1. Choose the Right PCB Material
Selecting the appropriate PCB material is crucial for your project’s success. The most common PCB materials are:
Material | Description | Applications |
---|---|---|
FR-4 | Glass-reinforced epoxy laminate | General-purpose, Low-Cost PCBs |
High-Tg FR-4 | Improved thermal stability and performance | High-temperature applications |
Rogers | Low-loss, high-frequency materials | RF and microwave applications |
Flex | Flexible polyimide or polyester film | Wearables, compact devices |
Aluminum | Metal-core PCBs for better heat dissipation | High-power LEDs, automotive |
Consider your project’s requirements, such as operating temperature, frequency, and flexibility, when choosing the PCB material.
2. Determine the Appropriate Layer Stack-up
The layer stack-up of your PCB can significantly impact its performance and manufacturability. When deciding on the layer stack-up, consider the following:
- Signal integrity requirements
- Power distribution needs
- EMI/EMC considerations
- Manufacturing constraints
A typical 4-Layer PCB stack-up might look like this:
Layer | Description |
---|---|
Top | Signal layer, components |
Inner 1 | Ground plane |
Inner 2 | Power plane |
Bottom | Signal layer, components |
Consult with your PCB manufacturer to determine the optimal layer stack-up for your project.
3. Follow Proper Trace Width and Spacing Guidelines
Trace width and spacing play a critical role in signal integrity and manufacturability. Consider the following guidelines:
- Use appropriate trace widths based on the current carrying requirements
- Maintain adequate spacing between traces to minimize crosstalk and EMI
- Follow your PCB manufacturer’s minimum trace width and spacing rules
Here’s a table with typical trace width and spacing values for different signal types:
Signal Type | Trace Width (mil) | Trace Spacing (mil) |
---|---|---|
Digital | 5-10 | 5-10 |
Analog | 10-20 | 10-20 |
Power | 20-50 | 20-50 |
High-speed | 5-8 | 8-12 |
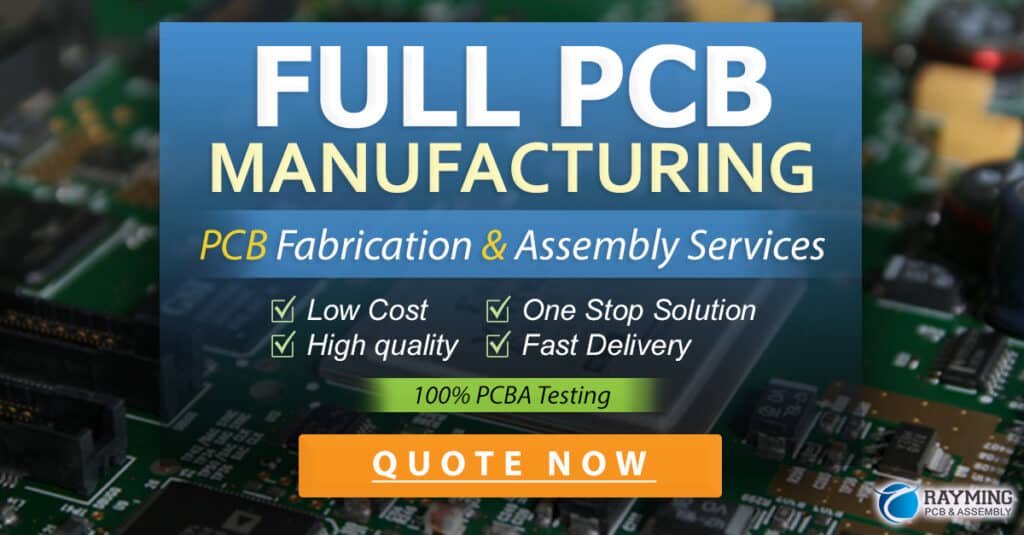
4. Implement Proper Grounding Techniques
Proper grounding is essential for minimizing noise, ensuring signal integrity, and preventing EMI/EMC issues. Follow these grounding tips:
- Use ground planes for low-impedance return paths
- Separate analog and digital grounds to minimize noise coupling
- Use star grounding for sensitive analog circuits
- Implement ground pours on signal layers to reduce impedance and provide shielding
5. Optimize Component Placement
Component placement is crucial for signal integrity, manufacturability, and thermal management. Consider the following tips:
- Place components to minimize trace lengths and crossing
- Group related components together to simplify routing and improve signal integrity
- Orient components for easy soldering and inspection
- Consider thermal requirements and provide adequate spacing for heat dissipation
6. Route High-Speed Signals with Care
High-speed signals require special attention to maintain signal integrity and minimize EMI. Follow these guidelines:
- Keep high-speed traces as short as possible
- Use controlled impedance techniques for critical high-speed traces
- Avoid sharp bends and use smooth curves for high-speed traces
- Provide adequate spacing between high-speed traces and other signals
7. Manage Power Distribution
Proper power distribution is essential for minimizing noise, ensuring voltage regulation, and preventing power-related issues. Consider the following tips:
- Use separate power planes for different voltage levels
- Implement proper decoupling capacitors near power pins of ICs
- Use wide traces or planes for power distribution to minimize inductance and resistance
- Consider using power integrity simulation tools to optimize power distribution
8. Implement Design for Manufacturing (DFM) Guidelines
Designing your PCB with manufacturability in mind can help reduce costs, improve yields, and accelerate time-to-market. Follow these DFM guidelines:
- Adhere to your PCB manufacturer’s minimum feature sizes and clearances
- Avoid using non-standard hole sizes and pad dimensions
- Provide adequate clearance around the board edges for panelization
- Use standardized component footprints and avoid custom packages when possible
9. Consider Testability and Assembly Requirements
Designing your PCB with testability and assembly in mind can help streamline the manufacturing process and improve quality. Consider the following tips:
- Provide test points for critical signals and power rails
