Introduction
Printed Circuit Board (PCB) design is a complex process that requires careful consideration of various factors, including component placement, routing, and manufacturability. As electronic devices become more compact and feature-rich, PCB designers face the challenge of accommodating an increasing number of components within limited board space. This article explores the importance of creative routing solutions and tight component placement in optimized PCB design, highlighting techniques and best practices to achieve efficient and reliable designs.
The Importance of Tight Component Placement
Tight component placement is crucial in modern PCB design for several reasons:
- Space optimization: By placing components closely together, designers can minimize the overall board size, resulting in more compact and lightweight devices.
- Reduced signal interference: Shorter trace lengths between components lead to reduced electromagnetic interference (EMI) and improved signal integrity.
- Enhanced thermal management: Tight component placement allows for better heat dissipation, as components can share heat sinks and benefit from improved airflow.
Factors to Consider in Component Placement
When placing components on a PCB, designers must take into account various factors:
Factor | Description |
---|---|
Component size | The physical dimensions of components dictate the available space for placement. |
Pin compatibility | Components with similar pin configurations should be placed close together for easier routing. |
Signal integrity | Critical components should be placed near their associated circuits to minimize trace lengths. |
Thermal considerations | Heat-generating components should be placed in areas with adequate cooling. |
Manufacturing constraints | Component placement must adhere to manufacturing guidelines for assembly and soldering. |
Best Practices for Tight Component Placement
To achieve optimal component placement, designers should follow these best practices:
- Group related components: Place components that belong to the same functional block or circuit close together to minimize trace lengths and improve signal integrity.
- Consider component orientation: Orient components in a way that facilitates efficient routing and minimizes the number of vias required.
- Use component libraries: Utilize component libraries with accurate footprint information to ensure precise placement and avoid spacing issues.
- Collaborate with manufacturing: Consult with the manufacturing team to ensure that component placement adheres to their guidelines and constraints.
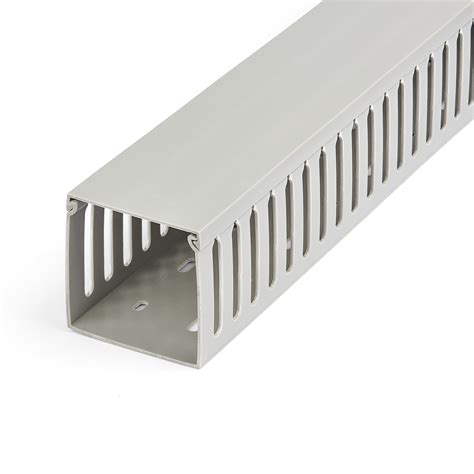
Creative Routing Solutions
Efficient routing is essential for achieving reliable and high-performance PCB designs. Creative routing solutions help designers navigate the challenges posed by tight component placement and complex circuitry.
Routing Techniques
Technique | Description |
---|---|
Orthogonal routing | Routes traces in horizontal and vertical directions, minimizing diagonal traces. |
Curved traces | Uses curved traces to avoid obstacles and create more efficient paths. |
Differential pairs | Routes two traces in parallel to maintain a constant spacing for differential signals. |
Via stitching | Places vias along a trace to minimize inductance and improve signal integrity. |
Length matching | Ensures that traces within a group have equal lengths to maintain signal synchronization. |
Routing Best Practices
To achieve optimal routing results, designers should adhere to the following best practices:
- Minimize trace lengths: Shorter traces reduce signal attenuation, EMI, and propagation delays.
- Avoid sharp angles: Use 45-degree angles or curved traces instead of 90-degree angles to reduce signal reflections and EMI.
- Maintain consistent trace width: Keep trace widths consistent throughout the design to ensure uniform impedance and minimize signal distortion.
- Use ground planes: Incorporate ground planes to provide a low-impedance return path for signals and reduce EMI.
- Avoid routing over split planes: Routing traces over split planes can cause signal integrity issues and should be avoided whenever possible.
