Introduction to Microvia and Its Superiority
Microvia, also known as HDI (High Density Interconnect) via, is a small-diameter via used in high-density PCB (Printed Circuit Board) designs. Compared to traditional through-hole vias and blind/buried vias, microvias offer several advantages that make them the preferred choice for modern electronic devices. In this article, we will explore the reasons behind microvia’s superiority and why it has become an essential component in PCB manufacturing.
What is a Microvia?
A microvia is a small-diameter via, typically less than 150 microns (0.15 mm) in diameter, that connects two or more layers in a PCB. Microvias are usually laser-drilled, which allows for precise control over their size and location. They can be stacked on top of each other to create complex interconnections between multiple layers, enabling higher density designs and improved signal integrity.
Types of Microvias
There are three main types of microvias:
- Blind via: Connects an outer layer to an inner layer, but does not pass through the entire board.
- Buried via: Connects two or more inner layers, but does not reach the outer layers.
- Through via: Passes through the entire board, connecting all layers.
Advantages of Microvias
1. Increased PCB Density
One of the primary advantages of microvias is their ability to increase PCB density. With smaller via diameters, designers can place more components and traces on a given board area. This is particularly important for devices that require high functionality in a compact form factor, such as smartphones, wearables, and IoT devices.
Via Type | Typical Diameter | Density Improvement |
---|---|---|
Through-hole | 0.5 – 1.0 mm | Baseline |
Blind/Buried | 0.2 – 0.5 mm | 2x – 4x |
Microvia | < 0.15 mm | 4x – 8x |
2. Improved Signal Integrity
Microvias also contribute to improved signal integrity in high-speed PCB designs. By reducing the via diameter and length, the parasitic capacitance and inductance associated with the via are minimized. This results in reduced signal reflections, crosstalk, and electromagnetic interference (EMI), leading to cleaner and more reliable signal transmission.
3. Shorter Signal Paths
With the ability to stack microvias and create interconnections between multiple layers, designers can optimize signal routing and reduce the overall signal path length. Shorter signal paths lead to reduced signal propagation delay, which is crucial for high-speed applications such as 5G communication, high-performance computing, and automotive electronics.
4. Enhanced Thermal Management
Microvias can also play a role in improving the thermal management of PCBs. By strategically placing microvias near heat-generating components, designers can create efficient thermal vias that help dissipate heat from the component to the PCB’s copper layers and, eventually, to the heatsink. This can help prevent component overheating and improve the overall reliability of the electronic device.
5. Cost-effective for High-volume Production
While the initial setup costs for microvia PCBs may be higher due to the specialized equipment and processes involved, they can be cost-effective for high-volume production runs. The increased density and functionality achieved through microvias can lead to smaller board sizes, reduced material costs, and simplified assembly processes, ultimately resulting in lower per-unit costs.
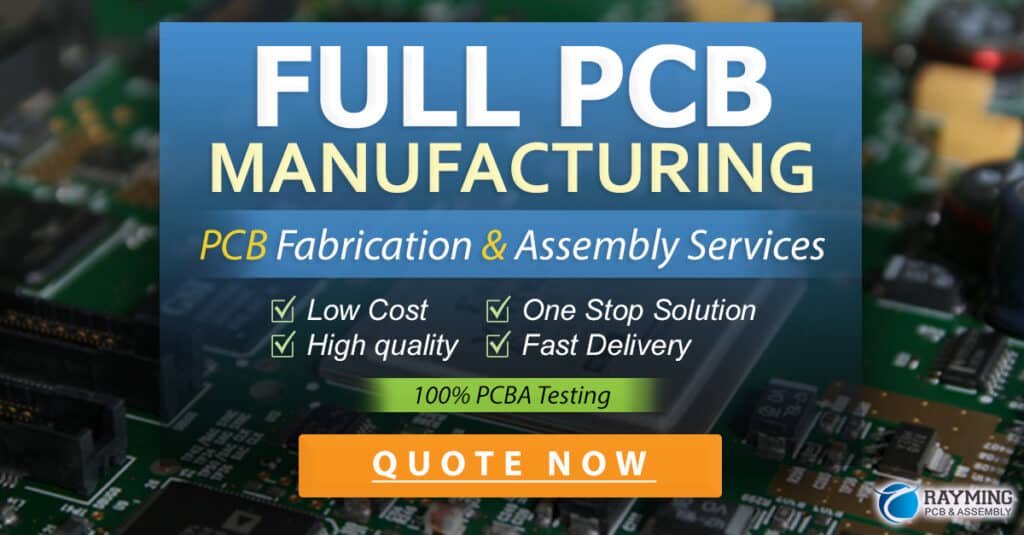
Microvia Manufacturing Process
The manufacturing process for microvias involves several steps:
-
Laser drilling: High-precision laser systems are used to drill the microvia holes in the PCB substrate. The laser type (CO2, UV, or YAG) and parameters are chosen based on the material and desired via size.
