Introduction to Wideband PCB Design
In today’s fast-paced digital world, the demand for high-speed data transmission and processing is increasing exponentially. To meet these requirements, engineers and designers are constantly pushing the boundaries of printed circuit board (PCB) design to accommodate wideband signals. Wideband PCB design is crucial for applications that require the transmission and processing of high-frequency signals, such as 5G networks, radar systems, and high-speed digital interfaces.
What is Wideband Signal Analysis?
Wideband signal analysis is the process of examining and characterizing signals that occupy a wide frequency range. These signals are typically characterized by their large bandwidth, which is the difference between the highest and lowest frequencies in the signal. Wideband signals are used in various applications, including:
- High-speed digital communication systems
- Radar and sonar systems
- Wireless networks (e.g., 5G, Wi-Fi)
- Satellite communication systems
- High-speed digital interfaces (e.g., USB, PCIe, HDMI)
Analyzing wideband signals requires specialized equipment and techniques to accurately capture and process the high-frequency components of the signal. This analysis is essential for ensuring the integrity and reliability of the signal transmission and reception.
The Importance of Ultra High Speed PCB Design
Ultra high speed PCB design is crucial for accommodating wideband signals and ensuring optimal signal integrity. As signal frequencies increase, the PCB layout and material properties become more critical factors in maintaining signal quality and minimizing distortion. Some of the key challenges in ultra high speed PCB design include:
- Controlling impedance and reducing reflections
- Minimizing crosstalk and electromagnetic interference (EMI)
- Managing signal propagation delay and skew
- Selecting appropriate PCB materials with suitable dielectric properties
- Optimizing trace routing and via placement
Addressing these challenges requires a thorough understanding of high-frequency signal behavior, PCB materials, and advanced design techniques. In the following sections, we will delve into the various aspects of wideband PCB design and provide practical tips and guidelines for achieving optimal performance.
High-Frequency Signal Behavior and PCB Materials
Understanding High-Frequency Signal Behavior
To effectively design PCBs for wideband signals, it is essential to understand the behavior of high-frequency signals and how they interact with the PCB environment. As signal frequencies increase, several phenomena become more pronounced and can significantly impact signal integrity:
-
Skin Effect: At high frequencies, current tends to flow primarily on the surface of conductors, leading to increased resistance and signal attenuation.
-
Dielectric Loss: PCB materials exhibit dielectric loss, which increases with frequency and leads to signal attenuation and distortion.
-
Reflections: Impedance discontinuities in the signal path cause reflections, which can lead to signal distortion and degradation.
-
Crosstalk: Electromagnetic coupling between adjacent traces can cause crosstalk, which can introduce noise and degrade signal quality.
Understanding and mitigating these effects is crucial for successful wideband PCB design.
Selecting Appropriate PCB Materials
The choice of PCB materials plays a critical role in the performance of high-speed designs. The key material properties to consider for wideband PCB design include:
-
Dielectric Constant (Dk): A lower Dk value reduces the signal propagation delay and helps maintain signal integrity.
-
Dissipation Factor (Df): A lower Df value minimizes dielectric loss and signal attenuation at high frequencies.
-
Thermal Conductivity: High thermal conductivity helps dissipate heat generated by high-frequency components and prevents thermal-related issues.
-
Coefficient of Thermal Expansion (CTE): A low CTE mismatch between the PCB material and components reduces mechanical stress and improves reliability.
Some common PCB materials suitable for high-speed designs include:
Material | Dk | Df | Thermal Conductivity (W/mK) | CTE (ppm/°C) |
---|---|---|---|---|
FR-4 | 4.3 | 0.02 | 0.3 | 14 |
Rogers RO4003C | 3.38 | 0.0027 | 0.71 | 11 |
Isola I-Tera MT40 | 3.45 | 0.0031 | 0.62 | 10 |
Nelco N4000-13EP | 3.7 | 0.009 | 0.4 | 12 |
Selecting the appropriate material based on the specific requirements of the design is essential for achieving optimal performance and signal integrity.
