Introduction to Rigid-flex PCB
Rigid-flex PCBs are a hybrid design that combines the benefits of both rigid and flexible printed circuit boards. This innovative technology has revolutionized the electronics industry by offering a compact, reliable, and cost-effective solution for complex electronic projects. In this article, we will explore the advantages of using rigid-flex PCBs over traditional flexible PCBs and why they have become the preferred choice for many engineers and designers.
What is a Rigid-Flex PCB?
A rigid-flex PCB is a printed circuit board that combines both rigid and flexible substrates, allowing for a more compact and lightweight design compared to traditional PCBs. The rigid portions of the board provide structural support and stability, while the flexible sections allow for bending and folding, making it easier to fit the PCB into tight spaces or to connect multiple boards together.
Advantages of Rigid-Flex PCBs
- Space Savings
- Increased Reliability
- Reduced Assembly Time
- Cost-Effectiveness
- Improved Signal integrity
Comparing Rigid-Flex PCBs and Flexible PCBs
Flexible PCBs: An Overview
Flexible PCBs, also known as Flex Circuits, are printed circuit boards made from flexible plastic substrates, such as polyimide or polyester. These boards are designed to bend and flex, making them suitable for applications that require movement or need to fit into tight spaces. Flex PCBs are commonly used in consumer electronics, medical devices, and aerospace industries.
Limitations of Flexible PCBs
While flexible PCBs offer several advantages, they also have some limitations that can impact their suitability for certain electronic projects:
- Limited Structural Support
- Reduced Durability
- Higher Manufacturing Costs
- Challenging Assembly Process
- Potential Signal Integrity Issues
Rigid-Flex PCBs: Overcoming the Limitations of Flexible PCBs
Rigid-flex PCBs offer a solution to the limitations of flexible PCBs by combining the benefits of both rigid and flexible substrates. The rigid portions of the board provide the necessary structural support and stability, while the flexible sections allow for the required flexibility and movement. This hybrid design overcomes the challenges associated with flexible PCBs, making rigid-flex PCBs a more suitable choice for many electronic projects.
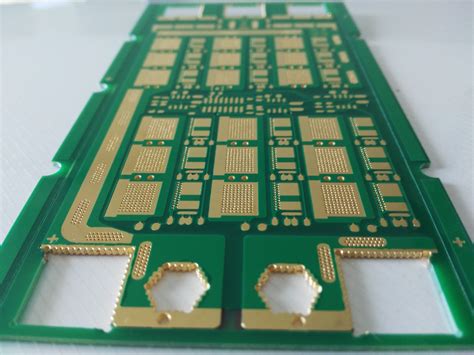
Benefits of Using Rigid-Flex PCBs in Electronic Projects
Space Savings and Compact Design
One of the primary advantages of using rigid-flex PCBs is the significant space savings they offer compared to traditional PCBs. By combining rigid and flexible substrates, designers can create more compact and lightweight electronic devices. The flexible sections of the board allow for bending and folding, enabling the PCB to fit into tight spaces or to connect multiple boards together seamlessly.
Example: In a smartphone design, a rigid-flex PCB can be used to connect the main logic board to the display and other components, reducing the overall size of the device and improving its portability.
Increased Reliability and Durability
Rigid-flex PCBs offer increased reliability and durability compared to flexible PCBs. The rigid portions of the board provide structural support and protection, reducing the risk of damage due to bending or flexing. Additionally, the use of high-quality materials and advanced manufacturing techniques ensures that rigid-flex PCBs can withstand harsh environments and prolonged use.
Example: In aerospace applications, rigid-flex PCBs are used to create reliable and durable electronic systems that can withstand extreme temperatures, vibrations, and shock.
Reduced Assembly Time and Cost-Effectiveness
Using rigid-flex PCBs can significantly reduce assembly time and costs compared to traditional PCBs. The ability to combine multiple boards into a single, compact design eliminates the need for separate connectors and cables, simplifying the assembly process. This not only saves time but also reduces the overall cost of the electronic project.
Example: In a medical device, a rigid-flex PCB can be used to integrate multiple sensors and components into a single, compact unit, reducing assembly time and costs while improving the device’s functionality.
Improved Signal Integrity and EMI Shielding
Rigid-flex PCBs offer improved signal integrity and electromagnetic interference (EMI) shielding compared to flexible PCBs. The rigid portions of the board provide a stable platform for high-speed signals, reducing the risk of signal distortion or loss. Additionally, the use of advanced shielding techniques and materials helps to minimize EMI, ensuring reliable performance in sensitive electronic applications.
Example: In a high-performance computing system, a rigid-flex PCB can be used to create a compact and efficient design with excellent signal integrity and EMI shielding, ensuring optimal performance and reliability.
