Misconception 1: More Layers Always Means Better Performance
One of the most common PCB misconceptions is that increasing the number of layers in a PCB will always result in better performance. While it is true that multi-layer PCBs offer advantages such as reduced electromagnetic interference (EMI) and improved signal integrity, the number of layers should be carefully considered based on the specific requirements of your design.
Number of Layers | Advantages | Disadvantages |
---|---|---|
Single Layer | Low cost, simple design | Limited routing options, higher EMI |
Double Layer | Improved routing, better signal integrity | Increased cost compared to single layer |
Multi-Layer | Excellent signal integrity, reduced EMI, high density | Higher cost, complex design and manufacturing |
It is essential to strike a balance between performance, cost, and manufacturability when deciding on the number of layers for your PCB. In many cases, a well-designed double-layer PCB can provide sufficient performance for most applications while keeping costs under control.
Misconception 2: Tighter Tolerances Always Lead to Better Results
Another common misconception is that specifying tighter tolerances for PCB fabrication will always result in better quality and performance. While tighter tolerances can indeed improve the precision of your PCB, they also come with increased manufacturing costs and potential delays.
Tolerance | Impact on Cost | Impact on Manufacturability |
---|---|---|
Loose | Low | High |
Moderate | Medium | Medium |
Tight | High | Low |
Before specifying tight tolerances, consider whether they are truly necessary for your design. In many cases, standard tolerances are sufficient to meet the requirements of your application. By avoiding unnecessarily tight tolerances, you can reduce costs and improve the manufacturability of your PCB.
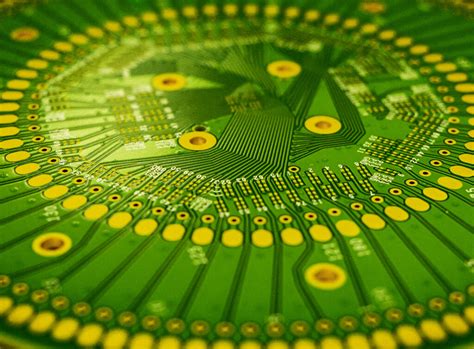
Misconception 3: Autorouting is Always the Best Option
Autorouting is a feature offered by many PCB design software packages that automatically routes traces between components on your PCB. While autorouting can be a useful tool for quickly generating Routing Solutions, it is not always the best option for optimizing your PCB layout.
Autorouting algorithms often prioritize shortest path connections, which may not always result in the most efficient or reliable routing. Manual routing, on the other hand, allows you to consider factors such as signal integrity, EMI reduction, and manufacturability when placing traces.
Routing Method | Advantages | Disadvantages |
---|---|---|
Autorouting | Fast, automated process | May not optimize for signal integrity or EMI |
Manual Routing | Full control over trace placement, optimized for specific requirements | Time-consuming, requires expertise |
In practice, a combination of autorouting and manual routing often yields the best results. By using autorouting as a starting point and then manually optimizing critical traces, you can achieve a balance between efficiency and performance.
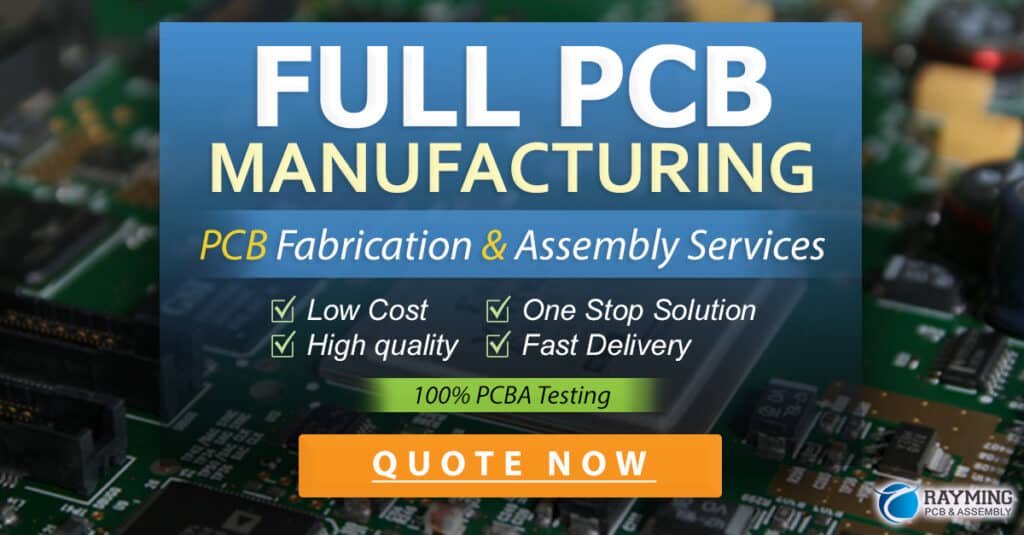
Misconception 4: Via-in-Pad is Always Bad
Via-in-pad (VIP) is a design technique where vias are placed directly on component pads, as opposed to being placed adjacent to the pads. Some designers believe that VIP should always be avoided due to concerns about manufacturing reliability and solder joint integrity.
