Introduction to 4-Layer PCBs
A 4-layer PCB, as the name suggests, is a printed circuit board that consists of four conductive layers. These layers are typically made of copper and are separated by insulating material. The four layers are arranged in a specific order: the top layer, the ground plane, the power plane, and the bottom layer. This arrangement allows for more complex circuit designs and improved signal integrity compared to simpler 2-layer PCBs.
Advantages of 4-Layer PCBs
- Increased routing space
- Better signal integrity
- Improved power distribution
- Enhanced electromagnetic interference (EMI) shielding
Understanding the Layer Stack-up
The layer stack-up of a 4-layer PCB is crucial to its performance. A typical stack-up consists of the following layers:
- Top Layer (Signal Layer 1)
- Ground Plane
- Power Plane
- Bottom Layer (Signal Layer 2)
The top and bottom layers are used for signal routing, while the inner layers (ground and power planes) provide a stable reference for the signals and distribute power to the components.
Signal Layers
The top and bottom layers of a 4-layer PCB are used for signal routing. These layers contain the traces that connect the components on the board. The signal layers are typically thinner than the inner layers to allow for finer trace widths and spacing, which is essential for high-density designs.
Ground Plane
The ground plane is an inner layer that provides a low-impedance return path for the signals. It helps to reduce electromagnetic interference (EMI) and improves signal integrity by minimizing the loop area between the signal traces and the ground.
Power Plane
The power plane is another inner layer that distributes power to the components on the board. It provides a low-impedance path for the power supply and helps to reduce voltage drops across the board. The power plane also acts as a shield between the signal layers, further reducing EMI.
Designing 4-Layer PCBs
Designing a 4-layer PCB requires careful consideration of several factors, including component placement, signal routing, and power distribution.
Component Placement
Component placement is a critical aspect of 4-layer PCB design. The components should be placed in a way that minimizes the length of the signal traces and reduces the risk of signal integrity issues. It is also essential to consider the thermal requirements of the components and ensure adequate cooling.
Signal Routing
Signal routing on a 4-layer PCB is more complex than on a 2-layer board due to the presence of the inner layers. The signal traces should be routed in a way that minimizes crosstalk and signal reflections. This can be achieved by following good design practices, such as keeping the traces as short as possible, avoiding sharp bends, and maintaining appropriate spacing between traces.
Power Distribution
Power distribution on a 4-layer PCB is simplified by the presence of the power plane. The power plane should be designed to provide a low-impedance path for the power supply and minimize voltage drops across the board. It is important to consider the current requirements of the components and ensure that the power plane has sufficient copper coverage to handle the current.
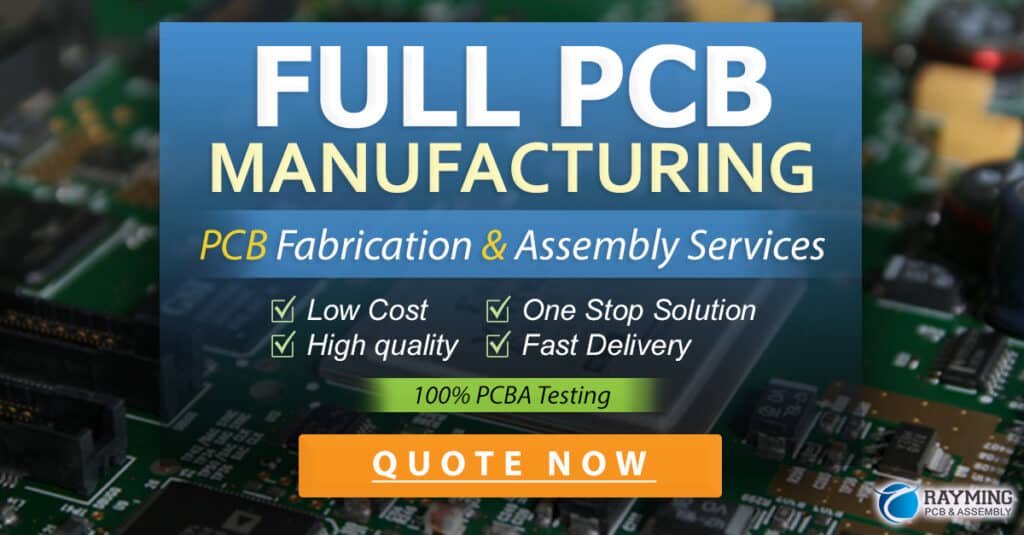
Manufacturing 4-Layer PCBs
Manufacturing a 4-layer PCB involves several steps, including:
- Creating the layer stack-up
- Generating the Gerber files
- Fabricating the PCB
- Assembling the components
Layer Stack-up Creation
The layer stack-up is created based on the design requirements and the desired electrical properties of the board. The stack-up specifies the thickness and material of each layer, as well as the spacing between layers.
