Introduction to PCB Prototyping
PCB prototyping is an essential step in the development of electronic devices. It allows designers and engineers to test and validate their designs before moving into mass production. High voltage PCBs, in particular, require careful consideration and planning during the prototyping phase to ensure safety and reliability.
Rushing to form factor, or trying to create a final product design too quickly, can lead to costly mistakes and delays. By focusing on designing a high voltage PCB for rapid prototyping first, designers can identify and address potential issues early on, saving time and resources in the long run.
The Importance of Proper High Voltage PCB Design
Safety Considerations
High voltage PCBs pose unique safety challenges due to the increased risk of electrical shock and fire hazards. Proper design techniques must be employed to ensure the safety of both the end-users and the designers working on the project.
Some key safety considerations include:
- Adequate isolation between high voltage and low voltage components
- Proper creepage and clearance distances
- Use of appropriate insulation materials
- Incorporation of safety features such as fuses and circuit breakers
Reliability and Performance
In addition to safety, high voltage PCBs must also be designed for optimal reliability and performance. This involves careful selection of components, layout optimization, and thorough testing.
Factors that can impact reliability and performance include:
- Component selection and rating
- PCB material choice
- Trace width and spacing
- Thermal management
- EMI/EMC considerations
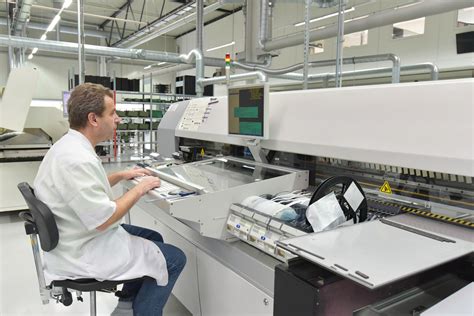
Advantages of Rapid Prototyping for High Voltage PCBs
Identifying Design Flaws Early
One of the primary benefits of focusing on rapid prototyping for high voltage PCBs is the ability to identify design flaws early in the development process. By creating and testing prototypes, designers can uncover potential issues related to safety, reliability, and performance before investing significant time and resources into the final product design.
Iterative Design Improvements
Rapid prototyping also allows for iterative design improvements. As issues are identified and addressed, designers can create new prototypes incorporating the necessary changes. This process can be repeated until an optimal design is achieved, ensuring a higher quality final product.
Cost and Time Savings
By identifying and addressing design flaws early through rapid prototyping, designers can ultimately save both time and money. Catching mistakes early reduces the risk of costly redesigns and delays later in the development process.
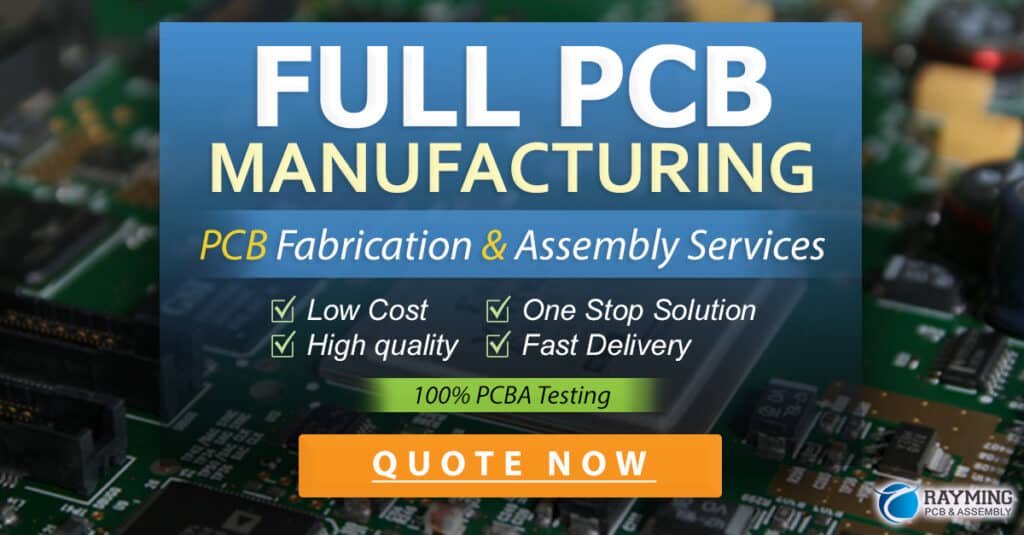
Best Practices for High Voltage PCB Prototyping
Component Selection and Placement
Proper component selection and placement are critical for high voltage PCB prototyping. Designers should choose components with appropriate voltage and power ratings, and position them in a way that minimizes the risk of arcing and other hazards.
