Introduction to PCB Track width
In the world of printed circuit board (PCB) design, track width is a crucial factor that can significantly impact the performance, reliability, and manufacturability of the final product. Track width refers to the width of the copper traces that carry electrical signals between components on a PCB. Choosing the appropriate track width is essential to ensure proper current carrying capacity, signal integrity, and heat dissipation.
What is PCB Track Width?
PCB track width is the measurement of the width of the copper traces on a printed circuit board. These traces act as the electrical pathways that connect various components on the PCB, allowing signals and power to flow between them. The width of these tracks can vary depending on the specific requirements of the design, such as the amount of current the track needs to carry, the desired impedance, and the available space on the PCB.
Why is Track Width Important?
Track width plays a vital role in PCB Design for several reasons:
-
Current Carrying Capacity: The width of a track determines its ability to carry electrical current without overheating or experiencing voltage drop. Wider tracks can handle higher currents, while narrower tracks are suitable for lower current applications.
-
Signal Integrity: Track width can affect the impedance of the signal path, which is crucial for maintaining signal integrity. Improper track width can lead to issues such as reflections, crosstalk, and electromagnetic interference (EMI).
-
Heat Dissipation: As current flows through the tracks, it generates heat. Wider tracks have a greater surface area, allowing for better heat dissipation and reducing the risk of thermal damage to the PCB and its components.
-
Manufacturing Constraints: The track width must be within the capabilities of the PCB manufacturing process. Overly narrow tracks can be difficult to manufacture reliably, while excessively wide tracks can increase the overall size and cost of the PCB.
Factors Affecting Track Width Selection
When determining the appropriate track width for a PCB design, several factors must be considered:
Current Carrying Capacity
One of the primary factors in selecting track width is the amount of current the track needs to carry. The current carrying capacity of a track is determined by its cross-sectional area, which is a function of its width and thickness. As a general rule, wider tracks can handle higher currents than narrower tracks.
To calculate the required track width based on current carrying capacity, designers can use the following formula:
Track Width (mm) = (Current (A) × Resistance (Ω/mm)) / (Allowed Temperature Rise (°C) × Copper Thickness (oz))
For example, if a track needs to carry 1A of current, has a resistance of 0.5Ω/mm, an allowed temperature rise of 10°C, and a copper thickness of 1oz, the required track width would be:
Track Width = (1A × 0.5Ω/mm) / (10°C × 1oz) = 0.05mm
It’s important to note that this is a simplified calculation, and designers should also consider other factors such as the ambient temperature, the duration of the current flow, and the proximity of other heat-generating components.
Signal Integrity
Signal integrity is another crucial factor in determining track width. The width of a track can affect its impedance, which is the measure of opposition to the flow of alternating current (AC) in a circuit. Impedance matching is essential for maintaining signal integrity and preventing issues such as reflections, crosstalk, and EMI.
The characteristic impedance of a track is determined by its width, thickness, and the properties of the PCB substrate. The following table provides a general guide for selecting track width based on the desired impedance:
Impedance (Ω) | Track Width (mm) |
---|---|
50 | 0.25 |
75 | 0.20 |
100 | 0.15 |
120 | 0.12 |
However, these values are only a starting point, and designers must also consider factors such as the PCB Stackup, the dielectric constant of the substrate, and the proximity of other tracks and planes.
Heat Dissipation
Heat dissipation is another important consideration when selecting track width. As current flows through a track, it generates heat due to the track’s resistance. If the track is too narrow, it may not be able to dissipate the heat effectively, leading to a temperature rise that could damage the PCB or its components.
To ensure adequate heat dissipation, designers can use wider tracks or increase the copper thickness. The following table provides a general guide for selecting track width based on the current carrying capacity and the allowed temperature rise:
Current (A) | Temperature Rise (°C) | Track Width (mm) |
---|---|---|
0.5 | 10 | 0.25 |
1.0 | 10 | 0.50 |
2.0 | 10 | 1.00 |
3.0 | 10 | 1.50 |
Again, these values are only a starting point, and designers must consider other factors such as the ambient temperature, the duration of the current flow, and the thermal properties of the PCB substrate.
Manufacturing Constraints
Finally, track width selection must take into account the capabilities of the PCB manufacturing process. While narrower tracks can help to reduce the overall size of the PCB, they can also be more challenging to manufacture reliably.
Most PCB Manufacturers have a minimum track width that they can produce consistently. This minimum width depends on factors such as the PCB material, the copper thickness, and the manufacturing equipment and processes used. Designers should consult with their PCB manufacturer to determine the minimum track width that can be achieved reliably.
In general, the following table provides a guide for selecting track width based on the capabilities of typical PCB manufacturing processes:
Process | Minimum Track Width (mm) |
---|---|
Standard | 0.15 |
Advanced | 0.10 |
High-Density | 0.08 |
Ultra-High-Density | 0.05 |
Best Practices for Track Width Selection
When selecting track widths for a PCB design, designers should follow these best practices:
-
Use the appropriate formula or calculator: Use the appropriate formula or calculator to determine the required track width based on the current carrying capacity, allowed temperature rise, and copper thickness.