However, modern PCB fabrication and assembly processes have made VIP a viable option in many cases. VIP can offer several advantages, such as:
- Reduced PCB size by eliminating the need for additional space around pads for vias
- Improved signal integrity by minimizing trace lengths
- Enhanced thermal dissipation for high-power components
Via Placement | Advantages | Disadvantages |
---|---|---|
Via-in-Pad | Reduced PCB size, improved signal integrity, enhanced thermal dissipation | Potential manufacturing and reliability concerns |
Via-Adjacent-to-Pad | Proven reliability, easier to manufacture | Increased PCB size, longer trace lengths |
When considering VIP, it is essential to consult with your PCB manufacturer to ensure that their processes are compatible with this technique. By carefully evaluating the benefits and risks of VIP, you can determine whether it is appropriate for your specific design.
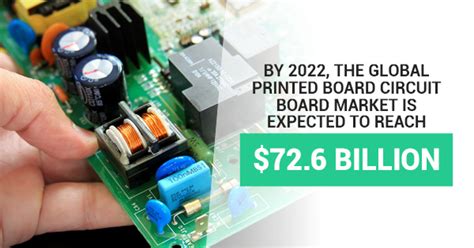
Misconception 5: Copper Pour is Just for Aesthetics
Copper pour, also known as a ground plane or power plane, is a large area of copper on a PCB layer that is typically connected to ground or a power supply. Some designers believe that copper pour is primarily used for aesthetic purposes, making the PCB look more professional or finished.
However, copper pour serves several important functions beyond aesthetics:
- Provides a low-impedance return path for high-frequency signals
- Reduces EMI by minimizing loop areas
- Improves thermal dissipation by increasing the overall copper area
- Enhances PCB mechanical stability
Copper Pour Usage | Advantages | Disadvantages |
---|---|---|
Full Coverage | Maximum EMI reduction, best thermal dissipation, improved mechanical stability | Increased PCB weight, higher manufacturing cost |
Strategic Placement | Targeted EMI reduction, improved signal integrity, lower cost compared to full coverage | Less overall EMI reduction and thermal dissipation compared to full coverage |
When incorporating copper pour into your PCB design, consider the specific requirements of your application. Full coverage copper pour may be necessary for designs with stringent EMI or thermal requirements, while strategic placement of copper pour can provide a balance between performance and cost for less demanding applications.
Misconception 6: Solder Mask Color is Purely Cosmetic
Solder mask is a protective coating applied to the copper traces on a PCB, leaving only the pads exposed for soldering. While solder mask color is often chosen for aesthetic reasons, it can also have functional implications.
Solder Mask Color | Advantages | Disadvantages |
---|---|---|
Green | Widely available, low cost, good contrast with copper traces | May not meet specific aesthetic requirements |
Black | Visually appealing, high contrast with copper traces, can improve thermal dissipation | Higher cost compared to green, may require additional processing steps |
White | Visually striking, can improve LED light reflection | Higher cost, may show dirt or scratches more easily |
Other Colors | Can meet specific aesthetic requirements or branding needs | Higher cost, limited availability, may require custom manufacturing |
When selecting a solder mask color, consider factors such as cost, availability, and the specific requirements of your application. For example, black solder mask may be preferable for designs with high thermal dissipation requirements, while white solder mask can enhance the performance of LED lighting applications.
Misconception 7: PCB Design Software is Too Expensive
Many designers believe that PCB design software is prohibitively expensive, leading them to rely on less capable or outdated tools. However, there are now a wide range of PCB design software options available at various price points, including free and open-source alternatives.
PCB Design Software | Advantages | Disadvantages |
---|---|---|
Commercial (e.g., Altium, Cadence) | Comprehensive feature set, extensive libraries, professional support | High cost, steep learning curve |
Free/Open-Source (e.g., KiCad, EasyEDA) | No cost, active community support, growing feature set | Limited libraries compared to commercial options, may lack advanced features |
When choosing PCB design software, consider your specific needs and budget. For many applications, free and open-source options such as KiCad or EasyEDA can provide sufficient functionality and community support. As your designs become more complex or your business grows, you may consider investing in commercial software for its advanced features and professional support.
Frequently Asked Questions (FAQ)
-
Q: How do I determine the appropriate number of layers for my PCB?
A: The number of layers in your PCB should be determined based on factors such as signal integrity requirements, routing density, EMI reduction needs, and cost constraints. Consult with your PCB manufacturer and carefully evaluate your design requirements to make an informed decision. -
Q: Can I use autorouting for my entire PCB design?
A: While autorouting can be a useful tool for quickly generating routing solutions, it is often best to use a combination of autorouting and manual routing. Autorouting can provide a good starting point, but manual optimization of critical traces is often necessary to ensure the best performance and manufacturability. -
Q: Is via-in-pad (VIP) a reliable design technique?
A: When properly implemented and supported by your PCB manufacturer, VIP can be a reliable and effective design technique. However, it is essential to consult with your manufacturer to ensure that their processes are compatible with VIP and to carefully evaluate the potential benefits and risks for your specific application. -
Q: What are the benefits of using copper pour in my PCB design?
A: Copper pour can provide several benefits, including reduced EMI, improved thermal dissipation, enhanced signal integrity, and increased mechanical stability of the PCB. The extent and placement of copper pour should be determined based on the specific requirements of your application. -
Q: How do I choose the right solder mask color for my PCB?
A: Solder mask color can be chosen based on aesthetic preferences, but it can also have functional implications. Consider factors such as cost, availability, contrast with copper traces, and specific application requirements (e.g., thermal dissipation, LED light reflection) when selecting a solder mask color.
By understanding and addressing these common PCB misconceptions, designers can make informed decisions that lead to more efficient, reliable, and cost-effective PCB designs. As with any aspect of electronic product development, careful consideration of design requirements, manufacturing capabilities, and industry best practices is essential for success.
No responses yet