Introduction
Converting a schematic design to a printed circuit board (PCB) layout is a crucial step in the electronics design process. It involves translating the abstract representation of the circuit into a physical layout that can be manufactured. This process requires careful consideration of various factors to ensure the PCB functions as intended and meets all the necessary requirements. In this article, we will discuss ten essential tips to keep in mind when converting a schematic to a PCB layout.
Tip 1: Understand the Schematic
Before starting the PCB layout process, it is essential to thoroughly understand the schematic. Take the time to study the circuit diagram, identify the components, and comprehend how they are interconnected. Familiarize yourself with the symbols used and any specific requirements noted in the schematic. A clear understanding of the schematic will help you make informed decisions during the layout process.
Tip 2: Consider Component Placement
Component placement is a critical aspect of PCB layout. When placing components on the board, consider factors such as signal integrity, thermal management, and mechanical constraints. Group related components together to minimize signal path lengths and reduce interference. Pay attention to the orientation of components, especially those with polarity or directionality requirements. Proper component placement can significantly impact the performance and reliability of the PCB.
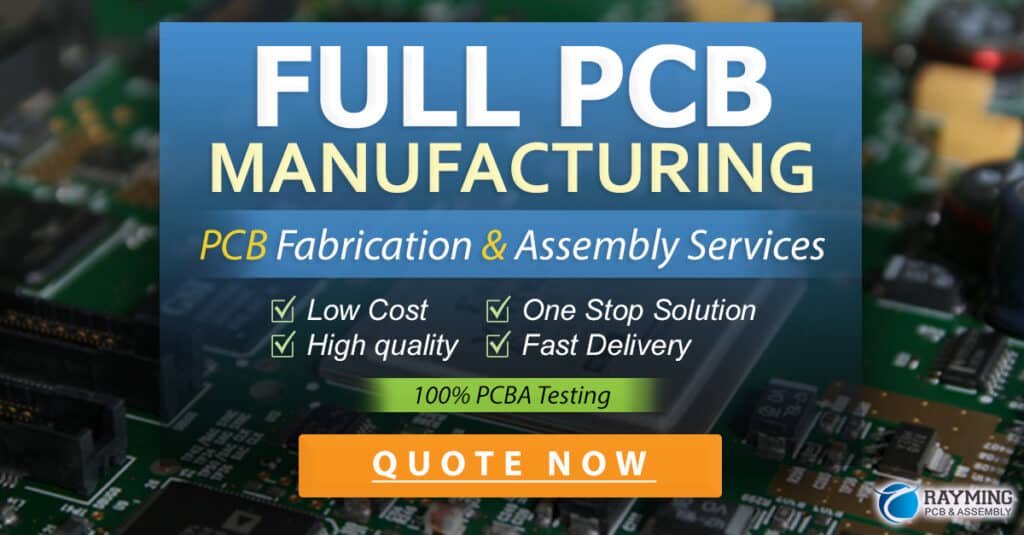
Tip 3: Optimize Signal Routing
Signal routing is the process of connecting components on the PCB through conductive traces. When routing signals, aim to minimize the length of traces to reduce signal loss and interference. Use appropriate trace widths based on the current carrying requirements and signal frequencies. Avoid sharp angles or unnecessary bends in the traces, as they can introduce signal reflections and degrade signal quality. Consider using ground planes and power planes to provide low-impedance paths for signals and reduce electromagnetic interference (EMI).
Tip 4: Implement Proper Grounding
Proper grounding is essential for the stability and performance of the PCB. Create a solid ground plane on one or more layers of the board to provide a low-impedance return path for signals. Connect all ground points to the ground plane using vias or through-hole connections. Avoid creating ground loops or isolated ground regions, as they can lead to noise and signal integrity issues. In high-speed designs, consider using a star ground topology to minimize ground bounce and ensure a stable reference voltage.
Tip 5: Manage Power Distribution
Efficient power distribution is crucial for the reliable operation of the PCB. Use dedicated power planes or wide traces to distribute power to the components. Decouple power supplies using appropriate capacitors placed close to the power pins of integrated circuits (ICs). This helps to reduce voltage fluctuations and provide a stable power supply. Consider using voltage regulators and power management ICs when necessary to ensure proper voltage levels and minimize power dissipation.
Tip 6: Adhere to Design Rules
PCB manufacturing processes have specific design rules that must be followed to ensure manufacturability and reliability. These rules define parameters such as minimum trace widths, minimum clearances between traces and components, and minimum drill sizes for vias and through-holes. Familiarize yourself with the design rules provided by your PCB manufacturer and adhere to them throughout the layout process. Violating design rules can lead to manufacturing issues, reduced yield, and potential failures.