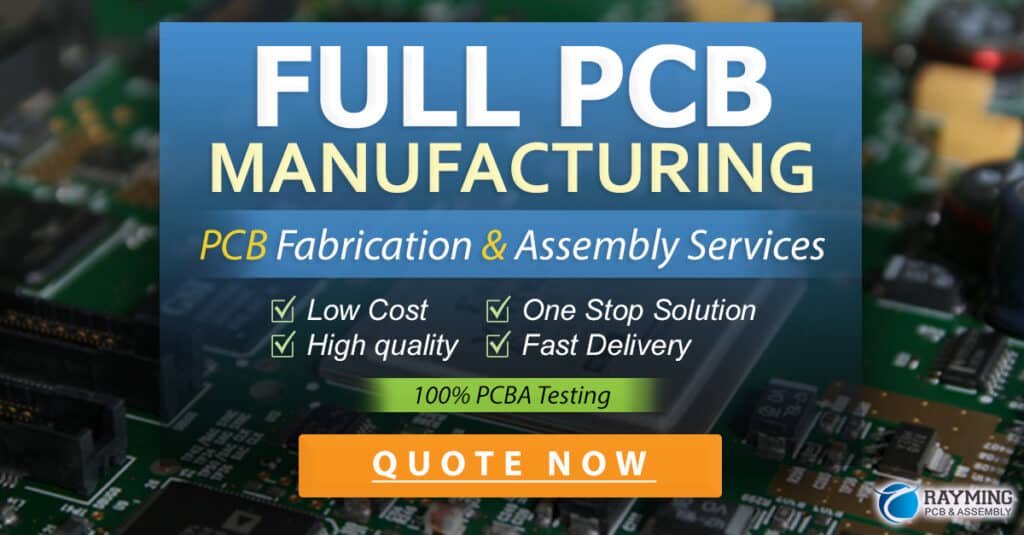
Applications of Rigid-Flex PCBs
Rigid-flex PCBs have found applications in a wide range of industries and electronic projects. Some of the most common applications include:
-
Consumer Electronics
- Smartphones
- Wearables
- Laptops
- Tablets
-
Medical Devices
- Implantable devices
- Portable medical equipment
- Diagnostic tools
-
Aerospace and Defense
- Satellites
- Avionics
- Military communication systems
-
Automotive Electronics
- In-vehicle infotainment systems
- Advanced driver assistance systems (ADAS)
- Electric vehicle battery management systems
-
Industrial Automation
- Robotics
- Machine vision systems
- Process control equipment
Industry | Applications | Benefits |
---|---|---|
Consumer Electronics | Smartphones, Wearables, Laptops, Tablets | Space savings, compact design, improved functionality |
Medical Devices | Implantable devices, Portable medical equipment, Diagnostic tools | Reliability, durability, compact size |
Aerospace and Defense | Satellites, Avionics, Military communication systems | Resistance to harsh environments, space savings, reliability |
Automotive Electronics | In-vehicle infotainment systems, ADAS, EV battery management systems | Compact design, reliability, improved functionality |
Industrial Automation | Robotics, Machine vision systems, Process control equipment | Durability, space savings, improved signal integrity |
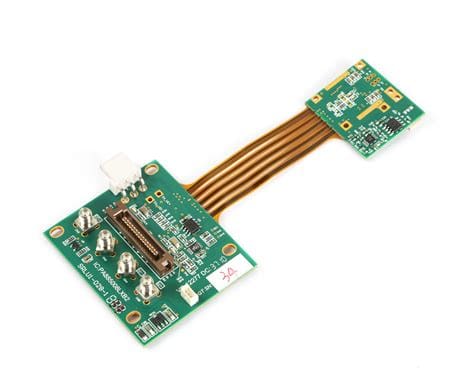
Designing and Manufacturing Rigid-Flex PCBs
Design Considerations
When designing rigid-flex PCBs, engineers and designers must consider several factors to ensure optimal performance and reliability:
-
Material Selection
- Choosing the right flexible and rigid substrates
- Selecting appropriate conductor and insulation materials
-
Bend Radius and Flexibility
- Determining the required bend radius and flexibility
- Ensuring proper placement of rigid and flexible sections
-
Layer Stack-Up
- Defining the layer stack-up for optimal signal integrity
- Considering the placement of ground and power planes
-
Component Placement
- Optimizing component placement for space savings and functionality
- Ensuring proper clearance and routing for flexible sections
-
Via and Interconnect Design
- Selecting appropriate via and interconnect technologies
- Ensuring reliable connections between rigid and flexible sections
Manufacturing Process
The manufacturing process for rigid-flex PCBs involves several steps and requires specialized equipment and expertise:
-
Material Preparation
- Cutting and laminating flexible and rigid substrates
- Applying adhesives and bonding layers
-
Patterning and Etching
- Creating conductor patterns using photolithography and etching
- Applying solder mask and silkscreen layers
-
Lamination
- Bonding the flexible and rigid sections together
- Applying pressure and heat for proper adhesion
-
Drilling and Plating
- Drilling via holes and plated through-holes
- Applying copper plating for electrical connectivity
-
Final Assembly
- Populating components and applying surface finishes
- Performing final inspection and testing
Challenges and Considerations
While rigid-flex PCBs offer numerous benefits, there are also some challenges and considerations that engineers and designers must keep in mind:
- Higher Initial Costs
-
The specialized materials and manufacturing processes required for rigid-flex PCBs can result in higher initial costs compared to traditional PCBs.
