What is ESD and Why is ESD Protection Important?
Electrostatic discharge (ESD) is a sudden flow of electricity between two electrically charged objects. It can be caused by direct contact or induced by an electrostatic field. ESD events are common in everyday life, such as the static shock you may experience when touching a doorknob after walking across a carpeted floor.
In the workplace, ESD can be a significant problem, particularly in industries dealing with sensitive electronic components. A single ESD event can damage or destroy electronic devices, leading to costly repairs, product failures, and decreased productivity. Implementing proper ESD protection measures is crucial for maintaining the integrity of electronic components and ensuring a safe and efficient work environment.
The Risks of ESD in the Workspace
ESD events can occur in various ways within the workspace, including:
- Human body model (HBM): When a charged person touches an electronic device.
- Charged device model (CDM): When a charged device touches a conductive surface.
- Machine model (MM): When a charged machine or tool touches an electronic device.
The severity of an ESD event depends on several factors, such as the voltage, current, and duration of the discharge. Even small ESD events, which may be imperceptible to humans, can cause latent damage to electronic components, leading to premature failure or reduced performance.
Implementing an Effective ESD Protection Plan
To minimize the risks associated with ESD in the workspace, it is essential to develop and implement a comprehensive ESD protection plan. This plan should include a combination of administrative controls, engineering controls, and personal protective equipment (PPE).
Administrative Controls
Administrative controls are policies and procedures designed to reduce the risk of ESD events. These controls include:
- ESD training: Educating employees about the risks of ESD, proper handling techniques, and the importance of following ESD protection protocols.
- ESD audits: Regularly assessing the workspace to identify potential ESD hazards and ensuring compliance with ESD protection standards.
- Document control: Maintaining accurate records of ESD training, audits, and incident reports.
Engineering Controls
Engineering controls are physical measures implemented to reduce the risk of ESD events. These controls include:
- ESD-safe workstations: Designing workstations with conductive or dissipative surfaces, grounding points, and ionizers to neutralize static charges.
- Grounding and bonding: Connecting all conductive objects within the workspace to a common ground point to equalize electrical potential and prevent static buildup.
- Ionization: Using ionizers to neutralize static charges on objects and surfaces that cannot be grounded.
- Humidity control: Maintaining relative humidity levels between 30% and 70% to reduce static buildup.
Personal Protective Equipment (PPE)
PPE is designed to protect individual workers from ESD events. Examples of ESD-safe PPE include:
- ESD-safe shoes or heel straps: Providing a conductive path between the worker and the ESD-safe flooring.
- ESD-safe smocks or lab coats: Preventing static buildup on clothing and providing a conductive path to the worker’s skin.
- ESD-safe gloves: Protecting workers’ hands and preventing static transfer when handling sensitive components.
- ESD-safe wrist straps: Providing a continuous ground path between the worker’s skin and the ESD-safe workstation.
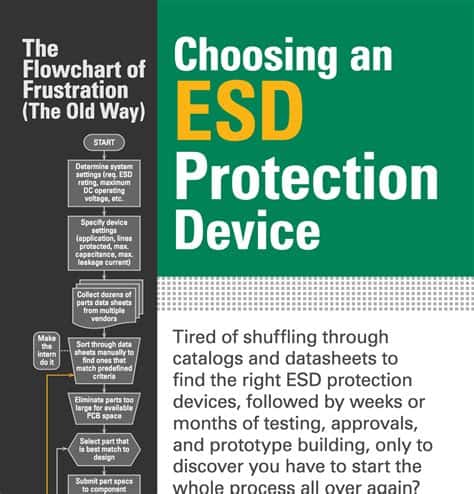
ESD-Safe Materials and Their Properties
When selecting materials for an ESD-safe workspace, it is essential to understand their electrical properties and how they contribute to ESD protection. Materials can be classified into three categories based on their electrical resistance:
- Conductive materials: Having a surface resistance less than 10^4 ohms. Examples include metals and carbon-filled plastics.
