleshooting DC Motor Controllers
If you encounter issues with your DC motor controller, there are several common problems and solutions to consider:
-
Motor not responding: Check the wiring connections and ensure that the power supply is providing the correct voltage and current. Also, verify that the controller’s settings are properly configured for your motor.
-
Erratic motor behavior: This could be caused by electrical noise or interference. Ensure that the wiring is properly shielded and that the controller is grounded correctly. It may also be necessary to add filtering capacitors or chokes to the power supply or motor leads.
-
Overheating: If the controller or motor is overheating, it may be operating beyond its rated capacity. Verify that the controller and motor are properly sized for your application and that there is adequate cooling or ventilation.
-
Inaccurate speed or position control: This could be due to incorrect feedback sensor settings or improper tuning of the controller’s parameters. Double-check the sensor wiring and calibration, and adjust the controller’s settings as needed.
Future Trends in DC Motor Controllers
As technology advances, DC motor controllers are becoming increasingly sophisticated and feature-rich. Some of the trends shaping the future of DC motor controllers include:
-
Integration with IoT: Controllers with built-in wireless connectivity (e.g., Wi-Fi, Bluetooth) allow for remote monitoring and control of motors via the Internet of Things (IoT) platforms.
-
Advanced algorithms: More sophisticated control algorithms, such as adaptive or predictive control, are being implemented in DC motor controllers to improve performance and efficiency.
-
Miniaturization: With the development of smaller, more powerful electronic components, DC motor controllers are becoming more compact and lightweight, allowing for integration into smaller devices and applications.
-
Energy efficiency: There is a growing emphasis on energy-efficient motor control, with controllers incorporating features such as regenerative braking and power optimization to reduce energy consumption.
Frequently Asked Questions (FAQ)
1. Can a DC motor controller be used with an AC motor?
No, DC motor controllers are designed specifically for use with DC motors. AC motors require different types of controllers, such as variable frequency drives (VFDs) or inverters.
2. What is the difference between open-loop and closed-loop control in DC motor controllers?
Open-loop control does not use feedback from the motor to make adjustments, while closed-loop control relies on feedback sensors to monitor the motor’s performance and make real-time adjustments. Closed-loop control generally offers better precision and stability.
3. How do I determine the power rating of the DC motor controller I need?
The power rating of the DC motor controller should match or exceed the power requirements of your motor. To determine this, multiply the motor’s rated voltage by its rated current. For example, a 24V motor with a rated current of 10A would require a controller with a power rating of at least 240W.
4. Can I use a DC motor controller to control multiple motors?
In some cases, yes. However, you must ensure that the controller’s power rating is sufficient to handle the combined load of all the motors. Additionally, some controllers may have a limited number of output channels, so you may need a controller specifically designed for multi-motor applications.
5. What safety features should I look for in a DC motor controller?
Important safety features in DC motor controllers include over-voltage and under-voltage protection, over-current protection, thermal shutdown, and Short-Circuit Protection. These features help protect both the controller and the motor from damage in the event of a fault or malfunction.
Conclusion
DC motor controllers are essential components in a wide range of applications, from robotics and automation to automotive and industrial systems. Understanding the basics of how these controllers work, the different types available, and how to select and implement them is crucial for anyone working with DC motors.
As technology continues to advance, DC motor controllers are becoming more sophisticated and feature-rich, offering opportunities for improved performance, efficiency, and connectivity. By staying informed about these developments and following best practices for implementation and troubleshooting, you can ensure that your DC motor control systems operate reliably and effectively.
No responses yet