Introduction to 3D-Printed PCBs
3D printing technology has revolutionized the way we manufacture products across various industries. From medical devices to automotive parts, 3D printing has enabled faster prototyping, customization, and cost-effective production. In recent years, this technology has also found its way into the electronics industry, specifically in the production of printed circuit boards (PCBs).
A 3D-printed PCB is a circuit board that is manufactured using additive manufacturing techniques, as opposed to traditional subtractive methods. This innovative approach to PCB fabrication offers several advantages, including faster turnaround times, increased design flexibility, and reduced waste.
How 3D Printing Technology Works in PCB Fabrication
The process of 3D printing a PCB involves several steps:
-
Design: The PCB Design is created using computer-aided design (CAD) software, which generates a 3D model of the board.
-
Slicing: The 3D model is then “sliced” into thin layers using specialized software, which generates instructions for the 3D printer.
-
Printing: The 3D printer follows these instructions, depositing conductive and insulating materials layer by layer to build the PCB.
-
Post-processing: After printing, the PCB undergoes post-processing steps, such as curing, cleaning, and finishing, to ensure its functionality and durability.
Several 3D printing technologies can be used for PCB fabrication, including:
- Fused Deposition Modeling (FDM)
- Stereolithography (SLA)
- Selective Laser Sintering (SLS)
- Inkjet Printing
Each technology has its advantages and limitations, and the choice depends on factors such as the required resolution, materials, and production volume.
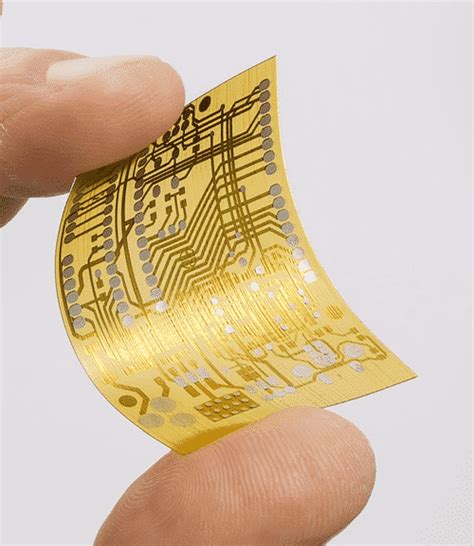
Advantages of 3D-Printed PCBs
3D-printed PCBs offer several benefits over traditionally manufactured boards:
Faster Prototyping and Iteration
With 3D printing, PCB Prototypes can be produced in a matter of hours, as opposed to days or weeks with traditional methods. This allows for faster iteration and testing, reducing the time to market for new products.
Increased Design Flexibility
3D printing enables the creation of complex geometries and unconventional board shapes that would be difficult or impossible to achieve with traditional manufacturing methods. This allows for greater design flexibility and customization.
Reduced Waste and Environmental Impact
Traditional PCB manufacturing involves subtractive processes, such as etching and drilling, which generate waste in the form of chemicals and materials. 3D printing, being an additive process, produces less waste and has a lower environmental impact.
Cost-Effective for Low-Volume Production
For low-volume production runs or prototyping, 3D printing can be more cost-effective than traditional manufacturing methods, as it eliminates the need for expensive tooling and setup costs.
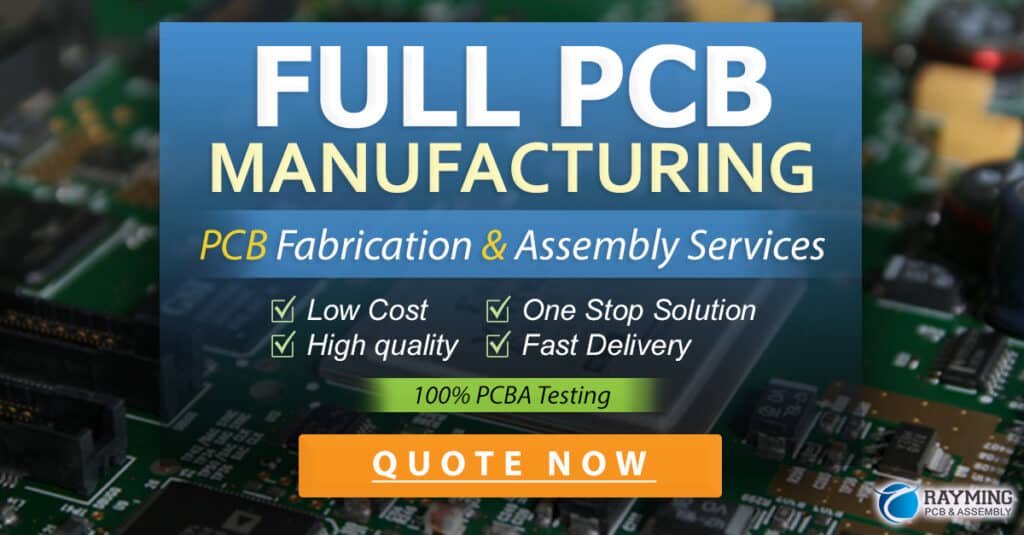
Challenges and Limitations of 3D-Printed PCBs
Despite their advantages, 3D-printed PCBs also face some challenges and limitations:
Material Properties and Conductivity
The conductive materials used in 3D-printed PCBs, such as conductive filaments or inks, may not have the same electrical properties as traditional copper traces. This can impact the performance and reliability of the board.