- Dissipative materials: Having a surface resistance between 10^4 and 10^11 ohms. Examples include ESD-safe vinyl and ESD-safe foam.
- Insulative materials: Having a surface resistance greater than 10^11 ohms. Examples include regular plastics and untreated wood.
In an ESD-safe workspace, it is crucial to use conductive or dissipative materials for surfaces that come into contact with sensitive electronic components. These materials allow static charges to dissipate safely, preventing harmful ESD events.
Common ESD-Safe Materials
Material | Surface Resistance (ohms) | Applications |
---|---|---|
Stainless Steel | < 10^4 | Workbench surfaces, shelving, tools |
ESD-Safe Vinyl | 10^6 – 10^8 | Flooring, table mats, chair mats |
ESD-Safe Foam | 10^9 – 10^11 | Packaging materials, cushioning for sensitive components |
Carbon-Filled Polyester | 10^4 – 10^6 | Smocks, lab coats, gloves |
Conductive Rubber | < 10^4 | Foot straps, wrist straps, grounding cords |
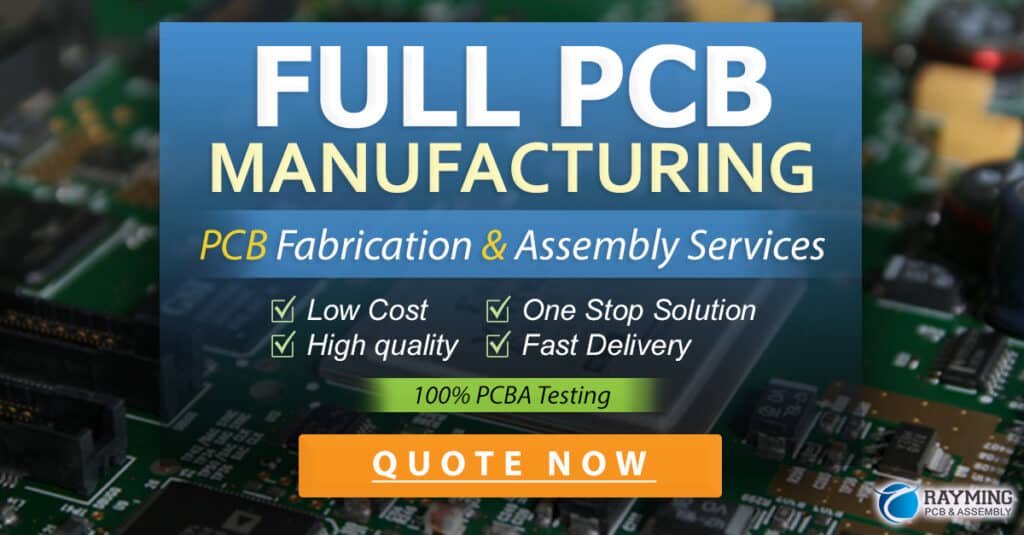
ESD Testing and Monitoring
To ensure the effectiveness of an ESD protection plan, regular testing and monitoring of the workspace, equipment, and personnel is necessary. There are several methods for testing and monitoring ESD, including:
- Surface resistance testing: Using a surface resistance meter to measure the electrical resistance of surfaces and ensure they fall within the desired range.
- Ground continuity testing: Verifying that all grounded objects within the workspace are properly connected to the common ground point.
- Personnel testing: Checking the resistance of wrist straps, heel straps, and ESD-safe shoes to ensure they provide adequate grounding for personnel.
- Ionizer testing: Measuring the balance and decay time of ionizers to ensure they are effectively neutralizing static charges.
Establishing a regular testing and monitoring schedule is essential for maintaining a safe and compliant ESD-protected workspace. The frequency of testing may vary depending on the sensitivity of the components being handled and the risk level of the environment.
