Introduction to Motherboard Colors
The motherboard is the backbone of every computer system, connecting all the components and allowing them to communicate with each other. One of the most striking features of a motherboard is its color, which is typically green. But have you ever wondered why motherboards are green? In this article, we’ll explore the reasons behind this color choice and delve into the world of PCB (Printed Circuit Board) colors.
What is a PCB?
A PCB is a flat board made of insulating materials, such as fiberglass or plastic, with conductive copper traces printed on its surface. These traces connect the various components on the board, such as the CPU, RAM, and expansion slots. PCBs are used in a wide range of electronic devices, from smartphones and laptops to industrial machinery and medical equipment.
The History of PCB Colors
The use of green as the standard color for PCBs dates back to the early days of electronic manufacturing. In the 1960s and 1970s, when PCBs were first being mass-produced, the most readily available and cost-effective solder mask was green. Solder mask is a layer of protective coating that covers the copper traces on the PCB, preventing short circuits and oxidation.
At the time, other colors were available, but they were more expensive and less reliable. As a result, green became the default choice for PCB manufacturers, and it has remained the most common color ever since.
The Advantages of Green PCBs
While the original reason for using green PCBs was largely based on cost and availability, there are several advantages to this color choice that have helped it remain popular over the years.
1. High Contrast
One of the main benefits of green PCBs is their high contrast. The green solder mask provides a clear visual contrast against the white silkscreen labels and the silver or gold-plated components on the board. This makes it easier for technicians to identify and work with the various components during assembly and repair.
2. Durability
Green solder mask is known for its durability and resistance to wear and tear. It provides excellent protection against scratches, impacts, and environmental factors such as moisture and heat. This durability helps ensure the longevity and reliability of the PCB.
3. Cost-Effectiveness
Despite advancements in PCB manufacturing technology, green remains one of the most cost-effective color options. This is due to its widespread availability and the fact that it has been the industry standard for decades. Choosing green PCBs can help keep production costs down, which is particularly important for large-scale manufacturing.
Other PCB Colors and Their Significance
While green is the most common color for PCBs, it’s not the only option available. In recent years, PCB manufacturers have begun offering a wider range of colors to meet the diverse needs and preferences of their customers.
Blue PCBs
Blue PCBs have gained popularity in recent years, particularly in the consumer electronics industry. Many high-end motherboards and graphics cards now feature blue PCBs as a way to differentiate themselves from the competition and appeal to enthusiasts who value aesthetics.
Black PCBs
Black PCBs are another popular choice, especially for industrial and military applications. The black solder mask provides excellent protection against UV light and helps conceal the internal components of the device, which can be important for security reasons.
Red PCBs
Red PCBs are less common but are sometimes used in high-end audio equipment and other specialized applications. The red color is often associated with high performance and quality, making it an attractive choice for premium products.
White PCBs
White PCBs are relatively rare but are occasionally used in LED lighting applications. The white solder mask helps reflect light more efficiently, improving the overall brightness and uniformity of the LED array.
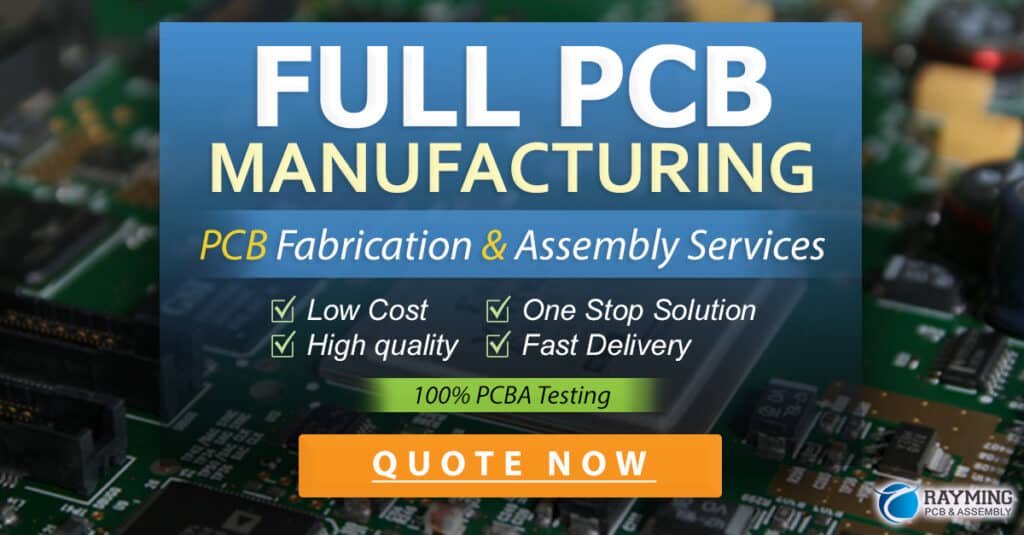
The Role of Solder Mask in PCB Colors
As mentioned earlier, the color of a PCB is determined by the color of its solder mask. Solder mask is a thin layer of polymer that is applied to the surface of the PCB, covering the copper traces while leaving the pads and other components exposed.
