Introduction to Wiring Harness Labels
In the world of electrical systems, wiring harnesses play a crucial role in connecting various components and ensuring the smooth functioning of devices. From automobiles to airplanes, wiring harnesses are used in a wide range of applications. However, the complexity of these systems can quickly become overwhelming without proper organization and identification. This is where wiring harness labels come into play.
Wiring harness labels are essential for identifying and tracking individual wires within a harness. They provide a clear and concise way to label each wire, making it easier for technicians and engineers to troubleshoot, repair, or modify the system. In this article, we will explore the importance of wiring harness labels, the different types of labels available, and the best practices for labeling your wiring harnesses.
The Importance of Wiring Harness Labels
Facilitating Maintenance and Repairs
One of the primary reasons for labeling wiring harnesses is to simplify maintenance and repair tasks. When a problem arises in an electrical system, technicians need to quickly identify the source of the issue. Without proper labeling, tracing the faulty wire can be a time-consuming and frustrating process. By using clear and consistent labels, technicians can easily locate the problematic wire and perform the necessary repairs, saving valuable time and resources.
Ensuring Safety
Wiring harness labels also play a crucial role in ensuring the safety of those working with electrical systems. Misidentified or unlabeled wires can lead to incorrect connections, which can result in short circuits, electrical fires, or even personal injury. By properly labeling each wire, you reduce the risk of accidents and create a safer working environment for technicians and engineers.
Facilitating System Upgrades and Modifications
As technology advances, electrical systems often require upgrades or modifications to keep up with changing requirements. Wiring harness labels make it easier to identify the various components of the system, allowing for smoother integration of new features or replacement of outdated parts. With clear labeling, engineers can quickly determine which wires need to be disconnected, rerouted, or replaced, streamlining the upgrade process.
Complying with Industry Standards
Many industries have specific standards and regulations regarding the labeling of electrical systems. For example, the aerospace industry follows strict guidelines set forth by the Federal Aviation Administration (FAA) to ensure the safety and reliability of aircraft wiring. By adhering to these standards and using appropriate wiring harness labels, companies can demonstrate compliance and avoid potential legal or financial consequences.
Types of Wiring Harness Labels
There are several types of wiring harness labels available, each with its own advantages and applications. Let’s take a closer look at some of the most common options:
Heat Shrink Labels
Heat shrink labels are made from a specialized material that shrinks when exposed to heat. These labels are applied to the wire and then heated using a heat gun or other heating device, causing them to conform tightly to the wire’s surface. Heat shrink labels provide excellent durability and resistance to abrasion, chemicals, and extreme temperatures, making them ideal for harsh environments.
Wrap-Around Labels
Wrap-around labels are designed to wrap completely around the wire, providing a secure and easily readable identification solution. These labels often feature an adhesive backing that adheres to itself, creating a tight and permanent seal around the wire. Wrap-around labels are available in various sizes and materials, making them suitable for a wide range of applications.
Flag Labels
Flag labels are attached to the wire at one end, with the other end remaining free to “flag” outward. This design allows for easy identification of the wire without the need to rotate or manipulate the harness. Flag labels are particularly useful in situations where the wiring harness is difficult to access or where quick identification is necessary.
Self-Laminating Labels
Self-laminating labels consist of a printed label area and a clear, laminating portion. After the label is applied to the wire, the clear laminate is wrapped around the label, providing an additional layer of protection against moisture, abrasion, and fading. Self-laminating labels are an excellent choice for environments where durability and long-term readability are essential.
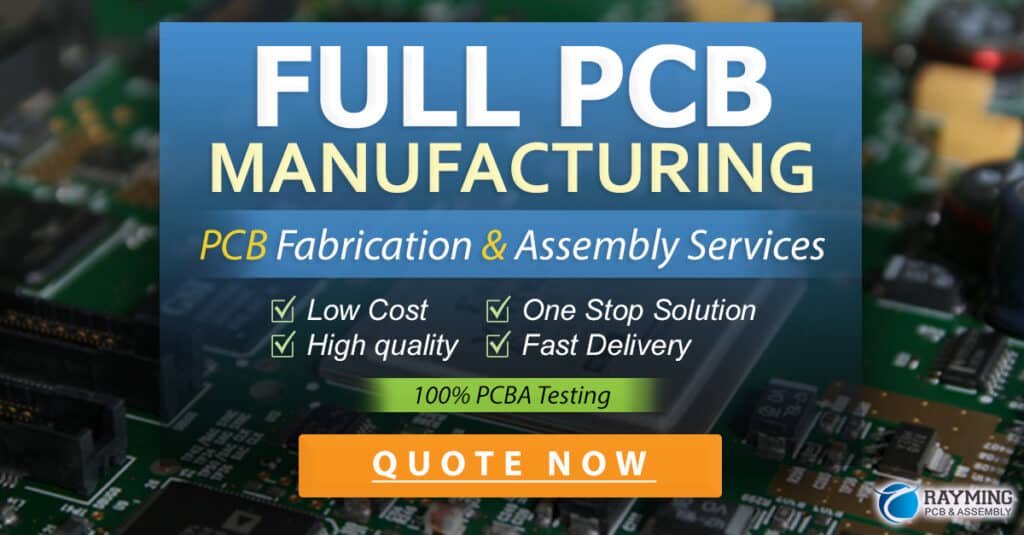
Best Practices for Labeling Wiring Harnesses
To ensure the effectiveness and longevity of your wiring harness labels, consider the following best practices:
Choose the Right Material
Select a label material that is appropriate for the environment in which the wiring harness will be used. Factors to consider include temperature range, exposure to chemicals or moisture, and the level of abrasion resistance required. For example, if the harness will be subjected to high temperatures, choose a label material that can withstand extreme heat without deteriorating or becoming illegible.