Layout Optimization
PCB layout optimization is another key consideration for high voltage prototyping. Designers should follow best practices for trace routing, including the use of wide traces for high current paths and adequate spacing between traces to minimize the risk of arcing.
Testing and Validation
Thorough testing and validation are essential for high voltage PCB prototypes. This may include:
- Electrical safety testing
- Functional testing
- Environmental testing (e.g., temperature, humidity, vibration)
- EMI/EMC testing
By conducting comprehensive testing, designers can ensure that their prototypes meet all necessary safety and performance requirements before moving on to the final product design.
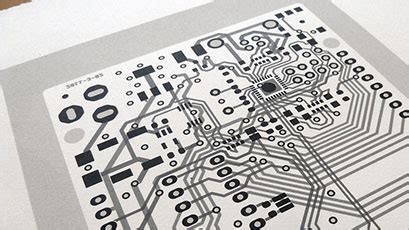
Case Studies
Case Study 1: Medical Device Manufacturer
A medical device manufacturer was developing a new high voltage power supply for their latest product. By focusing on rapid prototyping, they were able to identify and address several potential safety issues early in the design process, including inadequate creepage distances and insufficient insulation between high voltage components.
Thanks to their rapid prototyping approach, the manufacturer was able to make the necessary design changes quickly and efficiently, ultimately saving time and resources in the long run.
Case Study 2: Industrial Equipment Supplier
An industrial equipment supplier was working on a new high voltage motor controller. They initially rushed to create a final product design, but encountered numerous performance issues during testing.
After taking a step back and focusing on rapid prototyping, they were able to identify and address the root causes of the performance problems, including inadequate thermal management and EMI/EMC issues. By iterating on their prototype design, they ultimately created a more reliable and efficient final product.
FAQ
-
Q: What are the main safety concerns when designing high voltage PCBs?
A: The main safety concerns include electrical shock hazards, fire risks, and the potential for arcing between high voltage components. Proper isolation, creepage and clearance distances, insulation, and safety features like fuses and circuit breakers are essential for mitigating these risks. -
Q: Why is rapid prototyping so important for high voltage PCB design?
A: Rapid prototyping allows designers to identify and address potential safety, reliability, and performance issues early in the development process. This can ultimately save time and resources by reducing the risk of costly redesigns and delays later on. -
Q: What are some key considerations for component selection and placement in high voltage PCB design?
A: When selecting components for high voltage PCBs, designers should choose parts with appropriate voltage and power ratings. Components should also be positioned in a way that minimizes the risk of arcing and other hazards, with adequate spacing between high voltage components. -
Q: How can PCB layout optimization improve the performance of high voltage PCBs?
A: PCB layout optimization techniques, such as using wide traces for high current paths and ensuring adequate spacing between traces, can help minimize the risk of arcing and improve overall performance. Proper layout can also help with thermal management and EMI/EMC mitigation. -
Q: What types of testing are important for high voltage PCB prototypes?
A: High voltage PCB prototypes should undergo thorough testing, including electrical safety testing, functional testing, environmental testing (e.g., temperature, humidity, vibration), and EMI/EMC testing. This comprehensive testing approach ensures that the prototype meets all necessary safety and performance requirements before moving on to the final product design.
Conclusion
Designing a high voltage PCB for rapid prototyping is a critical step in the development of safe, reliable, and high-performance electronic devices. By focusing on prototyping first, designers can identify and address potential issues early, iterate on their designs, and ultimately save time and resources in the long run.
Through proper component selection, layout optimization, and thorough testing, designers can create high voltage PCB prototypes that meet all necessary safety and performance requirements. This approach, combined with best practices and a commitment to quality, can help ensure the success of the final product.
No responses yet