Gerber File Generation
Gerber files are the industry standard for PCB fabrication. They contain all the necessary information for manufacturing the board, including the layer images, drill files, and aperture lists. The Gerber files are generated from the PCB design software and sent to the PCB manufacturer.
PCB Fabrication
The PCB fabrication process involves several steps, including:
- Copper Cladding
- Dry film lamination
- Exposure and development
- Etching
- Solder mask application
- Silk screen printing
The fabrication process is highly automated and can produce high-quality 4-layer PCBs with tight tolerances.
Component Assembly
After the PCB is fabricated, the components are assembled onto the board. This can be done manually or using automated assembly equipment. The components are soldered onto the board using either through-hole or surface-mount technology (SMT).
Testing and Inspection
Once the 4-layer PCB is assembled, it undergoes a series of tests and inspections to ensure that it meets the design specifications and functions as intended.
Electrical Testing
Electrical testing is performed to verify that the board meets the specified electrical parameters, such as voltage, current, and resistance. This can be done using automated test equipment (ATE) or manual testing methods.
Visual Inspection
Visual inspection is performed to check for any visible defects, such as solder bridges, missing components, or damaged traces. This can be done using automated optical inspection (AOI) equipment or manual inspection methods.
Functional Testing
Functional testing is performed to verify that the board performs as intended in its intended application. This can involve testing the board in its final product or using specialized test fixtures to simulate the intended environment.
Applications of 4-Layer PCBs
4-layer PCBs are used in a wide range of applications, including:
- Telecommunications equipment
- Medical devices
- Automotive electronics
- Industrial control systems
- Consumer electronics
The increased routing space and improved signal integrity of 4-layer PCBs make them ideal for high-speed digital circuits and complex analog designs.
Frequently Asked Questions (FAQ)
1. What is the difference between a 2-layer and a 4-layer PCB?
A 2-layer PCB consists of two conductive layers (top and bottom) separated by an insulating material, while a 4-layer PCB has four conductive layers (top, ground plane, power plane, and bottom) separated by insulating material. 4-layer PCBs offer more routing space, better signal integrity, and improved power distribution compared to 2-layer PCBs.
2. When should I use a 4-layer PCB instead of a 2-layer PCB?
You should consider using a 4-layer PCB when your design requires:
- High component density
- High-speed digital circuits
- Complex analog circuits
- Improved signal integrity
- Better power distribution
- Enhanced EMI shielding
3. How much does a 4-layer PCB cost compared to a 2-layer PCB?
The cost of a 4-layer PCB is typically higher than that of a 2-layer PCB due to the additional materials and processing steps involved in fabrication. However, the exact cost difference depends on factors such as board size, quantity, and design complexity.
4. Can I route signals on the inner layers of a 4-layer PCB?
Yes, you can route signals on the inner layers of a 4-layer PCB, but it is generally not recommended. The inner layers are typically used for power and ground planes to provide a stable reference for the signals and distribute power to the components. Routing signals on the inner layers can compromise the signal integrity and increase the risk of EMI.
5. What are the challenges in designing a 4-layer PCB?
Designing a 4-layer PCB presents several challenges, including:
- Achieving optimal component placement
- Ensuring proper signal routing and impedance control
- Maintaining adequate power distribution
- Minimizing EMI and crosstalk
- Ensuring manufacturability and testability
Overcoming these challenges requires careful planning, adherence to good design practices, and close collaboration with the PCB manufacturer.
Conclusion
4-layer PCBs offer numerous advantages over simpler 2-layer designs, including increased routing space, better signal integrity, improved power distribution, and enhanced EMI shielding. However, designing and manufacturing 4-layer PCBs requires careful consideration of several factors, such as component placement, signal routing, and power distribution.
By understanding the layer stack-up, design considerations, and manufacturing process of 4-layer PCBs, engineers and designers can create high-performance, reliable, and cost-effective electronic products for a wide range of applications.
Layer | Description | Thickness (mm) |
---|---|---|
Top Layer | Signal routing | 0.035 |
Ground Plane | Low-impedance return path | 0.035 |
Power Plane | Power distribution | 0.035 |
Bottom Layer | Signal routing | 0.035 |
Table 1: Typical layer stack-up for a 4-layer PCB
Application | Benefits of 4-Layer PCBs |
---|---|
Telecommunications | High-speed digital circuits, improved signal integrity |
Medical devices | Complex analog circuits, enhanced EMI shielding |
Automotive electronics | High component density, improved power distribution |
Industrial control systems | Improved signal integrity, better power distribution |
Consumer electronics | High component density, enhanced EMI shielding |
Table 2: Benefits of 4-layer PCBs in various applications
No responses yet