-
Consider signal integrity requirements: Select track widths that provide the desired impedance for critical signal paths, and use impedance matching techniques where necessary.
-
Ensure adequate heat dissipation: Use wider tracks or increase the copper thickness to ensure adequate heat dissipation, especially for high-current paths.
-
Consult with the PCB manufacturer: Consult with the PCB manufacturer to determine the minimum track width that can be achieved reliably, and design within those constraints.
-
Use PCB design software: Use PCB design software that includes tools for calculating track widths based on current carrying capacity, impedance, and other factors.
-
Perform simulations and testing: Perform simulations and testing to verify that the selected track widths meet the design requirements for current carrying capacity, signal integrity, and heat dissipation.
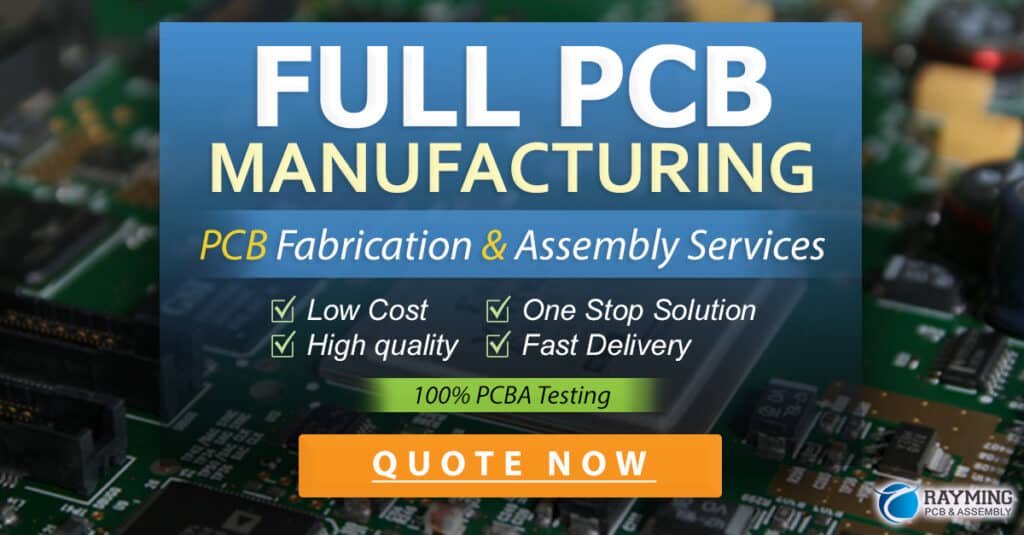
Frequently Asked Questions (FAQ)
-
What is the minimum track width that can be manufactured reliably?
The minimum track width that can be manufactured reliably depends on the capabilities of the PCB manufacturing process. Most standard processes can achieve a minimum track width of 0.15mm, while advanced processes can achieve 0.10mm or less. However, designers should always consult with their PCB manufacturer to determine the specific capabilities of their process. -
How does track width affect signal integrity?
Track width can affect signal integrity by influencing the impedance of the signal path. If the track width is too narrow or too wide, it can cause impedance mismatches that lead to reflections, crosstalk, and EMI. Designers must select track widths that provide the desired impedance for critical signal paths and use impedance matching techniques where necessary. -
Can increasing the copper thickness help with heat dissipation?
Yes, increasing the copper thickness can help with heat dissipation by providing a larger cross-sectional area for the current to flow through. This can help to reduce the temperature rise in the track and prevent damage to the PCB or its components. However, increasing the copper thickness can also increase the overall cost and weight of the PCB. -
What is the relationship between track width and current carrying capacity?
The current carrying capacity of a track is proportional to its cross-sectional area, which is determined by its width and thickness. Wider tracks can carry higher currents than narrower tracks, assuming the same thickness. Designers can use the appropriate formula or calculator to determine the required track width based on the desired current carrying capacity. -
How can PCB design software help with track width selection?
PCB design software typically includes tools for calculating track widths based on current carrying capacity, impedance, and other factors. These tools can help designers to quickly and accurately determine the appropriate track widths for their design, taking into account the specific requirements of the PCB and its components. Additionally, PCB design software can perform simulations and generate reports to verify that the selected track widths meet the design requirements.
Conclusion
Track width is a critical factor in PCB design that can significantly impact the performance, reliability, and manufacturability of the final product. By understanding the factors that influence track width selection, such as current carrying capacity, signal integrity, heat dissipation, and manufacturing constraints, designers can make informed decisions that optimize the PCB for its intended application.
When selecting track widths, designers should use the appropriate formulas and calculators, consider signal integrity requirements, ensure adequate heat dissipation, consult with the PCB manufacturer, use PCB design software, and perform simulations and testing. By following these best practices, designers can create PCBs that meet the highest standards of performance and reliability.
No responses yet