Use a Consistent Labeling Scheme
Develop a consistent and logical labeling scheme for your wiring harnesses. This may include using specific color codes, numbering systems, or abbreviations to identify different types of wires or components. A well-organized labeling scheme will make it easier for technicians and engineers to navigate the system and perform maintenance or repairs efficiently.
Ensure Legibility
When creating labels, use clear and easily readable fonts. Avoid using overly stylized or decorative fonts that may be difficult to read at a glance. Additionally, consider the size of the label and the amount of information it needs to convey. Strike a balance between providing enough detail and maintaining legibility.
Apply Labels Correctly
Follow the manufacturer’s instructions for applying wiring harness labels. Ensure that the label is positioned correctly and adheres securely to the wire. If using heat shrink labels, apply the appropriate amount of heat to achieve a tight and permanent fit. Improperly applied labels can become detached or unreadable over time, defeating the purpose of labeling.
Update Labels as Needed
As electrical systems undergo modifications or upgrades, it is essential to update the wiring harness labels accordingly. Outdated or inaccurate labels can lead to confusion and errors during maintenance or repair tasks. Regularly review and update your labels to ensure they reflect the current state of the system.
Frequently Asked Questions (FAQ)
1. Can I create my own wiring harness labels?
Yes, it is possible to create your own wiring harness labels using a label printer and appropriate label materials. However, ensure that your labels meet any applicable industry standards and are suitable for the intended environment.
2. How do I choose the right size label for my wiring harness?
The size of the label should be appropriate for the diameter of the wire and the amount of information you need to include. Consider the readability of the label and ensure that it can be easily seen and understood by technicians and engineers.
3. Are there any industry-specific standards for wiring harness labeling?
Yes, many industries have specific standards for wiring harness labeling. For example, the aerospace industry follows guidelines set forth by the FAA, while the automotive industry adheres to standards such as those established by the Society of Automotive Engineers (SAE).
4. How can I ensure the longevity of my wiring harness labels?
To ensure the longevity of your labels, choose a material that is appropriate for the environment in which the harness will be used. Consider factors such as temperature range, exposure to chemicals or moisture, and abrasion resistance. Additionally, apply the labels correctly and update them as needed to maintain accuracy.
5. Can wiring harness labels be removed and reapplied?
The ability to remove and reapply wiring harness labels depends on the type of label and the adhesive used. Some labels, such as those with a strong permanent adhesive, may be difficult or impossible to remove without damaging the wire insulation. If you anticipate the need to remove or reapply labels, consider using a label material with a removable adhesive.
Conclusion
Wiring harness labels are an essential component of any well-organized and efficient electrical system. By providing clear and consistent identification of individual wires, these labels facilitate maintenance, repair, and modification tasks, while also ensuring the safety of those working with the system. With a variety of label types available and best practices to follow, you can create a labeling system that meets the specific needs of your application and complies with any relevant industry standards.
By investing in high-quality wiring harness labels and implementing a comprehensive labeling strategy, you can streamline your electrical system’s management, reduce downtime, and improve overall efficiency. Whether you are working on a simple device or a complex network of wires, taking the time to properly label your harnesses will pay off in the long run, saving you time, money, and potential headaches down the line.
Label Type | Advantages | Applications |
---|---|---|
Heat Shrink Labels | Excellent durability and resistance to abrasion, chemicals, and extreme temperatures | Harsh environments |
Wrap-Around Labels | Secure and easily readable identification; available in various sizes and materials | Wide range of applications |
Flag Labels | Easy identification without the need to rotate or manipulate the harness | Difficult-to-access or quick identification situations |
Self-Laminating Labels | Additional layer of protection against moisture, abrasion, and fading | Environments where durability and long-term readability are essential |
No responses yet