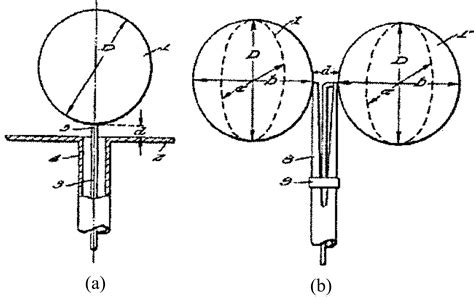
PCB Layout and Routing Techniques
Impedance Control and Matching
Maintaining proper impedance control and matching is crucial for minimizing reflections and ensuring signal integrity in wideband PCB designs. Some key techniques for impedance control include:
-
Microstrip and Stripline: These controlled impedance structures help maintain a consistent characteristic impedance along the signal path.
-
Differential Signaling: Using differential pairs helps reduce common-mode noise and improves signal integrity.
-
Termination Techniques: Proper termination techniques, such as series and parallel termination, help minimize reflections and maintain signal quality.
To achieve accurate impedance control, designers must carefully calculate trace widths, spacing, and dielectric thicknesses based on the target impedance and PCB material properties.
Trace Routing and Via Optimization
Proper trace routing and via optimization are essential for minimizing signal distortion and maintaining signal integrity in wideband PCB designs. Some best practices include:
-
Length Matching: Matching the lengths of traces within a group (e.g., data bus) helps minimize skew and ensures synchronous signal arrival.
-
Minimizing Via Count: Reducing the number of vias in the signal path helps minimize impedance discontinuities and reflections.
-
Via Optimization: Using techniques such as via shielding, back-drilling, and optimized via placement helps minimize via-related signal integrity issues.
-
Trace Corners and Bends: Using gentle angles (45° or 90°) and curved corners helps minimize reflections and maintain signal integrity.
Designers must also consider the impact of trace geometry on impedance and ensure that the trace dimensions are consistent throughout the signal path.
Crosstalk Reduction Techniques
Minimizing crosstalk is crucial for maintaining signal integrity and reducing noise in wideband PCB designs. Some effective techniques for crosstalk reduction include:
-
Trace Spacing: Increasing the spacing between adjacent traces helps reduce electromagnetic coupling and crosstalk.
-
Guard Traces: Placing grounded guard traces between sensitive signals helps shield them from crosstalk.
-
Orthogonal Routing: Routing sensitive traces orthogonally to each other helps minimize crosstalk by reducing the coupling area.
-
Stripline Shielding: Using stripline structures with ground planes on both sides helps confine the electromagnetic fields and reduces crosstalk.
Designers must carefully analyze the crosstalk risk and apply appropriate reduction techniques based on the specific requirements of the design.
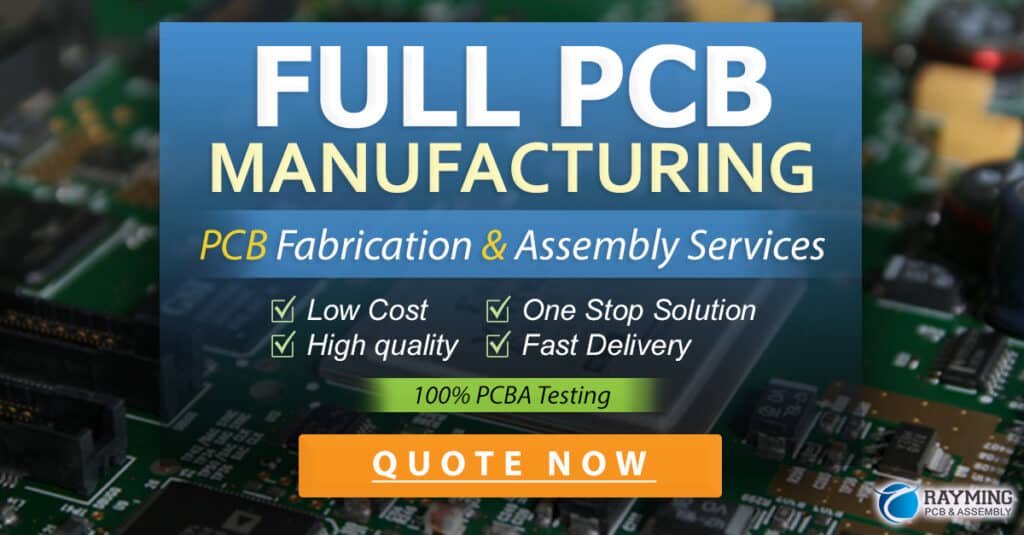
Simulation and Verification
Signal Integrity Simulation
Signal integrity (SI) simulation is a crucial step in the wideband PCB design process, as it helps predict and optimize the performance of the design before fabrication. SI simulation tools, such as Ansys Hyperlynx and Keysight ADS, allow designers to:
- Analyze impedance and reflections
- Simulate eye diagrams and bit error rates (BER)
- Evaluate crosstalk and EMI
- Optimize trace routing and termination
By performing SI simulations, designers can identify potential issues early in the design process and make necessary adjustments to ensure optimal signal integrity.