Resolution and Feature Size
The resolution and minimum feature size achievable with 3D printing technologies are generally lower than those of traditional PCB manufacturing methods. This can limit the complexity and density of the circuits that can be printed.
Scalability and Production Volume
While 3D printing is well-suited for prototyping and low-volume production, it may not be as cost-effective or efficient for high-volume production compared to traditional manufacturing methods.
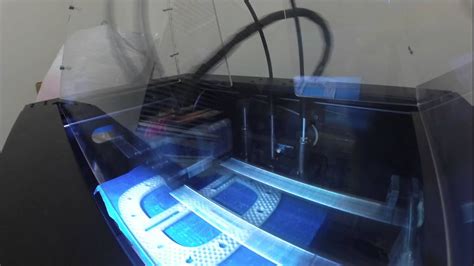
Applications of 3D-Printed PCBs
Despite these challenges, 3D-printed PCBs have found applications in various fields:
Rapid Prototyping and Proof-of-Concept
3D-printed PCBs are ideal for quickly validating designs and creating functional prototypes, allowing for faster iteration and testing.
Customized and Low-Volume Electronics
For applications that require customized or low-volume PCBs, such as in medical devices or specialized industrial equipment, 3D printing offers a cost-effective solution.
Aerospace and Defense
The aerospace and defense industries have shown interest in 3D-printed PCBs for their ability to create lightweight, complex, and customized electronic components.
Education and Research
3D-printed PCBs are also being used in educational and research settings, allowing students and researchers to quickly prototype and test their designs without the need for expensive equipment or long lead times.
Future Outlook and Developments
As 3D printing technology continues to advance, we can expect to see further improvements in the resolution, materials, and production capabilities of 3D-printed PCBs. Some of the key developments to watch for include:
Improved Conductive Materials
Researchers are working on developing new conductive materials with better electrical properties and compatibility with 3D printing processes. This could lead to higher-performance 3D-printed PCBs.
Multi-Material Printing
Advancements in multi-material 3D printing could allow for the simultaneous printing of conductive and insulating materials, enabling the creation of more complex and integrated PCBs.
Hybrid Manufacturing Approaches
Combining 3D printing with traditional PCB manufacturing methods, such as using 3D-printed substrates with conventionally applied copper traces, could offer the benefits of both technologies.
Frequently Asked Questions (FAQ)
-
Q: Are 3D-printed PCBs as reliable as traditionally manufactured boards?
A: While 3D-printed PCBs have shown promise in various applications, their reliability and performance may not yet match that of traditionally manufactured boards. However, ongoing research and development are aimed at improving the materials and processes used in 3D-printed PCBs to enhance their reliability. -
Q: Can 3D-printed PCBs be used for high-frequency applications?
A: Currently, 3D-printed PCBs may not be suitable for high-frequency applications due to the limitations in the electrical properties of the conductive materials used. However, as new materials and printing technologies are developed, this may change in the future. -
Q: What is the minimum feature size achievable with 3D-printed PCBs?
A: The minimum feature size achievable with 3D-printed PCBs depends on the specific printing technology used. For example, FDM printers typically have a minimum feature size of around 100 microns, while inkjet printing can achieve feature sizes down to 50 microns or less. -
Q: Are there any specific design considerations for 3D-printed PCBs?
A: Yes, when designing PCBs for 3D printing, it’s important to consider factors such as the minimum feature size, material properties, and post-processing requirements. Designers may need to adjust their designs to accommodate the capabilities and limitations of the chosen 3D printing technology. -
Q: How do the costs of 3D-printed PCBs compare to traditionally manufactured boards?
A: For low-volume production or prototyping, 3D-printed PCBs can be more cost-effective than traditional manufacturing methods, as they eliminate the need for expensive tooling and setup costs. However, for high-volume production, traditional manufacturing methods are likely to be more cost-effective due to economies of scale.
Conclusion
3D-printed PCBs represent an exciting development in the world of electronics manufacturing, offering benefits such as faster prototyping, increased design flexibility, and reduced waste. While there are still challenges to overcome, such as material properties and scalability, ongoing research and development in this field are poised to address these issues and expand the applications of 3D-printed PCBs.
As 3D printing technology continues to evolve, we can expect to see more widespread adoption of 3D-printed PCBs across various industries, from aerospace and defense to medical devices and consumer electronics. This innovative approach to PCB fabrication has the potential to transform the way we design, prototype, and manufacture electronic devices, ushering in a new era of customization, efficiency, and sustainability in the electronics industry.
Aspect | Traditional PCBs | 3D-Printed PCBs |
---|---|---|
Prototyping Speed | Days to weeks | Hours |
Design Flexibility | Limited by manufacturing constraints | High, enabling complex geometries |
Waste Generation | High, due to subtractive processes | Low, as an additive process |
Cost-Effectiveness (Low Volume) | Low, due to tooling and setup costs | High, no tooling required |
Cost-Effectiveness (High Volume) | High, due to economies of scale | Low, not suitable for mass production |
Material Properties | Well-established, high-performance | Limited, ongoing research for improvement |
Minimum Feature Size | Can achieve very fine features | Limited by printing technology |
No responses yet