The Solder Mask Application Process
The solder mask application process typically involves the following steps:
- The PCB is cleaned and dried to remove any contaminants.
- A layer of liquid photoimageable solder mask is applied to the surface of the PCB.
- The solder mask is exposed to UV light through a photographic film, which hardens the exposed areas.
- The unexposed areas are washed away, leaving behind a protective coating on the desired areas of the PCB.
- The PCB is then cured in an oven to fully harden the solder mask.
Solder Mask Colors and Additives
The color of the solder mask is determined by the pigments and additives used in its formulation. Green solder mask, for example, typically contains a combination of green pigments and fillers such as talc or silica.
Other colors are achieved by using different pigments and additives. For example, blue solder mask may contain phthalocyanine blue pigments, while red solder mask may use quinacridone red pigments.
In addition to color pigments, solder mask formulations may also include various additives to improve their performance and durability. These can include:
- Flame retardants to reduce the risk of fire
- UV stabilizers to prevent color fading and degradation
- Adhesion promoters to improve bonding between the solder mask and the PCB surface
- Flexibility agents to prevent cracking and peeling of the solder mask
PCB Color and Industry Standards
While PCB colors are largely a matter of preference and aesthetics, there are some industry standards and guidelines that relate to PCB color and solder mask.
IPC Standards
The Association Connecting Electronics Industries (IPC) is a global trade association that develops standards for the electronic manufacturing industry. Several IPC standards relate to PCBs and solder mask, including:
- IPC-SM-840: Qualification and Performance Specification of Permanent Solder Mask
- IPC-A-610: Acceptability of Electronic Assemblies
- IPC-6012: Qualification and Performance Specification for Rigid Printed Boards
These standards provide guidance on the quality, performance, and acceptability criteria for PCBs and solder mask, helping to ensure consistency and reliability across the industry.
Mil-Spec Standards
In addition to IPC standards, PCBs used in military and aerospace applications may be subject to Mil-Spec (Military Specification) standards. These standards are more stringent than IPC standards and may have specific requirements for solder mask color and performance.
For example, MIL-PRF-55110 is a performance specification for rigid printed circuit boards used in military applications. It includes requirements for solder mask color, adhesion, and resistance to solvents and environmental stress.
Frequently Asked Questions (FAQ)
-
Q: Are green PCBs better than other colors?
A: Green PCBs are not inherently better than other colors in terms of performance or functionality. The choice of PCB color is largely a matter of preference and aesthetics, although green does offer some advantages in terms of contrast and cost-effectiveness. -
Q: Can I choose any color for my PCB solder mask?
A: While most PCB manufacturers offer a range of standard colors (such as green, blue, red, and black), it is possible to request custom colors for your solder mask. However, custom colors may be more expensive and may require a minimum order quantity. -
Q: Does the color of the PCB affect its electrical properties?
A: No, the color of the PCB solder mask does not directly affect its electrical properties. The electrical performance of a PCB is determined by factors such as the quality of the copper traces, the dielectric properties of the substrate material, and the design of the circuit itself. -
Q: Are there any disadvantages to using colored PCBs?
A: One potential disadvantage of using colored PCBs is that they may be more difficult to inspect visually for defects or damage. The high contrast of green PCBs makes it easier to spot issues such as solder bridges or damaged traces. However, this can be mitigated by using automated optical inspection (AOI) equipment. -
Q: Can the color of the PCB affect its thermal performance?
A: The color of the PCB solder mask can have a minor effect on its thermal performance. Darker colors (such as black) may absorb more heat, while lighter colors (such as white) may reflect more heat. However, this effect is relatively small compared to other factors such as the thermal conductivity of the substrate material and the design of the heatsinks and cooling systems.
Conclusion
In conclusion, the green color of motherboards and other PCBs is largely a result of historical and economic factors, dating back to the early days of electronic manufacturing. Green solder mask was the most readily available and cost-effective option at the time, and it has remained the industry standard ever since.
However, the choice of PCB color is not just a matter of tradition or cost. Green PCBs offer several advantages, such as high contrast, durability, and cost-effectiveness, which have helped maintain their popularity over the years.
That being said, PCB color is ultimately a matter of preference and aesthetics, and there are now a wide range of color options available to suit different needs and preferences. Whether you choose green, blue, black, or any other color, the most important factor is the quality and reliability of the PCB itself.
As the electronics industry continues to evolve, it’s likely that we’ll see even more innovations and options in PCB color and design. But for now, the green motherboard remains a familiar and iconic sight in the world of computing.
No responses yet