Power Integrity Analysis
Power integrity (PI) analysis is equally important for wideband PCB designs, as it ensures that the power delivery network (PDN) can provide clean and stable power to the high-frequency components. PI analysis tools help designers:
- Evaluate PDN impedance and resonance
- Analyze voltage drop and current density
- Optimize decoupling capacitor placement and values
- Simulate the impact of via and trace inductance
Proper PI analysis and optimization help minimize power-related signal integrity issues and ensure reliable operation of the wideband system.
EMC Compliance and Testing
Electromagnetic compatibility (EMC) is a critical consideration for wideband PCB designs, as high-frequency signals can easily radiate and cause interference with other electronic devices. Designers must ensure that the PCB complies with relevant EMC standards, such as FCC Part 15 and EN 55022, to avoid legal and regulatory issues.
EMC compliance can be achieved through various techniques, such as:
- Proper grounding and shielding
- Filtering and suppression of high-frequency noise
- Minimizing loop areas and controlling return paths
- Using EMI-resistant components and materials
Pre-compliance EMC testing can help identify potential issues and guide design improvements before the final certification process.
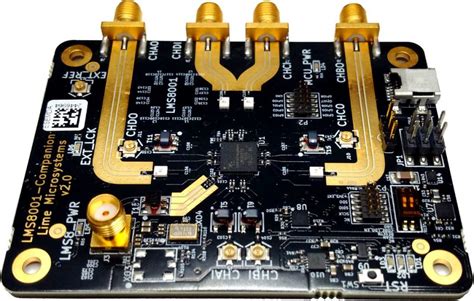
Advanced Wideband PCB Design Techniques
Substrate Integrated Waveguide (SIW)
Substrate Integrated Waveguide (SIW) is an emerging technology that combines the benefits of traditional waveguides and PCB technology. SIW structures are formed by creating a periodic array of metallic vias in a PCB substrate, which acts as a waveguide for high-frequency signals. Some advantages of SIW include:
- Low loss and high Q-factor
- Excellent isolation and shielding
- Compact size and easy integration with PCB components
- Cost-effective manufacturing using standard PCB processes
SIW technology is particularly useful for applications such as millimeter-wave systems, antenna arrays, and high-frequency filters.
Microwave and Millimeter-Wave PCB Design
Designing PCBs for microwave and millimeter-wave frequencies (30 GHz and above) presents additional challenges due to the extremely small wavelengths and high susceptibility to losses and distortion. Some key considerations for microwave and millimeter-wave PCB design include:
- Selection of low-loss PCB materials with stable dielectric properties
- Use of advanced transmission line structures, such as coplanar waveguides (CPW) and grounded coplanar waveguides (GCPW)
- Careful control of trace dimensions and spacing to maintain impedance and minimize losses
- Incorporation of on-board antennas and transitions for wireless signal transmission and reception
Designers must also be familiar with specialized simulation and analysis tools, such as electromagnetic (EM) field solvers, to accurately predict and optimize the performance of these high-frequency designs.