-
Design Complexity
-
Designing rigid-flex PCBs requires specialized knowledge and expertise, as the combination of rigid and flexible sections introduces additional complexity to the design process.
-
Manufacturing Challenges
-
The manufacturing of rigid-flex PCBs involves specialized equipment and processes, which can lead to longer lead times and potential supply chain challenges.
-
Reliability Testing
- Ensuring the reliability of rigid-flex PCBs requires extensive testing and validation, particularly for applications in harsh environments or mission-critical systems.
Despite these challenges, the benefits of using rigid-flex PCBs often outweigh the drawbacks, making them an attractive choice for many electronic projects.
Future Trends and Developments
As technology continues to evolve, the demand for more compact, reliable, and high-performance electronic devices will only increase. Rigid-flex PCBs are well-positioned to meet these demands, and several trends and developments are expected to shape the future of this technology:
- Advanced Materials
-
The development of new, high-performance materials for both rigid and flexible substrates will enable the creation of even more compact and reliable rigid-flex PCBs.
-
Increased Adoption in Emerging Industries
-
As industries such as 5G communication, autonomous vehicles, and IoT continue to grow, the adoption of rigid-flex PCBs is expected to increase significantly.
-
Miniaturization and High-Density Packaging
-
The trend towards miniaturization and high-density packaging will drive the development of more advanced rigid-Flex PCB Designs, enabling even greater space savings and functionality.
-
Sustainable and Eco-Friendly Solutions
- With a growing focus on sustainability, the development of eco-friendly materials and manufacturing processes for rigid-flex PCBs will become increasingly important.
FAQ
-
Q: What is the main difference between rigid-flex PCBs and flexible PCBs?
A: Rigid-flex PCBs combine both rigid and flexible substrates, offering structural support and flexibility in a single design. Flexible PCBs, on the other hand, are made entirely from flexible materials and lack the structural support provided by rigid sections. -
Q: Are rigid-flex PCBs more expensive than traditional PCBs?
A: Yes, rigid-flex PCBs can have higher initial costs compared to traditional PCBs due to the specialized materials and manufacturing processes required. However, the long-term benefits, such as space savings, reliability, and reduced assembly costs, often justify the initial investment. -
Q: Can rigid-flex PCBs be used in harsh environments?
A: Yes, rigid-flex PCBs are well-suited for use in harsh environments, such as those encountered in aerospace, defense, and industrial applications. The combination of rigid and flexible sections, along with the use of high-quality materials, enables rigid-flex PCBs to withstand extreme temperatures, vibrations, and shock. -
Q: How do I determine if a rigid-flex PCB is the right choice for my electronic project?
A: Consider using a rigid-flex PCB if your project requires a compact, lightweight design, improved reliability, reduced assembly time, or enhanced signal integrity. Rigid-flex PCBs are particularly well-suited for applications in consumer electronics, medical devices, aerospace, automotive, and industrial automation. -
Q: What are the key design considerations when creating a rigid-flex PCB?
A: When designing a rigid-flex PCB, key considerations include material selection, bend radius and flexibility, layer stack-up, component placement, and via and interconnect design. It is essential to work with experienced designers and manufacturers to ensure optimal performance and reliability.
Conclusion
In conclusion, rigid-flex PCBs offer a superior alternative to traditional flexible PCBs in many electronic projects. By combining the benefits of both rigid and flexible substrates, rigid-flex PCBs enable more compact, reliable, and cost-effective designs. With applications spanning across various industries, from consumer electronics to aerospace and defense, rigid-flex PCBs have proven to be a versatile and innovative solution for today’s complex electronic challenges.
As technology continues to advance, the adoption of rigid-flex PCBs is expected to grow, driven by the demand for smaller, more powerful, and more reliable electronic devices. By staying informed about the latest trends and developments in rigid-flex PCB technology, engineers and designers can create cutting-edge electronic products that meet the evolving needs of their customers and industries.
No responses yet