Tip 7: Incorporate Testability Features
Designing for testability is an important consideration when creating a PCB layout. Incorporate test points and probe pads at strategic locations to facilitate testing and debugging of the assembled board. Provide access to critical signals and power rails to enable easy probing and measurement. Consider including boundary scan or JTAG interfaces for advanced testing capabilities. Designing for testability from the beginning can save time and effort during the validation and troubleshooting phases.
Tip 8: Plan for Manufacturability
When converting a schematic to a PCB layout, keep manufacturability in mind. Consider the capabilities and limitations of the PCB fabrication and assembly processes. Ensure that component footprints and pad sizes are compatible with the manufacturing equipment. Provide sufficient clearances for pick-and-place machines and avoid placing components too close to the board edges. Incorporate Fiducial Markers and alignment features to aid in the assembly process. Designing for manufacturability reduces the risk of production issues and improves the overall quality of the PCB.
Tip 9: Conduct Design Reviews
Design reviews are essential for catching potential issues and improving the overall quality of the PCB layout. Collaborate with experienced engineers, PCB designers, and subject matter experts to review your layout at different stages. They can provide valuable feedback, identify potential problems, and suggest improvements. Design reviews help to catch errors early in the process, saving time and costs associated with redesigns and rework.
Tip 10: Perform Thorough Verification
Before finalizing the PCB layout, perform thorough verification to ensure the design meets all the requirements and functions as intended. Use electronic design automation (EDA) tools to run design rule checks (DRC) and ensure compliance with the manufacturing guidelines. Conduct signal integrity simulations to analyze the behavior of critical signals and identify potential issues. Perform thermal analysis to verify that the PCB can dissipate heat effectively and operate within the specified temperature range. Thorough verification helps to minimize the risk of design flaws and ensures a robust and reliable PCB.
Conclusion
Converting a schematic to a PCB layout is a complex process that requires careful consideration of various factors. By following these ten tips, you can streamline the process, improve the quality of your PCB design, and increase the chances of a successful manufacturing outcome. Remember to understand the schematic, optimize component placement and signal routing, implement proper grounding and power distribution, adhere to design rules, incorporate testability features, plan for manufacturability, conduct design reviews, and perform thorough verification. By keeping these considerations in mind, you can create a PCB layout that meets the functional and performance requirements of your electronic device.
Frequently Asked Questions (FAQ)
1. What is the importance of component placement in PCB layout?
Component placement plays a crucial role in PCB layout as it directly impacts signal integrity, thermal management, and mechanical constraints. Proper component placement helps to minimize signal path lengths, reduce interference, and ensure optimal performance of the PCB.
2. Why is proper grounding important in PCB layout?
Proper grounding is essential for the stability and performance of the PCB. It provides a low-impedance return path for signals, reduces electromagnetic interference (EMI), and ensures a stable reference voltage. Implementing a solid ground plane and avoiding ground loops or isolated ground regions are key considerations in PCB layout.
3. What are design rules in PCB layout, and why should they be followed?
Design rules are specific guidelines provided by PCB manufacturers that define parameters such as minimum trace widths, clearances, and drill sizes. Adhering to these rules ensures manufacturability and reliability of the PCB. Violating design rules can lead to manufacturing issues, reduced yield, and potential failures.
4. How can designing for testability benefit the PCB Development process?
Designing for testability involves incorporating features such as test points, probe pads, and boundary scan interfaces into the PCB layout. These features facilitate testing and debugging of the assembled board, saving time and effort during the validation and troubleshooting phases. Designing for testability from the beginning can streamline the development process and improve the overall quality of the PCB.
5. What is the purpose of conducting design reviews in PCB layout?
Design reviews are essential for catching potential issues and improving the overall quality of the PCB layout. They involve collaborating with experienced engineers, PCB designers, and subject matter experts to review the layout at different stages. Design reviews help to identify errors early in the process, suggest improvements, and minimize the risk of costly redesigns and rework.
Consideration | Description |
---|---|
Component Placement | Group related components together, consider signal integrity, thermal management, and mechanical constraints |
Signal Routing | Minimize trace lengths, use appropriate trace widths, avoid sharp angles, use ground and power planes |
Grounding | Create a solid ground plane, connect all ground points, avoid ground loops and isolated regions |
Power Distribution | Use dedicated power planes or wide traces, decouple power supplies, consider voltage regulators |
Design Rules | Adhere to manufacturer’s guidelines for trace widths, clearances, and drill sizes |
By following these tips and considerations, you can convert a schematic to a PCB layout that meets the functional and performance requirements of your electronic device. Careful planning, attention to detail, and thorough verification are key to achieving a successful PCB design.
No responses yet