-
Desmear: After drilling, a chemical or plasma desmear process is performed to remove any debris and prepare the via walls for plating.
-
Electroless copper plating: A thin layer of copper is deposited onto the via walls using an electroless plating process. This layer acts as a seed for the subsequent electrolytic plating.
-
Electrolytic copper plating: The microvia is filled with copper using an electrolytic plating process, ensuring a reliable electrical connection between the layers.
-
Stacking and repeating: For multi-layer microvia designs, the process is repeated, with new layers being added and microvias being stacked on top of each other.
Challenges and Limitations
While microvias offer numerous benefits, there are some challenges and limitations to consider:
-
Higher initial setup costs: The specialized equipment and processes required for microvia manufacturing can result in higher initial setup costs compared to traditional PCB fabrication methods.
-
Design complexity: Designing with microvias requires careful consideration of via placement, stacking, and signal routing to ensure optimal performance and manufacturability.
-
Material selection: Not all PCB substrate materials are suitable for microvia manufacturing. The material must be compatible with the laser drilling process and have the necessary electrical and thermal properties.
-
Reliability concerns: Microvia reliability can be affected by factors such as via geometry, plating quality, and thermal cycling. Proper design and manufacturing practices must be followed to ensure long-term reliability.
FAQ
-
Q: What is the difference between a microvia and a standard via?
A: A microvia is a small-diameter via (typically < 0.15 mm) that connects two or more layers in a PCB, while a standard via has a larger diameter (0.5 – 1.0 mm) and is used for through-hole connections. -
Q: Can microvias be used in all PCB designs?
A: Microvias are primarily used in high-density PCB designs that require increased functionality in a compact form factor. They may not be necessary or cost-effective for simpler, low-density designs. -
Q: Are microvias more expensive than standard vias?
A: The initial setup costs for microvia PCBs can be higher due to the specialized equipment and processes involved. However, for high-volume production runs, microvias can be cost-effective due to increased density, reduced material costs, and simplified assembly. -
Q: What materials are suitable for microvia PCBs?
A: Common materials for microvia PCBs include FR-4, polyimide, and high-frequency laminates such as Rogers and Isola. The material must be compatible with the laser drilling process and have the necessary electrical and thermal properties. -
Q: How can I ensure the reliability of microvia PCBs?
A: To ensure the reliability of microvia PCBs, follow best practices in design and manufacturing, such as optimizing via geometry, ensuring proper plating quality, and conducting thorough testing and inspection. Working with experienced PCB manufacturers and adhering to industry standards can also help minimize reliability issues.
Conclusion
Microvias have revolutionized the world of PCB design and manufacturing, offering numerous advantages over traditional via technologies. With their ability to increase PCB density, improve signal integrity, shorten signal paths, enhance thermal management, and provide cost-effective solutions for high-volume production, microvias have become an essential component in modern electronic devices.
As the demand for smaller, faster, and more functional electronics continues to grow, the adoption of microvia technology is expected to increase. However, designers and manufacturers must also be aware of the challenges and limitations associated with microvias, such as higher initial setup costs, design complexity, material selection, and reliability concerns.
By understanding the benefits and challenges of microvias and following best practices in design and manufacturing, engineers and PCB manufacturers can harness the full potential of this technology to create innovative, high-performance electronic devices that meet the evolving needs of the market.
No responses yet