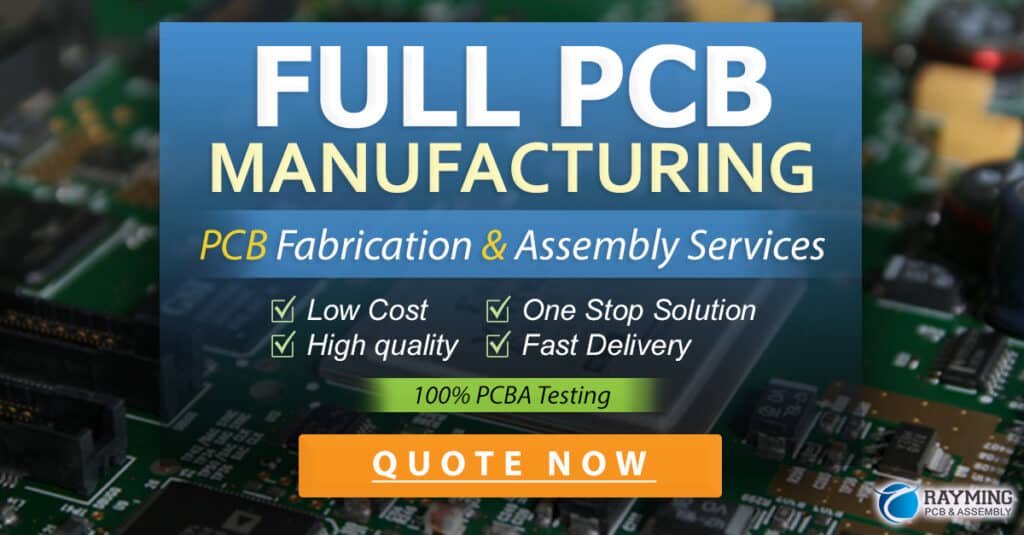
Advanced Routing Techniques
In addition to basic routing techniques, designers can employ advanced methods to further optimize their PCB designs.
Multi-Layer Routing
Multi-layer PCBs offer several advantages over single-layer boards:
- Increased routing density: Additional layers provide more space for routing traces, allowing for tighter component placement and more complex circuitry.
- Improved signal integrity: Dedicated signal and ground layers help minimize crosstalk and EMI, resulting in better signal quality.
- Enhanced thermal management: Multi-layer PCBs can dissipate heat more effectively by incorporating thermal vias and dedicated copper layers for heat spreading.
High-Speed Routing Considerations
When routing high-speed signals, designers must take extra precautions to ensure signal integrity:
- Impedance matching: Ensure that the characteristic impedance of the traces matches the impedance of the source and load to minimize reflections.
- Length matching: Match the lengths of traces within a group to maintain signal synchronization and minimize timing skew.
- Differential pair routing: Use differential pair routing techniques to maintain a constant spacing between the positive and negative traces of a differential signal.
- Crosstalk mitigation: Minimize crosstalk by increasing the spacing between adjacent traces and using guard traces or ground planes to shield sensitive signals.
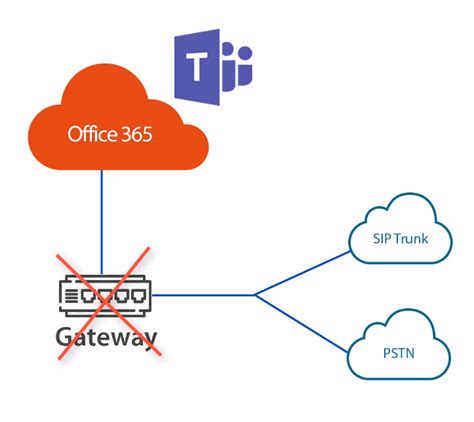
Design for Manufacturing (DFM)
To ensure that a PCB design can be successfully manufactured, designers must consider DFM guidelines throughout the design process.