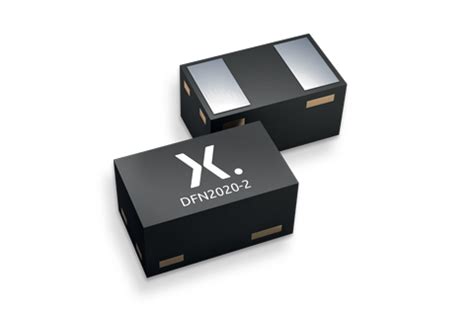
ESD Standards and Compliance
Several international standards provide guidelines and requirements for implementing ESD protection in the workspace. Adhering to these standards helps ensure the effectiveness of ESD protection measures and demonstrates compliance to customers and regulatory bodies.
Some of the most widely recognized ESD standards include:
- ANSI/ESD S20.20: Protection of Electrical and Electronic Parts, Assemblies, and Equipment (Excluding Electrically Initiated Explosive Devices)
- IEC 61340-5-1: Electrostatics – Part 5-1: Protection of Electronic Devices from Electrostatic Phenomena – General Requirements
- MIL-STD-1686: Electrostatic Discharge Control Program for Protection of Electrical and Electronic Parts, Assemblies, and Equipment (Excluding Electrically Initiated Explosive Devices)
To maintain compliance with these standards, organizations must develop and implement a comprehensive ESD control program, which includes:
- Establishing an ESD control plan
- Designating an ESD coordinator
- Providing ESD training for personnel
- Implementing ESD-safe workstations and materials
- Conducting regular ESD testing and monitoring
- Maintaining accurate documentation and records
By adhering to these standards and implementing a robust ESD control program, organizations can minimize the risks associated with ESD events and ensure the quality and reliability of their products.
Frequently Asked Questions (FAQ)
- What is the difference between ESD and EMI?
-
ESD (Electrostatic Discharge) refers to the sudden transfer of static electricity between two objects, which can damage electronic components. EMI (Electromagnetic Interference) is the disruption of electronic devices caused by electromagnetic radiation emitted by other devices or sources. While both can impact electronic devices, ESD is related to static electricity, and EMI is related to electromagnetic radiation.
-
Can ESD damage occur without visible or audible signs?
-
Yes, ESD events can occur without any visible or audible signs, such as sparks or crackling sounds. These events, known as silent discharges, can still cause damage to sensitive electronic components. This is why it is crucial to implement a comprehensive ESD protection plan, even if ESD events are not readily apparent.
-
How often should ESD testing and monitoring be conducted?
-
The frequency of ESD testing and monitoring depends on several factors, including the sensitivity of the electronic components being handled, the risk level of the environment, and the requirements of relevant ESD standards. As a general guideline, surface resistance testing and personnel testing should be conducted daily, while ground continuity testing and ionizer testing should be performed monthly or quarterly.
-
Can regular cleaning products be used in an ESD-safe workspace?
-
No, regular cleaning products should not be used in an ESD-safe workspace, as they may contain ingredients that can generate static charges or leave residues that can interfere with ESD protection. Instead, use ESD-safe cleaning products specifically designed for use in ESD-protected environments. These products are formulated to minimize static generation and maintain the integrity of ESD-safe surfaces.
-
What should be done if an ESD event occurs in the workspace?
- If an ESD event occurs, the first step is to assess the situation and determine if any damage has occurred to electronic components or equipment. If damage is suspected, the affected items should be quarantined and inspected by qualified personnel. The ESD event should be documented, and the root cause investigated to prevent future occurrences. This may involve reviewing ESD protection measures, conducting additional training, or updating ESD control procedures.
Conclusion
Implementing a comprehensive ESD protection plan is essential for minimizing the risks associated with electrostatic discharge in the workspace. By understanding the causes and consequences of ESD events, selecting appropriate ESD-safe materials, and establishing regular testing and monitoring procedures, organizations can safeguard sensitive electronic components and maintain a safe and efficient work environment.
Adhering to industry standards and best practices for ESD protection not only helps prevent costly damage and product failures but also demonstrates a commitment to quality and reliability to customers and stakeholders. As technology continues to advance and electronic devices become increasingly sensitive, the importance of effective ESD protection will only continue to grow.
No responses yet