- Use components with standard pitch and package sizes for easy assembly
- Provide clear silkscreen markings for component orientation and reference designators
- Consider using boundary scan or other testability features for complex designs
10. Conduct Signal and Power Integrity Simulations
Signal and power integrity simulations can help identify potential issues early in the design process, allowing you to make necessary adjustments before fabrication. Consider the following simulation techniques:
- Use SPICE or other Circuit Simulation tools to analyze critical signal paths
- Perform power integrity simulations to ensure proper voltage regulation and minimize noise
- Conduct electromagnetic simulations to assess EMI/EMC performance
- Use 3D electromagnetic solvers for high-frequency and complex structures
11. Perform Design Reviews and Collaborate with Stakeholders
Design reviews and collaboration with stakeholders can help catch potential issues and ensure that your PCB meets all requirements. Follow these tips:
- Conduct regular design reviews with your team and stakeholders
- Collaborate with your PCB manufacturer to ensure design manufacturability
- Engage with component suppliers to select the best parts for your design
- Seek feedback from assembly and test teams to optimize your design for their processes
12. Stay Up-to-Date with Industry Standards and Best Practices
PCB Design is a constantly evolving field, with new technologies, materials, and techniques emerging regularly. To ensure that your designs remain competitive and compliant, stay up-to-date with industry standards and best practices:
- Follow IPC Standards for PCB design, fabrication, and assembly
- Attend industry conferences and workshops to learn about new technologies and techniques
- Participate in online forums and communities to share knowledge and learn from others
- Continuously update your skills and knowledge through training and education
Frequently Asked Questions (FAQ)
-
What is the difference between a 2-layer and a 4-layer PCB?
A 2-layer PCB has conductive copper layers on the top and bottom surfaces of the board, while a 4-layer PCB has two additional internal copper layers. 4-layer PCBs offer better signal integrity, power distribution, and EMI performance compared to 2-layer PCBs, but they are more expensive to manufacture. -
What is controlled impedance, and when is it necessary?
Controlled impedance is a technique used to maintain a consistent characteristic impedance along a transmission line, such as a high-speed signal trace. It is necessary when dealing with high-frequency signals, long trace lengths, or sensitive circuits to minimize reflections, crosstalk, and signal distortion. Controlled impedance is achieved by carefully designing the trace width, thickness, and spacing relative to the reference plane. -
What are the most common PCB Surface Finishes, and how do they differ?
The most common PCB surface finishes are: - HASL (Hot Air Solder Leveling): Inexpensive, good solderability, but not suitable for fine-pitch components
- ENIG (Electroless Nickel Immersion Gold): Flat surface, good solderability, and shelf life, but more expensive
- OSP (Organic Solderability Preservative): Inexpensive, flat surface, but limited shelf life
-
Immersion Silver: Flat surface, good solderability, and lower cost than ENIG, but can tarnish over time
-
What is the purpose of a solder mask on a PCB?
A solder mask is a protective layer applied to the copper traces on a PCB, leaving only the exposed pads for component soldering. The primary purposes of a solder mask are: - Preventing solder bridges and short circuits during assembly
- Protecting the copper traces from oxidation and contamination
- Providing electrical insulation between adjacent traces
-
Improving the PCB’s aesthetic appearance
-
What are some common PCB design software packages?
Some popular PCB design software packages include: - Altium Designer
- KiCad
- Eagle
- OrCAD
- Mentor Graphics PADS
- Cadence Allegro
These software packages offer schematic capture, layout design, and various simulation and analysis tools to help you create high-quality PCB designs.
By following these 12 essential PCB design rules and tips, you can create reliable, high-performance PCBs that meet your project’s requirements. Remember to collaborate with your team, stay up-to-date with industry standards, and continuously refine your designs based on feedback and experience. Happy PCB designing!
No responses yet