DFM Guidelines for Component Placement
Guideline | Description |
---|---|
Component spacing | Maintain adequate spacing between components to allow for proper soldering and inspection. |
Component orientation | Orient components in a way that facilitates automated assembly and minimizes manual intervention. |
Soldering accessibility | Ensure that component pads are accessible for soldering and rework. |
Panelization | Consider panelization requirements when placing components near the board edges. |
DFM Guidelines for Routing
Guideline | Description |
---|---|
Trace width and spacing | Adhere to the manufacturer’s minimum trace width and spacing requirements. |
Via size and spacing | Ensure that via sizes and spacing comply with the manufacturer’s guidelines. |
Copper pour clearance | Maintain adequate clearance between copper pour and traces to avoid short circuits. |
Solder mask and silkscreen | Follow the manufacturer’s guidelines for solder mask and silkscreen placement and sizing. |
Case Studies
Case Study 1: Smartwatch PCB Design
In this case study, a smartwatch PCB was designed using tight component placement and creative routing solutions. The main challenges included accommodating a large number of components within a small form factor and ensuring reliable high-speed communication between the processor and sensors.
The design team employed the following techniques:
- Multi-layer PCB: A 6-layer PCB was used to provide adequate routing space and dedicated signal and ground layers.
- Tight component placement: Components were grouped based on their function and placed in close proximity to minimize trace lengths.
- High-speed routing: Differential pair routing and length matching were used for high-speed signals, such as USB and MIPI interfaces.
- DFM considerations: The design adhered to the manufacturer’s guidelines for component spacing, trace width, and via size to ensure manufacturability.
The resulting design achieved a compact form factor, reliable high-speed communication, and successful manufacturing, demonstrating the effectiveness of tight component placement and creative routing solutions.
Case Study 2: Automotive ECU Design
In this case study, an automotive electronic control unit (ECU) was designed using advanced routing techniques and DFM considerations. The main challenges included managing a large number of I/O signals, ensuring reliable operation in harsh environments, and meeting strict automotive quality standards.
The design team employed the following techniques:
- Multi-layer PCB: A 10-layer PCB was used to accommodate the large number of signals and provide dedicated power and ground layers.
- Impedance-controlled routing: Traces were designed with controlled impedance to ensure signal integrity and minimize reflections.
- Crosstalk mitigation: Guard traces and ground planes were used to shield sensitive signals and minimize crosstalk.
- DFM considerations: The design adhered to automotive-grade manufacturing guidelines, including increased component spacing, wider traces, and more stringent soldering requirements.
The resulting ECU design achieved reliable operation in harsh automotive environments, met all quality standards, and demonstrated the importance of advanced routing techniques and DFM considerations in complex PCB designs.
Frequently Asked Questions (FAQ)
- What is the importance of tight component placement in PCB design?
-
Tight component placement helps optimize board space, reduce signal interference, and enhance thermal management, resulting in more compact and reliable PCB designs.
-
What are some creative routing solutions for PCB design?
-
Creative routing solutions include orthogonal routing, curved traces, differential pair routing, via stitching, and length matching. These techniques help designers navigate the challenges posed by tight component placement and complex circuitry.
-
How can multi-layer PCBs benefit routing and component placement?
-
Multi-layer PCBs offer increased routing density, improved signal integrity, and enhanced thermal management by providing additional layers for routing, dedicated signal and ground layers, and thermal dissipation through vias and copper layers.
-
What are some important DFM considerations for component placement and routing?
-
DFM considerations for component placement include maintaining adequate spacing, orienting components for automated assembly, ensuring soldering accessibility, and considering panelization requirements. For routing, designers must adhere to manufacturer guidelines for trace width and spacing, via size and spacing, copper pour clearance, and solder mask and silkscreen placement.
-
How can designers ensure signal integrity in high-speed PCB designs?
- To ensure signal integrity in high-speed PCB designs, designers should use techniques such as impedance matching, length matching, differential pair routing, and crosstalk mitigation. These techniques help minimize signal reflections, maintain synchronization, and reduce electromagnetic interference.
Conclusion
Creative routing solutions and tight component placement are essential aspects of optimized PCB design. By employing techniques such as multi-layer routing, high-speed signal management, and DFM considerations, designers can create compact, reliable, and high-performance PCBs that meet the demands of modern electronic devices. As technology continues to advance, the importance of these design strategies will only continue to grow, making it crucial for PCB designers to stay up-to-date with the latest techniques and best practices in the field.
No responses yet