High-Density Interconnect (HDI) PCBs
High-Density Interconnect (HDI) PCBs are characterized by their fine trace widths, small via sizes, and high component density. HDI technology enables the miniaturization of wideband systems and improves signal integrity by reducing trace lengths and impedance discontinuities. Some features of HDI PCBs include:
- Microvias and buried vias for high-density interconnects
- Fine-pitch BGA and CSP components for compact assembly
- Sequential lamination and multi-layer construction for enhanced functionality
- Advanced via filling and planarization techniques for improved reliability
HDI PCBs are widely used in applications such as smartphones, wearable devices, and high-performance computing systems.
Frequently Asked Questions (FAQ)
-
Q: What is the difference between a wideband signal and a narrowband signal?
A: A wideband signal has a large bandwidth, typically occupying a wide frequency range, while a narrowband signal has a small bandwidth and occupies a narrow frequency range. Wideband signals are used in applications that require high data rates and fast signal processing, while narrowband signals are used in applications that require high frequency selectivity and noise rejection. -
Q: What are the main challenges in designing PCBs for wideband signals?
A: The main challenges in wideband PCB design include controlling impedance and reducing reflections, minimizing crosstalk and EMI, managing signal propagation delay and skew, selecting appropriate PCB materials with suitable dielectric properties, and optimizing trace routing and via placement. These challenges become more pronounced as signal frequencies increase, requiring advanced design techniques and simulation tools. -
Q: How does the choice of PCB material affect the performance of wideband designs?
A: The choice of PCB material is critical for wideband designs, as the material properties directly impact signal integrity and performance. Key material properties to consider include dielectric constant (Dk), dissipation factor (Df), thermal conductivity, and coefficient of thermal expansion (CTE). Low Dk and Df values help reduce signal propagation delay and dielectric loss, while high thermal conductivity and low CTE mismatch improve reliability and prevent thermal-related issues. -
Q: What is the role of signal integrity simulation in wideband PCB design?
A: Signal integrity (SI) simulation is a crucial step in the wideband PCB design process, as it helps predict and optimize the performance of the design before fabrication. SI simulation tools allow designers to analyze impedance and reflections, simulate eye diagrams and bit error rates (BER), evaluate crosstalk and EMI, and optimize trace routing and termination. By performing SI simulations, designers can identify potential issues early in the design process and make necessary adjustments to ensure optimal signal integrity. -
Q: What are some advanced techniques for designing PCBs at microwave and millimeter-wave frequencies?
A: Designing PCBs for microwave and millimeter-wave frequencies requires specialized techniques and considerations. These include the selection of low-loss PCB materials with stable dielectric properties, the use of advanced transmission line structures such as coplanar waveguides (CPW) and grounded coplanar waveguides (GCPW), careful control of trace dimensions and spacing to maintain impedance and minimize losses, and the incorporation of on-board antennas and transitions for wireless signal transmission and reception. Designers must also be familiar with specialized simulation and analysis tools, such as electromagnetic (EM) field solvers, to accurately predict and optimize the performance of these high-frequency designs.
Conclusion
Wideband signal analysis and ultra high speed PCB design are critical aspects of modern electronic systems that demand high data rates, fast signal processing, and robust performance. Designing PCBs for wideband signals requires a deep understanding of high-frequency signal behavior, PCB materials, and advanced layout and routing techniques.
Key considerations in wideband PCB design include impedance control and matching, trace routing and via optimization, crosstalk reduction, signal and power integrity analysis, and EMC compliance. Advanced techniques such as substrate integrated waveguides (SIW), microwave and millimeter-wave design, and high-density interconnect (HDI) PCBs offer additional opportunities for enhancing the performance and functionality of wideband systems.
As the demand for high-speed data transmission and processing continues to grow, the importance of wideband signal analysis and ultra high speed PCB design will only increase. By staying up-to-date with the latest design techniques, simulation tools, and industry best practices, engineers and designers can create robust and reliable wideband systems that meet the ever-increasing demands of the modern world.
No responses yet